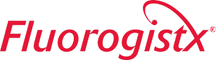
Of the many quality
assurance tools that a coating services supplier should have on hand, coating
thickness gauges are one of the most important for maintaining
high-quality coatings that both perform properly and meet external standards.
Another substantial benefit is cost savings, as keeping coatings consistently within
specifications can reduce material and labor waste. And you should consider
whether the time savings of a tester
that measures continuously at 140 times per minute is worth the investment
to prove your coatings are consistent.
Coating thickness gauges (aka paint meters or mil gauges) are used
to measure dry film thickness without leaving marks on your parts. These are a “non-destructive
testers” with great repeatability in measurements. Dry film thickness is
probably the most critical measurement in the coatings industry because every
coating has thickness range specifications. A coating thickness gauge provides
vital information that can confirm the expected life of the substrate, the
coating properties’ performance, the coating appearance, customer expectations,
and the job’s compliance with international standards.
Many jobs in the Military and Aerospace segments require
verification of the work that you are performing. Suitable coating thickness gauges
are certified by the all the applicable ASTM Standard test methodologies, which
allows you to compete in markets that are sensitive to these specifications. Thickness
testers can also compile the measurements you take and deliver a formal report
that can be shared with the end user.
Most quality shops lay out pass/fail expectations of their customers before
accepting their order, and more end users these days are requiring proof of
testing. Coating thickness gauges demonstrate to your customers that the
coatings were applied to the thickness they requested. This will help you
eliminate rejects and take your customer satisfaction to new levels.
Incorporating thickness measurement into your everyday processes also
saves on material costs. Monitoring coating thickness will drive your coaters
to better control thickness and eliminate excessive wasted coating. As an
example, if you purchase $10,000 in coatings a year and improve your thickness
control by .5 mils, you would save $2,552 a year.
By using these simple techniques, you’ll be able to cut out the
waste as well as achieve a better, more consistent finish for your Teflon™
industrial coatings.
If you’re looking for more tips on keeping your Teflon™ coating
services at the highest quality consistently, read our other blogs on “Basic Quality
Testing” and “Advanced Quality
Testing.”