
Fluoropolymer Sustainability and Responsible Manufacturing to Support Cable and Connectivity
Speaker Bio: Bianca Hydutsky, Global Technology Director – Advanced Performance Materials, The Chemours Company
Register Now
Abstract: Regulatory activity targeting fluorinated materials has increased globally, which may impact the ability to select and utilize the optimal materials to achieve performance and safety criteria in cable and connectivity designs. Many essential use cases have been identified both for safety and performance across a wide range of applications, such as, clean energy, transportation, aerospace, automation, advanced electronics, oil & gas, defense, security, medical, pharma, and more.
There are many questions and misconceptions across these industries, ranging from the chemistries of such materials to the development and deployment of responsible manufacturing technologies.
This work provides an overview of the regulatory landscape, examples of fluoropolymer materials of critical essentiality, and a deeper understanding of the sustainability impact of responsible manufacturing investments and analytical expertise needed to move forward.
About the Presenter: Dr. Bianca Hydutsky is the Global Technology Director for the Advanced Performance Materials Division of The Chemours Company, LLC. She received her B.S. in Chemistry from Millersville University and Ph.D. in Chemistry from The Pennsylvania State University.
The safety and quality of our products are top priorities, and that includes protecting them during colder months. Starting October 15, 2024, we are entering our annual Freeze Protect Season, which will run through April 15, 2025.
During this period, we implement additional packaging and shipping services to ensure our customers’ shipments remain unaffected by freezing temperatures. This applies to the following product lines (by prefix): 459G, 699N, 850G, 851G, 852G, 855G, 856G, 857G, 858G, and 953G.
Freeze Protect Services and Fees:
- Freeze Protect Fee: A $39.00 per box over-pack charge will be applied to all shipments, and $39.00 per shipment for freeze protect services.
- Overnight Service: Available for critical shipments (except for product codes 850-7799 and 850G-204, which ship freight only).
Receiving Freeze Protected Shipments
When you receive a freeze-protected shipment, it’s crucial to follow the proper procedures:
- Check the product before signing the Bill of Lading. Open the box and inspect the product immediately.
- Check the freeze indicator: If the indicator is broken or turns blue/purple, the product may have been exposed to freezing temperatures.
- Do not reject the shipment: Instead, sign the Bill of Lading with the note, “Frozen Shipment Will Accept to Determine Extent of Damage.”
- Evaluate the product: Let it sit overnight, reincorporate the coating the next day, and assess the product.
- Notify Fluorogistx within 4 days of receiving the shipment if there’s any damage. Contact Corey Leigh at (302) 479-7734 or via email at leigh@fluorogistx.com.
Please ensure this information is shared with all relevant departments in your organization, including shipping, receiving, and procurement.
If you have questions about protecting your Teflon™ shipment, reach out through e-mail, phone, or by contact form on this websiste.
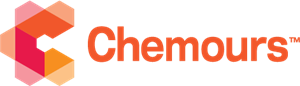
Fluorogistx is proud to share that Chemours is the recipient of a gold medal for their efforts in sustainability by EcoVadis, a sustainability management system. With the excellent rating on Chemours’ sustainable supply chain, Chemours is now in the top 5% of all responding companies.
According to the Corporative Responsibility Commitment goals articulated, Chemours is committed to a baseline sustainability performance of 80% suppliers by spend. This sustainable supply chain spans 9,000 suppliers across 60+ countries. Chemours plans to demonstrate a 15% improvement by the year 2030.
Read more about Chemours’ gold medal and efforts to keep supplies and sustainability at the forefront of their fulfilment.
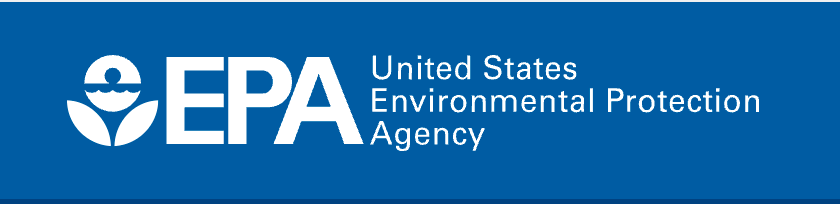
The Environmental Protection Agency (EPA) hosted a comprehensive webinar on the TSCA 8(a) PFAS reporting obligations. It is recommended that all manufacturers (including importers) of PFAS and PFAS-containing products since 2011 review the webinar or its transcript. This reporting mandate is stipulated by the FY2020 National Defense Authorization Act.
For those seeking further insight into the TSCA 8(a) PFAS reporting requirements enacted in October 2023, additional information is available via an EPA-sponsored webinar accessible through this link.
Below is a quick Q&A regarding purchasing Teflon™ coatings after the acquisition of Intech Services by Fluorogistx.
Q: Who do I contact for new orders? What about order status and tracking?
A: You can contact Patrick Garyantes to place new orders, check order status, and track your orders. E-mail him at Patrick.Garyantes@Fluorogistx.com You can callPatrick at 302-479-7614. If you prefer, you can fax new orders at 302-479-7618.
Q: When will orders ship?
A: Orders placed before 11:00AM will ship same day. All orders placed after will be shipped the next business day.
Q: Who are shipping carriers for ground and LTL shipments?
A: We typically use FED EX freight, XPO, A. Duie Pyle, etc. Depending on the location, however, customers can designate any shipping carriers for ground they wish.
Q: Certifications – what type of certs do you provide?
A: We will continue to provide certification of analysis and conformance.
Q: Are invoices mailed or emailed?
A: Depending on the customer’s prior communication and preferences, you will continue to receive invoices by mail or e-mail as you have in the past.
Q: Who do I contact regarding invoices and accounts payable?
A: You can contact Cathy Delaney for Invoices at Cathy.Delaney@Fluorogistx.com You can contact Marianne Morrow for accounts payable at Marianne.Morrow@Fluorogistx.com.
Q: How can I get a W-9?
A: E-mail PatrickGaryantes at Patrick.Garyantes@Fluorogistx.com for a W-9.
We are here to answer your most pressing questions about the Intech Services transition.
Q: Is Mike retiring?
A: No, Mike isn’t sailing off into the sunset yet. He will continue working with the Teflon™ team and customers at FGX to grow the industrial Teflon™ coatings business.
Q: Who is my sales representative, and who else is going with the move?
A: Mike Patterson, Chris Lord, and Steve Bucci will be moving to FGX and continue to be responsible for sales, technical support, and market development for the industrial coatings product line.
Q: How do I reach you by e-mail? Is there a new phone number?
A: You can contact our team through their Intech Services e-mails and phone numbers even after the sale. All e-mail and phone calls will be forwarded. You will receive e-mails from the new FGX e-mail addresses starting in May.
Q: Does this change of ownership mean there’s a price increase?
A: There will be no price increase associated with this transition.
Q: Do I need to reapply for credit at FGX? What will terms be?
A: No, you do not need to reapply for credit. Your terms stay the same and transfer with the sale.
Q: Did MOQs change? What about lead time for ordering?
A: No, there are no changes for MOQs, price, nor lead times for orders.
Q: Will we still be able to get material certifications?
A: Yes – we will still be able to provide Certifications of Conformance and Analysis.
Q: Can I buy online and what is happening with the Intech Marketplace?
A: You will have access to the Intech Marketplace and all e-commerce on our website until the end of April. Because FGX does not have the same backend support and software, you will not be able to purchase products from the Marketplace after the move. Our hope is to reopen the portal in the future. We encourage you to place orders for tapes, masking products, etc. ASAP!
Q: I have an invoice I need to pay. Where do I send the check?A: You can still send all checks to 211 Lake Drive Suite J Newark, DE 19702.
A: Any payments that arrive after we relocate will be forwarded to the new address.
Q: Any recommendations for customers?
A: Yes. Buying inventory in April will guarantee you have product on hand through the move. While we don’t anticipate a disruption in deliveries and service, it is still a good idea to stock up.
Q: What if I have specific questions about ordering and operations?
A: Our next email will cover more details. We will also be providing the new W9 for FGX in the near future.
Did we get your question answered? If not, let us know what it is, and we’ll add it to our blog post. Check back for more Q&As as we get closer to a final sale.
After 31 years of business as the exclusive distributor of Teflon™ industrial coatings, Intech has been acquired by fellow Chemours’ channel partner, Fluorogistx (FGX).
As the exclusive distributor for Chemours™ Fluoropolymer resins and dispersions in the United States and Canada since 2009, Fluorogistx services a broad spectrum of industries including aerospace, chemical processing, and data communication.
Bob Smith, President of Fluorogistx, joined the company in 2012. Some of you may know him from his 32 years at DuPont managing Teflon ™ businesses. Bob has a well-deserved reputation for serving customers and supporting them through industry economic cycles, some of which have been very challenging.
Fluorogistx and Intech Services share a similar long-term legacy of serving North American customers on behalf of Chemours™. Combining the two entities will create an even stronger market presence and further our ability to meet the needs of our customers in the future.
We are in the process of putting together an extensive list of answers to questions you may have about this transition and how it will affect you. The important takeaways now include:
- Expected transition date is May 1, 2023.
- Intech Services will continue to take and fulfill orders through the end of April.
- There is no price increase for Teflon™ coatings planned.
- Throughout the transition, all open orders and backorders will be fulfilled seamlessly.
- Our team will continue to provide the same excellent product and technical support.
- Fast, reliable shipping will continue.
- The Intech Services name will be retired, and all future business will conducted under Fluorogistx.
Keep your eyes open for more details in the near future.
On behalf of the entire team at Intech, I am very proud of the work we have done at Intech Services and the growth we’ve fostered over the past 31 years. This transition marks an exciting, new chapter for all of us involved, and we will continue to earn your business by providing the same excellence in service and support that you have been accustomed to for the last three decades.
Intech Services, the Newark, Delaware-based pioneers and sole sellers of Teflon™ coatings in North America, have announced the launch of a new coating material to rival Cerakote for recreational, tactical and military firearms.
The product launch represents the culmination of years of research and product development by Intech and their partners Chemours.
Designed to supersede and improve upon the industry standard Cerakote material, Intech Services’ new Teflon™ based coating material promises to improve the overall performance of hand guns, rifles, and shotguns. In particular, their new technologically advanced coating material ensures a low coefficient of friction surface, corrosion resistance and increased durability.
Firearm manufacturers, owners and enthusiasts will also note reduced jamming, reduced sliding friction, reduced carbon fouling and the elimination of rust for firearms. The superior Teflon™ based technology also guarantees a high quality flawless finish and is available in low gloss, rich colors such as Desert Tan, Drab Green and Matte Black.
With its smooth application, shorter oven cure time, and 20+ year UV resistance, Intech Services and Chemours believe they are providing the most superior firearm coating material in the North American market.
Intech Services has been the sole US & Canadian seller and distributor for Teflon™ industrial coatings for 30 years. They are constantly focusing on growth through market development, innovation, service, and support. Through their partnership with Chemours, Intech is determined to provide the highest quality and performing coatings to their customers.
Intech is the exclusive distributor of this new firearm coating technology. They offer online ordering, fast shipping, and competitive pricing for customers across the United States and Canada.
A spokesperson for the company said, “Intech Services goes beyond the transaction. When you purchase with us, you also get access to our world-class support. Our business is comprised of friendly, knowledgeable people that can offer technical support, troubleshoot application issues, provide failure analysis and more. We are here to help you coat more, better.”
More information on their new firearm coating material is available at https://fluorogistx.com/teflon-ptfe-dry-film-lubricants
Do you work in the industrial coatings industry? What marketing and sales techniques do you currently use? Are they working for you? Do you want to hear from like-minded individuals and industry professionals? If you are ready to take your business to the next level, this is the YouTube talk show for you!
‘Deliver More’ is the name of the new talk show, which was created to fill the media void within the coatings industry in Canada and the US. Intech Services understands the challenges faced by you and other industrial manufacturers, and how difficult they can be to manage as these issues rarely gain mainstream attention.
You can view more information here.
If you want to listen to quality conversations on the issues that matter most to you in the coatings industry, this is the monthly YouTube talk show for you. In each episode, the hosts invite different guests to offer advice so you can take your company to the next level.
‘Customer Service with Monica Trout’ is the latest episode and focuses on the importance of quality customer service. During the show, the global health crisis is discussed alongside the ways it has highlighted the need for regular customer updates.
You can view more about Intech Services at https://fluorogistx.com
Intech Services provide support via email and telephone to ensure customers can reach them when they need to, through their preferred medium. As you may be aware, a key challenge being faced by the industry, and manufacturers around the world, is supply chain issues.
A lack of raw materials is causing issues throughout the supply chain, which is having knock-on effects, including product shortages. As the world reopens for business, these shortages are becoming more noticeable.
Monica states that there are tough conversations that need to be had between you and your customers to highlight the materials shortages and possible solutions. In these situations, she explains that giving your customers advance notice of the challenges can prevent dissatisfaction in the future.
It can also build trust and brand loyalty when your customers are listened to and supported, even when there may not be an immediate resolution.
A company spokesperson said: “The ‘Deliver More’ video series will cover a wide range of topics that will help you become a better, and more profitable, Teflon coater. If you have a specific Teflon coating technical question, call our Technical Team anytime at 1-302-366-8530.”
Go to the links provided to find out more, or click on https://anchor.fm/deliver-more so you can stream the podcast.
If you operate in the chemical, petro-chemical, mining, or semi-conductor industries, these EFTE coatings have been developed and tested with you in mind.
Replacement of parts is not an ideal solution when there are supply chain issues. Intech Services states that EFTE coatings provide you with a cost-effective alternative now and well into the future.
As you’re probably aware, Teflon™ is a household name when it comes to non-stick coatings. However, its use as an industrial coating, both in liquid and powder forms, is lesser-known. The various product families all use fluoropolymer technologies, which possess unique protective properties.
More specifically, the expanded line of ethylene tetrafluoroethylene (ETFE) products is designed to provide high corrosion resistance across a wide temperature range. Intech Services states that these qualities make them ideal for chemical processing applications.
Indeed, EFTE coatings are already widely used in the chemical industry. Teflon™ products are regularly exposed to acids, polymers, petrochemicals, and inorganics and have demonstrated excellent corrosion resistance and durability to date. With the latest range, the company provides you with the ability to reach thicknesses of between 80 and 100 mils, resulting in a greater degree of protection.
Some examples of places where you could apply the coatings include tanks, vessels, flanges, piping, impellors, manifolds, and reactors. While metal components and other treatments can be expensive, Intech Services states that the updated range provides you with a cost-effective solution.
About Intech Services
As the sole distributor of Teflon™ products in the US and Canada, Intech Services has embraced its position of leadership to provide a range of education programs in support of customers and suppliers. Workshops inform you on available products, emerging markets, and sales strategies. In addition to Teflon™, the company also supplies TCI powder coating, Mighty Hook, Gemma Powder Equipment, and Steelman Ovens.
A company representative stated:
“Intech’s long-term relationships are built on solid foundations of fast and courteous customer service. We look at our leadership role as a responsibility to help grow our coating customers’ capabilities and services and lift the industry as a whole in the process.”
Teflon™ is a household name for a good reason. Click here to learn more.
On this special edition of Deliver More we celebrate an important milestone for the company. To celebrate 30 years of business, we sit down for a talk with Mike & Bob Patterson to discuss the very beginning of Intech Services, and the vision that’s allowed the company to deliver more for 3 decades.
PTFE Zonyl™ Micropowders
Based on rigorous testing of representative samples, Chemours™ Zonyl™ PTFE Micropowders are certified to comply with Annex I to Regulation (EU REACH) 2019/1021.
Recently, the EU has taken measures to regulate PFOA, its salts and related substances in a wide range of products under the EU REACH program. The new regulation requires that, subject to certain exceptions, as of July 4, 2020, mixtures and articles placed on the market in the European Union will have to meet the concentration limits set under Annex I to Regulation (EU) 2019/1021 (EU Persistent Organic Pollutants Regulation). Based on rigorous testing of representative samples, Chemours™ Zonyl™ PTFE Micropowders comply with Annex I to Regulation (EU REACH) 2019/1021.
Currently Chemours™ offers multiple Micropowder offerings that meet the above regulation. For more information download the Zonyl Micropowder product brochure here.
Curing is the last step to good adhesion of your Teflon™ coatings. Reaching and maintaining proper cure temperatures for a sufficient period of time to cure the coating is one of the most important factors in achieving a finish with optimal adhesion performance.
It’s important to remember that all temperatures mentioned in the Teflon™ Fact Sheets refer to metal temperatures, meaning that it’s the part itself must reach the recommended cure temperature. Ovens should be calibrated at least twice per year, and thermocouples should be used to check part temperatures. Each coating has different curing instructions, so always check the Fact Sheets first, and always follow the cure schedule very carefully.
Class A Oven Curing
All commonly used types of industrial ovens are used for curing Teflon™ industrial coatings. Teflon™ coating systems are not affected by the combustion products of coal gas or natural gas, so direct fired gas ovens may be used. Both batch ovens and high production conveyorized ovens are used. Conveyorized ovens must be carefully designed to give accurate and uniform temperature control since maximum conveyor speed and minimum oven length are important economic factors which operate to reduce dwell time.
CONVECTION OVENS may be gas fired, direct or indirect, or heated by electrical resistance coils. Good circulation is required for uniform heating. Convection ovens require longer time to warm up than infrared ovens, and conveyorized systems require greater floor space for equivalent line speeds.
GAS AND ELECTRIC INFRARED OVENS offer the advantages of rapid transfer of radiant energy, ability to control speed of warm-up by placement of the radiant elements and reduced dwell time. It is less effective where coated parts are complex in shape, since infrared energy travels in a straight line and the intensity of heat is inversely related to the distance (squared) from the source, so inner crevices and angles will not cure at the same rate as outer surfaces facing the source. High velocity air may be used to make the air temperature more uniform.
Oven Safety
Ventilation of ovens is very important for the safety of workers. Ventilation is usually provided via an outdoor stack. Negative pressure should be maintained at all times with an inward draft at both the entrance and exit of the oven. Even the small amounts of decomposition products of fluoropolymers which occur at bake temperatures may cause discomfort to people in the area if the fumes are not vented to the outdoors and allowed to be diluted by the outside air.
Oven Calibration
Ovens should be calibrated at least twice per year, and thermocouples used on the parts themselves or in the oven at several locations, recognizing that air temperatures are of little value except when based on experience with a given oven and oven load over a period of time.
Factors which affect total bake time (including warm-up):
Time in oven
Heat capacity of oven
Mass and thermal conductivity of the substrate
Air circulation
Oven air temperature and/or radiant energy
Percent of substrate covered by Teflon™ (insulator)
Load of work in the oven
Weight to surface area ratio
Here’s an inexpensive oven calibration tool.
Troubleshooting Curing
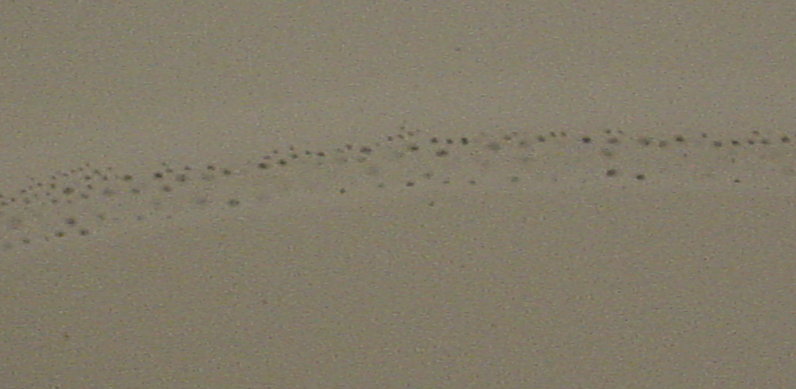
OUTGASSING occurs with cast iron or cast metal substrates and can be prevented by preheating the part up to 250° F before applying the Teflon™ coating. Preheating the part will release all air that is trapped inside the substrate.
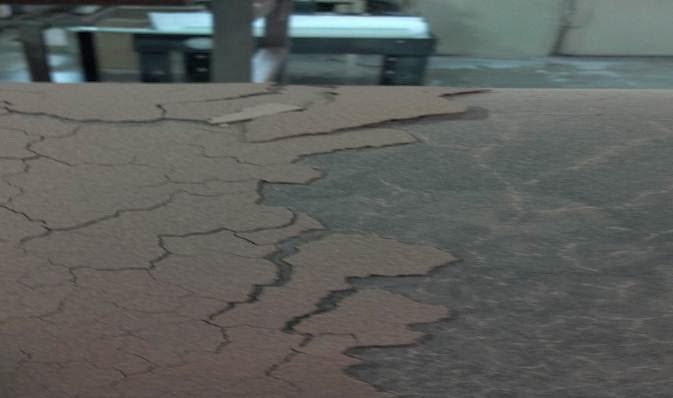
BRITTLENESS usually means the part was over-baked. When the Fact Sheet states the cure temperatures, it is referring to the actual metal part’s temperature. In order to assure that your part has reached the required cure temperature, use a thermocouple to measure the part temperature while curing.
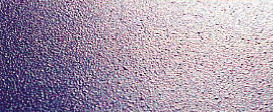
ROUGH TEXTURE can happen when the part is under-baked. Teflon™ industrial coatings should be smooth and have a soft touch to them. Use a thermocouple to make sure the part temperature is correct. Another cause of under-baking can be poor oven calibration.
In previous blog posts, we’ve covered the common types of spray guns, choosing spray guns and keeping them clean, troubleshooting spray gun issues, and overcoming the Faraday Cage Effect. Here we’ll review some techniques that will help you save money while spraying and also how to choose which feed system and gun type will be best for your applications.
Film thickness consistency plays a big role in saving money in the coating shop. Having inconsistent thicknesses means you’re probably wasting coating, and therefore wasting money. By using these simple techniques, you’ll be able to cut out the waste, as well as achieve a better, more consistent finish for your application.’
1. Spray Distance
The spray distance is based on the spray equipment, coating, complexity of the part and spray environment. By keeping the gun at the same distance from the part the entire time you’re spraying, you can improve the consistency the film thickness over the whole part. Increasing the gun distance increases the pattern fan size, and the coating thickness decreases as it is distributed over a larger area.
2. Gun Angle
Maintain controlled gun angle to the part. Yaw and pitch spray angles will result in a non-uniform spray pattern distribution, causing inconsistent film thicknesses.
3. Spray Pass Overlap
Each spray pass should overlap 50% to 75% of the previous pass. Overlapping below 50% results in “striping,” or variations in the film thickness. The more you increase the overlap, the thicker the coating, so overlapping above 75% requires more spray passes and more coating.
4. Spray Pass Speed
Adjust the spray gun speed to achieve consistent films. Before pulling the trigger, consider the coating flow rate and the target wet film thickness. Adjust the equipment before spraying to find a flow rate that lets the applicator move at a controllable, comfortable speed. Spraying too fast can lead to decreased film thickness, and sometimes extra coats will be needed to make up the deficit.
5. Trigger Control
Maintaining a consistent trigger pull on each spray pass directly impacts the flow rate, spray pattern size, and transfer efficiency. Start triggering immediately before the lead edge of the part and release the trigger immediately following the lag edge. Fully pulling the trigger provides constant flow rate control. The fluid knob on your spray gun can be adjusted to restrict the trigger travel distance so you can always pull the trigger all the way. Partial triggering, however, can be very useful for blending and touching up.
6. Edge Banding
Partially pull the trigger to spray a light coat around the edges of the part. Then spray the center of the part, blending the edges into the first coat. Banding can increase transfer efficiency and increase film thickness on the edges. This technique ensures the edges get coated completely while maintaining consistent film thicknesses.
Spray Gun Feed Systems
We have a large selection of spray guns with many combinations of gun platforms and feed systems. Here is some information to help you decide on the best feed system for your shop:
GRAVITY FEED SYSTEMS use cups attached to the top of the gun and use gravity to feed the coating into the gun. Gravity feed guns can have different coatings switched out quickly and require less pressure to operate. However, the cups are usually small and do not hold much coating, so they are best for coating small parts.
SIPHON FEED SYSTEMS use cups attached to the bottom of the gun and create a vacuum that sucks the coating into the gun. Siphon feed guns are heavier that gravity feed guns, but the cups hold more coating.
PRESSURE FEED SYSTEMS use pots that utilize air pressure to push the coating through a tube into the gun. No fluid can leak from the pot, so you don’t have to worry about wasting coating. The gun itself is lighter than gravity and siphon feed guns because there is no cup attached to the gun at all. You can also spray with the gun upside-down or at sharp angles and not worry about the coating coming out of the cup.
Choosing Spray Gun Types
CONVENTIONAL SPRAY GUNS use a basic high pressure. The coating is blasted onto the part at this high pressure using an air compressor. The high pressure finely atomizes the spray giving the coating a very smooth finish. Transfer efficiency for Conventional spray guns is typically 50% or less.
HIGH-VOLUME LOW-PRESSURE (HVLP) spray guns increase transfer efficiency, typically to about 65%, meaning more of the coating actually makes it to the part instead of being wasted. With HVLP guns, air is delivered at much higher volume than conventional guns, but with a much lower pressure, so that more finish ends up on the part instead of in the air. HVLP guns are compliant with the California South Coast Air Quality Management District.
TRANS-TECH SPRAY GUNS use low volume, medium pressures. Transfer efficiencies are normally about 60% or better. Trans-tech guns are the best of both worlds: the finish quality is almost that of a conventional spray gun with close to the efficiency of an HVLP spray gun. Trans-Tech is used where compliance is not required but cost savings is important.
Here’s a handy chart for deciding between Conventional/Air Spray, HVLP, and Trans Tech/Compliant.
And more on Troubleshooting spray guns here.
How to overcome the Faraday Cage Effect.
…and more on the most common spraying methods.
Any Teflon™ industrial coating system is only as good as the prepared surface it is being applied to. Good adhesion can make or break the performance of a properly baked Teflon™ coating. The life of a coating can be directly related to the steps taken in cleaning and providing a good surface to adhere to. Find out the best substrates, proper surface preparation materials, and processes necessary to maximize adhesion results for Teflon™ coating systems in the “Application Overview” section of our website.
Are you thinking about upgrading your shop so you can apply Teflon™ coating systems? This can feel like an overwhelming task, but that’s where we come in.
As the sole distributor of Chemours Teflon™ industrial coatings for over 27 years, Intech Services has come to have a deep understanding of the coating process and the equipment needed to apply our coatings. And we have collected the best equipment for your coating business in our online Shop.
Essential Equipment for Coating
In this “Equipment Start-Up Guide,” we have put together a baseline estimate of what it would cost to start up your Teflon™ industrial coating operation. Whether you are a coating shop looking to expand business or if your company wants to bring an outsourced coating job in-house, this Guide provides the foundation of what you will need to get started.
The process for applying Chemours Teflon™ industrial coatings includes reincorporating solids in the coating by rolling, preparing the surface by grit blasting, spraying the coating with the correct spray equipment, and curing the coating in a Class A industrial oven. In order to achieve the optimal coating, each step is important and should be considered as you evaluate this process. This Guide covers it all’.
And our Technical Services Team is here to guide you through the process:
- Selecting the right equipment
- Selecting the right coatings
- Managing multiple vendors
- Reliable options and upfront pricing
- Convenient payment schedules
- Coordinating delivery and installation of new equipment
- Post-sale follow-up and service
Call the Technical Services Team anytime at: 302-366-8530.
Adelhelm LubriCoat NA was formed in 2018 when the Adelhelm Coaters Group acquired the remaining shares of Quality Coatings Inc. located in Mukwonago, WI. Adelhelm is a group of industrial coaters applying nonstick, dry film lubrication, and corrosion and chemical protection coatings. Chemours Company awards Licensed Industrial Applicator (LIA) certification to coaters that demonstrate consistently high quality control in operations and production.
The Adelhelm Group, established in 1971, has grown to an internationally recognized provider of engineered coating solutions in the automotive, aeronautic, medical, chemical, offshore, and food processing industries. Working closely with Tier 1 and 2 companies and other end users, Adelhelm can select from the most efficient coating methods combined with coating products from Chemours Company supplied through Intech Services.
The Adelhelm group continues to grow with the headquarters in Eningen, Germany, and satellite locations in Switzerland, U.S., Czech Republic, Poland, Romania, and India. Adelhelm LubriCoat NA is headed up by Adam Berres (left) and Dan Drayna (right). For more, visit their website.
All Teflon™ coating varieties are “fluoropolymers,” which are fluorocarbon-based polymers with multiple carbon-fluorine bonds. This classification means that they possess a number of performance characteristics that are highly desirable in industrial and consumer applications. There are currently over 50 varieties of Teflon™ fluoropolymers that Intech Services provides.
However, there are four main “families” of fluoropolymer chemical formulations. And within each product family, there are a number of Teflon™ products to provide you with the best industrial coating for your particular application. The four main families are:
PTFE: polytetrafluoroethylene
FEP: fluorinated ethylene propylene
PFA: perfluoroalkoxy
ETFE: ethylene tetrafluoroethylene
If you need help selecting the exact Teflon™ variety for your application, the Intech Services on-call Technical Support Team is always available to answer your questions: 302-366-8530. If you want to research every variety on your own, click here for Teflon™ SDS and Fact Sheets.
Teflon™ PTFE Coatings
PTFE nonstick coatings are two-coat (primer/topcoat) systems. These products have the highest operating temperature of any fluoropolymer (260°C/500°F), an extremely low coefficient of friction, good abrasion resistance, and good chemical resistance. Teflon™ PTFE is available only in water-based liquid form.
Teflon™ FEP Coatings
FEP nonstick coatings melt and flow during baking to provide nonporous films. These coatings provide excellent chemical resistance. In addition to low friction, Teflon™ FEP coatings have excellent nonstick coating properties. Maximum use temperature is 204°C/400°F. Teflon™ FEP coatings are available in water-based liquid and powder forms.
Teflon™ PFA Coatings
PFA nonstick coatings melt and flow during baking to provide nonporous films. Teflon™ PFA coatings offer the additional benefits of higher continuous use temperature (260°C/500°F), greater toughness than Teflon™ PTFE or Teflon™ FEP, and some Teflon™ PFA coatings can have film thicknesses of up to 1,000 micrometers (40 mils). This combination of properties makes Teflon™ PFA an excellent choice for a wide variety of uses, especially those involving chemical resistance. Teflon™ PFA protective coatings are available in both water-based liquid and powder forms.
Teflon™ ETFE Coatings
ETFE is a copolymer of ethylene and tetrafluoroethylene and is also sold under the Tefzel® trademark. Although not fully fluorinated, Tefzel® ETFE has excellent chemical resistance and can operate continuously at 149°C/300°F. This resin is the toughest of the fluoropolymer coatings and can be applied at film builds up to 2,000 micrometers (80 mils) to provide a highly durable protective coating. ETFE is available in powder form.
Intech Service Delivers Quality… Reliably
- Quality – 6 product lines that are the industry standard
- Flexibility – Over 50 Teflon™ varieties for catered solutions
- Accessibility – 24/7 e-commerce site for Teflon & supplies
- Availability – 98% of shipments ship same or next day
- Stability – 28 years supplying Teflon; thousands of satisfied customers
- Reliability – Our in-house experts know what you need
Intech Services President Mike Patterson introduces his Teflon™ industrial coating Technical Team, with over 50 years of combined Teflon™ coating experience.
Any Teflon™ industrial coating system is only as good as the prepared surface it is being applied to. Good adhesion can make or break the performance of a properly baked Teflon™ coating. The life of a coating can be directly related to the steps taken in cleaning and providing a good surface to adhere to. Find out the best substrates, proper surface preparation materials, and processes necessary to maximize adhesion results for Teflon™ coating systems in the “Application Overview” section of our website.
Substrate Considerations
Any substrate which is dimensionally and thermally stable at the bake temperature required for the particular product can be coated with Teflon™ Industrial coatings. Articles to be coated should be free of sharp corners and edges, excessive pits or porosity and excessive roughness as at welds and joints.
At bake temperatures greater than 450°F/232°C, certain metallic substrates are unacceptable. The melting points of tin (450°F/232°C) and lead (622°F/328°C) are too low to permit some Teflon™ bakes. The poor adhesion of copper to the copper oxide formed when copper is baked in air at high temperatures results in poor adhesion of the Teflon™ industrial coatings.
Because of reactivity at the high baking temperatures, Teflon™ coatings have relatively poor adhesion to magnesium and to aluminum/magnesium alloys containing more than 0.5% magnesium. Aluminum permanent-mold castings and die castings are successfully coated with Teflon™ coatings, but may show a high reject rate due to the formation of blisters caused by expansion of air bubbles in the metal during the high temperature bake.
Cleaning the Surface
In all cases, Teflon™ coatings should be applied over clean substrates. Normal industrial practices can be used, such as chemical washes or solvent cleaning and degreasing, but precautions must be taken to remove all residues from the cleaning process. Depending on the initial condition of the metal, it may be necessary to physically remove dirt, rust, mill scale, paint, etc. After cleaning, the metal should be handled with latex or nitrile gloves. Fingerprint and residual oil contamination may show up as a stain on the finish.
Preheating the Parts
Preheating metal substrates to the temperature of the Teflon™ bake is advantageous in removing traces of oil and other contaminants, especially when the metal is cast and somewhat porous. With most ferrous metal, this procedure has the advantage of temporarily passivating the surface against rusting and the blue oxide formed increases the adhesion of the acid primers. In the case of aluminum and stainless steel, these advantages are not apparent, and the preheating step can be omitted where clean metal is involved. Copper and brass should not be preheated in air because the resulting oxide has poor adhesion to the metal. A formic acid rinse reduces oxide formation to a degree on copper.
More on Grit Blasting and measuring surface profiles here.
Abrasive Media for Grit Blasting
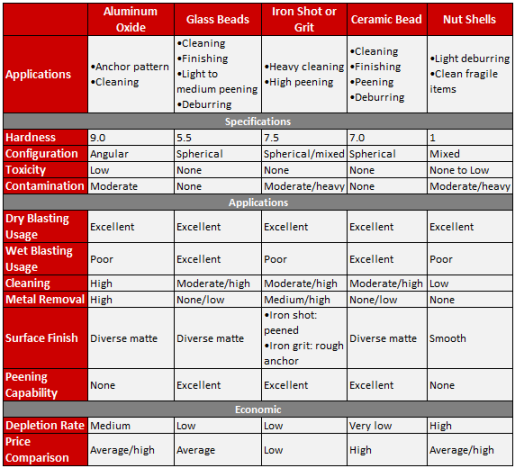
Conversion Coatings
Conversion coatings are the modified surfaces of metal resulting from specific chemical treatment. These conversion coatings, which can be on steel, aluminum, or most other metals, typically include zinc, manganese, and iron phosphates or chromates. The principle function of these coatings is to improve adhesion of finishes and maximize corrosion resistance. The functionality of conversion coatings depends upon their uniformity and the integrity of the coating, both before and after application of the final finish.
Preventing Rust
Since steel and iron rust rapidly after grit blasting, coatings should be applied immediately. Where delay is expected; or under conditions of high humidity, a solvent rinse with VM &P naphtha, or toluene containing 5% of kerosene may be employed. When the volatile solvent evaporates, a very thin film of kerosene remains to prevent rusting temporarily. While the presence of thin films of kerosene does not appear to affect the application of the 850-Line primers, the kerosene film may collect dust on long standing and require solvent washing before the finish is applied.
Testing Adhesion
There are several techniques for testing the bond strength between the coating and the metal surface. The most common test is a cross hatch test. Since this is a destructive test, it is typically performed on a test panel that is processed along with actual parts.
Common Problems Caused by Poor Surface Preparation
Air bubble pops: This is called outgassing, and can be prevented by preheating the part to 250°F before applying the coating.
Crater-like holes: These are called fisheyes, and can be caused by contaminants in the coating or on the substrate. This could even be grit from blasting that wasn’t totally removed. Make sure the spray area and substrate are completely contaminant-free before spraying.
Substrate adhesion failure: If the coating is coming off of the substrate, it could be because the blast profile is not deep enough or there are contaminants under the coating. Blast profiles of at least 2.5 microns are recommended, and profiles between 5.1 – 6.5 microns are frequently used. Always be careful to remove all of the blast media from the substrate before spraying. To make sure all grit has been removed, pre-bake the part at the coating’s cure temperature or higher.
Mudcracking: Mudcracking is when the finished coating looks like the bottom of a dry, cracked pond. This can be caused by too severe grit blasting, wire brushing, or sanding that causes pits and scratches in the substrate’s surface. When sprayed, the coating will flow into the depressions, causing cracks in the cured coating.
There are over 50 varieties of Teflon™ industrial coatings, serving many uses in the current industrial marketplace. But deciding which one to choose for your particular application can be a challenge. Help us help you by preparing your answers to the following questions:
- What is the reason for coating?
- What is the substrate?
- What is the end-use service temperature?
- Will there be chemical exposure?
- Will the part come into contact with food?
- Are there any abrasion/durability concerns?
- What are the heat limitationsof the part?
- What are the part dimensions?
- What are the cost limitations?
- Can the part be removed?
- Have you tried another coating on the same part previously?
We’ve developed a downloadable worksheet to help you prepare for a call with our Technical Service Team.
Here’s a Handy Teflon™ Coating Chart:
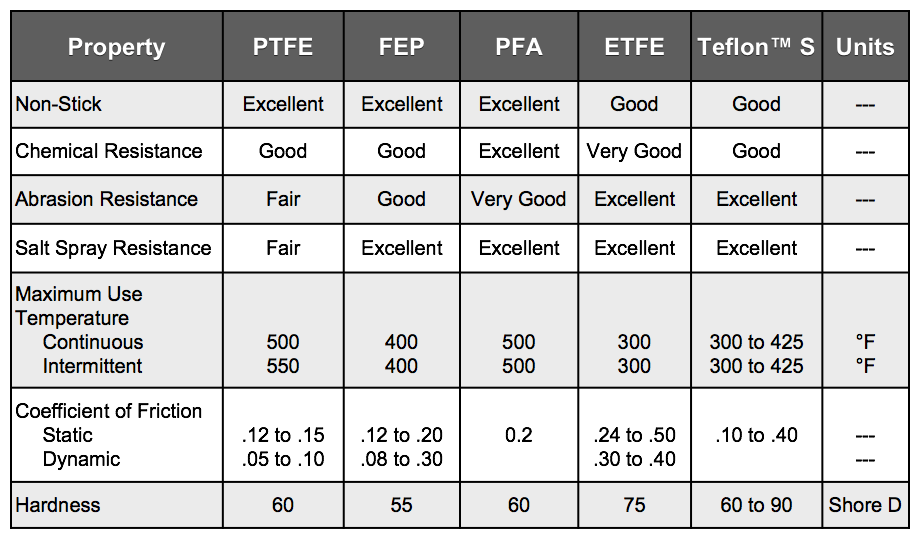
Calculating Teflon™ Coating Costs:
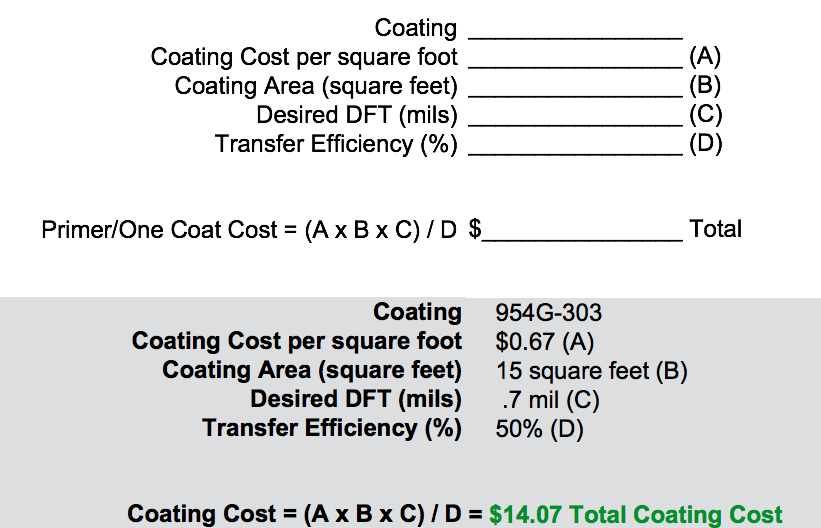
Additional Considerations When Comparing Coatings:
Film Thickness
Improved transfer efficiency
Extreme part cleaning
Extreme masking
Extended oven time (energy)
Complex part geometry, size, or weight
Special packaging requirement
Special inventory
Likelihood of rejects/rework
Rush delivery/maintaining inadequate stock
Money collection
Overtime
“Teflon™Coatings 2020” Kickoff Video! Join us on our journey to educate the coating community on Teflon™ coating application tips, troubleshooting, coating business strategies, Intech Insights—and much more. Catch them here or subscribe to our YouTube channel!
Semiconductor industry manufacturers use Teflon™ coatings to
prevent chip and component contamination from airborne particles. In “clean
rooms,” where often no personnel are even permitted, manufacturers coat
equipment parts with Teflon™ coatings to keep any extraneous particles from
entering the manufacturing process.
How Are Teflon™ Coatings High Purity?
The high purity and inertness properties of Teflon™ coatings have
several secondary benefits in clean rooms. Teflon™ coatings have superior
reliability, retention, and durability while also preventing contamination of
any kind. Another benefit is that Teflon™ coatings are easy to clean. This is due
to another Teflon™ coating property—“non-wetting.”
Non-wetting means that Teflon™ coatings are both hydrophobic and
oleophobic, making cleanup easier and more thorough. Hydrophobic substances
repel the polar ions in water and resist wetting. The low surface energy of the
coatings means that the cohesive forces in the water are strong enough to make
the water bead up and not spread across the surface of the coating. Oleophobic
means oil molecules are “repelled” from the surface. To be completely accurate,
molecules are not repelled, rather there is a complete lack of any attraction.
Teflon™ Coatings in Semiconductor Manufacturing
PFA
topcoats are also popular for semiconductor factory applications because
of their versatility, abrasion resistance, and purity. PFA topcoats are often used
for coat liquid tanks, liquid nozzles, and semiconductor wafer carriers. The
non-wetting property of Teflon™ coatings is especially important for coating
laboratory glassware, such as beakers and test tubes, in order to minimize
cross-contamination.
Teflon™ coatings also coat less critical semiconductor industry
parts, such as robotic armatures, for corrosion resistance. Popular one-coat
options include the FEP Epoxy
Liquid line that comes in green (954G-304) or black (954G-303). These
coatings resist chemicals and chemical vapors and can be easily cleaned.
Spray guns for Teflon™ coatings come in
a variety of shapes, sizes, and spraying technologies. The most
popular guns in Teflon™ coating shops are conventional spray guns, HVLP spray
guns, and Trans-tech spray guns. Here we look at the differences…
Conventional
spray guns use basic high pressure. The coating is blasted onto the
part at this high pressure using an air compressor. The high pressure finely
atomizes the spray giving the coating a very smooth finish. Transfer efficiency
for conventional spray guns is typically 50% or less.
High-volume
low-pressure (HVLP) spray guns increase transfer efficiency,
typically to about 65%. This means more of the coating actually makes it to the
part instead of being wasted. With HVLP guns, air is delivered at much higher
volume than conventional guns, but with a much lower pressure, so that more
finish ends up on the part instead of in the air. HVLP guns are compliant with
the California South Coast Air Quality Management District.
Trans-tech
spray guns use low volume, medium pressure. Transfer efficiencies are
normally about 60% or better. Trans-tech guns are the best of both worlds: the
finish quality is almost that of a conventional spray gun, with close to the
efficiency of an HVLP spray gun. Trans-Tech is used where compliance is not
required but cost savings is important.
Here’s a handy chart to help you choose:
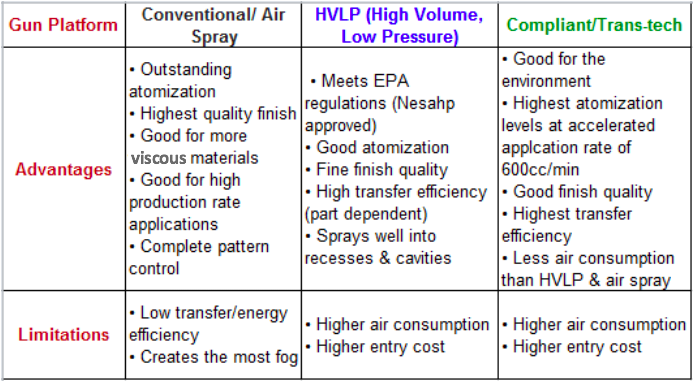
Spray Gun Cleaning
To clean air caps: Remove the air cap from the gun,
place it in a clean solvent, and blow dry. If the small holes are clogged,
after soaking the cap in the solvent, use a toothpick or some other similar
soft implement to ream the holes. Never use wires or a nail because they can
damage the cap.
To clean pressure feed guns with an attached cup: Turn off the air
supply, loosen the cup cover and remove the fluid tube from the paint. Pull the
trigger while holding the gun over the paint cup to let the rest of the paint
drain back into the cup. Empty the cup and wash with a clean solvent and cloth,
then fill the cup halfway with clean solvent and spray it through the gun to
wash out the fluid passages. Make sure you spray into an approved, closed
container and that you follow local codes about disposing of solvents! Clean
the air cap and wipe the gun with a cloth soaked in solvent.
To clean pressure feed gun with a detached cup or tank: Turn off
the air supply and open the relief valve. Material in the hoses may be blown
back, so make sure the lid is loose and the gun is higher than the cup or tank!
Loosen the air cap and pull the trigger until all the material is back in the
cup or tank. A gun cleaner should be used to ensure proper cleaning. Place the
gun and cups over the nozzles in the cleaner and close the lid tightly. The
cleaner will spray solvent through the nozzles, keeping the solvent contained
so it can be disposed of properly. Be sure to dispose of the solvent correctly
according to local codes.
And here’s a handy Spray Gun Troubleshooting Guide:
https://fluorogistx.com/intech-insider-blog/troubleshooting-common-spray-gun-issues/
The flawless, repeatable release
properties of Teflon™ coatings
make them ideal for a number of
applications on packaging lines. Teflon™ coatings consistently convey goods and
packaging materials, seal plastic bags, and line glue pots, among many other
functions. These coatings cover the high-temperature bars that seal plastic
packages, as well as the glue pots that dispense glue for sealing.
Popular Teflon™ Systems for Packaging
The 3-Coat
Reinforced System (857G-040/-140/-240) is the preferred Teflon™
coating for packaging because of its high temperature rating, nonstick
properties, and industry-leading durability. Other applications on packaging
lines use
FEP Teflon™
S One Coats, and pure FEP and PFA topcoats.
The 3-Coat Improved Standard is the premium Teflon™ coating line
reinforced for scratch and durability. The line is for end-uses that require
non-stick, thermal stability to 500° F, and high lubricity. Decades of
innovation and technology have led to significant improvements in this coating.
This water-based, multi-color system is a unique blend of PTFE, PFA, and FEP
fluoropolymer chemistry. The three coats are Primer (855G-021), Midcoat
(857G-135 or -130), and Topcoat (857G-240).
These coatings are available in FDA-Compliant versions. It’s
always a good reminder to note that that there are
21 FDA-compliant Teflon™ coating
systems. According to the FDA
website: “It is the responsibility of the manufacturer of a Food Contact
Substance (FCS) to ensure that food contact materials comply with the
specifications and limitations in all applicable authorizations.” In the simplest
terms, FDA compliance means that any material that might contact food is inert
and safe for human consumption.
Here’s more on FDA Compliance:
https://fluorogistx.com/intech-insider-blog/what-does-fda-compliance-for-teflon-mean-/
We congratulate Nordic Ware Industrial on becoming a Licensed Industrial
Applicator of Teflon™! Nordic Ware Industrial takes full advantage of FDA-compliant
Teflon™ products, coating thousands upon thousands of commercial and restaurant-grade
products out of its Minneapolis, MN, headquarters.
Over 40 years ago, the company began coating parts for industrial
applications to fill a market need for high-release properties. Since that time,
Nordic Ware Industrial has coated parts with a broad range of high-performance
coatings for applications ranging from appliances to space stations, for
customers located in places from the Arctic Circle to Central America.
Learn more on the Nordic
Ware Industrial Coating site.
Choosing respirators, filters, and cartridges that fit your Teflon™
coating shop’s needs is very important because respirators come in many
shapes and sizes. You must make a decision between disposable
or reusable respirators, and you must make sure that the respirator is equipped
with the correct cartridge or filter for the respiratory hazards in your work
environment.
Both disposable and reusable respirators can be used to protect you from many harmful
substances. But it’s most critical to make sure you are using the right filter
or cartridge. For dusts, fumes, and mists, use a particulate filter, and for
gasses and vapors, use an appropriate chemical cartridge. Intech offers
all the Teflon™ supplies you need for coating Teflon™ in its online
Shop.
Particulate Filters
- Dusts: Created by sanding, dusting, or
sweeping some materials.
- Fumes: When metal is heated to its boiling
point, then cooled again quickly, there will be fumes.
- Mists: Little drops of a sprayed
material that stay in the air.
Chemical Cartridges
- Gases: Particles that diffuse freely to
fill the container or area they are in.
- Vapors: Created when liquids evaporate
(changing from a liquid state to a gaseous state) or solids sublimate (changing
from a solid state to a gaseous state, bypassing the liquid state all together).
Cartridge Care
A respirator cartridge starts working from the moment you open the
package it was shipped in, whether it is being used occasionally or constantly.
The environment in the facility will determine how long the wearer of the
cartridge is protected from the airborne toxins for which it was designed to
shield him or her from.
There are recommended procedures that management can use to evaluate the
environment, estimate cartridge expiration, and replace in time to assure the
coater’s safety. The cartridge wearer cannot determine when the cartridge
has expired because toxic air has no telltale taste or smell.
Disposable Respirators
Disposable
respirators usually only have particulate filters and are relatively
inexpensive. The benefits of disposable respirators are comfort, lightweight
composition, adjustable straps, and overall economy. Particulate
respirators will filter up to 10 times the applicable exposure limits only
for general dust, steel/manganese alloys, stainless steel, aluminum, and
galvanized steel. Do not use particulate respirators for cadmium or lead. Popular
disposable respirators are the 8210 model, which is
$16.99 for a box and the 8511
respirator, which is $24.99 a box.
Reusable Respirators
Reusable respirators can use either particulate filters or chemical
cartridges in half and full facepieces, but you can replace filters and cartridges
as they’re useful life expires. Filters and cartridges are available for many
applications, and many styles can be adapted to PAPR or Supplied Air Respirator
setups. Popular reusable respirators are the 3M 6000 series and 7000 series,
with cartridges that will filter up to 50 times the exposure limits for all the
contaminants listed below.
The Health Risks
The contaminants listed here have severe potential effects if you
are exposed to them:
- Steel/Manganese Alloys can cause
pneumoconiosis, siderosis, and central nervous system harm.
- Stainless Steel can cause pneumoconiosis,
kidney damage, lung irritation, and cancer.
- Aluminum can cause respiratory irritation.
- Galvanized Steel can cause metal fume
fever.
- Cadmium can cause metal fume fever,
respiratory irritation, kidney damage, and lung cancer.
- Lead can cause central nervous system
harm and systemic poisoning.
Of the eight Teflon™ coating properties, nonstick
and FDA-compliant may be the most familiar to consumers because of their use on
baking pans. But most consumers probably have no idea that that there
are
21
FDA-compliant Teflon™ coating systems
.
According the FDA
website
: “It is the responsibility of the manufacturer of
a Food Contact Substance (FCS) to ensure that food contact materials comply
with the specifications and limitations in all applicable authorizations. When
reviewing your composite formulations to determine compliance, consider each
authorization to be composed of three parts: the
identity of
the substance,
specifications including purity, or physical
properties and
limitations on the conditions of use.”
In the simplest terms, FDA compliance means that any material that
might contact food is inert and safe for human consumption. Teflon™-compliant
systems also offer temperature resistance, release, lubricity, and durability
for a multitude of applications such as baking molds, food production, food
assembly lines, and packaging lines. FDA-compliant Teflon™ coatings are
available in water and solvent based liquid formulations as well as powder.
Official FDA Regulations on Coatings
The Food and Drug Administration (FDA) Regulation
21.CFR
(and specifically Part 177) governs
components of coatings for direct food contact. Each category of the Teflon™
fluoropolymers has coating systems that, when applied correctly according to
Fact Sheet instructions, are FDA-compliant. (
Here’s a handy
printable list
.) When checking the Fact Sheet, check under
the “Food Contact” subhead to confirm FDA compliance.
One important thing to note is that when using a multiple coat
system, all the components (primer, mid-coat, topcoat) must be FDA-compliant in
order for the system to be FDA-compliant. And if your coating is
FDA-compliant, it is also technically USDA-compliant, but the USDA requires a
special letter from the applicator.
For more information on the USDA compliance process, contact the Intech
Services technical team at
302-366-8530.
Polyurethane foams are used in construction for insulation, sound
absorption, various types of padding, and structural reinforcement. Outside of
construction, polyurethane foam is an integral part of household appliances,
automobiles, packaging, and footwear. The Teflon™
coating properties that allow for excellent release are
non-stick, low coefficient of friction, ease of cleaning, and FDA compliance.
Polyurethane Molds
The polyurethane
molding industry has long relied on manually applied release
agents on their metal molds for rubber or plastic components during the
manufacturing process. The procedure of applying these release agents is both time-consuming
and expensive. Teflon™ coatings are now offering long-term solutions that
completely replace release agents for a variety of the products used in polyurethane
molding.
When maintained properly with regular cleaning, Teflon™ coatings
can perform through thousands of molding cycles. Removing release agents offers
significant benefits to polyurethane foam manufacturers in the form of enhanced
compliance with environmental regulation, improved safety conditions for
employees, reductions in product defects, and the complete elimination of dry
ice blasting.
Polyurethane Processing
Teflon™ coatings are also now being used to coat polyurethane mixing
blades for easy cleaning and extended service life of the blades. Hardened
foam quickly builds up on the steel mixing blades, and the processes for
removing it can be very time-consuming and labor-intensive. One case
study saw polyurethane foam production increase dramatically. By
cleaning quickly between mixes with methylene chloride and paper towels, the
company was able to accomplish up to 13 mixes in a single day.
When
coating services employees’ hands are in contact with hazards, employers must
require the proper hand protection to be worn. To figure out which kind of
glove works best for hazardous environments such as surface blasting and
Teflon™ coating, coating services companies must evaluate the gloves’
protection requirements relative to the tasks being performed, and consult
industry standards for safety.
The
Occupational Safety and Health Administration, or OSHA, has the general
requirements for selecting appropriate gloves (Standard
1910.138 – Hand Protection). This standard covers protection selection requirements when
hands areexposed to
hazards such as those from skin absorption of harmful substances, severe cuts
or lacerations, severe abrasions, punctures, chemical burns, thermal burns, and
harmful temperature extremes.
The
American National Standard for Hand
Protection Classification is another guide for selecting appropriate gloves. The document
gives test methods
and classification levels for many glove characteristics. It also has pass/fail criteria
for hazardous exposures, such as chemical permeation, detection of holes, and
heat and flame resistance. Here we review common high-temperature gloves that
should be part of your Teflon™ coating supplies, and the
basics of sizing and maintenance.
Gloves
that Take the Heat
For
applications where high heat protection is the top priority, Kevlar®
gloves
are often the answer. The looped construction of Kevlar traps air, making these
gloves excellent insulators. The fabric also gives greater durability and cut
resistance than regular string knit work gloves. Other high-temperature
gloves
include reversible mitts, Flextra® unlined heat resistant gloves, and heavy
duty olive drab flame retardant knit wrist gloves.
Gloves
with Permeation Resistance
Butyl gloves have the highest permeation
resistance to gases and water vapors of any other glove material. They offer
excellent resistance to methyl isobutyl ketone and methyl pyrrolidone, found in
thinners TN-8595 and TN-8718. Blasting gloves protect hands and arms from high
pressure particles, and welders gloves include options such as reflective
aluminized leather back wool-lined gloves.
Glove
Maintenance
Regular
glove maintenance is important in ensuring employee hand protection. Proper
care can also save you money by extending the life of each pair. Proper glove
maintenance focuses on three main areas: cleaning, inspection, and storage. Each
pair should be inspected for damages on both the inside and outside prior to
use, and all gloves should be kept in well ventilated containers away from
direct sunlight.
Glove
Sizing and Cuff Types
When
choosing gloves for workplace safety, two key factors that should always be
considered are glove size and cuff style. Choosing appropriately sized gloves
is as simple as measuring the circumference of your hand just below the
knuckles.
- XSmall: 6” to 7”
Hand Circumference
- Small: 7” to 8”
Hand Circumference
- Medium: 8” to 9”
Hand Circumference
- Large: 9” to 10”
Hand Circumference
- XLarge: 10” to 11”
Hand Circumference
Cuff
Listing Terms
- Knitwrist: Prevents debris from entering the
glove, keeps cold air out and warmth in, fits under clothing sleeves
- Slip On: No cuff, easy to put on and off,
primary use for general purpose applications
- Safety Cuff: Length varies from 2.5″ –
2.75″, gives added protection to forearms
- Rolled beaded Cuff: Increased
strength and protection from chemical droplets
- Gauntlet Cuff: Typically
4.5″ or longer, greater upper wrist protection
- Serrated Cuff: Better
gripping on surface edge for easier glove removal
- Band Top: Allows air circulation, light wrist
protection
- Straight Cuff: Addition
length to protect from chemical runoff
Release agents comprise any substance that helps a container
“release” whatever it is holding easily and without residue sticking to the container.
The most common release agents are oils that keep surfaces slippery and
“non-stick.” Of course, oils can be messy, costly, and a safety risk. A variety
of chemical formulations are also used, but all have similar drawbacks.
Teflon™ coatings remove release agents from the equation by
providing the same release performance in a more permanent way. The Teflon™coating properties that allow for excellent release are non-stick,
low coefficient of friction, ease of cleaning, and FDA compliance. The most
common places where Teflon™ coatings successfully and economically replace release
agents are in the molding industry.
Industrial Plastic Parts Molding
Teflon™ coatings cut manufacturing costs by eliminating release
agents and reducing product defects. Teflon™ coatings provide a more permanent,
nonstick, repeatable high-release solution for processes across every molding
industry segment. Popular
Teflon™ coating lines for molding include FEP, FEP Teflon
S
one-coats, and PFA coatings for
higher operating temperatures.
Medical Device Parts Molding
The majority of the medical industry molding market is represented
by the makers of medical instruments, pharmaceutical processing, and packaging.
Applications where Teflon™ coatings can replace release agents are in the
manufacturing of medical waste trays, surgical handles, forming mandrels, pill
molds, gel cap molds, centrifuge baskets, lab equipment, and dental molds.
Packaging applications include material handling, blister pack forming, and heat
sealing.
Molding Industry Resource
The Society of Plastics Engineers (SPE) unites
plastics professionals worldwide, helping them succeed and strengthening their
skills through networking, events, training, and knowledge sharing. The SPE’s ANTEC®
2020 conference is the largest, most respected and well-known technical
conference in the plastics industry. The next conference is March 30 to April
2, 2020, in San Antonio.
Polyurethane Molding
For more specific details on the Polyurethane Molding industry, read this blog post.
All products and parts used in the
aerospace industry have to be proven safe through rigorous testing and high
production standards. Aerospace parts from small fasteners to wire insulations
to fluid gaskets must stand up to demanding operating conditions for extended
periods of time.
Teflon™ coatings used in the aerospace
industry are highly specified, highly qualified, and resistant to a wide range
of stresses. They offer durability and toughness for an industry with unique
needs. Here we’ll review Teflon™ product lines commonly used in aerospace as
well as pertinent SAE standards and aerospace standards resources.
Teflon™
for Aerospace
The combination of many Teflon™ coating
properties make these coatings particularly robust for aerospace. Teflon™ PTFE and
FEP coating systems are among the most popular in the industry.
PTFE 851G-2XX and 852G-2XX are ideal systems for aerospace applications
requiring thermal stability and superior coefficient of friction. The acid primers
850G-204 and 850G-314 offer high
lubricity in a thin film. Acid primers are usually used under a PTFE Topcoat,
but the acid primer alone is useful in some applications such as fuel filter
screens.
FEP One Coats (954G-3XX and
959G-2XX) are also well-suited for aerospace because of their durability and
high service temperatures of up to 425° F. And the FEP system of 953G-506 (primer) and 953G-401 topcoat provides premium release
properties with good chemical resistance. Toilet bowls on airplanes are often
coated with this FEP system so the toilets use less water, planes carry less
water, and planes use less fuel.
Call Intech Services for more technical
details at 302-366-8530.
Common SAE
Standards:
- AMS2515H PTFE
Resin Coating, Low Build, 370 to 400 °C (698 to 752 °F) Fusion – This
specification establishes the engineering requirements for producing thin
coatings of PTFE (with acid primer) on parts and the properties of such
coatings.
- AS 9100D Quality
Management Systems – Requirements for Aviation, Space, and Defense
Organizations – This standard includes ISO
9001:2015 quality management system requirements and specifies additional
aviation, space, and defense industry requirements, definitions, and notes.
- AS12500 Corrosion
Prevention and Deterioration Control in Electronic Components and Assemblies – This
specification covers corrosion prevention and mitigation aspects in Avionics,
Electronics, and Electrical Wire Interconnect Systems. (Replaced MIL-HDBK-1250.)
- AS7489 Standard
Requirements for Aerospace Organic Coatings Applicator Certification – This
standard establishes the minimum requirements for training, examination, and
certification of aerospace coatings application personnel applying liquid
organic coatings to interior structural or exterior substrates.
Aerospace Coating Resources:
- Aerospace
Industries Association–The National
Aerospace Standards (NAS) are voluntary standards developed by the aerospace industry.
- Aerospace Standards Overview by ASTM – Compiled by
a number of ASTM International committees covering aircraft construction and
parts manufacturing.
- The Gardner-Sward Handbook – This “Paint
and Coating Testing Manual” is a valuable guide to standards of many national
and international organizations.
- IAQG-OASIS
Database – The Online Aerospace Supplier Information System (IAQG-OASIS) is a
reliable source for aerospace supplier certification and registration data.
- Nadcap
– Nadcap is the leading worldwide cooperative program
of major companies designed to manage a cost-effective consensus approach to
special processes and products and provide continual improvement within the
aerospace and defense industries. And here’s an FAQ Page on Nadcap
Accreditation by Boeing.
One common manufacturer’s specification
not listed is the Boeing BMS10-146 material specification, which outlines
application and performance requirements of Teflon™ 958G-203 One-Coat. This is not a
public standard, but one you should be aware of nonetheless.
Of the many quality
assurance tools that a coating services supplier should have on hand, coating
thickness gauges are one of the most important for maintaining
high-quality coatings that both perform properly and meet external standards.
Another substantial benefit is cost savings, as keeping coatings consistently within
specifications can reduce material and labor waste. And you should consider
whether the time savings of a tester
that measures continuously at 140 times per minute is worth the investment
to prove your coatings are consistent.
Coating thickness gauges (aka paint meters or mil gauges) are used
to measure dry film thickness without leaving marks on your parts. These are a “non-destructive
testers” with great repeatability in measurements. Dry film thickness is
probably the most critical measurement in the coatings industry because every
coating has thickness range specifications. A coating thickness gauge provides
vital information that can confirm the expected life of the substrate, the
coating properties’ performance, the coating appearance, customer expectations,
and the job’s compliance with international standards.
Managing
Coating Expectations
Many jobs in the Military and Aerospace segments require
verification of the work that you are performing. Suitable coating thickness gauges
are certified by the all the applicable ASTM Standard test methodologies, which
allows you to compete in markets that are sensitive to these specifications. Thickness
testers can also compile the measurements you take and deliver a formal report
that can be shared with the end user.
Most quality shops lay out pass/fail expectations of their customers before
accepting their order, and more end users these days are requiring proof of
testing. Coating thickness gauges demonstrate to your customers that the
coatings were applied to the thickness they requested. This will help you
eliminate rejects and take your customer satisfaction to new levels.
Incorporating thickness measurement into your everyday processes also
saves on material costs. Monitoring coating thickness will drive your coaters
to better control thickness and eliminate excessive wasted coating. As an
example, if you purchase $10,000 in coatings a year and improve your thickness
control by .5 mils, you would save $2,552 a year.
Save Money with Better Technique
By using these simple techniques, you’ll be able to cut out the
waste as well as achieve a better, more consistent finish for your Teflon™
industrial coatings.
- Plan of Attack: Have a plan before pulling the trigger. Plan to attack trouble
spots and difficult to reach areas first.
- Spray
Distance: The spray distance is based on the spray equipment,
coating, complexity of the part, and spray environment. By keeping the gun at
the same distance from the part the entire time you’re spraying, you can
improve the consistency of the film thickness over the whole part. Increasing
the gun distance increases the pattern fan size, and the coating thickness
decreases as it is distributed over a larger area.
- Gun Angle: Maintain
controlled gun angle to the part. Yaw and pitch spray angles will result in a
non-uniform spray pattern distribution, causing inconsistent film thicknesses.
- Spray Pass
Overlap: Each spray pass should overlap 50% to 75% of the previous
pass. Overlapping below 50% results in “striping,” or variations in the film
thickness. The more you increase the overlap, the thicker the coating, so
overlapping above 75% requires more spray passes and more coating.
- Spray Pass
Speed: Adjust the spray gun speed to achieve consistent films.
Before pulling the trigger, consider the coating flow rate and the target wet
film thickness. Adjust the equipment before spraying to find a flow rate that
lets the applicator move at a controllable, comfortable speed. Spraying too
fast can lead to decreased film thickness, and sometimes extra coats will be
needed to make up the deficit.
- Trigger
Control: Maintaining a consistent trigger pull on each spray pass directly
impacts the flow rate, spray pattern size, and transfer efficiency. Start
triggering immediately before the lead edge of the part and release the trigger
immediately following the lag edge. Fully pulling the trigger provides constant
flow rate control. The fluid knob on your spray gun can be adjusted to restrict
the trigger travel distance so you can always pull the trigger all the way.
Partial triggering, however, can be very useful for blending and touching up.
- Edge
Banding: Partially pull the trigger to spray a light coat around the
edges of the part. Then spray the center of the part, blending the edges into
the first coat. Banding can increase transfer efficiency and increase film
thickness on the edges. This technique ensures the edges get coated completely
while maintaining consistent film thicknesses.
If you’re looking for more tips on keeping your Teflon™ coating
services at the highest quality consistently, read our other blogs on “Basic Quality
Testing” and “Advanced Quality
Testing.”
We usually list the total number of Teflon™
coating properties at eight. The Dry Lubrication property also goes by
“Lubricity” and “Low Coefficient of Friction.” To the layman, this Teflon™
property might sound a lot like “non-stick,” but there is a significant
functional difference.
Non-stick means that almost no solid substance will adhere to the
surface. Dry Lubrication, on the other hand, refers to how easily a coated
surface will slide over another surface. The most common Teflon™ coatings used
for high lubricity in industrial applications are PTFE
one-coats in the 958G line (-303, -313, -404, and -414).
Dry Lubrication and Friction
Friction is the force created when two objects rub together and
motion is hindered. With a Teflon™ industrial coating, the “coefficient
of friction” is generally lowered to a range of 0.05 to 0.20, depending on
the load, sliding speed, and type of coating used. Dry Lubrication is very
important in any application that has moving parts touching each other
frequently or with significant force.
Teflon™ PTFE one-coats are superior dry film lubricants with
smooth and slick finishes fusing to substrates with strong adhesion to provide
great durability. These industrial coatings are excellent for minimizing
friction and galling, as well as preventing seizing, especially where
re-lubrication with fluid is not possible or there is exposure to dirt or dust.
PTFE one-coats are often used in the automotive, aerospace, and oil & gas industries
because of the ideal combination of Teflon™ properties available under different
grades of durability and thickness.
958G Teflon™ Coating Properties
The popular 958G PTFE
line provides high heat resistance to operating temperatures of
up to 500 degrees F. These solvent-based coatings are also easy to apply for a
number of reasons. They apply in one coat, cure schedules can be flexible, they
have superior adhesion, and cleanup is painless.
The thin-film 958G-303 version is an industry standard and has
been used for dry lubrication for many years. The 958G-313 version, introduced
in 2016, is also a good option because it is more durable than -303. For
thicker film applications (up to 4 mils DFT) with high lubricity, we recommend
using 958G-406 (black) or -414 (dark green).
A “Make-or-Buy” decision is when you wonder if you’ll save money
by fabricating parts in-house instead of purchasing them pre-made from a supplier.
In a Make-or-Buy decision, the most important factors to consider are availability
of production capacity, labor costs, material costs, and total time.
A Teflon™ coating or powder spraying shop may decide to purchase any
part if it is cheaper to buy or if the shop does not have sufficient production
capacity to produce it in-house. The Make-or-Buy decision is one that managers
and shop owners must consider frequently in order to keep operational costs as
low as possible.
The following is an example of a cost analysis for the Make-or-Buy
decision that analyzes industrial hooks, assuming
that the shop has sufficient production capacity. We took hook part number
C-4076 as a typical example. This hook is a standard “C” style
hook that is 4” long, made of 0.076 wire that can hold up to 20 lbs.
We’ll consider how much it might cost to produce 2,000 hooks, which is a standard
shipping quantity.
“Make” Costs
- Wire cost: $30 (1,420 feet of 0.076 diameter
wire; 8.5” long hard drawn spring steel wire to produce 4” long standard “C”
style hooks)
- Cutting time: 4 hours (500/hr.)
- Forming time (2 ends per hook): 5 hours (400/hr.)
- Employee pay rate: $12 per hour
- Labor cost for 2,000 hooks: $108
Total Cost: $138 ($30 wire cost + $108 labor)
“Buy” Costs
- 2,000 pre-made C-4076 hooks: $67.60
- Shipping: $8.55
Total Cost: $76.15
Savings from buying hooks vs. making them in-house:
$138 – $76.15 = $61.85 (45% savings)
The above cost analysis for buying vs. making hooks in-house shows
that it is more cost effective to purchase the C-4076 C-style standard hooks
rather than to produce them in-house.
Manufactured from hard drawn spring steel, these hooks survive
repeated stripping and offer higher loading capabilities than mild steel
hooks. These hooks are ideal for wider parts or multiple styles of parts
with varying thicknesses. For maximum loading and repeated usage, ensure the
product being hung seats into the bottom of the “C.”
The speed of any food production line is only as fast as the
slowest station in the line. This can vary by the type of food processing—e.g.,
bread, cookies, bread, dairy—so the ways Teflon™ coatings can help vary from
product to product. And because so many Teflon™ coatings are FDA-compliant, there
are always options to fit any particular set of performance needs.
Industrial Baking
The high-release and non-stick properties of Teflon™ are well
known in the consumer bakeware category, but these properties also apply very
well to industrial baking in a number of capacities. Speed is important to
maintain profitability, so bakers are always looking for an edge. Higher baking
temperatures can mean shorter baking times, but there is a limit to continuous
use temperatures in fluoropolymer coatings.
FDA-compliant Teflon™ coatings such as PFA and PTFE come in
varieties that can maintain peak performance through repeated cycles of 500° F (260° C). Both single-coat and multiple-coat options are available.
For multiple-coat systems, each “layer” (including primer layer) must be
FDA-compliant independently in order for the complete coating system to be
FDA-compliant.
Teflon™ coatings also help keep food products of all kinds moving
down the line at speed on conveyors, down channels, through feeders, and into
packaging. It is frequently used on industrial food processing equipment such
as mixers, feeders, cutting blades, molds, guide rails, and die rollers.
Before Baking
In other baking applications, a Teflon™ coating can replace oil as
a release agent when storing and moving products, such as bread dough, prior to
baking. Dough troughs are large bins that store bread dough temporarily in
commercial bakeries. The problem is that when the dough rises it becomes sticky
and it is difficult to remove from its trough.
One common solution is to spray the entire surface with vegetable
oil so that the dough will slide out easily when ready. But the high volume of
oil can be costly and messy, can affect taste, and can become a safety issue.
Applying Teflon™ coatings on dough troughs can reduce oil consumption and cleaning
times dramatically.
Other food applications:
- Cheese
Production – Teflon™ coatings eliminate the problematic buildup of dried
cheese crust.
- Fast Food
Restaurants – Teflon™ coatings help reduce recoating frequency on cooking
equipment.
- Potato
Chip Manufacturing – Teflon™ coatings help reduce residue build-up by
coating knives used to cut potatoes, resulting in less downtime and lower
cleaning and maintenance costs.
- Pineapple
Processing (and similar high-acidity products) – Teflon™ coatings reduce
corrosion caused by acidic juices, reduce need for lubrication with
food-grade oil, and result in improved replacement frequency levels due to
longer life of the housings.
Here’s a complete printable list of FDA-Compliant
Teflon™ Coatings, and here’s a competitive
analysis of FDA-Compliant One Coats.
Intech Services congratulates PerformaCoat Inc. in Houston for
becoming the newest Teflon™ Industrial Coatings Licensed Industrial Applicator
(LIA). To become an LIA, a company must meet a list of criteria and
qualifications as well as prove the quality of workmanship of its services.
PerformaCoat’s customer service mission provides what customers
need—when they need it—using multiple ovens, multiple paint booths, and an
isolated grit blasting area. The PerformaCoat staff understands the pivotal
role coatings play in manufacturing. They embrace the opportunity to exceed
customer expectations while developing trustworthy and long-lasting client
relationships.
Learn more on the Performacoat
website.
Both the powder and liquid versions of Ruby Red PFA Teflon™ coatings are excellent chemically resistant options because of their high permeation resistance to both liquids and gasses. This permeation resistance is a result of the proprietary filler materials in Ruby Red Teflon™ coatings that you won’t find in other PFA coatings.
In the chemical industry specifically, Ruby Red has proven to hold up longer than other alternatives against extremely corrosive chemicals at temperatures as high as 500° F. The advanced technology of the Ruby Red coating allows it to be applied in multiple layers at 3 – 10 mils per coat—and up to 40 mils total.
Ruby Red PFA coatings require high oven curing temperatures, as high as 750 – 800° F, and the chemical industry parts coated with Ruby Red tend to be large. Ruby Red is used most often on aluminum, steel, cold-rolled steel, and stainless steel products.
Ruby Red Liquid vs. Powder
The main differences between Ruby Red liquid and powder are the maximum thicknesses and the curing times for each. Because of the differences, liquid Ruby Red PFA is more often used when coating larger parts.
Liquid Ruby Red can achieve thick film builds, up to 10 mil per coat and a 40 mil maximum dry film thickness (DFT). The powder Ruby Red has a lower maximum DFT of 20 mil. However, Intech and Chemours do not recommend pushing those upper limits when avoidable.
Liquid Ruby Red also requires longer cure times, up to 3-hour final bakes, while the powder Ruby Red has shorter cure times. Powder coating is applied electrostatically with hot flocking for additional coats. One other advantage of the liquid coating is that it is water-based for easy cleanup.
Ruby Red Best Practices
The length of active service life for Ruby Red PFA depends greatly on the quality of the initial coating. Here are some tips for keeping that coating quality high:
- Blast profile depth is VERY important to anchor Ruby Red coatings
- Make sure to rotate parts for DFT uniformity and to prevent sagging
- Oven temperature uniformity is vital for long-lasting performance
- Slow part temperature ramp up can help prevent blistering
- Lower the cure temperature 15° F for each additional coating of Ruby Red
- A clear liquid or powder PFA seal layer prevents leaching and discoloration
The main considerations for choosing masking tapes
for your coating jobs is the tape material, the temperature the tape will be
exposed to, the thickness, and the residue the tape might leave behind. Many
tapes can now perform under very high temperatures—even over 500 degrees F—and
still leave little or no residue.
Below we’ll review some of the most popular masking
tapes for Teflon paint and powder coating in each of four temperature ranges.
It’s also important to remember that many tape types also come in precut “disc” versions for convenience.
Low Temperature: 0° – 325°F
The common industrial-grade “crepe” tape available
at most hardware stores will only perform well up to 225° F, though there is a High-Temp Crepe Tape for applications up to 325° F. The
advantages of the High-Temp Crepe Tape are the thickness (7.5 mil), the ability
to handle corners, the lack of residue, and the low price. In addition, 3M
offers material and color options in this low temperature range,
including crepe, vinyl, aluminum foil, and lead foil tapes.
Mid-Temperature: 325° – 425°F
Polyester is the most popular material
for this temperature range (up to 400° F) because it is thin, extremely
economical, and removes cleanly from surfaces without leaving a residue. Available
in green (2 mil), red (1 mil), and blue (1 mil). These
polyester tapes are the industry standard for general purpose powder
coating, e-coating, anodizing, plating, and painting.
High
Temperature: 425°–
500°F
The most common tape for Teflon™ paint is a polyimide
tape often known by the name Kapton®. Kapton can withstand ovens up to 500°
F, adheres well to any surface, and removes cleanly from surfaces without
leaving a residue. It has an amber color and is available in 1 mil or 2
mil thicknesses.
Glass Cloth, or fiberglass tape, is also commonly
used for Teflon™ coatings and other high-temperature (up to 500°
F) coating processes such as thermal spray and plasma spray. It is very
abrasion resistant, which makes it ideal for a grit blasting mask. It
adheres well to any surface and removes cleanly from surfaces without leaving a
residue.
Aluminum/Glass Flame Spray Tape is another high-temp (500° F) tape that
combines strong fiberglass cloth with aluminum foil and is coated with special
silicone adhesive. This tape has high reflection to radiant heat and good flexibility
for plasma spray masking, grit blasting, and extreme temperature coating.
Very High
Temperature: Over 500° F
The High-Temperature Aluminum Foil Tape from 3M
is a shiny silver, 3.6 mil aluminum foil backing with silicone adhesive used in
many high-temperature applications. This tape provides good holding, splicing,
patching, or general protection. It is also flame resistant and meets requirements
of F.A.R. 25.853(a). The performance range is from -65° F to over 600° F. As
the adhesive thermosets at high temperatures, the adhesive mass becomes firm,
gradually losing its pressure sensitivity while still holding the tape in
place.
The spray gun is a key component to achieving an excellent Teflon
paint or powder coating finish, but spray guns
are far from maintenance-free. Cleaning your spray gun regularly is important to
avoid slowdowns—or stoppages—in production. One way to prevent problems
with your spray gun is to have repair
and cleaning kits for your guns on your shop floor.
The small investment in repair and cleaning kits can prevent
major maintenance bills or the cost of gun replacement. If you’re cleaning your
spray guns regularly but still are encountering issues, refer to the
troubleshooting guides below to get back on track.
COMMON GUN ISSUE TROUBLESHOOTING
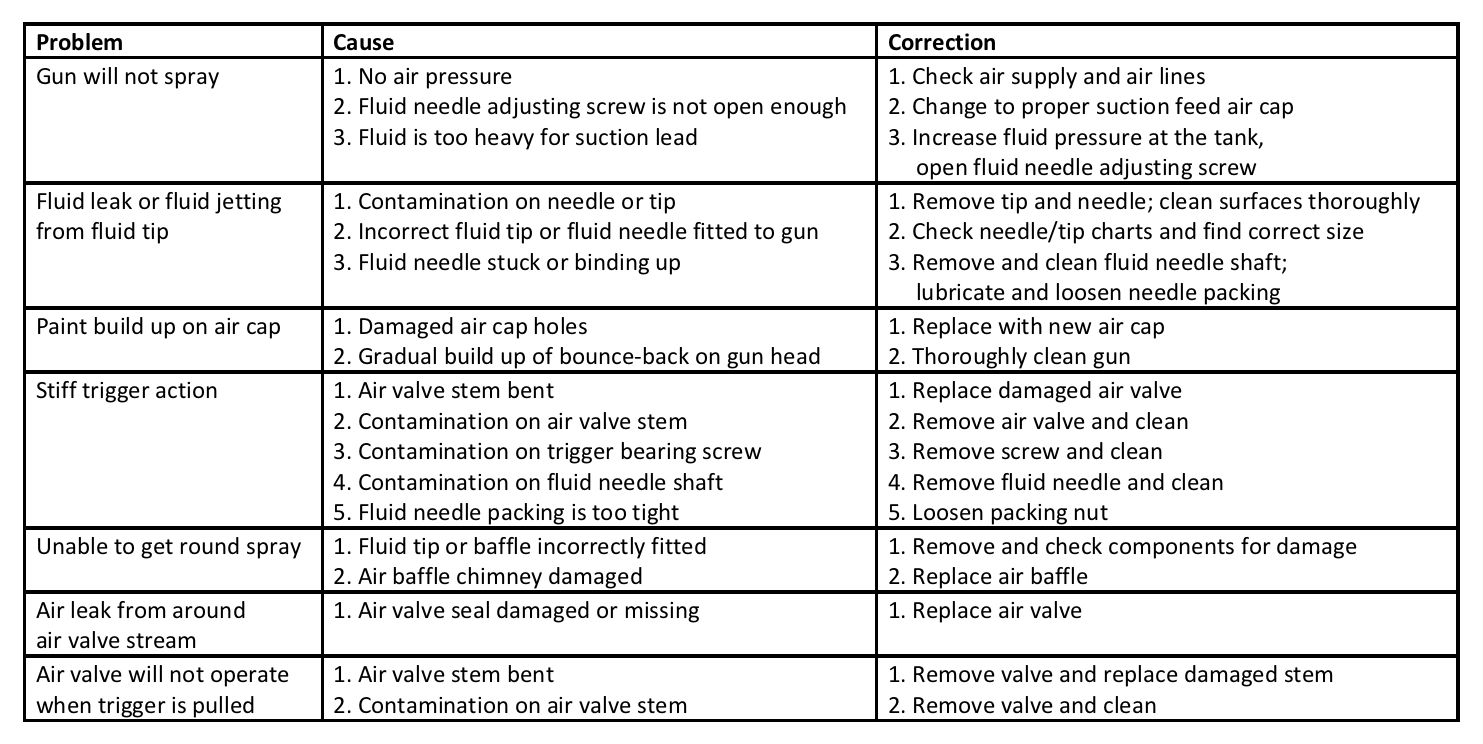
INCORRECT SPRAY PATTERN TROUBLESHOOTING
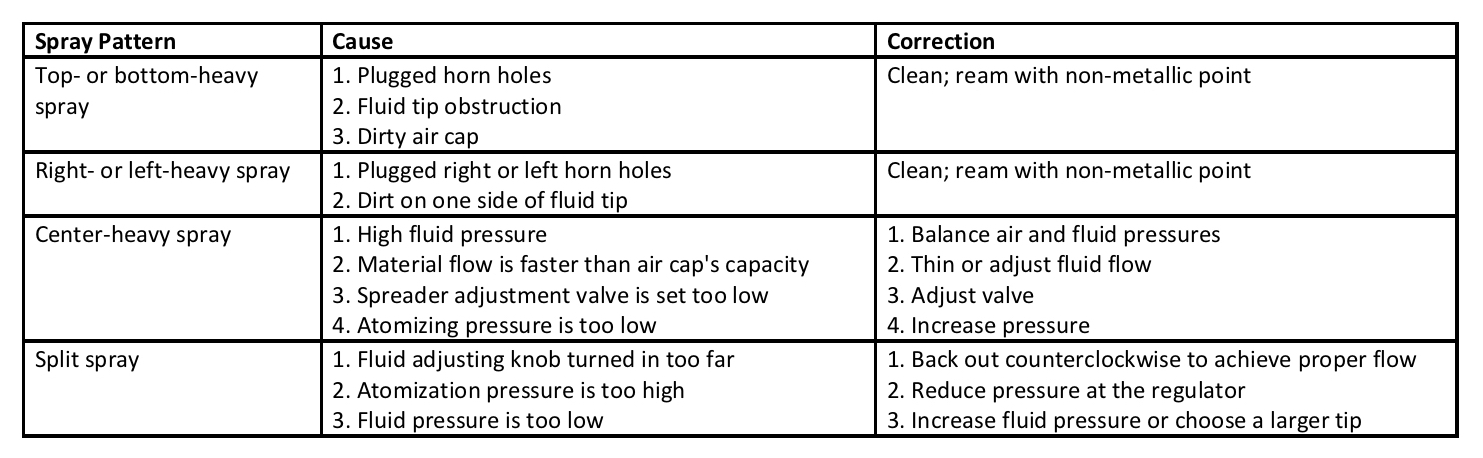
The
“Faraday Cage effect” happens when coating charged parts with sharp
inside corners or recesses during an electrostatic coating process. The
“effect” prevents powder from a gun from getting into those corners and
recesses because they do not hold a charge. The difference in charge causes the
charged powder particles above the corners and recesses to create resistance to
incoming powder—the Faraday Cage—making it difficult to coat these areas.
While
it might be impossible to prevent the Faraday Cage effect from occurring
completely, there are ways to overcome it. Here are three “levels” of strategies
and tips that will help you better coat inner corners, recesses, and many parts
with odd geometries.
Level One – Overpower Faraday Cage effect:
- Use
slotted tip to concentrate the spray
- Blast
powder into recesses
- Increase
the powder flow rate
- Maximize
the gun to part distance
Level
One Tradeoffs – These strategies can use excessive amounts of powder, have
higher film thicknesses than desired, and could result in an uneven film build.
Level Two – Fine-tune the gun settings:
- Use slotted tip to concentrate the spray
- Decrease powder gun flow rates
- Reduce
gun voltage to 40-60 Kv
- Maintain
gun-to-part distance of 8-10 inches
Level
Two Tradeoff – These gun settings could mean slower
application times.
Level
Three – Modify spray technique for unavoidable Faraday Cage:
- “Finesse”
the powder into corners and recesses
- Spray corners
and recesses of a part at obtuse angles
- Reduces
air turbulence
- Allows for
deeper penetration
- Minimizes
early back ionization
- Utilizes
more lines of force
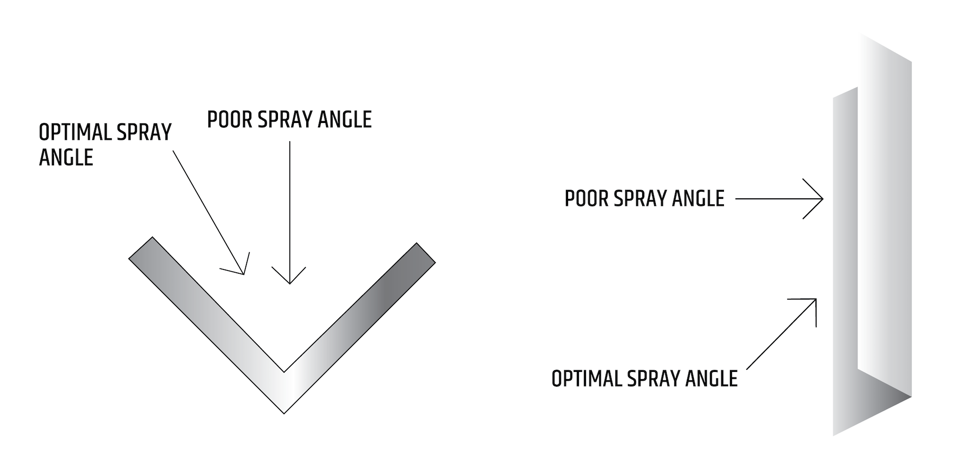
For
more information about how to fine-tune your application settings and
techniques, read TCI Powder’s Troubleshooting
Guide,
especially Chapter 10, “Powder
Application Tips,” and Chapter 13, “Troubleshooting.”
…And
more application tips…
https://fluorogistx.com/teflon-application-overview
Like any paint, the liquid components of Teflon™ coatings tend to
separate gradually over time. Intech Services and Chemours® recommend mixing
all Teflon™ coatings before using and, when not being used regularly, mixing those
containers every 30 days. The 30-day recommendation ensures that the Teflon
coating will be usable for its entire shelf life, or even longer.
The Preferred Mixing Method
When we say “mix” we usually mean “roll,” but
always consult the
Teflon™ Fact Sheets in the “Handling and Storage” section. Some coatings may tolerate
mixing blades, but most times blade mixers and shakers are too aggressive and
can separate the fluoropolymer from the solids. Teflon coatings are sheer
sensitive, so mixing and shaking can damage the coating and adversely affect the
performance and quality of the cured coating.
Rolling both water- and solvent-based Teflon™coatings ensures proper
“reincorporation” of the solids in the coatings for consistently high-quality
applications over the product’s shelf life. For thorough reincorporation of the
solids, the container should be rolled before the first use each day for 30
minutes at 30 RPM. When coating intermittently throughout the day, 10 minutes
at 30 RPM each time is sufficient.
Intech Services supplies
Paint
Rollers
specifically designed for mixing Teflon™ paint. Constructed of solid
steel bars and a reinforced fiberglass base, these rollers can operate at variable
speeds and accommodate a variety of container sizes. You set the desired RPM
and a timer and the paint roller will turn off automatically after the time has
expired.
Paint Roller features include:
- Fits
1-gallon cans or jugs and 5-gallon pails of Teflon coatings
- Can
roll two gallon cans at the same time
- Variable
speed selection
- Set
rolling time up to an hour
- Automatically
turns off when timer is done
- Explosion-proof
motor
- 120
V, 60 Htz
- Solid
steel bars, cast in urethane and precision ground
- High
quality reinforced fiberglass base with wide footprint for stability
- Cover
is gloss white and easy to clean
- Dimensions:
36” wide X 16” deep X 14” high; 5” between bars
- Roller
Bars are a total of 25” long (22” of rolling surface)
Sometimes when rolling, solids stay stuck to the bottom of the
container. If you notice this problem, stop the roller and use a stainless
steel blade to scrape the solids from the bottom of the container, then
continue rolling again. To make sure the solids are fully reincorporated,
test the
viscosity
.
How Long Are Teflon™ Coating Shelf Lifes?
All Teflon coating
Fact Sheets contain
the specific maintenance, handling, and storage information for the Teflon coating
process for that specific product. Shelf life is the amount of time, starting
from the date the coating was manufactured, that a coating can be stored and
still be fit for use. Each Teflon industrial coating line has a different shelf
life, but 12 to 18 months is typical.
Most Teflon paint should be stored at room temperature, but some
have special storage instructions that will keep a coating ready to use during
its full shelf life. For example, the acid primer 850G-204 needs to be
refrigerated. When in doubt, always refer to the Fact Sheet for specific
instructions about storage and rolling. Fact Sheets are always available online
under the “
Technical
Literature
” section of IntechServices.com.
The
best type of spraying application method for any particular Teflon™ coating depends
upon a number of factors. That’s why we recommend you
always consult
Teflon Fact
Sheets
for both “preferred” and “not preferred” methods. Fact sheets outline Teflon
properties and can even be as specific as what kind of gun to use, the best
nozzle size, or what the ideal air pressure range should be, for instance.
Teflon
coatings are usually applied with commercial spray techniques in a hood or well-ventilated
area. You should keep water-based and solvent-based spray guns separate and not
use one for both. Many coatings are shear sensitive, and the action of the
needle moving in the fluid tip of the gun can cause coagulation. Minimize this
coagulation by keeping the fluid delivery open and altering the fluid delivery
by regulating the pressure on the pressure pot.
Manual
Spray
More
often than not, Teflon can be applied manually with compressed air and standard
spray equipment. All spray equipment should be made from aluminum or stainless
steel or coated with Teflon S. Transfer lines should be chemically inert and
solvent resistant (e.g. Teflon tubing, polyethylene, or stainless steel). Air
lines must be trapped to prevent oil or water from contaminating the compressed
air or the product.
Manual
Spray Application Tips:
- Maintain a normal distance from the gun to the
part of 4-12 inches (10-30 cm). If the gun is too close, the finish will look
rippled. If it is too far, the spray will be dry and rough.
- If you’re still getting ripples or rough
finishes, reduce the atomizing pressure.
- The spray guns should be held perpendicular to
the piece using a flat, rectangular motion of the spray gun.
- “Whipping” the gun in an arc tends
to make the wet film bubble and will cause excessive beading on the edges of
the part.
Automatic
Spray
Automatic
spray guns are generally used in large volume, conveyorized systems, where the
parts to be coated are uniform in shape. While the set-up requires experience
and careful adjustment, films can be applied more uniformly and at a faster
rate. The finishes are fed to the guns through pressure pots with fluid
pressures in the range of 5-8 psi (0.5-0.6 kg/cm2). Where flat items are
carried on a flatbed conveyor, the spray guns may reciprocate transversely and
spray continuously.
Electrostatic
Spray
Electrostatic
guns or discs are suitable for the application of many Teflon coatings. The
advantages of electrostatic application include better film uniformity and 10%
to 15% savings in material, due to the reduction in overspray. High volume
production is usually required to justify the expense of automatic
electrostatic systems, but relatively low-priced hand units are available.
Airless
Spray
This
technique uses high pressures to atomize and direct the coating material. Since
the opening of the gun tip is generally smaller in diameter than in
conventional compressed air spray, shear conditions during spray may be too
high for aqueous Teflon products. Airless spray is generally used when coatings
must be applied in deep recesses.
Powder
Coating
Teflon
powder coatings are free-flowing powders which are applied with conventional
electrostatic powder equipment, with either spray guns or fluidized bed. The application
voltage and technique depends on the particular equipment, although the highly
attractive nature of the powder permits a wide range of application voltages.
What
about Multiple Coats?
Many
Teflon coatings can be applied in multiple coats. This process requires careful
attention to bakes of intermediate coats to prevent deterioration of underlying
coats. The opportunity to apply multiple coats also depends on the wettability
of the intermediate coats. This property varies considerably depending on the
product. Consult the Fact Sheet for the product you are using to see if it can
be applied in multiple coats.
To
view Teflon Fact Sheets and other Teflon Technical Literature, please
login or register for an account.
Additional
Resources:
Chemours-recommended
“Guide for the Safe Handling of Fluoropolymer Resins”:
https://www.plasticseurope.org/en/resources/publications/108-guide-safe-handling-fluoropolymer-resins
Chemours
introduction to Fluoropolymers:
https://www.chemours.com/Teflon/en_US/assets/downloads/pdf/teflon-introduction-fluropolymers.pdf
SPI
Guide for Safe Handling of Fluoropolymers:
https://fluorogistx.com/its-assets/SPI_Guide_for_Safe_Handling_of_Fluoropolymer_Resins.pdf
…And
more application tips:
https://fluorogistx.com/teflon-application-overview
Breakout
torque is the force required to loosen a securely tightened—and corroded—nut or
bolt. If threads are sufficiently corroded, that torque might be two or three
times the tightening torque.
Breakout
torque is important because service costs in the Oil & Gas industry can
rise when equipment and hardware seize up from excessive corrosion. Servicing
engineers often have to use a torch to loosen or remove nuts. When coated with
Teflon™, those same nuts and bolts can maintain consistently low breakout
torque for many years, or even decades.
What
is Lubricity?
Lubricity
refers to the functionality of a smooth, dry surface. Teflon is said to have
lubricity because it provides low friction resistance with a dry coating.
Lubricity is a function—or characteristic—of a surface’s low coefficient of
friction. Friction is the force that hinders motion when two objects rub
together. The coefficient of friction with Teflon coatings is generally in the
range of 0.05 to 0.20, depending on the load, sliding speed, and type of
Teflon.
Lubricity
is very important in any application that has moving parts touching each other
and reapplying oil or grease is not easy. For example, in the automotive and
aerospace industries, springs, clamps, and clips are coated with Teflon
coatings to avoid wearing down the part and to reduce squeaking.
Generally
speaking, Teflon PTFE coatings have the lowest coefficient of friction—or
highest lubricity. For fasteners, lubricity means that the surface retains a
certain release capability, even at high torque under harsh conditions. Many
industries look for long-term fastener protection while having uniform lubricity
and breakout torque release that also lasts a long time.
Other
Benefits of PTFE Systems
Teflon
PTFE coating systems are versatile coatings for carbon steel, stainless steel,
and aluminum. There are thin and thick film build options, and the strictly
water-based formula allows for easy clean-up.
Color-coding
of fasteners is also important in utilities such as waterworks to identify the
function of the pipe, for instance, that requires servicing. Teflon ideal for
fasteners is available in blue, red, yellow, and black in the PTFE 857G product
line.
Making spray booths work exactly the way you want can be a
challenge because of space and ventilation constraints. Spray booths can take
up a lot of space on shop floors, so finding the right spot that will also vent
exhaust properly is key. Also important are choosing the right type of spray
booth, installing proper ventilation, replacing paint filters regularly, adjusting for unusual jobs, and keeping
an eye out for poor airflow issues.
Types of Spray Booths
There are four main categories of spray booths:
- Open Front
Spray Booths offer a safe and clean environment for any type of finishing
operation for both batch and conveyorized production systems. Airflow is drawn
in through the open front, across the work area and exhausted through a filter
bank in the back of the booth.
- Open Front
Bench Booths are a structural variation of Open Front Spray Booths with
similar airflow that are also suitable for both batch type and automated
production systems. Conveyor pass-through openings can be as much as 25% of the
booth open front area, without requiring additional exhaust fan capacity.
- Batch Powder
Booths have an open front design that is ideal for powder applications. Air
is drawn in through the open front of the spray booth and passes through the
booth’s working area into the filtered exhaust plenum. The air is filtered in
three stages and discharged back into the room.
- Cartridge
Batch Powder Booths also have an open front design ideal for
small- to mid-size powder applications. To ensure cartridge filters remain
clean, the booth has a purge control feature, which assures the safe operation
of the coatings enclosure by maintaining the airflow at design levels.
Fans, Ducts, Controls, and Extension Kits
Spray booth exhaust fans typically run at speeds in the thousands
of cubic feet per minute (CFM) range. To accommodate that airflow, common
ductwork comes in diameters ranging from 12 inches to 48 inches in
six-inch increments. These size ranges can also be found in 45° and 90° elbows,
duct cleanout doors, and automatic roof ventilators. To gain even more control
over airflow, you might consider motor starters, multi-fan control panels, and
VFD control panels.
If you need to expand capacity, you don’t always need to install
an entirely new spray booth system. You can economically upscale your business
with spray booth “extension kits” customized to handle the particular equipment
being coated within your spray space limitations. Instead of paying to make
permanent changes for a temporary job, extension
kits offer a more flexible alternative that keeps your work space
versatile while maximizing productivity.
Preventing Powder Drift
Even if you have installed all your spray booth systems correctly,
you may find powder drifting out of your spray booth openings. Here are some
possible causes and solutions of this unwanted issue.
- Cause: Insufficient
airflow through the booth and the recovery system.
Solution: Position
powder guns away from booth openings and check air volume control.
- Cause: Cartridge
filters are not failing to receive adequate cleaning.
Solution: Increase
air pressure or the volume.
- Cause: Cartridge
filters at end of life.
Solution: Replace
cartridge filters.
- Cause:
Final filters clogged.
Solution: Check the
final filters for leakage; repair or replace filters as needed.
Salt spray testing is used to ensure long-lasting coating performance in a number of industries. For instance, the Oil & Gas industry often requires salt spray testing to confirm that fasteners (nuts, bolts, etc.) are being coated properly to be used in particularly harsh environments, such as on oil rigs in the ocean. The end-user can require assurance—and certification—that the parts that a coater is supplying will be both corrosion resistant and perform well many years down the road. The results of the salt spray testing supplies that assurance and certifcation.
Salt Spray Testers are closed cabinets that continually introduce a salt water (5% NaCl) solution to parts via a mist or fog. Spray nozzles atomize the salt water with pressurized air, accelerating a corrosive environment for test parts.
One Teflon™ product line that does particularly well in corrosion-resistance and salt spray testing for Oil & Gas industry parts is the PTFE 857G product line. These coatings have low coefficient of friction, anti-galling, and dry lubrication properties that are ideal for the Oil & Gas industry. The 857G coating system is available in blue, red, yellow, and black.
Other one-coat Teflon products that have excellent salt spray resistance for industrial applications would be FEP Teflon S One-Coats. These user-friendly thin film options are a combination of fluoropolymer with binder resin and are thermally set:
- 954G-303 – Black (Epoxy Liquid)
- 954G-304 – Green (Epoxy Liquid)
- 958G-203 – Black (Polyamidimide)
- 959G-203 – Black (Polyamidimide)
- 959G-204 – Green (Polyamidimide)
- 959G-205 – Brown (Polyamidimide)
The Teflon 857G coating system is comprised of two coats: a sacrificial base coat of electroplated zinc or ceramic/metallic coating, and a fluoropolymer top coat applied by a qualified applicator. The coating is water-based, low VOC, and easy-to-use, applied at .0005 to .0045 inches thick by conventional spray or dip-spinning. When tested according to the ASTM B117 Standard, fasteners coated with 857G-018 (blue) showed less than 10% rust after 3,000 salt spray hours, and VOC emissions were less than 3.0 pounds per gallon. Find Authorized 857G Coaters here, or become an Authorized Coater yourself here.
Teflon™ in the Molding Industry cuts manufacturing costs by
eliminating release agents and reducing product defects. Teflon coatings
provide a more permanent, nonstick, and repeatable high-release solution for
processes across every molding industry segment.
Here’s how to choose the right coating for your molding project:
- Need superior release for end-use temperatures
up to 400° F? Use FEP
- Is your end-use above 400° F? Use PFA
- Prefer a one-coat with excellent durabilty? Use FEP
Teflon S
Teflon coatings in the molding industry offer secondary benefits
such as improved product quality and consistency, enhanced process efficiency, less
scrapped material, and reduced labor costs. The benefits also include a safer
work environment, reduced mold/tool maintenance and wastewater.
One growing molding market segment is using Teflon in the polyurethane
molding industry. Again, Teflon removes the necessity of
release agents while also offering enhanced compliance with environmental regulations,
improved safety conditions for employees, reductions in product defects, and
the complete elimination of dry ice blasting. Teflon can also be used to coat
polyurethane mixing blades for easy cleaning.
Key Benefits of Teflon™ industrial coatings:
- Nonstick
surface
- High
thermal stability
- Low
coefficient of friction
- Corrosion
and Chemical resistance
- Compliance
with health standards
For more resources on Teflon for the molding industry, see our “Markets”
page on Molding.
Today’s powder coatings offer more performance qualities than ever before. They are highly functional and durable while also being affordable, safe for workers, and safe for the environment. Powder’s superior film properties simply can’t be found in many other finishes.
This post is the second in a two-part summary of The Benefits of Powder Coating. The first part (1/31/19) covered the Performance, Mechanical, and Production benefits of powder coatings. In this second part, we’ll look at and examine the Economic, Safety, and Environmental benefits of powder coatings. Through its TruPak small package program, Intech Services offers over 300 of the most popular powder coatings in 1, 3, 5, and 10 pound boxes.
Economic – Lower Overhead
95% of the powder is used when powder coating, and any loss and overspray of powder can be reused. A powder coating plant has less equipment overhead and labor overhead than other finishing systems, and safety requirements are lower because solvent-free means fire-safe.
Safety – Healthy Workplace
Powder coatings are also safer because these coatings no longer contain chemicals such as solvents and VOCs, which can be harmful to the health of workers. And cleaning powders off hands and arms no longer requires industrial hand cleaners—only warm water.
Environmental – Less Waste
Aside from reducing chemicals released into the environment, the powder coating process also reduces waste. There is little to no overspray and no powder escapes into the atmosphere. The minimal waste after coating is not hazardous and can be safely disposed of in landfills.
Much of the improved application efficiency of powders vs. liquids can be summed up by “transfer efficiency.” That is, the wrapping effect that powders have when electrostatically applied. In addition, powders are readily available and usable from the start without having to mix the powder with solvents or other materials.
For further information, here is a flyer on the “6 Primary Benefits of Powder Coating.”
There are two categories of quality tests that can be performed on Teflon™ coatings after they have been applied. The first category we call “Basic Quality Tests,” which we covered in the January 18th blog post. The basic quality test category includes Visual Inspection, Finger/Coin Test, Holiday/Spark Test, and Dry Film Thickness Test.
The second category of quality tests for industrial coatings includes more advanced tests that require specialty equipment. These quality assurance tests can measure the quality of the bond of the coating to the substrate, the quality of the gloss finish, and the accuracy of your final color. And, you can increase the quality consistency by testing the viscosity of your coatings and confirming that your oven is calibrated and operating correctly.
Cross-Hatch Tape Adhesion Test
This test provides an instant assessment of the quality of the bond to the substrate either in your shop, your lab, or in the field. Cross-hatch gauges are ideal for thin, thick, or tough coatings on all surfaces. The critical measurement is the amount of pressure (in PSI) required to detach the coating from the substrate. This test is often used to comply with the ASTM D3359-02 standard.
Gloss and Color Testing
Digital gloss meters use an infrared source that emits a beam of light at an angle to the surface, and a sensor measures the reflected light. The standard test is usually a 60-degree light beam angle, and high-gloss surfaces are measured with a 20-degree angle. Advanced color testers can differentiate between over 16,000,000 colors. They are portable devices that can also include gloss testing in a single tester.
Viscosity Testers
The correct viscosity of Teflon coatings is a critical element to make sure that the coating is fresh and properly mixed. Viscosity testers are either glass tubes or stainless steel cups. The glass tube models measure the time a stainless steel ball takes to drop through the liquid. The cup viscosity testers have a hole in the bottom that the coating passes through. The viscosity measurement is calculated from the time it takes before the first break in the liquid stream.
Oven Testers
To make sure that you are baking your Teflon to the correct temperature, you should make sure your oven is calibrated correctly. And to prove your oven is operating correctly, you can also use an oven data logger.
Teflon coating systems only perform properly when all the specified processes are followed to a “T.” To make sure your industrial coatings will perform in the field, keep quality assurance testing equipment close at hand.
The
benefits of Teflon™ in food processing are well-known, from large-scale food
production to a family’s home cooking. They offer highly repeatable release from
pans and molds, do not require the use of release agents, are designed to
withstand the high temperatures required in cooking and baking, and are
extremely durable. Teflon-coated bakeware and food processing products are able
to withstand hundreds if not thousands of repeated uses before showing signs of
degradation.
All
four major Teflon coating types—PTFE, PFA, FEP, and ETFE—have FDA-compliant
options. All of these options offer high release consistency, high thermal
stability, and wear and corrosion resistance. Here’s a list of the most popular
FDA-compliant coatings. These Teflon coatings, when fully cured, will comply with U.S.
FDA food contact regulations. Check the fact sheet for your specific coating to
confirm FDA-compliance.
The
industrial Bakeware, Cookie, Cracker, and Cheese industries are particularly
strong markets for Teflon application growth. The food industry as a whole is
stable and mostly insulated from swings in the U.S. economic outlook. And
today’s industrial food processers are in such high-volume facilities, with
many food contact parts, that there are often untapped opportunities for Teflon
applications to be discovered there.
Key
Benefits of Teflon™ industrial coatings:
- High
thermal stability
- Nonstick
surface
- Low
coefficient of friction
- Corrosion
resistance
- Compliance
with health standards
For
more resources on Teflon for the Food Processing industry, see our “Markets”
page on Food Processing.
Today’s powder coatings offer more performance qualities than ever before. They are decorative, functional, and durable—all at the same time. Powder’s superior film properties simply can’t be found in many other finishes.
In this first blog of a two-part series, we’ll examine the Performance, Mechanical, and Production benefits of powder coatings. In the second blog to be posted next month, we’ll outline powder coating’s Economic, Safety, and Environmental benefits. Through its TruPak small package program, Intech Services offers over 300 of the most popular powder coatings in 1, 3, 5, and 10 pound boxes.
Performance – Twice As Thick
Powder coatings are twice as thick as standard liquid finishes. That’s right, twice as thick. This thickness provides better adhesion and stronger corrosion protection. At the optimal thickness, a powder coating provides the durability to withstand continuous day-in-day-out use under tough environmental conditions. If you’re looking for a finish that will stand up to the elements and improve adhesion and corrosion resistance, powder coating is your top choice.
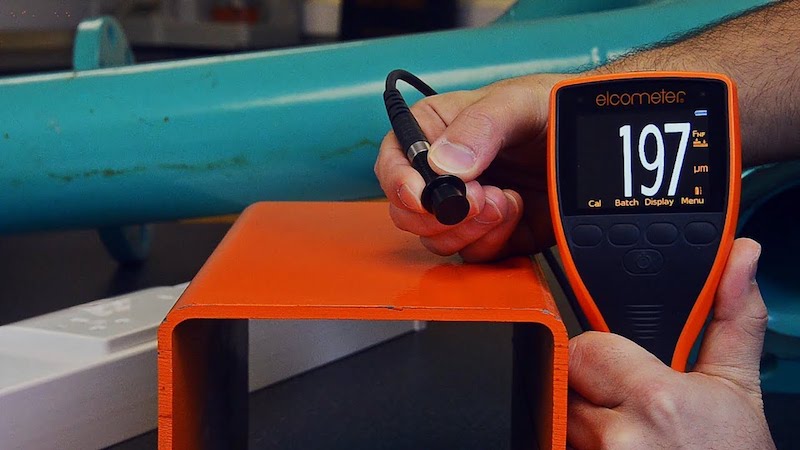
Mechanical – Durable and Decorative
Powder coatings are increasingly resistant to chemicals, weathering, chipping, and scratching. The resistance stems from the thermal bonding process during curing that is unlike any other finishing process. The thermal bonding process delivers longer-lasting vibrancy of color, and the flexibility of powder coatings lets them bend and yield along with the material they are applied to. Flexibility is often ideal in the transportation industry where products often vibrate and twist out of necessity.
Production – Shorter Processing Times
Lower bake temperatures are expanding both the materials that can be coated and the options for coating properties. Processing times stay low because there is no flash off without a solvent, and powder coatings can be done curing within 20 minutes of leaving the oven.
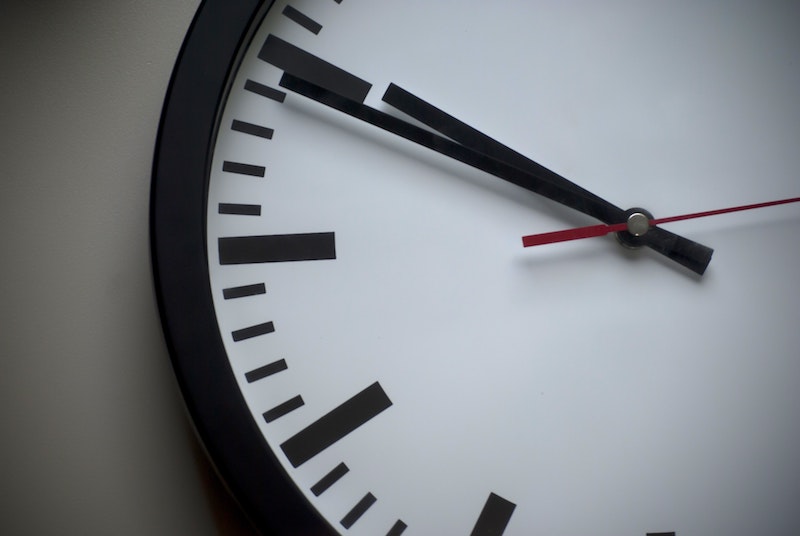
There are several other production benefits of powder coating. Generally, powder is readily available and usable from the start without the necessity of mixing the powder with solvents or other materials. With correct application, powders create an almost perfectly smooth coat while other finishes tend to run, drip, and chip in the process. The last production benefit is the reduction of energy requirements. There is no energy required to evaporate a solvent or evacuate it from the oven.
Here’s a flyer on the “6 Primary Benefits of Powder Coating.”
There are two categories of Quality Tests that can be
performed on Teflon™ coatings after they have been applied. The first category we’ll
call “Basic Quality Tests,” which are
four straightforward tests to gauge the quality of the coating application. Every
industrial coating shop should have equipment on hand to perform these basic
tests.
The second category includes more “Advanced Quality Tests” that
require specialty equipment, such as the Cross-Hatch Tape Adhesion Test. We cover these advanced quality tests in more detail in a post published on March 12, 2019.
The Basics
The four Basic Quality Tests for high-temp coatings like
Teflon are Visual Inspection, Finger/Coin Test, Holiday/Spark Test, and Dry
Film Thickness Test.
A Visual Inspection
is just what it sounds like—a thorough inspection for any defect in the coating
with your eyes. For a more thorough inspection, use a high-illumination
flashlight, magnifier, or microscope.
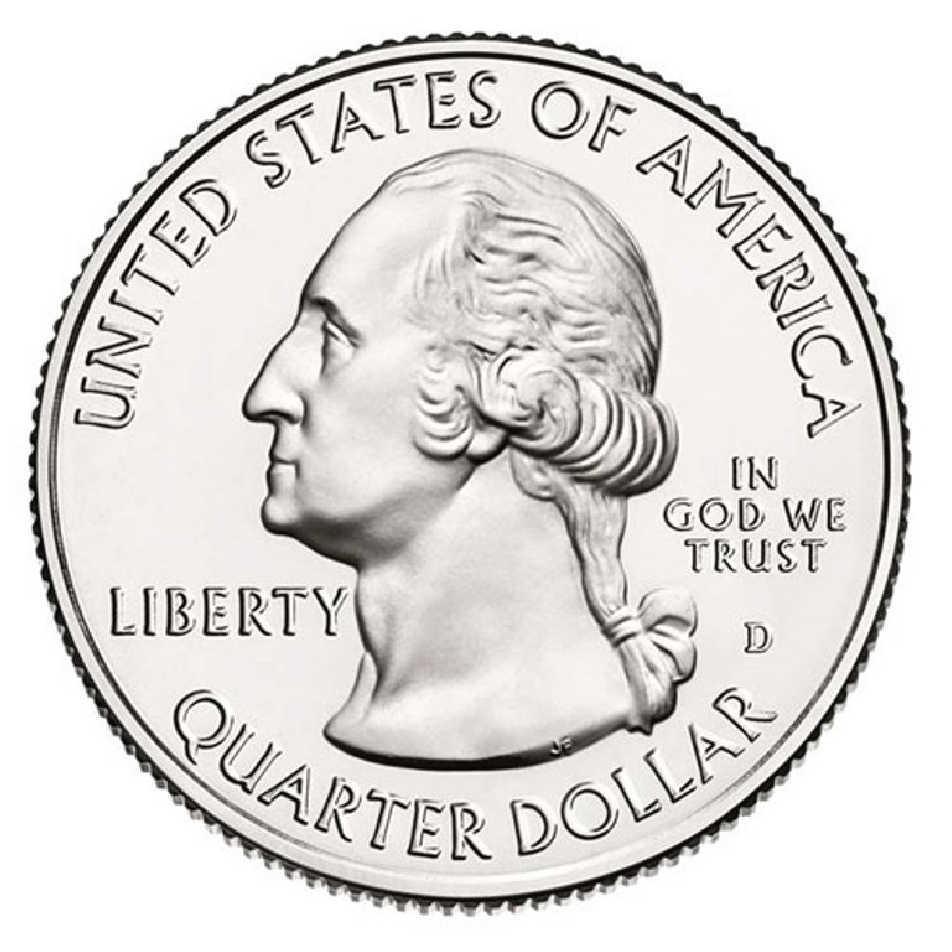
The Finger or Coin Test confirms proper intercoat and
substrate adhesion. After the curing process of the topcoat is complete, run
your fingernail or a nickel over the coating with moderate force to check if the
topcoat will peel. Another version of this test is performed after coated panels
are immersed in boiling water for 15 minutes.
To test porosity and flammability, use the Holiday/Spark
Test. This is a dry film porosity test that utilizes an electronic transmission to identify the presence of a porous film. Any positive result received during the test indicates porosity in the coating.
The Dry Film
Thickness Test uses an instrument to precisely measure the dried thickness of the coating system. A high-quality
thickness gauge provides accurate readings with great repeatability to ensure coatings are applied within the required specifications.
The aerospace and automotive industries have highly specific
needs and require exhaustive testing before a product can be finalized. Chemours
and Intech are proud to supply these industries with superior Teflon™ coatings
for countless integral parts.
The aerospace
industry has seen the founding of the privatized space sector and
the expansion of established companies into near-space flight. Products used in
the aerospace industry have to stand up to rigorous testing and demanding
operating conditions. As such, Teflon coatings used in the aerospace industry
are highly specified, highly qualified, and resistant to a wide range of
stresses. Commonly coated aerospace parts are fuel molds, toilets, gaskets,
bearings, fasteners, clamps, and clips.
The automotive
industry, with its vast network of
suppliers, is an enormous one, because every car has about 30,000
parts. To succeed, Teflon coatings have to stand up to corrosion, salt spray,
constant abrasion, and NVH (noise, vibration, and harshness) challenges, while
providing dry lubrication and working seamlessly alongside fluids specific to
the automotive industry. The most common auto parts that Teflon is applied to
are brake shims, brake clips, tie rods, piston skirts, springs, and clamps.
Teflon coatings offer durability and toughness for both of
these expansive industries. The most common coatings for aerospace are FEP and
PTFE, and the most common ones for automotive are Teflon S One-Coats and ETFE. Discover
more about Aerospace
and Automotive
common coatings and important Teflon properties under the Markets menu tab on IntechServices.com.
Sun Coating Company has worked on projects in every industry
and its staff has acquired the knowledge and reputation that comes with such a
long and varied resume. They often take products all the way from prototyping
to full-scale, high-volume production. Sun Coating’s proficiency with a myriad
of application techniques means they are always ready to experiment or face new
challenges.
To learn more, check out their website.
Precision Coating engineers innovative surface modification solutions to enhance the value and performance of highly engineered devices and instruments, applying Teflon™ industrial coatings in applications such as semi-conductor components.
If you want to learn more, check out their website, https://www.precisioncoating.com.
It means you have “In Stock” options at Intech Services! The
Ethylene Chlorotrifluoroethylene (ECTFE) polymer is most frequently used to
provide chemical resistance in heavy-duty applications. ECTFE is manufactured under the brand name Halar®
by Solvay, an international company headquartered in Belgium.
The shortage of ECTFE has been caused by industrial sector
demand in Asia, raw material scarcity, and production limits in certain parts
of the world. Effective ECTFE replacements are Teflon™ ETFE coatings.
ETFE coatings have excellent chemical resistance along with being exceptionally
tough and abrasion-resistant, and are manufactured under the brand
name Tefzel®.
ETFE has a maximum continuous service temperature of 300° F
and melts at 520° F. This nonporous Teflon™ offering has high dielectric
strength and good release properties. There are FDA-compliant offerings for
food applications, but not for cooking. Acceptable Tefzel options to be
considered as ECTFE replacements would be either 532-6410 or 532-63XX with a
DFT range of 6 mil to 40 mil.
For more on our ETFE products, call us directly at
302-366-8530 or ask a question on our Contact Us page.
Endura Coatings has been in business for nearly 50 years, so
they are confident their staff can perform virtually any coating job you could imagine.
Endura has coated for nearly every industry, and their work is as likely to be
found in a cutting-edge hospital as it is in your kitchen at home. Endura always
works closely with clients to determine the best coating solution for the particular
specifications of the project at hand.
To see more, check out their website.
Not only does Newco Industrial Services do excellent coating
work, where they deal with the automotive, textile, and food and beverage
industries (among many others), they’re very active in their local community. They’re
always working with local and international groups to provide fundraising and
awareness to causes close to their hearts. When you work with Newco, know
you’re supporting a community-focused business.
Learn more about them and their initiatives on their website.
The Impreglon Surface Technology Group is a great example of
how Teflon™ has grown into an international product. Impreglon has 37 coating
sites spread across 15 countries in North America, Europe, Asia, and Australia,
making it an LIA with considerable reach.
Our main contact is with their site in Fairburn, Georgia.
It’s gotten a lot of attention over the years and is now a 35,000 sq. ft.,
state of the art coating facility. They’re always turning out great coating
jobs on time and in every industry you can think of.
If you want to know more about Impreglon and what they can
do for you, take a look at their website.
Keco Engineered Coatings, Inc. is quickly approaching its
40th year in business, an impressive milestone no matter what industry you’re
in. All that time, they’ve been devoted to improving the quality and
performance of their customers’ products using their coating expertise. They’re
a great company to work with and we’re happy to have them in the LIA program.
We’ve also found consistency in the company across their
divisions. We regularly deal with two different Keco locations and are
confident in saying you’ll get great results from the company regardless of
where you work with them.
Look through their website information on how you can work
with Keco. http://www.kecocoatings.com
By now you’ve probably noticed most LIAs are well
established in the industry, often having a few decades of experience coating
parts of all kinds. Stamar Engineering is no exception. They’ve been at work in
Montebello, California, for more than 60 years and have done work in every
industry that could possibly want something coated. They’re experienced,
professional, and reliable, exactly what you want in an LIA.
Contact them through their website if you’re on the search
for a high quality coater. http://www.stamarindustrialcoatingsla.com
Slipmate is another one of the charter members of the LIA program,
having joined in 1966. They’ve set a high bar for quality for every other LIA
and hold themselves strictly to the standards they’ve set. Without them, it’s
possible the LIA program would have never gotten off the ground.
Check out Slipmate’s website, https://www.slipmate.com, to see if this
legacy company is a good fit for your next Teflon™ coating job.
Orion Industries has the unique policy of allowing anyone
working on their coating line to stop the process at any point, saying
“the smartest person in the room is three feet from the job.” The
result is a product of exceedingly high quality and a return rate below 1%. We’re
proud to have them in the LIA program.
Explore their website, http://www.orioncoat.com,
to see if their high-quality work is right for your project.
Plas-Tech Coatings became an LIA back in 1981 and have worn
their title proudly ever since. Their handiwork can be found all over North
America, serving needs in cities across the United States, as well as
businesses in Canada, Mexico, and Puerto Rico. They’re part of the reason LIAs
enjoy a great international reputation.
Thank you to Plas-Tech for sticking with us for so long. If
you think they’re a company you might want to work with, check out their
website, here: https://www.plastechcoatings.com.
They’ve already answered almost every question you could think of.
Nordic Ware takes full advantage of FDA compliant Teflon™
products, coating thousands upon thousands of household kitchen products. They
have dozens of pots, pans, Dutch ovens, griddles, and microwaveable products
you can choose from, all coated in high-quality, nonstick coatings.Not to mention their products are extremely
attractive. They wouldn’t be a bad company to go with if you’re looking to
replace every bit of kitchenware you’ve ever bought.
See what they have to offer on their website, here: https://www.nordicware.com.
Cantech Precision Coatings Inc. is a fairly specialized
coater. They pride themselves on the nonstick, conductive EMC, and cosmetic
work they do for the food manufacturing, electronic component, and plastic
industries, respectively. But they’re well rounded and can do the general work
too. No matter what you bring them, they can coat it.
Look through their capabilities on their website, here: http://www.cantechcoatings.com.
It’s always helpful when a company will walk you through
figuring out what coating your project needs, and Pro-Tek Surface Technologies is
always willing to be that helpful. They’ll pull from their years of experience
to make sure you’re getting all the coating benefits you need, without trying
to upsell you on stuff that’s way too expensive, or supply you with cheap
coatings that won’t get the job done. With Pro-Tek, you’ll get exactly what you
need.
Connect with them on their website to find out more. http://protekcoatings.com
Teff-Line Ltd. is another one of our Canadian LIAs. This is
their 40th anniversary, so let’s celebrate by thanking them for being a
faithful LIA and for providing such great service to customers across North
America. Here’s to another 40 years of working with Teff-Line.
To help Teff-Line hit their 80th anniversary, visit their
website to see about giving them your business. https://teff-line.com
Plasma Coatings was founded in 1969 and is quickly
approaching its 50th anniversary. That’s nearly half a century of the highest
quality service and availability.
Everything we told you about their Connecticut location
holds true in Tennessee too. Plasma Coatings is proud of its history, both in its
individual story and as a part of ARCOTEQ and the American Roller Company.
Between the two, you’re looking at 80 years of industrial services from a
trailblazing company.
We’re proud to work with Plasma Coatings and gladly reaffirm
their place in the LIA program. Learn more about them on their website at https://americanroller.com.
For how big their company is, you wouldn’t expect E.L. Stone
Co. to be a family operation. But their team page reads like family road trip
role call, with the name “Micire” filling up the page. They’re devoted to their
company and bring a familial touch other companies can’t replicate.
If you’ve found success dealing with tight-knit, family run
companies before, you might as well keep the streak going with the Micires at
E.L. Stone. Check out their website to learn more: http://www.elstone.com.
Sun Coating Company is yet another LIA that’s ready and
willing to take your product from prototyping to full-scale production. They’ve
worked on projects in every industry and have the knowledge and reputation that
comes with a resume that’s long and varied. They’re also always ready to
experiment with a new challenge and devote time to it every day at their
facility.
Check out their website to see if you’d be able to work
together. http://www.suncoating.com/index.html
Endura Coatings has been in business for nearly 50 years, so
they’re confident their staff can perform virtually any coatings job you could
come up with. They’ve coated for almost every industry possible, and their work
is as likely to be found in a cutting edge hospital as it is your own personal
kitchen. They’ll work with you to figure out the best coating solution to
whatever problem you’re facing.
Their website has even more information, http://www.enduracoatings.com, so
check them out to see if they’re right for you.
One of the most reliable indicators of a company’s
effectiveness is employee turnover. At AST/ACME, there’s next to none. The
average length of employment at AST/ACME is 10 years, meaning that not only has
the company seen all manner of coatings jobs, individual employees have. That’s
the kind of work experience you want when you’re putting your product in
someone else’s hands.
Find out more about AST/ACME over on their website at http://www.astacme.com/index.html.
Matrix Coatings Corp. has been at work in the sunshine state
for more than 50 years. They’ve had a name change or two, but they’ve always
done great work no matter what they were called. They’re constantly looking
ahead and working toward the next coating innovation and we’re happy to have
them as an LIA.
Make sure you consider them next time you have a coating job
that needs doing, and check out there website at https://www.matrixcoat.com to learn more
about them.
We’ve created some great educational resources for our Teflon™
S One Coat product line. Read through it here, or download [Link to 420G One Coat Sheet] it for your convenience.
We’ve created some great educational resources for our Teflon™
S One Coat product line. Read through it here, or download [Link to 959G One Coat Sheet] it for your convenience.
We’ve created some great educational resources for our Teflon™
S One Coat product line. Read through it here, or download [Link to 958G One Coat Sheet] it for your convenience.
We’ve created some great educational resources for our Teflon™
S One Coat product line. Read through it here, or download [Link to 954G One Coat Sheet] it for your convenience.
We’ve created some great educational resources for our Teflon™
S One Coat product line. Read through it here, or download [Link to 857G One Coat Sheet] it for your convenience.
This year, Livingstone Coating Corporation marks its 65th
year in business, an impressive feat for a company in any industry. In all that
time, they’ve had plenty of practice with all kinds of plastic treatment,
blasting, and coating jobs, not least of which is Chemours Teflon™ line. They’re
an LIA who can handle virtually any industrial coating job you throw at them. Look them up if you need a company who can
take you through every step of the coating process.
When Chemours, known at the time as DuPont, first instituted
the LIA program, the Donwell Company was one of the first companies admitted.
It was a good call too, since Donwell’s been applying Teflon™ since 1957. They’ve
held on to the title proudly, and are one of the longest running Teflon
applicators.
Their website, http://www.donwell.com,
is a great resource for anyone who’s in need of an experienced, reliable LIA.
Thermech Engineering Corporation is a unique LIA in that
they’re only one who has worked with NASA to make parts for the Apollo
missions. When a company can confidently say they helped put a man on the moon,
how much better of a testimonial could you possibly want?
They tell you all about their involvement in the Apollo
missions on their website. While
you’re there, you can decide whether or not you want Space Race contributors
working to fulfill your coating needs.
Denmac Industries’ Teflon™ coating capabilities are a
perfect example of the kind of versatility and dedication to job completion
customers can expect from the LIA program. They’ve served customers in every industry,
including automotive, aerospace, cookware, construction, food service, oil
& gas, metal fabrication, and many others. When you work with Denmac, you
get consistent results, highly durable products, and a company who’s committed
to your success.
To find out more about working with Denmac, visit their website. They have plenty of
resources online to help you understand their company.
Crest Coating, Inc. is a mainstay of the LIA program. The
company was founded in 1967 and became an LIA soon after, with a membership
spanning more than 40 years. They’ve seen just about everything this industry
has to offer and they’re helping to push Teflon™ into uncharted territory.
If you have a coating job that needs to be done, check out
Crest Coating. They handle jobs from across the United States and are more than
capable of whatever you need. Click around on their website for some more background
info before giving them a call.
Plasma Coatings was founded in 1969 is quickly approaching
its 50th anniversary.That’s nearly half
a century of the highest quality service and availability.
Plasma Coatings is one of ARCOTEQ’s subsidiaries and part of
a larger effort to offer a robust range of manufacturing services. Before
ARCOTEQ was the American Roller Company, founded in 1938 and a trailblazer in
the industrial services industry. The company prides itself on its history and
its varied, high quality services.
We’re proud to work with Plasma Coatings and gladly reaffirm
their place in the LIA program.Learn
more about them on their
website.
Industrial Fluoro-Plastics has been an LIA for 13 years and
is one of only a handful of coaters out West. They’ve worked in just about
every industry you can think of, include medical, aerospace, food and beverage,
construction, chemical, firearms, oil and gas, and many more.They even have a gallery over on
their website you can go check out to see their handiwork.
We’re lucky to have them and their expertise, so we’d like
to thank them for keeping the coating industry exciting and showing consumers
just how valuable LIAs can be.
Our Pioneer Series is thrilled to introduce you to Dave Ring, Owner of Applied Plastics Co. Inc. Applied Plastics has been in business for 64 years and is a trusted LIA. Read about the company’s origins, evolution, and future interests in this interview.
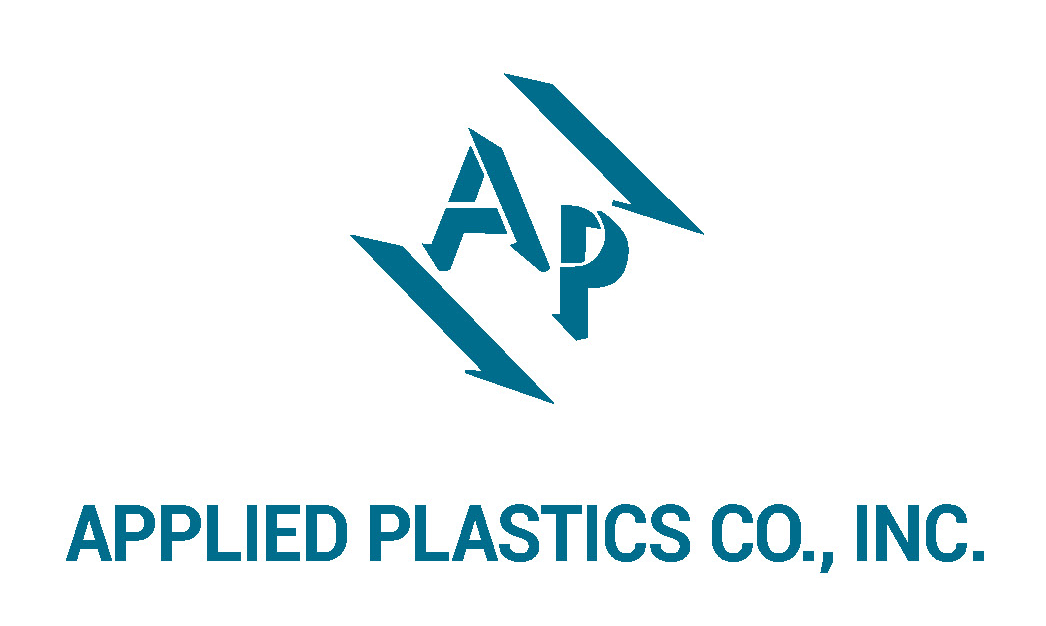
Q: When was your company
founded?
A: 1953 in Norwood, Massachusetts.
Q: Who founded the
company and why?
A: My father, Frank Ring, was the
founder. He couldn’t work for anyone else and wanted the independence of
working for himself. He already had a history in industrial coatings and
decided a move over to Teflon™coatings made the most sense.
Another motivation for starting his
own company was, he was a Type 1 diabetic and had experienced some discrimination
in his career. When he had it, Type 1 diabetics had to keep a strict treatment
routine that many offices weren’t willing to accommodate. Working for himself,
he could build his schedule around the routine rather than be discriminated
against for it.
Q: What was the first
significant piece of equipment you purchased?
A: My father’s first piece was an
old-fashioned pizza oven, which was still around when I started in the late
60s. There was a lot of sentiment attached to the oven, so it was a long time
before anyone did anything with it.
Q: How would you
describe the changes in the company now from when it was first started?
A: For the most part, society changed
more and faster than our company did. Our changes happened a little every day
so no one notices. Then you look back after five or ten years and the company
is very different. Customers’ needs change, so you change to meet them without
realizing you’ve done anything differently. For example, New England industry
went from textiles and rubber to medical supplies. A contract manufacturer like
Applied Plastics has to listen to its customers, so now we do more medical.
Adding computers and new ordering
systems were two of the few big changes we implemented. Another was the
introduction of powdered Teflon coatings or powdered epoxies. When I first
started, we didn’t have those.
Q: What would you
consider significant milestones in your company?
A: Buying that first pizza oven,
moving locations three times, and building our second building, while
maintaining constant production in first building, would be our biggest
milestones. We also developed custom coating equipment a little more than 30
years ago so we could coat customers’ odd shaped parts.
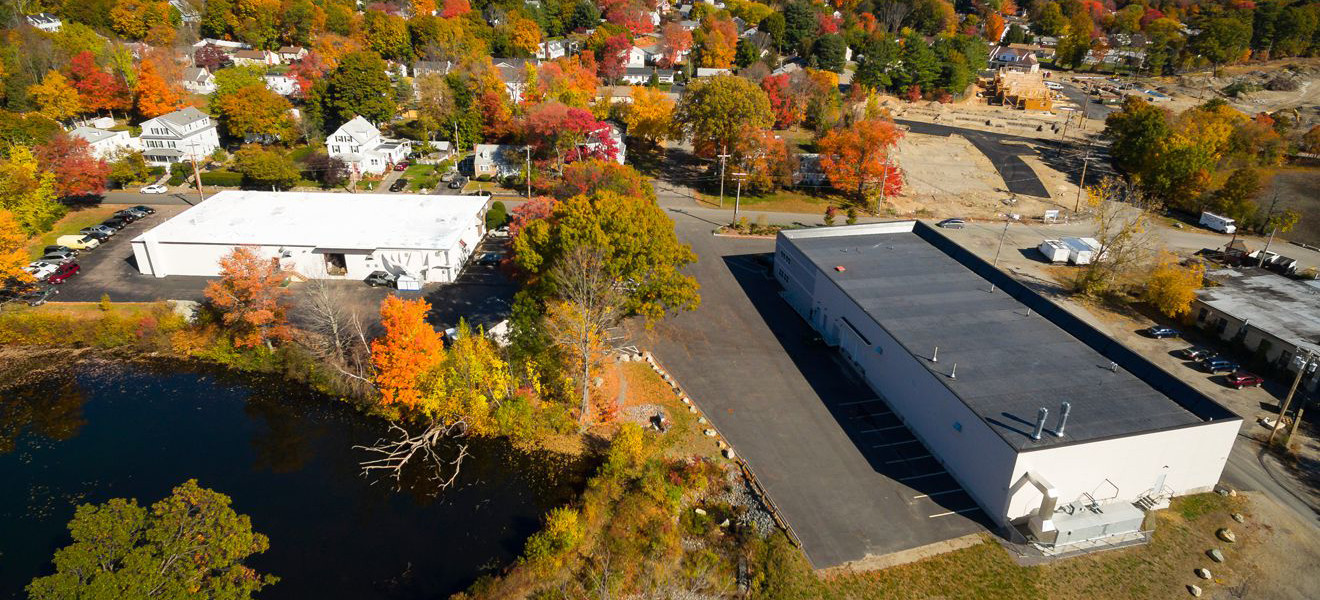
Q: How has the coating
industry itself changed over time?
A: Equipment’s improved, customers’
demands are more rigid, and environmental regulations and worker safety
regulations have changed and gotten stricter.
Overall, we started local, and now we
ship worldwide. There also was no FedEx or faxing when we first started, but we
recently filled an order for a company out in the middle of the Indian Ocean. That’s
how the industry is now. Every contract manufacturer develops their own little
expertise. For example, a Texas company might develop something specifically
for the oil industry, then they’re selling that product to someone in the North
Sea, not just in Texas.

Q: When did you get your
LIA license?
A: Applied Plastics was one of the
originals in the early 60s. A sales rep from DuPont showed up with a plaque and
said the company had a great record and wanted Applied Plastics to start
handling local service and the detailed questions of customers in New England.
Q: How has being an LIA
affected your company?
A: It’s not a bought license. It can
only be earned a good reputation and consistent product. Being an LIA connects
Applied Plastics with great technical information from DuPont (now Chemours),
legitimizes smaller companies, and improves relations with customers, who tend
to listen more attentively if you’re an LIA.
Q: What is your favorite
Teflon coating?
A: The 856 series FEP coating. It has a
great balance between release, chemical resistance, and tolerance. You get good
results without having to build up too thick of a coating.
Q: What excites you
about the future of the coating industry?
A: It’s fun to come to work everyday. Learning
about new applications and solving customers’ problems, as well as seeing how
the company’s going to change day by day is why I look forward to my job every
day.
For more information on Applied Plastics, visit their website here.
Congratulations
to Canadian Coatings of Longueuil, Québec. They’re the most recent addition to
Chemours’ Licensed Industrial Applicator (LIA) program. The LIA program is an elite group of
coating companies that have extensive knowledge of Teflon™ industrial coatings
and experience in recommending and applying fluoropolymers in a variety of
applications. LIAs meet a list of criteria and qualifications as well as quality
of workmanship and are a reliable resource for recommending coating solutions
and applying them to a customer’s specifications.
Canadian
Coatings’ journey to its current LIA status is an inspirational one. It’s their
second time being recognized, as the lack of a succession plan caused the near
failure of the company. But new owners and the partnership of Maxime Biron and
Gary Coons brought the company back from the brink of collapse. Chemours
approved the restoration of their LIA status thanks to years of commitment to
Teflon™ coatings, as well as their willingness to experiment with new products
as Chemours released them.
We
should have known Canadian Coatings was going to make a triumphant comeback
when Mr. Biron came to us at I3 in Chicago, 6 years ago. At the age
of 22, Mr. Biron told us he was going to bring the LIA status back to Canadian
Coatings. After only 6 years, he achieved his goal. We’re proud to have such a
promising young business owner as an example of the quality and conviction of
all our LIAs.
Chemours is transitioning its water-based FEP coatings line, specifically 856G-200 and 856G-204 to 856G-300 and 856G-304; products that are already in production and use in Europe. These two new coatings have improved stability and shelf life, allowing us to supply you with better products that fit your evolving needs. The new 856G-3XX line has a shelf life of 12 months, double that of the previous 856G-2XX line while keeping the same performance characteristics and handling. We’re looking to completely transition to the 856G-3XX line by July, 2018.
If you have concerns or technical questions about this transition, please contact Chris Lord at clord@intechservices.com.
We make it a priority to make sure that our customers know what they are getting. For this reason, we send out coated panels to be lab tested by our buyers. The panels can undergo tests such as crosshatch, release, chemical, and hardness testing. Many other tests can be done with these panels as well, depending on the facility’s unique requirements and quality testing capabilities. After this easy yet important step of testing, customers may buy the amount they need and can feel assured in their purchase.
We pride ourselves in our ability to help customers avoid wasting time and money. We give them the confidence they need to move forward with their purchase and their application.
Intech places a high value on educating the coating community. We provide programs such as the Intech Informational Institute (I3), onsite evaluation, and Virtual Paint®. We find it important to educate our customers on our product line and coating techniques to ensure the best use of our products. Because of our hands-on experience with our products, as well as face-to-face communication with customers, we are aware of common misconceptions, problems, and concerns. Utilizing this knowledge, we are able to focus on each individual customer’s needed education. Additionally, our workshops help customers to understand what applications they can use for their specific industry.
Our Pioneer Series is thrilled to introduce you to Dave Walls, Plant Manager at Plasma Coatings, a division of American Roller. Plasma Coatings has been in business for 48 years and is a trusted LIA. Read about the company’s origins, evolution, and future interests in this interview.
Q:When was Plasma Coatings founded?
A:1969
Q:Who founded Plasma Coatings and why?
A:Originally, the company was founded by some investors that recognized the need for a non-stick coating in the paper industry. They hired Bob Carlo, the president and CEO, who gets credit for the growth of the company. He ran it until he retired in 2003.
Q:What was the first significant piece of equipment you purchased?
A:An oven: critical for curing Teflon™.
Q:How would you describe the changes in the company now from when it was first started?
A:The first plant was Plasma Coatings headquarters in Waterbury CT. They went from being a single plant to looking at who else had a need. They grew in different industries other than paper. As they were growing in Connecticut, they found the same needs in different parts of the country and branched out to the south. 1986 marked the opening of the Tennessee plant. It was an area rich in paper industry and other manufacturing. Then, with so much manufacturing in the Midwest, we opened a plant in Minneapolis in 1991. Later in 2003 when Bob Carlo and the shareholders decided it was time for them to retire, Plasma Coatings was acquired by American Roller Company. In 2011, American Roller opened a new Plasma Coatings plant in Houston, TX and then in 2013 we opened in Shanghai, China. Leading the way is Dan Cahalane, president of American Roller and Randy Mittelstaedt, corporate operations manager of the coatings group, who do a terrific job of driving the growth and general operations of the company and coating facilities. Their contributions to our success are both substantial and vital.
Q:What would you consider significant milestones in your company?
A:The expansions of the company gave us a wider national and global reach. Over time, Plasma Coatings became involved in a variety of industries including paper, rubber, chemical, power generation, converting, petro-chemical, adhesive products, food, and oil and gas, among others. Another significant milestone was Plasma Coatings coordinating licensee activity in several different countries. The First licensee came on board about 1980 (late 70s) in Italy. We found success with the Italians having the same challenges in industries as the U.S. We then started looking for other opportunities to spread that around. Eventually, we set up licensees in Australia, South America, Japan, and a few other places and we now have 8 licensees we provide training to. But, one of the biggest milestones was us becoming a part of the American Roller team. With a 75 year plus history, American Roller has great engineering and machine shop services in their multiple plants, as well as Teflon application, which combined with Plasma Coatings capabilities, really make us a one stop shopping company with a full range of services.
Q:How has the coating industry itself changed over time?
A:The biggest change is the expansion of the Teflon industry to all kinds of manufacturing markets. In the early days, companies weren’t really using much Teflon. It wasn’t spread into so many industries and applications as it is today. It’s interesting seeing that growth in all different markets; even today we’re selling to companies that have never used Teflon. There’s a regular sales activity that uncovers these new opportunities.
Q:How has being an LIA affected your company?
A:An easy go-to is a PFA or FEP because they work well in so many applications. But, one coating that works in many areas is the 420G-109. We try to provide all coatings. Anything that is in the Teflon offering that is needed, we can provide. We pride ourselves on offering custom solutions for specific problems. We look more deeply into applications and rely on history and experience about how things work in certain areas so we can provide a customer with specific solutions as opposed to a couple of do-it-all coatings
Q:What is your favorite Teflon coating?
A:An easy go-to is a PFA or FEP because they work well in so many applications. But, one coating that works in many areas is the 420G-109. We try to provide all coatings. Anything that is in the Teflon offering that is needed, we can provide. We pride ourselves on offering custom solutions for specific problems. We look more deeply into applications and rely on history and experience about how things work in certain areas so we can provide a customer with specific solutions as opposed to a couple of do-it-all coatings
Q:What excites you about the future of the coating industry?
A:Plasma Coatings for 29 years, and although I have seen a lot in those years, still today I learn new things essentially daily. We are looking forward to the future of new applications that we can uncover. Everything doesn’t turn into a blockbuster volume of sales, but it’s interesting to find the different things going on in manufacturing so that we’re part of a never ending learning process. We are looking forward to a future of continuing that growth. It’s all out there. There’s new opportunity around every corner, and I find it really exciting.
Q: When was your company founded?A: Plastics Consulting and Manufacturing Company was founded in February 1962.
Q: Who founded the company and why?
A: Sol Schwartz, my father, originally created the company as Plastics Consulting Company in 1962. Sol was a plant manager with DuPont in the first plant that produced Teflon™. He decided to start a company consulting for industrial businesses using plastics as a potential solution. Over time, as he couldn’t find people to manufacture the solutions that he developed, he figured he would start doing it himself. Thus, the company transitioned into “Plastics Consulting and Manufacturing Company”, or PCM for short. Since the beginning, and even to this day, our mantra is “solutions for the customer”. If we’re not doing that, if we’re strictly putting a coating on a part, we’re not doing our job. Our job is to provide a value added solution for the customer. That’s how the company was started and how it continues to this day.
Q: What was the first significant piece of equipment you purchased?
A: There were two significant equipment purchases. When Sol could not find solutions for his customers, he decided to provide them. He spent $300 in 1964 for a 12-inch cube oven and a $50 spray gun. He built his own spray booth from scrap metal, and that’s how he began spraying coatings. More recently, in 2014, we built a completely new plant, and, with the help of Intech, we purchased a 10’x10’x16’ 850° Precision Quincy oven. As far as airflow and uniformity, it’s as good or better than anything I have ever seen.
Q: How would you describe the changes in the company now from when it was first started?
A: Today, we are 100% focused on coatings-based solutions for our customers. A vast majority of those are fluoropolymer solutions. That transition to coated parts really took hold in the mid 70s. Prior to that, we did linings, injection molding, and machine fluoropolymer parts as well. Every day, the constant is that somebody comes to us with a problem or question or looking for a cost saving in his or her process, and we look to do it in a way that adds value.
Q: What would you consider significant milestones in your company?
A: In the late 90s, we narrowed our focus to the food processing industry. This was a very purposeful move because we saw food processing from a regulatory standpoint and the increased focus on food safety as a good match with our product line. It was a big turning point for us. Of course, the building of the new plant in 2014 was another milestone. We had a fire in part of our old plant, so we decided to level the facility and build a new facility from scratch. The opportunity to build this new facility and the focus on food processing opened up all kinds of efficiencies for us. It increased our capacity, we went to state of the art equipment, and we were able to design a better workflow that allowed us to be more flexible and more competitive.
Q: How has the coating industry itself changed over time?
A: From 1,000 feet up, the most significant change is the deep focus on sustainability. I think we have an obligation to use materials and processes in our business that support responsible environmental practices. I think that our customers are far more attuned to those issues today than they were 10-20 years ago. At the same time, with that in the background, our partners, such as Chemours, are coming up with new materials that perform even better in this environment, and not even just in the materials but also in the process technology. There’s a history of coaters, like me, isolating companies like Chemours. Those days are over in the U.S. We now work together as partners, which is advantageous in terms of protecting customers and delivering superior products and solutions that adhere to regulations. There are real implications and it’s not something we do to just pass paper on.
Q: When did you get your LIA license?
A: In the late 60s, a customer came to us who was an injection molder down south. They were having issues with sticking, build-up, and the process. We showed them that if they got a Teflon™ coating on the processing parts, they could run substantially quicker with lower pressures and less waste. Back then, DuPont liked that we were proactively going out to find problems in the industry. They offered us the opportunity to become an LIA, and of course we accepted.
Q: How has being an LIA affected your company?
A: It lends a certain level of credibility when we communicate with our customer base. The name speaks for itself. Perhaps the biggest impact is the closeness that it allows us to work with the Intech and Chemours teams. Whether it’s lead generation, technical support, sales support, or inventory management, it’s really one of those few truly symbiotic, vertical relationships that we see as a strong value-add. It also gives us a freedom to develop new markets and opportunities. The net result of that, which goes back to the original company’s DNA, is a very closely tailored solution for our customers’ needs.
Q: What is your favorite Teflon ™ coating?
A: My favorite coating is the coating that works the best and provides the maximum value for my customers’ needs. You’re kind of asking me which of my children I love the most. I don’t have a favorite. Much like my children, there are some coatings that I like on some days more than others. We’re a big fan of the ETFE line. It’s extremely user friendly and provides strong value for many of our customers. The 421 coating line is also a workhorse for us. Finally, we’ve been impressed with some of the new water-based technology. For us, reducing or eliminating VOCs is a big focus.
Q: What excites you about the future of the coating industry?
A: It’s never ceased to amaze me, every day, a phone call or e-mail is initiated, where somebody has a problem that we can solve. Often, it’s the case that the customer doesn’t even know that this solution exists, even with as mature of a product as Teflon™ coatings. Mostly, it is just about educating them on the proper coating and the proper application. So, every day there’s a new opportunity that could be seismic in terms of the potential impact on our business. There aren’t a lot of industries that can say that. I’ve been doing this for 22 years now, and I remember when I started, that was one of my big takeaways.To this day, 22 years later, it’s still true.
Q: Is there anything else that you’d like to include that we haven’t covered?
A: Everything that PCM does is truly a team effort, from the guys on the shop floor, who in some cases are truly artists, to quality control, to the office staff, to the sales team, to the management team; it truly is a team effort that I am really proud of.
Teflon has a simple, classic product line. It doesn’t leave room for confusion, yet allows room for change and evolution. Other companies that sell industrial coatings will claim that they have the most complete line, but customers often find this false or confusing. The coding of the Teflon™ brand is straightforward and direct. Customers need not question the quality of a multitude of colors.
The Teflon™ brand colors are limited because we focus on performance and durability over appearance. The colors that we have are the best and always chosen because of their strength and effectiveness. We keep our line small because we focus on each coating, making complete assurance that no matter what a customer chooses, it will be fully functional and successful, not just decorative.
This being said, the Teflon™ line is still a robust product line of powders and liquids, leaving no coater or industry out of the loop. The line stems across all Teflon™ families as an entire array of coatings for all practices and end uses.
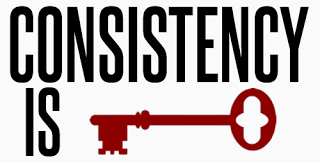
If there is anything that our distributors here at Intech Services hear often, it’s that the Teflon™ brand has superior batch consistency over the competition. With other companies, clients worry about color variations and mismatches as well as disparities in quality and appearance. The batch consistency Teflon™ provides makes customers feel secure that they’ll get the right hue and quality-every time.
Hitting the Target of a Firearm Finish
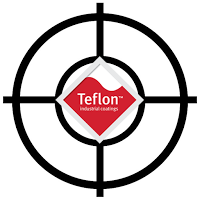
You may have heard that the custom firearm industry has been using Teflon™ finishes on several types of gun and rifle parts. Why is Teflon™ the most effective and long lasting choice?
Teflon™ provides dry film lubricity, thermal stability, durability, chemical and corrosion resistance, easy cleaning and a matte finish.
Teflon™ is used as a dry film alternative for wet lubricants on interior, moving components, such as bolts, trigger assemblies, magazines, sliding rifle stocks, and bipods. All of these parts normally require repetitive maintenance (causing gun owners to spend added time and money). Many times, wet lubricants such as oil cause residual dirt to build up, resulting in the need for routine cleaning or the use of harsh chemical cleaners that can be damaging to finishes or firearm parts.
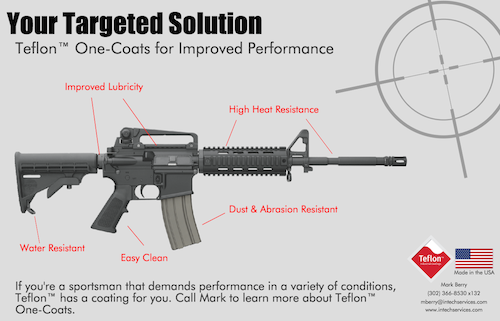
One finish often used on gun parts is ceramic paint, which lacks lubricity and is not specifically made for tight tolerances. Teflon™ coatings offer unsurpassed lubricity in comparison to ceramic coatings. Additionally, Teflon™ coatings’ thin film application ability is the perfect fit for tight tolerances.
Metal treatments and plating processes are also known to harden and protect metals from corrosion. Yet, what these treatments provide in corrosion resistance, they, too, lack in lubricity.
Teflon™ finishes offer a wide range of solutions to the firearm industry where other coatings fall short. This American made finish can give firearm owners the outstanding qualities they are looking for in order to enhance and protect their investment.
For more information, visit our website here. If you would like to learn more or discuss how this solution could work for you, contact Mark Berry, our General Market Segment Leader.
On Saturday, January 28th, Intech President Mike Patterson had the distinct honor of attending the retirement party of DuPont/Chemours salesman, Mr. Jay Kennedy. Jay has been a dedicated salesman for DuPont/Chemours for 30 years, and a large portion of his career was within the Teflon™ segment. Colleagues and customers would all agree that Jay’s infectious personality and sense of humor will truly be missed.
Congratulations to Jay on a great career, and the many lifetime relationships he created during his time in Teflon™ sales.
A premiere coating system for end-uses that require nonstick, thermal stability, and abrasion-resistant properties.
Product Overview
The 3-Coat Improved Standard is the premium Teflon™ coating line reinforced for scratch and durability. The line is for end-uses that require non-stick, thermal stability to 500°F, and high lubricity. Decades of innovation and technology have led to significant improvements in this coating.
This water-based, multi-color system is a unique blend of PTFE, PFA, and FEP fluoropolymer chemistry. The primer utilizes On-Smooth technology for easy adhesion to smooth surfaces when necessary. When your application requires ultimate release and superior durability, 3-Coat Improved Standard is your choice.
Feature & Performance Benefits
- Primer can be applied On-Smooth on aluminum substrates
- Thin film, “wet on wet” mid-coat/topcoat for quick application and cure
- Water-based for low emission environmental standards
- PFOA free
- Maximum use temperature of 500°F
Properties
Excellent nonstick properties: premium coating for providing releaseHigh lubricityFDA approved for direct food contact regulations in 21CFR
Chemical and abrasion resistant
Application Process
For best application, apply to aluminum oxide grit blasted metal substrate. If grit blasting is not appropriate, the coating can be applied to a smooth, clean surface. Spray applied primer is force dried at 5-8 min. at 120-150°C (248-302°F), then mid coat/topcoat applied wet on wet and cured minimum 5 min. at 428°C (802°F) or 3 min. at 435°C (815°F) (metal temperature). Peak temperature should not exceed 440°C (824°F).
For more information on this coating, contact Intech Services, Inc.
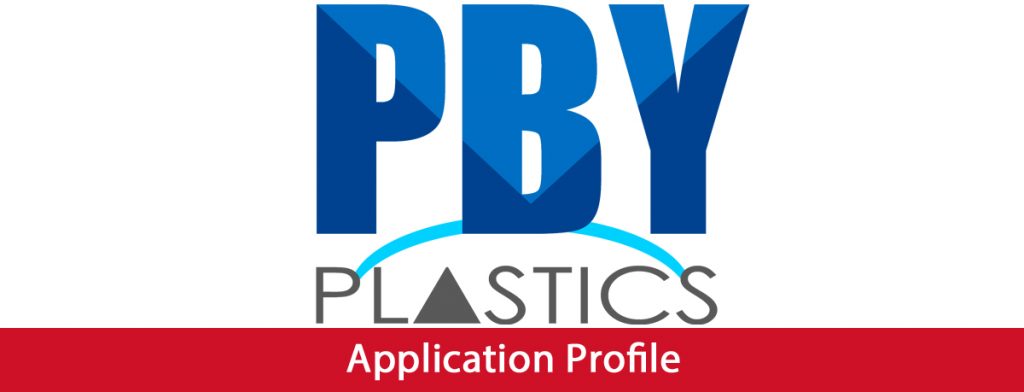
One Piece Molded Tanks using Teflon™ PFA High Purity Resin
Introduction
PBY Plastics, Inc. (Ontario CA) is an innovator in the custom molding of high performance plastic materials. Using a number of unique proprietary manufacturing processes PBY produces stock shapes, near net shapes and its new line of one piece molded PFA high purity molded tanks.
Key Benefits
- Thermal stability, in service temperature range: ‑328°F to 500°F
- Virtually leak free, no welded seams
- High purity, ultra-low metals and extractibles
- Superior chemical, solvent and environmental toughness
- The tanks are molded in a controlled environment for unmatched cleanliness
- Smooth walls, full radius corners, drafted to center bottom
- Resistant to sunlight and other UV sources
Technology
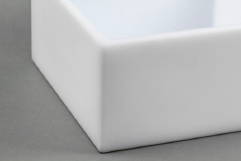
PBY Plastics has made significant investments in its proprietary high purity compression molding operations and processes. It now has the capability to handle high purity resins, and the compression molding of its one piece tanks, in a tightly controlled environment. Virtually every step of the process from raw material storage, mold tool resin loading, and the final step of molding the tanks, has been designed to produce the highest quality finished article for the most demanding of applications.
The PBY technology, equipment and systems allow it to produce high purity PFA molded tanks virtually free of contribution contamination, metals and particulate. In addition to improved cleanliness and purity the tanks have exceptional surface smoothness and low permeation characteristics. The new process allows PBY to compression mold a true one piece molded process tank that can effectively replace sheet fabricated tanks in a number of applications where ultra-high purity, cleanliness and leak free durability are the primary requirements.
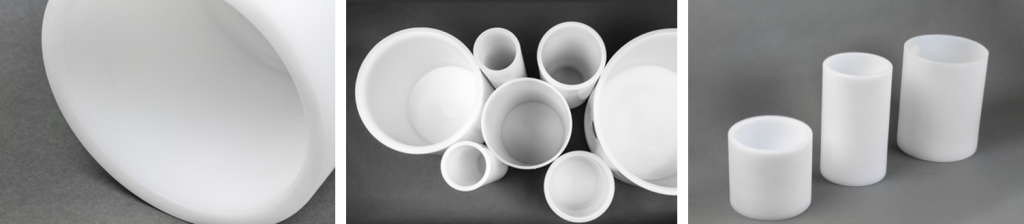
One Piece Molded Process Tank – Round
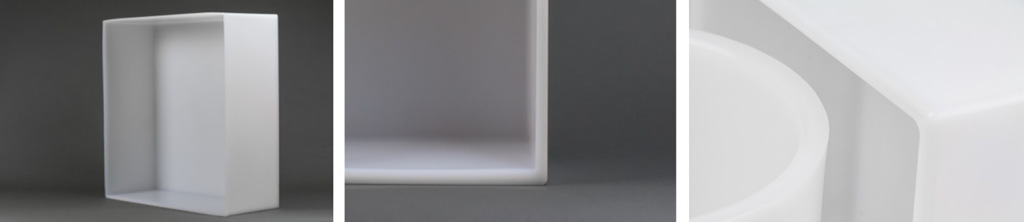
One Piece Molded Process Tank – Square or Rectangle
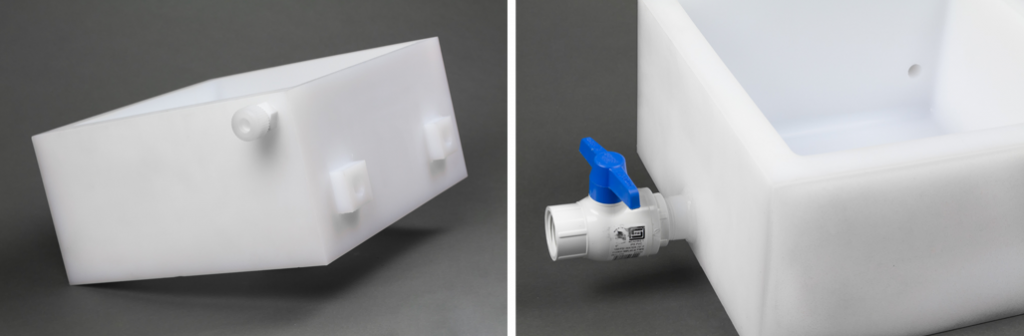
One Piece Molded Tanks Promote Endless Design Possibilities
Materials Selected and Why
PBY Plastics selected Teflon™ HP-PFA resin for its unique line of one piece molded process tanks. Teflon™ HP-PFA allowed PBY design engineers to move past traditional design boundaries by starting with a premium industry standard material that exhibits high purity, low metals and very low levels of environmental particulate and background contamination.
PBY compression molded one piece process tanks produced with Teflon™ HP-PFA exhibit extreme performance and World Class quality, and offer a value added alternative to sheet fabricated and welded tanks.
The Teflon™ HP-PFA one piece molded tanks are well suited for chemical and process applications that do not require a custom sheet fabricated tank or where a heavier walled tank is desirable.
The tanks are available in a range of standard sizes, through 25 liter, and are available in rectangle, square or round configurations.
Options and design possibilities include:
- PFA mounting tabs for hardware and accessories
- Tank body threaded bosses for fittings, valves, sensors and drains
- Welded in place cover or removable cover
- Heavy wall options available for custom machining
- Custom sizes and configurations quoted on request
Please contact PBY Plastics for more information on their product line and manufacturing capabilities.
Click here to download a copy of this article.
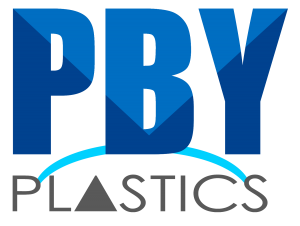
PBY Plastics, Inc.
2571 E. Lindsay Privado
Ontario, CA 91767
909-930-6700

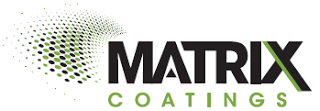
Chemours and Intech Services, Inc. are proud to announce Matrix Coatings Corp. of West Palm Beach, Florida as a Licensed Industrial Applicator (LIA) of Teflon™ industrial coatings. The LIA program is an elite group of coating companies that have extensive knowledge of Teflon™ industrial coatings and experience in recommending and applying fluoropolymers in a variety of applications. LIAs meet a list of criteria and qualifications as well as quality of workmanship and are a reliable resource for recommending coating solutions and applying them to a customer’s specifications.
Since its founding in 1964, Matrix Coatings (originally named Southeastern Coatings) has been serving the Eastern US as a reliable coating company. Their goal is to use their experience to provide customers with coatings solutions and quality products in a timely manner. Matrix Coatings is committed to its role as an AS9100C/ISO 9001:2008 Registered company and is currently expanding and investing in new equipment as the need for high performance coatings rises. These coatings solve problems of corrosion, provide dry film lubrication, create non-stick surfaces, and meet MIL Spec requirements.
Larry Sloan of Matrix Coatings stated, “I have been involved in the Teflon™ coating business since 1978 and fully understand the great honor it is to be a member of the prestigious group of Chemours LIAs.” Additionally, “It validates for our customers and potential customers that they have come to the right place,” and most important is the “closer working relationship it creates between Matrix and Intech & Chemours, allowing us to be on top of new product developments…”
Congratulations, Matrix Coatings Corp.! Click here to view the full press release.
This year, Intech Information Institute (I3) was held at Embassy Suites in Newark, Delaware from September 27-29th. I3 is a yearly workshop hosted by Intech Services Inc. designed to fully explain and comprehensively examine the products, sales, marketing, and technology behind Teflon™ coatings and the coatings market. Additionally, one day of the workshop is dedicated to Virtual Paint®, a simulated, hands-on spray-painting seminar. This year, we received excellent feedback from all of the attendees. When asked to fill out workshop evaluation forms, attendees ranked us almost all 5 for 5s in all areas of the curriculum and instruction. Some additional comments reminded us of the notable contribution we make in the coatings industry and the impact the workshop experience has on those who attend.
“Well done, Intech! Very comprehensive! Knowledgeable team! Showed sincere interest in our success!”
“I found the segments on sales and marketing gave me a good general overview that will allow us to dig deeper into sales and marketing and create programs specific to our company.”
“The product list and breakdowns are things that will be very helpful when choosing a coating or system.”
This year was a great success. We are confident in our ability to share coatings knowledge with our clients and friends within the coating world and look forward to seeing both new and returning faces at next year’s I3workshop.
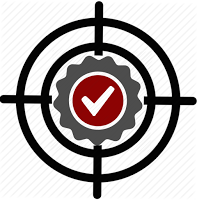
Teflon™ products are not only reliable because of their history, but because of their superior quality. These finishes have immediate impact on the current quality of products, yet they also extend the service life, creating long-lasting durability.
Teflon™ coatings have superior reliability and retention while also preventing contamination of process fluids. Additionally, the coatings have low friction and ideal release properties for several applications.
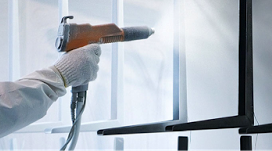
Why is powder drifting out of your spray booth openings? Here are some possible causes and solutions of this unwanted issue:
- Insufficient airflow through the booth and the recovery system.
Solution: Position powder guns away from booth openings and check air volume control.
- Cartridge filters are not failing to receive adequate cleaning.
Solution: Increase air pressure or the volume.
- Cartridge filters at end of life.
Solution: Replace cartridge filters
Solution: Check the final filters for leakage; repair or replace filters as needed.
It’s very clear to see the successful track record that the Teflon™ brand has held up for years. Whether you’ve just started taking advantage of the successful products, or you’ve used them since 1938 when chemist Roy Plunkett discovered them, you understand the value of their history, and the trust you have in the brand is immeasurable and irreplaceable. As “your partner in the kitchen for 50 years” or your go-to coating in an industrial facility, Teflon™ has you covered, and keeps your products long lasting and durable.
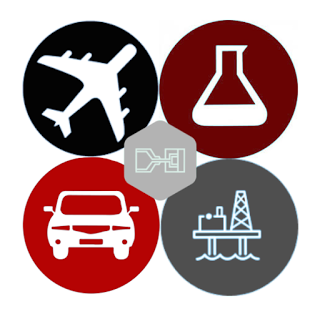
“We didn’t just invent the nonstick cookware category; we’re constantly perfecting it.” –Cookware, Chemours
As the basic technology has expanded over time, Teflon industrial coatings have continued to enhance the functional qualities in today’s high techapplications. Teflon coating’s non-stick qualities, low coefficient of friction, heat resistance, cryogenic stability, chemical resistance, non-wetting, unique electrical properties, abrasion resistance, and FDA conforming are just some of many highlights of the brand’s available products. All products have grown and evolved over time as the brand has demonstrated benefits in the following industries: aerospace, chemical, oil and gas, automotive, molds, and industrial bakeware.
“Intech and the Chemours R&D team are actively working on new coating technologies that will provide even better durability and release. We are also working on new products for areas where our coatings have not been utilized in the past.” –Nicole McCall, Molds Market Segment Leader
Not only do we have you covered, but we can even grant you certification with Teflon™ Industrial Licensing. This licensing gives companies that use Teflon™ products a matchless edge.
Looking for a more durable solution for your mold release applications? Below we share some of the benefits of the Teflon™ FEP two-coat system. You may have heard of the product, but the benefits it offers your shop are highlighted in the short description below.
This system has extreme release capabilities for mold and food processing applications, providesnonstick, chemical, and corrosion resistancefor low abrasion release applications, and can be used on steel, stainless steel, and aluminum.
To get the most out of the coatings’ release characteristics, Intech Services recommends the thickness be no less than 2 mils but not exceed 5 mils.
If you have a plastic or rubber molded material that needs release over a long period of time, this solution will increase process efficiency and reduce scrap rates.
More features:
- Excellent release qualities
- Good thermal stability
- Good wear resistance
- FDA approval
For more information on this product, visit this page.
Your shop can benefit from this long-lasting solution. Please contact Intech Services at 302-366-8530 with any questions or for further information.
STORAGE AND HANDLING OF GRANULAR TEFLON™ PTFE RESINS
INTRODUCTION
TEFLON™ PTFE granular molding powders are manufactured in an enclosed, positive pressure system using purified air and water. The packaging area is under positive pressure with “air-lock” doors, tile floors, enamel walls and flush-mounted lighting. The following storage and handling recommendations will help to preserve the high quality of these resins.
SHIPPING
Teflon™ granular resins are not shipped refrigerated. However, when these resins are shipped in a truck with fine powder resins, the granular products may arrive at the customer’s plant below PTFE’s room temperature transition temperature of 19°C (66°F).
STORAGE OF GRANULAR PTFE RESINS BY CUSTOMERS
Chilled resin: When granular PTFE resins arrive in a refrigerated truck, the drums should not be opened immediately. Good practice is to let them sit in the sealed container for 24 to 48 hours at a temperature of 23°C-27°C (73°F-80°F). Granular PTFE resins stored by customers in a refrigerated area must be removed from cold storage to an area where they will have time to warm before the drums are opened.
While PTFE resins are not hygroscopic, powder which has been chilled and then exposed to a damp atmosphere will become wet from condensation. Moisture will cause the preform to crack during sintering.
It is important not to preform PTFE powder below the 19°C (66°F) transition temperature even when the relative humidity is below 50%. Preforming cold powder will result in cracked preforms because the resin expands 1.5% in volume as it goes through the room temperature transition. The easily damaged preform cracks because it cannot resist the forces of the large volume change. To avoid this type of cracking, it is important to preform all granular powders at 23°C (73°F) or higher.
Unchilled resin: Unchilled resin received by customers should be stored at a temperature of 23°C-27°C (73°F-80°F) in a clean, dry area.
HANDLING OF GRANULAR PTFE RESINS
The Importance of Cleanliness: The importance of cleanliness in processing PTFE resins can hardly be over-emphasized. PTFE readily attracts particulate contaminants because it is a highly electrostatic material. The high sintering temperature and the whiteness of the resin intensify the effects of contamination. The smallest speck of atmospheric dust, oil or other organic substance can be carbonized during sintering leaving clearly visible dark, white or clear spots in a contaminated molding. While such imperfections may not have important effects on physical properties, they are undesirable in appearance. Conditions and practices suitable for molding other plastics may not be adequate for PTFE resins.
Opening the Drum: Before opening a drum of “Teflon” PTFE granular resin carefully clean the outside of the lid to remove contaminants picked up during shipping and storage. Granular PTFE resin is packed in a drum lined with a loose polyethylene bag. The bag is twisted and tied at its top. Before removing the tie, the outer surface of the bag should be vacuum cleaned to remove particles of contamination. Remove the tie, untwist the bag and fold the bag over the rim of the drum to protect the powder from contaminants trapped between the outside of the bag and inside of the drum. Promptly remove the amount of resin needed (into a clean container with a lid), close and twist the bag, and retie. Replace the drum lid until more resin is needed.
It is important to vacuum the inside of the drum and the outer surfaces of the bag liner when the entire drum is to be dumped into the mold cavity at one time (see footnote A). This will prevent loose particles trapped between the liner and the inside of the drum from falling into the mold cavity along with the resin.
Preforming: Preforming normally is carried out at temperatures between 23°C-27°C (73°F-80°F). Storing the powder before use in a room maintained at 23°C-27°C (73°F-80°F) and below 50% relative humidity helps avoid moisture condensation and also minimizes the tendency of the powder to form lumps in hot weather. Improved product quality, uniformity and reduced scrap losses justify the investment in such facilities.
An ideal arrangement for the molder consists of a room at 23°C-27°C (73°F-80°F) for temperature conditioning, weighing and preforming the powders. The room should be separated from the sintering operation and from the processing of other plastics. It should have a separate filtered air supply maintaining a slight positive pressure inside the room. Cleanliness conditions and practices suitable for molding other plastics are usually not adequate for PTFE resins. Operators should wear clean, lint-free coveralls and maintain a high standard of cleanliness.
Lumps: Granular PTFE resins may compact and form lumps during shipment. Soft lumps usually can be broken up sufficiently with a clean scoop to permit filling of mold cavities over 25mm (1 inch) wide. In rare instances screening through a clean, coarse (8 to 10 mesh) screen may be advisable. Remember: it is difficult to screen the resin and avoid contamination.
Harder lumps should be placed in a clean, covered container, chilled to about 10°C (50°F) and shaken vigorously. Be sure to allow the container and the resin to warm to the 23°C-27°C (73°F-80°F) range before removing the container’s lid.
Footnote (A): We do not recommend or encourage dumping an entire bag of resin into the mold cavity at one time. This practice will produce moldings with non-uniform density and can cause cracking. We recommend loading powder evenly into the cavity (no matter how large the mold) with a clean scoop.
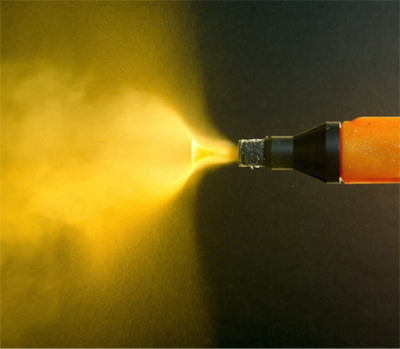
Reasons your control gun is not showing any reading of Kv could be any one of the following:
- Loss of power to gun
- Faulty circuit board
- Internal gun failure
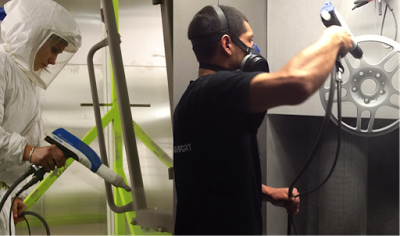
A few causes for powder surging from the gun includes:
- Insufficient supplemental air to ensure the powder is in suspension as it moves through the hose.
- Improper seal between the powder injector and the lift tube in the gun feed hopper.
- Blockage from buildup or impact fusion. Check powder hose, gun tube, and pump insert.
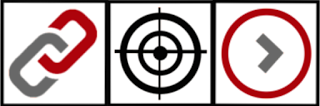
As a customer, a client, or a friend of Intech Services, you may be aware of our core values: Genuine Connection, Unique Focus, and Deliver More. These values are best shown through our ability to interact genuinely with customers, our focus on expanding and exploring new opportunities, and our success rate as Teflon™ distributors.
As distributors, we are confident in the Teflon™ brand and all that it has to offer, and are proud of our robust, committed team here at Intech. We see Teflon™ as the real deal: top quality, consistent products that are delivered on time, with ease. That’s why we’ve created the Real Deal Teflon™ blog series. Check back on the Intech Insider each month to read about the brand’s qualities and learn about the dedication and loyalty of the Intech Services team.
A premiere coating system for end-uses that require durability, non-stick, thermal stability, and abrasion-resistant properties. Product OverviewDecades of innovation and technology for the Teflon™ brand have led to significant improvements for this specific coating line. The system is water-based, and a unique blend of PTFE, PFA, and FEP fluoropolymer chemisty. On-smooth technology is utilized for easy adhesion to smooth surfaces when necessary. If your application requires superior durability and ultimate release, we recommend trying the 2-Coat reinforced system.
Properties
- Extended service life due to excellent durability
- Excellent nonstick properties
- FDA approved for direct food contact regulations in 21CFR
- Chemical and abrasion resistant
Additional Features
Some additional features of the coating line include thin film primer topcoat for quick application and cure, a water base that contributes to easy cleaning and meets low emission environmental standards, and a maximum use temperature of 500° F. Additionally, this line of coatings has excellent non-stick properties, extended service life due to excellent durability, FDA approval for direct food contact, and chemical and abrasion resistance.Application
Process
For best application, apply to aluminum oxide grit blasted metal substrate. If grit blasting is not appropriate, the coating can be applied to a smooth, clean surface. Spray applied primer is force-dried (Ref. 5-8 min. at 120–150 °C (248–302 °F). The temperature of the primer should be between 35–45 °C (95–113 °F) before application of the topcoat. The total system should include a minimum of 5 min. at 428 °C (802 °F) or 3 min. at 435 °C (815 °F) (metal temperature). Peak temperature should not exceed 440 °C (824 °F). See Fact Sheet for complete application information.
Marketing Material
To download this information in a PDF, click here.
For more information on this coating system, call Intech Services, Inc. at (302)366-8530 or visit our website here.
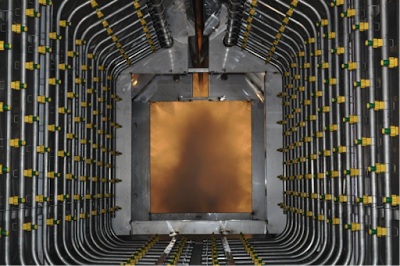
Ever wonder about what you should really be doing with the waste that comes from the pretreatment process?
- Oil, grease, metals, and pH are the most common environmental reporting concerns
- Sludge and contaminant buildup may call for a regular clean-out of the cleaner and phosphate stages
- The waste treatment process usually just needs adjustments in pH and flocculation
For accurate information on acceptable results, contact a treatment chemical or waste equipment supplier.
Chris Lord is the segment leader for Teflon™ applications in the Automotive industry. We sat down and talked to him about applications of Teflon finishes in the automotive world. Read on to find out about current and future uses of Teflon coatings within this industry
Q: What are the most common problems within the Automotive industry?
Chris: A main reason automotive manufacturers and suppliers consider Teflon™ products is to resolve noise, vibration, and hardness (NVH) situations which are common with automobiles. NVH are sources of complaints or results of premature wear that can greatly affect quality ratings and future sales of automotive manufacturers.
There are also opportunities to create efficiencies in the automotive plants where tooling maintenance is frequent. Reducing this maintenance can lead to increased plant safety and cost savings.
Q: How do Teflon™ coatings solve these problems
Chris: Flagship Teflon™ S products such as 958G-303 and 958G-203 provide inexpensive options that are a perfect fit for intricate automotive components produced in high volumes. For in-car parts, OEM’s are looking for coatings with high lubricity, thermal stability, and durability that can be applied in a relatively simple manner. Our one-coat Teflon™ S products fit these requirements.
Q: What is one specific coating or coating system that provides lubricity with great abrasion resistance?
Chris: Our PTFE dry lubrication line is very robust with a variety of thick and thin film options to choose from. 958G-303 is an industry standard and has been used for dry lubrication for many years. In 2016, Intech Services began offering the abrasion resistant version of 958G-303 called 958G-313, and the response to this coating has been very favorable. For thicker film applications, we recommend using 958G-414. This coating system would be the ultimate option for applications that allow 2 mils dry film thickness (dft) or more.
Q: What trends are you seeing in the automotive industry?
Chris: CAFE (Corporate Average Fuel Economy) standards continually push automobile manufacturers to improve miles per gallon (mpg), which is why Ford transitioned to using aluminum (lighter metal) for the F-150. By 2025, automobile manufacturers are required to average 54.5 mpg across their fleet of vehicles. Because of these standards, more and more alternative fuel vehicles are being introduced into the market. Additionally, improved resistance to corrosion will always be stressed within the automotive market.
For further information on Teflon coatings in the automotive industry, contact market segment leader Chris Lord at (302) 366-8530 x 104 or clord@intechservices.com.
Have you been having trouble achieving Salt Spray performance requirements? Are you unsure what to do or where to look?
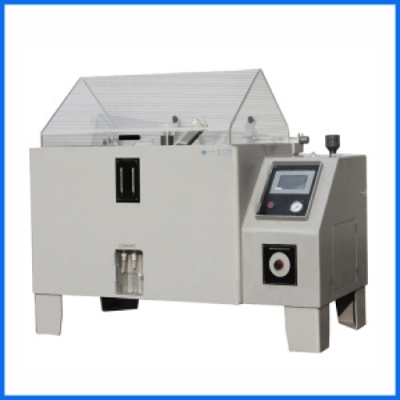
Improving the process line can be confusing and complicated. Take these steps to enhance Salt Spray performance:
- Evaluate the process and establish if anything has changed about the incoming piece (either the incoming soil or the metal).
- Determine if anything has changed within the wash process (focus on the cleaning stage).
- Check for correct concentrations, nozzle performance and alignment, temperatures, and bath cleanliness.
- Make sure that the pretreatment coating is still up to the desired conditions (differences in color, blotchiness, etc.)
- Ensure quality of rinse water.
Many problems with Salt Spray performance can be traced back to an inefficiency of cleaning. Signs of this inefficiency are often found at the exit stage of the rinse cycle. In terms of the rinse water, the coating will be as clean as the last fluid it encountered. Rinses that are contaminated can result in salt deposits that reduce Salt Spray performance radically and interfere with the adhesion of coating.
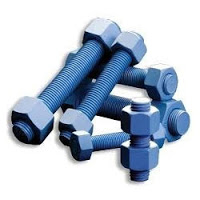
Q: What are the common problems within your industry?
Chris: Corrosion is the most common issue in the Oil and Gas industry, particularly in subsea applications. Along with corrosion, lubricity for metal on metal surfaces also poses a problem. Many steel components are exposed to harsh environmental conditions that cause galling and overall component failures. Corroded threaded fasteners and other large componentry cause massive down time and costly maintenance.
Q: How do Teflon™ coatings solve these problems?
Chris: We have a series of coatings that prevent corrosion and provide enough slip to prevent galling that frequently occurs on threaded bolts, fasteners, and large oil and gas equipment.
Q: What is one specific coating or coating system that has impressive resistance against corrosion for oil and gas industry applications?
Chris: The 857G series has impressive corrosion resistance at very thin levels. Depending on your basecoat, achieving 3000 hours of salt spray is possible with the 857G at a thickness of only .8mils. This coating is also resistant to hydraulic fluids, aggressive rig wash products, has very good UV stability, and has a consistently lower coefficient of friction than uncoated threaded components and fasteners.Chemours developed a water based coating series specifically designed for Oil and Gas applications. These one coat systems can be coated as thin as .8mils but can be coated as thick as 4.5 mils to prevent corrosion in harsh environments like the Gulf Coast, Northern Africa, the North Sea, and other corrosive coast lines.
Q: What new coating applications are on the horizon in the oil and gas industry?
Chris: Currently the R&D team is working to develop a cermet primer and topcoat system that will enable fasteners and other componentry to withstand upwards of 10,000 salt spray hours. Enhancing the coating system’s corrosion protection while maintaining a very thin build up is a constant challenge for the R&D team
Q: Are there new technologies in development for this industry?
Chris: Chemours is currently evaluating how traditional coatings in the Teflon™ product line can replace linings and other exotic metal and coating systems to prevent corrosion. Chemours recently developed a process to properly apply corrosion protection coatings inside of very narrow diameter tubes. This process has the potential to save OEM’s significant money on existing applications.
Q: What associations are you involved in within the industry?
Chris: NACE, the National Association of Corrosion Engineering has been an excellent organization in understanding the latest industrial trends, test methodology, products, and applications that focus on corrosion protection. Regardless of the economy, rust never stops, and NACE allows the industries brightest engineers, chemists, and general technologist members to focus on preventing corrosion.
If you may have any questions or inquiries for Chris about the oil and gas industry, email chris@intechservices.com or call (302)366-8530 x 103.
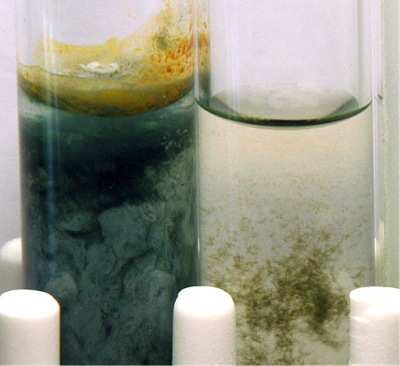
Most frequently, iron phosphate is used to pretreat powder coating, but other materials can be used as well. The reason that people choose to utilize iron phosphate is its usability with almost all substrates. Often, powder coatings will show improvements in performance over liquid paint when iron phosphate is used to pretreat.
A more costly process used for higher-end products is zinc phosphate. This process does have downfalls of using heavy metals, producing sludge, and needing added washer stages, yet sometimes is necessary if the desired performance is not accomplished with iron phosphate.
We continue the pioneer series with a spotlight on a devoted Teflon™ coater with significant accomplishments in the industrial coatings field. All pioneers in the Teflon coatings industry are early adopters of the coatings and have helped to shape the way Teflon has grown and evolved as a reputable industrial fluoropolymer. With the vision and ingenuity of all pioneers, Teflon coatings continue to be regarded as the elite fluoropolymer of choice.
This interview spotlights Artie McElwee of Toefco® Engineered Coating Systems, Inc. Through innovation and diversification, Toefco® strives every day to provide quality products and quality services with excellent delivery at a fair price. A family-owned and operated company for over 60 years, Toefco has been a frontrunner in coating application services. With the capacity to spray over 400 types of coatings and bake them in their 20+ ovens, Toefco has the capability to handle almost any coating project.
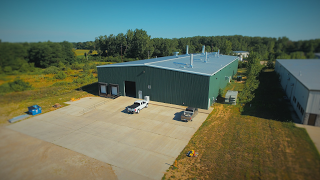
Q:When was your company founded? Who founded it?
A: The late Jim Jaden founded Toefco in 1955. For over 60 years, we have continued to stand behind our coating solutions and have engineered spray coating solutions for nearly any component you can think of.
Q:What was the first significant piece of equipment you purchased?
A: My family took over the company in 1994. The first significant pieces of equipment we purchased were new air compressors, air dryers, air and water separators, and filtration equipment.
Q: How would you describe changes in the company from when it started to today?
A: The list is long. The company is light-years ahead of where it first began, largely due to technological advances. Industrial equipment such as state of the art spray booths, robotics, and regenerative thermal oxidizers for the environment all play a part in the changing aspects of our business. These have all served as significant pieces of equipment and have been major investments towards the future of Toefco Engineered Coating Systems, Inc.
Q: What would you consider significant milestones in your company?
A: I consider the growth of Toefco, adding on to the facility and finding a great,great group of people to contribute to the company to be significant highlights within the last few years especially. We’re in the process of a big milestone right now. We’re just finishing a 20,000 square foot satellite facility only a mile away. This facility will accommodate our growth and expansion with our current customer base and support the new business that we’ve been awarded. In addition, we have built our state of the art equipment, which has the capability of coating and curing a 750 lb part, so that we can meet the needs of both new and existing customers. To see footage of our expansion, check out this video.
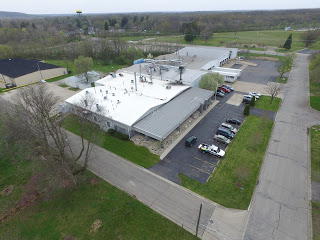
Q: How has the coating industry itself changed over time? How have you seen it change over time?
A: The coating industry is constantly evolving, particularly due to increasing environmental concerns. High-performance coating manufacturers have had to be progressive and get away from PFOAs and other constituents in these materials. These companies have strived to protect the environment and maintain earth-conscious practices, which has inspired a lot of change.
Q: When did you get your LIA license?
A: We got our LIA license well before I became a part of the Toefco team, and I’ve been here about 22 years. I believe we earned our LIA license in the early 1960s.
Q: How has being an LIA affected your company?
A: Being an LIA with Chemours has been very positive. Additionally, what Intech Services has done for our company has put us on the forefront as an LIA. Intech’s service and support as well as lead generation and opportunities we’ve been able to get have been significant. Their technical support and environmental help have really broadened our reach to customers.
Q: What is your favorite Teflon™ coating?
A: There are so many of them. The 851 Series and the 959G are great coatings. Tefzel is also a fabulous coating. As an applicator, we are committed to picking the best technology to solve the problem for the customer.
Q: What excites you about the future of the coating industry?
A: What excites me most are the opportunities that come with technological advancements as well as the progression towards more of a green thumb by lowering VOC content. Regulations are inevitable in our industry and causing it to progress and change. Several industries, such as car manufacturing, tractor manufacturing, and food processing are all increasingly regulated, giving us the opportunity to aid in their needed change. In the powder coating industry, we provide solutions such as fretting, galling, non-stick, corrosion resistance, and many more. What excites us at Toefco is being able to solve the problems that those within the industry did not have back in the day. Now that these industries are under regulation, Teflon produces new process solutions to create better results.
For questions and inquiries for Toefco, please visit their contact us page, or contact Artie McElwee directly at Artie@toefco.co
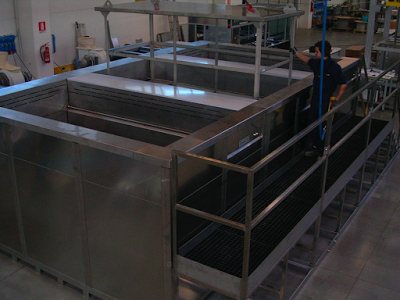
Phosphating is a process that uses an acid to remove parts of the metal substrate and re-deposit a layer of material that is a combination of the phosphate, metal substrate, and other metals. The new material sticks to the surface of the metal and provides a good coating base.
The surface created firmly adheres to the metal, provides better corrosion inhibition, increases surface area, and ensures that the powder coating will stick. With phosphating, the good coating base extends the working life of the piece.
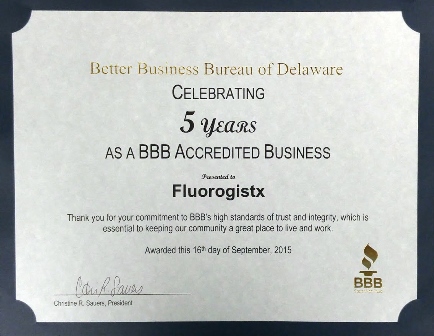
Fluorogistx® is proud to announce our fifth anniversary as BBB Accredited Business by the Better Business Bureau of Delaware.
Access to the Teflon™ brand for commercial usage:
The use of the Teflon™ brand and/or diamond shaped Teflon™ logo, requires specific approval from The Chemours Company.
If you are a current customer of Fluorogistx CT LLC, purchase Teflon™ branded fluoropolymer products, and wish to use the Teflon™ mark please contact us. We can assist you in the application process.
To inquire about a Teflon™ brand license application, please complete the form below and we will contact you.
Mark Berry is the segment leader for Teflon™ applications in the General industry. We sat down and spoke with him about applications of Teflon finishes. Read on to find out about current and future uses of Teflon coatings in the general industry.
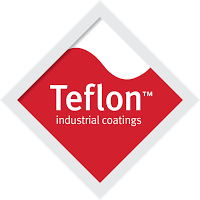
Q: What are the common problems within the general market segment?
Mark: There are many common issues in the general industry. Some barriers to quality results include corrosion, harsh chemical effects, high manufacturing temperatures, and over-use of petroleum-based products. Coaters and end-users strive to find materials that combat excessive corrosion, are heat and chemical resistant, and provide a dry film, non-grease, permanent solution. Repetitive, over-use of petroleum-based products calls for more manual labor and increased overall maintenance costs. For example, too often, companies repeatedly use a petroleum-based epoxy. After several instances of the chemicals eating through the epoxy, coaters search for something strong and long-lasting.
Q: How do Teflon™ coatings solve these problems?
Mark: Teflon™ finishes provide a more permanent solution for many of these challenges instead of repetitive use of low-quality solutions that work for a short time. These varied products and services fill our customers’ industrial needs and help them overcome barriers to success.
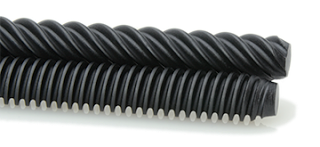
Q: When should people use Teflon coatings in the general market segment?
Mark: Customers should use Teflon products when they are looking for a long-term solution. The use of a higher quality material, such as Teflon, yields greater value than a cheaper, short-term solution that will call for repeated application.
Q: What Teflon coating systems work best for general industry applications?
Mark: Our “one-coat” products satisfy the many coating needs of our general industry customers. These products utilize hybrid technology and have high level performance and durability characteristics.
Q: Are there new areas that could benefit from the use of Teflon products?
Mark: Much of my work involves exploring new industries and new applications for Teflon, and one of my ongoing tasks is to educate materials scientists and process engineers on the characteristics and benefits of Teflon coatings. Since these scientists and engineers are involved in industries that do not traditionally use Teflon, it is important to help them better understand how Teflon products can truly benefit their processes, save them time, and decrease their overall costs.

Q: What trade shows have you attended within the industry?
Mark: This past year I attended both the National Association of Corrosion Engineers (NACE) tradeshow as well as FABTECH, a general industry metal fabrication trade show.I am always looking for and exploring information on trade shows for industries that have not historically used Teflon. There are many trade shows that I would like to attend in the future to further the education and reach of Teflon products.
For further information on Teflon coatings in the general market segment, contact Intech Services.
Several tests exist to help you to determine the cleanliness of your parts. The most common test is the “water break free” test. This test is used to observe whether the liquid draws away from or beads on the cleaned parts, or if it fully sheets over them.
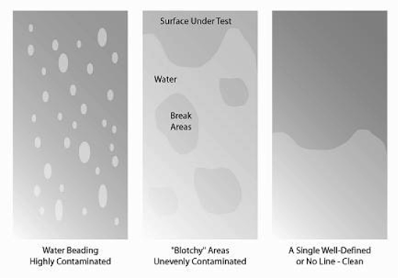
Alternative assessments to the “water break free” test include:
- Wiping with a white cloth
- Alcohol drop tests
- Coulometry (organic soil burned off substrate, measured)
To get recommendations on evaluating the cleanliness of parts, never hesitate to contact a pretreatment supplier.
Our series continues with another spotlight on a long-standing, devoted Teflon™ coater and his accomplishments in the industrial coatings field. All pioneers in the Teflon coatings industry are early adopters of the coatings and have helped to shape the way Teflon has grown and evolved as a reputable industrial fluoropolymer. With the pioneers’ vision and ingenuity, Teflon™ coatings continue to be regarded as the elite fluoropolymer of choice. This interview spotlights Michael Stechschulte of Endura® Coatings. Endura® is committed to providing the most innovative, technologically advanced, environmentally conscience, and highest qualified coating services available today. Endura Coatings has been a leader in coating application services since 1970. With over 750 engineeredcoating solutions spanning 11 technology platforms, they offer the most comprehensive array of coating expertise and services available today.
Q: When was your company founded?
A: Endura was founded in 1970 outside Detroit, MI.
Q: Who founded the company and why?
A: Dan Crowley, Art Coleman, and Bill Vicere. With the help of DuPont, Endura was one of the original LIA’s pioneering the use and proliferation of nickel Teflon. Endura helped identify industrial applications and uses for Teflon industrial fluoropolymer division.
Q: What was the first significant piece of equipment you purchased?A: A curing oven in 1970 for high temperature bakes.
Q: How would you describe the changes in the company now from when it was first started?A: What makes Endura different today is our ability to be “consultative engineers.” We are committed to understanding our customers’ needs using our KBER (Knowledge Based Engineering Repositories). In doing so, we are able to identify horizontals and verticals, industries and applications, all while documenting what coatings work and in what situations. We are also positioned to advise our customers on the latest raw materials, manufacturing processes, and specifications. We pride ourselves in our ability to modify coatings to meet the customers’ needs. Whether it’s through working with Chemours or modifying the resins ourselves using certain reinforcements and formulations, we strive to give our customers exactly what they need.
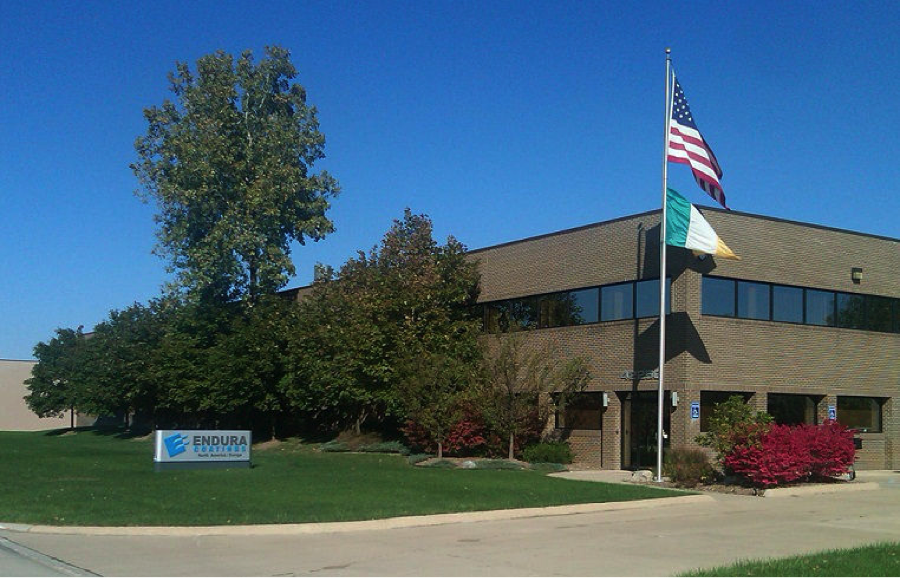
Q: What would you consider significant milestones in your company?
A: We made a significant shift in our business in 2001. It happened to be after 9/11 when many industries were going through financial turmoil. Given everything happening in the U.S., we took a larger, global view of how we were doing business and how we were going to be less reliant on the Detroit industry, specifically automotive. The decision was made to become a more multi-faceted organization. We made significant investments into medical, pharmaceutical, surgical/disposables, food packaging, and many other specialty niche applications, where we could be written into the specification. When one of our coatings is specified in a drawing, we would have long-term commitments. We tweaked the other part of the business, which was the value added coating business.Our focus shifted to providing products and product solutions.
Q: How has the coating industry itself changed over time?
A: Clearly government regulation comes to mind as well as the reduction of the PFOAs. Reformulations of our resins have forced us to reevaluate our coating chemistries, formulations, and customer use applications. We continually grow, learn, and understand the reach and depth of these changes as they occur.
Q: When did you get your LIA license?
A: 1970/1971. Unfortunately, the official recognition plaque has been lost over the years.
Q: How has being an LIA affected your company?
A: It shows that our company has been a long-term customer of Chemours. We have become a steward of growth for the organization. It is clearly an opportunity for us to do cross branding and cross e-marketing. We would like to do more to leverage the LIA program and Teflon brand.
Q: What is your favorite Teflon coating?
A: Our favorite Teflon coating system would have to be the Tefzel system. This coating system possesses an exceptional range of performance characteristics which make its use extremely versatile across a wide range of applications and industry niches. Its combination of non-stick, mechanical toughness, and chemical inertness make it a great candidate for use in food processing, food packaging, and chemical processing use environments.
Q: What excites you about the future of the coating industry?
A: The future entails continually increasing customer satisfaction by creating widely specified products using Teflon finishes. System integration is the future for the coating industry; being able to provide not only value, but product solutions for customers is what I’m most excited for!
For questions and inquiries for Endura coatings, please contact sales at sales@enduracoatings.com or 586-739-0101. Visit the website for more information at www.enduracoatings.com.
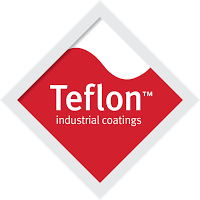
The 3-coat Improved Standard is the premium Teflon™coating line reinforced for scratch resistance and durability. The line is for end-uses that require non-stick, high lubricity thermal stability to 500 °F. Decades of innovation and technology have led to this water-based, multi-color system with a unique blend of PTFE, PFA, and FEP fluoropolymer chemistry. The primer utilizes On-Smooth technology for easy adhesion to smooth surfaces when needed. When your application requires ultimate release and superior durability, 3-coat Improved Standard should be your choice of the Teflon™ products.
The 3-coat Improved Standard is a blend of Teflon™ fluoropolymers with great features and performance benefits that create superior durability and premium properties. The easy, single cure application and reinforced primer and mid-layer make this product superior in durability. This high-performing system comes in blue, black, and dark pewter.
For more information on the 3-Coat Improved Standard coating, visit our information sheet here. Please direct any questions or concerns to Intech Services, Inc. at (302) 366-8530. We would love to assist you in your purchasing and answer any questions you may have.
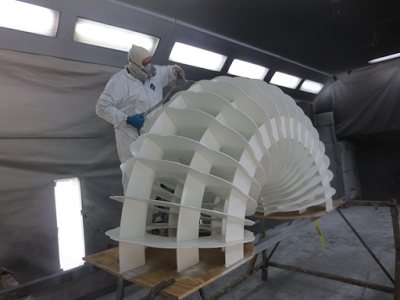
Cleaners come in both powder and liquid forms. There are different types of each form, including the following:
- Acid cleaners are best for metallic or inorganic soils
- Alkaline cleaners are often used for organic soils
- Soils on substrates that react with strong acids or alkalis are usually removed by neutral cleaners
When high levels of oil build inside of the substrate, oil-splitting cleaners will be best. In order to decide which cleaner is best for you, contact a pretreatment supplier.
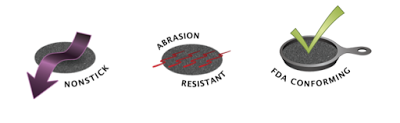
Looking for non-stick capability? Abrasion and scratch resistance? The 2-Coat Reinforced is the premium Teflon™ coating line for end-uses that require non-stick capability, abrasion or scratch resistance, thermal stability to 500°F, and durability in a thin film coating. Decades of innovation and technology have led to this water-based system with a unique blend of PTFE, PFA, and FEP fluoropolymer chemistry. The primer utilizes On-Smooth technology for easy adhesion to smooth surfaces when needed. If your application requires ultimate release and superior durability at a great value, 2-Coat Reinforced should be your choice of Teflon™.
With great features and performance benefits, a blend of Teflon fluoropolymers that together create superior durability and premium properties, this product peaks above the rest in resilience and reliability. Additionally, with the coating’s fairly simple application and shining black hue, your choice of coating is made easy.
For more information on this 2-Coat Reinforced coating, visit our information sheet. Please direct any questions or concerns to Intech Services, Inc. at (302) 366-8530. We would love to assist you in your purchasing and answer any questions you may have.
Chris Lord is the segment leader for Teflon™ applications in the Molding industry. We sat down and picked his brain about applications of Teflon finishes in the molding world. Read on to find out about current and future uses of Teflon coatings as a mold release agent.
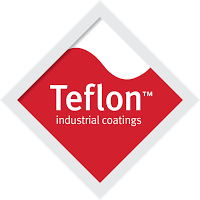
Q: What problems are prevalent in the molding industry?
Chris: Many manufacturers rely on temporary mold release agents on their molds. While this may seem adequate, these temporary mold release agents simply do not provide consistent, long-term performance. Coating with Teflon provides a long lasting and more reliable solution for mold release.
Q: What are the benefits of using Teflon coatings?
Chris: In working with manufacturers, we have been able to document many areas where Teflon coating has had a positive impact on their business. Some of these areas include improved product quality and consistency, enhanced process efficiency, reduced cost of release agents and mold cleaning, fewer defects and scrap rates, as well as a decrease in demand for manpower. The benefits also include a safer work environment and reduced wastewater.
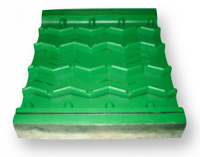
Q: What Teflon coating system(s) work best for applications in the molding industry?
Chris: Generally speaking, FEP is the top fluoropolymer coating for this industry. However, depending on the specific process and materials being molded, PFA and PTFE may also be ideal candidates. My job is to find the system that works best for the specific end user environment.
Q: Are there new technologies in development for the molding industry?
Chris: Intech and the Chemours R&D team are actively working on new coating technologies that will provide even better durability and release. We are also working on new products for areas where our coatings have not been utilized in the past. It is exciting to see the growing interest in this market segment. I receive daily inquiries for new molding applications.
For further information on Teflon coatings in the molding industry, contact Intech Services Inc. at (302) 366-8530, and ask for Chris Lord.
Intech Services, Inc. is proud to announce the arrival of 958G-313 abrasion resistant, black, PTFE dry lubrication coatings. This product is closely related to 958G-303, which has been an industry standard for dry lubrication applications for decades.
958G-313, 0.6-0.8 mils dry film thickness (dft), provides another option for end-users and engineers who need more durability in a thin film coating. The addition of this coating to the list of quality Teflon™ finishes provides coaters and specifiers with four dry lubrication product choices to suit their performance coating needs!
958G-303 is still recommended for dry lubrication in a thin film; however, if added durability is required, we now have both thick and thin film options to choose from:
- 958G-406 (4 mils dft) abrasion resistant, black
- 958G-414 (4 mils max dft) extra abrasion resistant, dark green
- 958G-313 (0.6-0.8 mils dft) abrasion resistant, black
All of these products are in stock at Intech Services with no required minimum order quantity to purchase.
Within the automotive industry, the use of Teflon™ is driven by vehicle enhancements and the need for light-weighting vehicles. Better fuel efficiency and anti-squeak, quiet cars both influence the coating industry as well. Teflon materials can soften the NVH (noise vibration or harshness) of the car and protect the car from vibration, corrosion, and over-lubrication. Teflon provides vehicles with enhancements that allow them to function correctly while staying under warranty and solves problems with anticorrosion, dry lubrication, and noise cancellation properties.
Automotive is a highly specified industry, and many people attempt to promote Teflon-like coatings. Yet, Teflon is the original. It is not a mere copy or tweaked version of coating. Nonetheless, Teflon consistently tries to look for ways to improve its product, and as specs and cars get more challenging and increasingly better, manufacturers want to utilize a company that they can trust.
Customers are encouraged to contact Chris Lord with any questions about internal operating efficiency, dry lubrication, thin film, durability, corrosion resistance, chemical resistance, and more.
For more information regarding the automotive industry, contact Automotive Market Segment Leader, Chris Lord:
Office: (302) 366-8530 x 104
Cell: (302) 547-1610
clord@intechservices.com
Intech Services is excited to keep you updated on the latest news about the spinoff of DuPont into The Chemours Company. Today, we are letting you know that the new labels for Teflon™ are here. While the product is the same Teflon™ you’ve known, used, and loved, the label’s look is brand new. Below is a photo of the new labels. The orange band and The Chemours Company logo are at the top. The code and coating description are in larger, block font. To read more about the spinoff to The Chemours Company, visit Understanding The Chemours Transition.
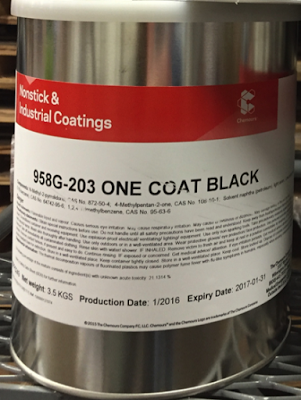
Curt Jarrell of Newco Industrial Services has had a long-standing, devoted career with Teflon™ industrial finishings, and has had several accomplishments in the industrial coating field. He was one of the early adopters of Teflon™ and helped to shape the way the coating has grown and evolved to be a reputable industrial fluoropolymer.
Newco Industrial Services is located in Fairburn Georgia and has been applying Teflon™ industrial coatings for the past five years. They specialize in applying technologically advanced coatings to enhance and improve the properties for release, nonstick, low friction, abrasion-, wear-, and corrosion-resistance, dry-film lubrication, galling, noise reduction, high temperature, and FDA-compliance. Curt generously took some time to speak with us and share some of his successes, challenges, and views on the future of the industrial coating industry.
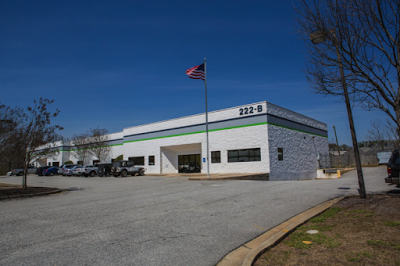
Q: When was your company founded?
Newco was founded in 1996.
Q: Who founded the company and why?
Gerry Hicks founded Newco with the primary purpose being to serve the diaper industry. Actually, it was to serve the equipment that manufactures diapers and feminine care products. The company was built around the equipment side of things that needed coatings. There was a need for coatings because diaper construction uses an adhesive that is very sticky. You can’t run the line without some kind of coating.
Q: What was the first significant piece of equipment you purchased?
We purchased grit blast equipment, ovens, and a spray booth all at the same time.
Q: How would you describe the changes in the company from when it was first started to now
? The company has really expanded. We do a lot of work in the food industry. Our biggest segment is the automotive industry. We do a lot of work with the robots that build cars and a lot of the sealants that are used to seal the windows in and seal the body. Much of that requires coating because there is a lot of urethane involved. We do work with several companies in the food industry and feminine care industry. So the biggest change has been the overall expansion. The company is five times the size it was when it started.
Q: What would you consider significant milestones in your company?
Probably the most significant are the problems that we solve. We are a reliability- centered maintenance type company. So what we do is go in and do recall analysis, mode of failure for problems that they have, and keep their cost down and their manufacturing up to keep their run time up. An example of a significant milestone for us is at Mercedes. We had 27/28 reliability projects, which were initiatives we created for them within the past year. For us, the most significant milestone is serving our customers well. To be able to help them with their problems and make them more competitive and more successful with what they are doing. Coating fits into that because so many times coating will extend the life of a part making the process work better. For example, a significant milestone was enabling sugar manufacturers to go from forty bags a minute to sixty bags a minute with a more accurate weight. It saved them $600,000.00 a year on their line. Everything for us is customer centered, which is anything we can do to make things better for them, and coatings play a big role in that.
Q: How has the coating industry itself changed over time?
One of the big things we’ve seen, as coatings have been around a long time, is higher customer awareness, which sometimes can be negative. They see coatings as something that belongs on cookware, and we serve the industrial market. We have seen better performance, better durability, and better selection. Selecting the right coating for the right application has changed the perceptions of many. The greater awareness of coatings mostly came from the cookware industry and was not well understood in the industrial market until we come in to help match up the coating to the application.
Q: When did you get your LIA license from DuPont?
I’ve had 2 LIA licenses. I had one at my previous company and have one at my current company that I have had for the past 4-5 years.
Q: How has being an LIA affected your company?
The biggest effect is the credibility it creates. We have a lot of international customers: Mercedes, BMW, Hyundai, and Kia. The legacy of Teflon™ carries a lot of weight. So that is the biggest impact.
Q: What is your favorite Teflon™ coating?My favorite would be Ruby Red. It’s just a versatile coating for the industrial market. It can do a lot of things: it has high durability and a strong chemical application, and you can use it where you need nonstick and abrasion resistance. It holds up well. You can change the thickness of it to accommodate a high wear application. Abrasion and chemical resistance as well as nonstick and overall ability to tailor to the application is pretty.
Q: What excites you about the future of the coating industry?
The thing that excites me the most is that coatings have been around since the 30s, yet in the future there will always a spot for coatings. They’re timeless. So, I don’t think we’ve reached the end of the road yet, and that’s pretty exciting.
Curt’s contributions to TeflonTM and the industrial coating field as a whole are great successes within our industry. We extend our thanks to Curt Jarrell of Newco Industrial Services.
AST And PQ’s Partnership For An Equipped Industrial Oven Solution
The Intech team is proud to highlight an industrial oven success story from our vendor, Precision Quincy Ovens, an industry-leading manufacturer of industrial ovens.
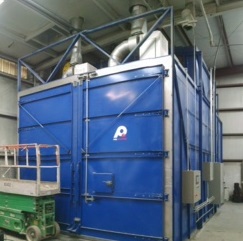
AST/ACME needed new, durable industrial ovens for their latest application opportunity. After careful evaluation, AST chose Precision Quincy Ovens to meet the needs of the new project because of the design and build of the products. Through this agreement, Precision Quincy was able to provide AST with the highly intuitive, large capacity oven their new application required. With Precision Quincy, AST gained a state-of-the-art oven specifically created for their particular needs.
Precision Quincy has helped AST and its skilled employees:
- Meet their new application needs
- Change oven profiles quickly and easily with very low user error
- Avoid profiles that are too difficult to set, change, and monitor
- Multi-task easily and without worry of improper cure
- Produce consistent, quality parts because of consistent oven airflow and uniformity
- Record detailed data using oven thermocouples, which enable AST to share the data to ensure customers the cure process was done correctly
- Coat extremely large substrates, opening up many new application opportunities
- Significantly decrease bake time by increasing ramp rate and reducing soak times
- Record and analyze bake data to optimize all bake processes
- Increase production and coating possibilities
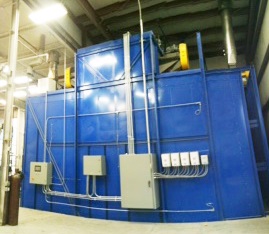
Building a relationship with Precision Quincy for a new, custom, state-of-the-art industrial oven creates a long-term destination for AST’s business and provides a roadmap for moving forward, enhancing quality and growth in the industrial coating industry.
AST can protect their investment with Precision Quincy’s outstanding Preventative Maintenance service plans. These service programs are designed to suit the individual needs of any company and include emergency services and technical help.
Click here to read the full case study.
For information on new Precision Quincy ovens, contact sales@pqovens.com
There are a variety of methods that will clean and remove soils from metals. The pretreatment method used is determined by the part to be coated (size, configuration, and material), the type of soil to be removed (dust, wax, and oil) and the performance requirements of the finished product. This process of pretreatment requires three steps. The first two steps are explained the previous pretreatment blog post, below is the final pretreatment step.
CHEMICAL CONVERSION OF THE SURFACE
Phosphating, or conversion coating, is the application of a phosphate coating to the substrate. The most common conversion coatings are iron and zinc phosphate which are applied for the following purposes:
- Provide temporary in-process corrosion protection before application of powder coating
- Converts the substrate into a uniform surface, promoting good adhesion of the powder coating
- Provide under-paint corrosion inhibitor to improve the life of the powder coating
The end product is the most important factor when deciding between iron and zinc phosphate. Iron works well for indoor use in non-corrosive environments and has several economic and environmental advantages. When undercoat protection is needed in a more demanding outdoor, corrosive environment, zinc phosphate is the better option.
Pretreatment is the base for powder coating. The highest quality powder coating will show you excellent results ONLY if the pretreatment is done correctly, maximizing the benefits of powder coating. Oily patches, pin holes, rust spots, reduced resistance to weather, and overall poor powder coating performance will result with improper pretreatment.
The following table compares iron and zinc phosphate processes in more detail.
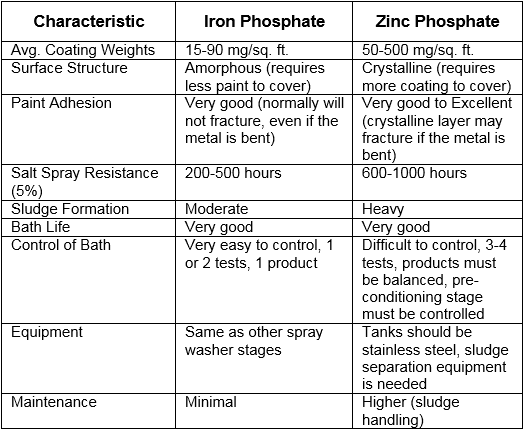
Have a question about pretreatment? Contact our technical help today for advice from an expert. Or you can always reference our trouble shooting guide online first.
There are a variety of methods that will clean and remove soils from metals. The pretreatment method used is determined by the part to be coated (size, configuration, material), the type of soil to be removed (dust, wax, oil, etc.), and the performance requirements of the finished product. This process of pretreatment requires three steps. The first two steps are explained in detail below, and look for the third step in a later blog.
1. CLEANING
Mechanical cleaning – includes methods like scratch brushing and sand blasting. This abrasive action not only removes the surface impurities but also eliminates scratches and surface irregularities. Mechanical cleaning is sometimes the only way to remove excessive dirt, rust, or scale but can be labor intensive and expensive.
Chemical cleaning – includes removal of dirt, oil, and grease present on the surface by means of chemicals. The chemicals may be applied by wiping, spraying, or dipping, which depends on the soils to be removed, the size and type of the part, the type of coating to be applied, and the substrate material.
2. RINSE
Proper rinsing between process stages removes any remaining contaminated solutions from the substrate surface and is essential for successful pretreatment and coating performance.
Pretreatment is the base for powder coating. The highest quality powder coating will show you excellent results ONLY if the pretreatment is done correctly, maximizing the benefits of powder coating. Oily patches, pin holes, rust spots, reduced resistance to weather, and overall poor powder coating performance will result with improper pretreatment.
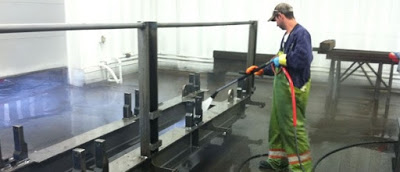
Have a question about pretreatment? Contact our technical help today for advice from an expert. Or you can always reference our trouble shooting guide online first.
In search of an economical coating solution that provides excellent release and durability? Check out Teflon™ FEP (fluorinated etheylene propylene copolymer) single coatings. This high performance, thin film combines fluoropolymers with binder resin and is thermally set with flexible cure temperatures. There are seven options of different FEP one coats, four with an Epoxy resin and three with a PAI resin. Primarily water-based liquids, there is one powder form available. By providing high release and durability, as well as great chemical and abrasion resistance, the FEP one coats are the high performing, easy-to-use coating to choose when in need of a thin film solution.
Properties of FEP One Coats:
- Excellent non-stick or release
- Excellent durability
- Good chemical resistance and abrasion resistance
- Economical single-coat application
- Flexible cure temperatures
Click here to view information about FEP One Coats on our website.
Click here to download a PDF of the marketing piece.

The US commercial water and sewer industry includes approximately 5,000 companies who generate an estimated $9 billion in annual revenue. Their primary focus is on companies that provide equipment and services to communities, chemical facilities, and food manufacturers with water treatment issues. The commercial segment of the water treatment industry is relatively small compared to the $55 billion spent annually on water and sewage services by regional and local governments. With continued population growth and more stringent drinking water standards, the EPA estimates the industry will be spending some $280 billion to upgrade facilities during the next 20 years.
The market is concentrated, with the 50 largest companies (e.g., American Water Works, California Water, Aqua America, etc.) accounting for nearly 65% of overall revenue. The industry is expected to continue to consolidate, as larger companies find it easier to gain capital funding for expensive maintenance projects.
Key Benefits of Teflon™ industrial coatings:

Typical Applications:
- T bolts for ductile iron water pipe – anti-galling with corrosion resistance
- Grates – releases build up of sediment material that occurs during the waste process
- Pumps – minor chemical resistance and low COF
For more information on the coating markets for Teflon™ industrial coatings and resources available, visit our Solution Center
Proper oven calibration is essential to consistency and quality control. If industrial ovens temperatures are not properly calibrated, you run the risk of improper curing, incomplete drying, and a costly waste of energy and product. Even minor alterations in temperature can compromise the integrity of your product, Therefore it’s important to follow a regular oven calibration schedule.Benefits of PQ’s Oven Calibration Service:
- Ensures oven operates consistently and correctly
- Highly trained experts with onsite service
- Flexible service options
- Gain peace of mind that your oven is performing optimally and meeting your specific process needs
- Services any make and model oven
By choosing one of PQ’s Preventative Maintenance Programs, your oven will be serviced by those that know your equipment best, ensuring long-term performance and reliability of your oven. The Preventative Maintenance Service Programs are designed to suit the individual needs of any company.
Call for a quote today! Contact Cheryl Goldstein today at 302-602-8738 or emailservice@pqovens.com.
To read our more information about our services, download our service catalog.
Useful for lowering viscosity of Teflon™ coatings as well as keeping spray equipment clean and at optimal functioning.
Product Overview
Teflon™ thinners can be used for jobs where a lower viscosity is needed or for cleaning and maintaining your spray equipment. Thinners are a cost effective and simple way to clean spray guns by simply running thinner through the gun to clean out the coating from the passage. Well-maintained guns apply coatings with more efficiency and uniformity, as well as save time and money caused by equipment breakdowns. TN-8595 can be used for thinning and cleaning 420G, 958G, and 959G solvent-based products.
Thinner |
Clean Up and Viscosity Reduction |
TN-8595 |
420G line 958G line 959G line |
TN-8748 |
954G line |
Deionized water |
All water-based products |
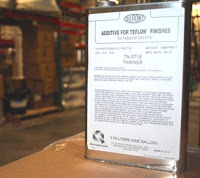
Uses
- Used to thin material for jobs that require low viscosity
- Easy clean up for certain solvent-based Teflon™ product lines
Aplication Processes
To clean with TN-8595/8718/8748:
Run some thinner through the gun through the spray equipment, just as if it were a coating.
To reduce material with TN-8595/8748:
- It is recommended that you do so in small increments, around 2-3% at a time, typically no more than 5-6% overall
- After adding thinner, the material should be re-incorporated by rolling.
- Rolling is the preferred re-incorporation method for liquid Teflon™ coatings.
- De-ionized water is recommended for reduction and and clean up of water-based products
Effects
The reduction of the liquid coatings will change the performance properties of the finished coating and the coating mixture while spraying. Thinning can have effects on:
- The appearance of the finished product
- The performance quality of the coating
- Increase the sensitivity to the required bake cycles
- Shorten the pot life of the material
Technicians should be aware of these potential changes when applying reduced material.
Marketing Material
To download this information in a PDF, click here.
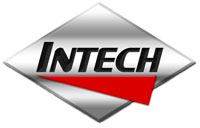
Mike Patterson, President of Intech Services in Newark, DE is celebrating his 20th anniversary with the company this year. Mike’s start with Intech came when he was going through the interview process following college graduation. He needed a job, and Intech offered him the opportunity to fill a “short term” gap in his search. At the time, Mike was one of four employees at Intech; it was co-owned by Mike’s father Bob Patterson and Bob’s business partner, BobKacmarcik. Mike’s mother Jean also worked at Intech, making it a genuinely small, family business. Like many small businesses, employees wore many hats.In the morning Mike would work in the warehouse then spend the rest of the day doing technical sales and service, accounts receivable, order entry, customer service, labeling, and checking order supply.
His position with Intech enabled him to travel and gain a better understanding of Teflon™ coatings, cultivating an excitement for a career in Teflon™ coatings. Mike enjoyed having the opportunity to visit customers across the country and advise them on how Teflon™ could make their business better. Realizing he wanted to learn more, Mike decided to continue his education and completed his MBA in 1997. The practical knowledge he gained from his masters program left him better prepared to understand the mechanics of running a small business. However, his formal education was only the first in a number of steps he would take to evolve into the role of President and owner he has today.
While Mike’s evolution with Intech has had several significant milestones, the first was in 1998 when Mike bought part of the company from his father, Bob Patterson, part owner, who was retiring. Mike, now partners in ownership with Bob Kacmarcik, became president in 2006. Under Mike’s budding leadership, diversification and growth for Intech became priorities resulting in the development and implementation of Intech Marketplace in 2007. In 2009, Mike acquired complete ownership of Intech. While sole owner, Mike kept the influences of leaders before him top of mind. He combined his father’s strong knowledge of the technical side of the industry, including products, markets, and customers with Bob Kacmarcik’s keen understanding of business principles and strategy, as well as the political aspects of working with a large corporations such as DuPont. Mike continued to build Intech Services to be a resource for customers beyond just distributing. Mike saw Intech as a place to help customers with issues regarding coating, processing, equipment sourcing, shop layout, and so much more. He wanted to originate a program that allowed customers to interact with technical staff, improving their shop processes in a fun, interactive way. In 2009 he achieved this goal by establishing Intech Information Institute, or I3,providing a forum for coaters and technicians to meet face-to-face and discuss ways to use Teflon™ better. By combining the wisdom of his influencers with his own drive to innovate, the future of Intech began to take shape.
Under Mike’s sole ownership, Intech upgraded to include new web capabilities, software systems, a company-wide transition to Apple platform, the addition of a marketing department, and more. In 2011, the company moved from a small office/warehouse to the larger, more modern facility it is in today. Mike’s unwavering commitment to invest in improving the efficiency and effectiveness of his business remains a source of motivation to his employees. “Mike has the ability to inspire all of us at Intech Services. He has been our lighthouse, providing a bright and clear strategic direction for us all over the past 20 years. His leadership is what transformed this company from a single service organization to its current multi-platform sales and marketing company,” says Chris Dohl, Vice President.
As the company has increased from 4 to 24 people in the past 24 years, Mike’s greatest satisfaction comes from seeing his employees grow and the pride he feels in seeing their accomplishments. “The team culture established within the company has allowed people the chance to create their own destiny, which is a really cool thing,” says Mike. Employees have already recognized Mike’s vision. “Mike makes everyone feel like part of the team. He is a very approachable leader with a competitive nature and passion for success,” says Ken Barnes, Account Manager.
What does the future hold for Mike and Intech? “I want to see Intech grow: the company, the culture, and the people. My ultimate goal is to have Intech be a self-sustaining company powered by the employees. That is the evolution of a truly successful business. I am extremely proud of what we have accomplished at Intech. However, we are not even close to being what I think we can and will be in the future.”
Click here to view the press release.
A highly fragmented industry with some 16,000 companies generating annual revenues of approximately $215 billion, the plastic parts manufacturing market will be a “sweet spot” for many coaters to target. Primary market segments include packaging (bottles and wrapping), construction (pipes and insulation), electrical and electronics, and consumer. Typical customers include OEMs in the automotive, aircraft, and medical device markets and large consumer product companies such as Procter and Gamble. Other large prospects include Pactiv, Textron, and Mark IV Industries.

Key Benefits of Teflon™ industrial coatings:
- Release
- Low coefficient of friction
- Abrasion resistance
- Increased hardness
- Corrosion resistance
- Regulatory compliance (FDA)
Typical Applications:

- Rubber molds
- Golf ball cores
- Shoes
- Tire molds
- Rotational molds
- Playground equipment
- Toys
- Kayaks
- Lawn & garden equipment
- Injection molds, foam molds, thermoforming molds, compression molds
- Heat seal bars
For more information on the coating markets for Teflon™ industrial coatings and resources available, visit our Solution Cente
About 1500 companies in the U.S. manufacture and market medicinal drugs, generating combined revenues of over $200 billion. The pharmaceutical industry is highly concentrated, with the 50 largest manufacturers (e.g., Merck, Pfizer, Abbott, Eli Lilly, etc.) accounting for over 80% of the total revenue. Small companies are mainly active in research or the manufacture of non-prescription drugs. The larger companies offer the most potential for coating operations in areas such as chemical resistance and some molding operations in the final packaging stages. Overall industry fundamentals are very positive as the aging of the baby boomer generation promises to increase market demand. The market is driven primarily by the research and development and marketing functions, and speed to market is essential for continued growth.

Key Benefits of Teflon™ industrial coatings:
- Chemical resistance
- Release
- Regulatory compliance (FDA)
- High purity
- Ease of cleaning
Typical Applications:
- Chemical vessels
- Impellers
- Conical blenders
- Ducts
- Vacuum dryers
- Capsule filling equipment
- Pill and capsule packaging
- Heat seal bars
- Gel cap cutting wedge
For more information on the coating markets for Teflon™ industrial coatings and resources available, visit our Solution Center
This series is intended to highlight the long-standing careers of devoted Teflon™ coaters and their accomplishments in the industrial coating field. These pioneers in the Teflon™ coating industry are early adopters of the coating and have helped to shape the way Teflon™ has grown and evolved as a reputable industrial fluoropolymer. With the pioneers’ vision and ingenuity, Teflon™ coating continues to be regarded as the elite fluoropolymer of choice.
Our interview series continues with a spotlight on Mike Klinge of Keco Engineered Coatings, Inc. KECO has been applying Teflon™ industrial coatings for over 28 years and is one of only a select few applicators in the United States with an industrial applicator license. KECO’s coating catalog consists of hundreds of fluoropolymer formulations including Teflon™ PTFE, FEP, and PFA designed to offer a wide range of nonstick attributes.
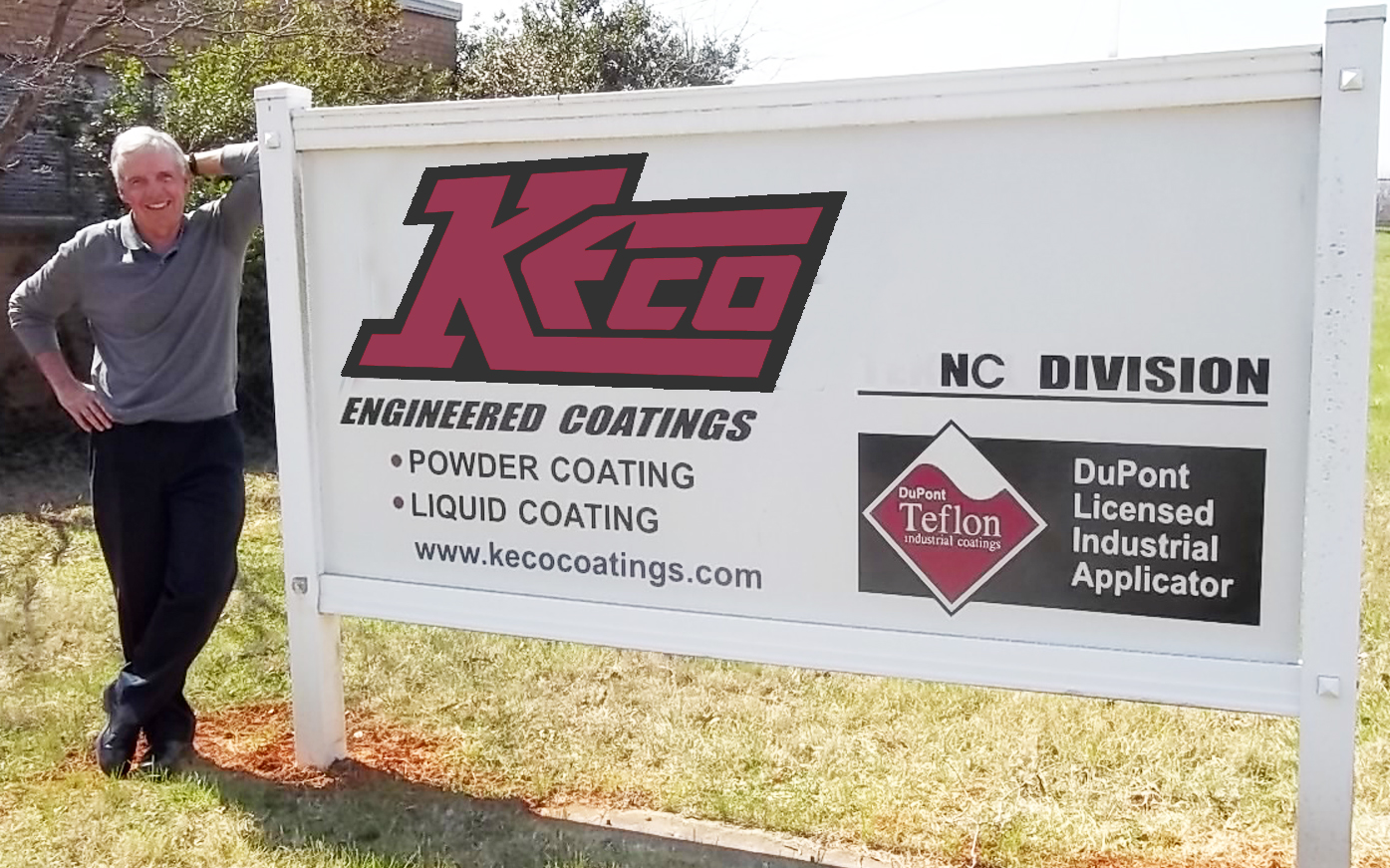
Q: When was your company founded?
A: 1980
Q: Who founded the company and why?
A: I founded the company. My interest started when I was working in a sales position for my grandfather’s industrial painting business that provided military aircraft applications. While serving on an executive committee for the Indianapolis Chapter of Society of Manufacturing Engineers (SME), I heard some of my peers talking about DuPont Teflon™ coatings. So I did some market research and worked with some of those committee members, and I found that I could make a business case for applying Teflon™ coatings. My grandfather was very instrumental in helping me achieve that goal. He could have easily reinvested in new infrastructure and personnel and expanded his business to provide Teflon™ coating applications, but at 80 years old, he supported my idea of starting the business on my own. With his support I started KECO Engineered Coatings.
Q: What was the first significant piece of equipment you purchased?
A: With a $25,000 second mortgage on my house, I purchased a used spray booth, small batch oven, cabinet sand blaster, and fax machine (instrumental at the time!).
Q: How would you describe the changes in the company now from when it was first started?
A: From a footprint standpoint, we purchased the building we were originally leasing, and we increased our infrastructure from 5,000 square feet to 25,000 square feet. We enhanced our regional footprint in 2008, by making an acquisition in North Carolina and adding the DuPont Teflon™ coating process to the facility. We increased our capabilities in Indianapolis, in 2010, by purchasing the real estate and assets of Industrial Coatings Services (ICS), as well as, rehiring the key legacy employees of ICS to enhance our production, quality, and process engineering team. One thing that hasn’t changed in the last 35 years is our belief that we are only as good as our team members.
Q: What would you consider significant milestones in your company?
A:
- Receiving the DuPont Teflon™ Licensed Industrial Applicators (LIA) status in 1987.
- Becoming ISO 9000 certified in 1987.
- Becoming an IndyCar series sponsor in the 1990’s, enabling KECO to create company awareness and provide a platform to entertain customers and suppliers.
- Co-founding the Racing for Corey charity.
- Launching KECO’s first website in 1996.
- Opening a KECO Coatings office in Arizona, in 1998.
- Making the North Carolina acquisition in 2008.
- Purchasing the real estate and assets of ICS in 2010.
- Receiving the second DuPont Teflon™ LIA in North Carolina, in 2013.
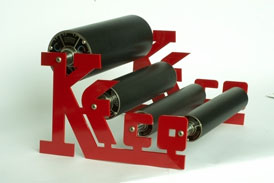
Q: How has the coating industry itself changed over time?
A: Obviously the coating industry is a huge category. There are certainly more companies applying Teflon™ coatings today than in 1980; however, we are a firm believer that having competition is healthy, and enables us to constantly improve our service.
Q: When did you get your LIA license from DuPont?
A: Over 25 years ago.
Q: What is your favorite Teflon™ coating?
A: We use various coatings, but significant amounts of Teflon™ S, FEP and PFA. I don’t have a favorite. Teflon™ coatings account for 30 percent of our “bundled” orders. The Tefzel® process is something that we would like to explore deeper in the future.
Q: What excites you about the future of the coating industry?
A: From my lens, there is a real opportunity to reintroduce the Teflon™ coating portfolio to companies who are currently using this technology or have used the technology in the past. Identifying new applications and markets for Teflon™ coatings is challenging, however, it’s exciting as well. We believe that increasing the understanding of the technology and the added value, while reducing costs for customers, will provide organic growth for companies like KECO as well as the category in general. We get excited when we see this happen.
We appreciate the time Mike took to help us with this interview series. To learn more about becoming a member of the LIA network or telling your Teflon™ story, email april@intechservices.com.
The DuPont™ Teflon® 420G-line is used primarily in the food processing industry because of its excellent release qualities. Compared to a competitor’s FDA-conforming one-coat, the DuPont™ Teflon® 420G-line has several competitive advantages over the other coating, including better release, a lower coefficient of friction, and higher abrasion resistance. The following test results show that Teflon® 420G coatings are superior to the competition and are a long-lasting coating solution in the food processing industry.
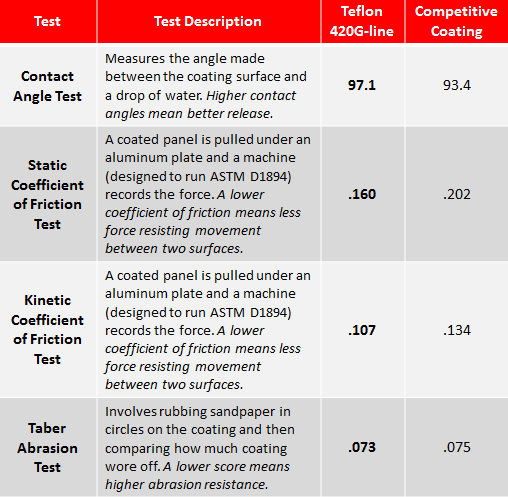
Teflon® Coatings’ Superior Performance Qualities:
- Stratification: DuPont™ Teflon® industrial coatings stratify while curing, which means the fluoropolymer rises to the top of the coating and the resin stays on the bottom close to the substrate. Stratification results in better release qualities from the fluoropolymer on the top and higher durability from the resin on the bottom. The competition’s coating does not stratify.
- Chemistry: Reverse engineering of the coatings found that Teflon® coatings contain PTFE and PES resin, while the competitive coating contains PTFE, FEP, and PES resin.
- Fluoropolymer Ratio: Teflon® coatings have a higher ratio of fluoropolymer to resin than the competition, which means there is more fluoropolymer in the coating.
- Property Comparison: The 420G-line has better release, a lower coefficient of friction, and showed a higher resistance to wear and abrasion than the competitor’s one-coat.
Introducing an FDA One-Coat Competitive Analysis Marketing Piece:
We have created a marketing piece for you to utilize in your sales efforts with customers. You can download a copy of this marketing piece here. If you would like to see the full testing data, please contact Intech to request the data sheet.
Teflon™ FEP coatings provide outstanding low-temperature toughness and unique flame resistance, as well as excellent nonstick properties and a low coefficient of friction.
Teflon™ ETFE coatings are exceptionally tough and abrasion resistant coatings with both water-based and powder offerings, high film build capabilities, and industry-leading chemical resistance.
To download a PDF of the marketing piece for FEP coatings, click here.
To download a PDF of the marketing piece for ETFE coatings, click here.
To see this information on the web, visit Intech Services website
This summer Intech Services has provided a series of blogs dedicated to the Teflon™ coating selection process. In order to select the right product for your coating job, there are three important areas that need to be understood:
- Understanding the Project
- Understanding the Part
- Understanding the End-Use Environment
Within each of these areas are vital questions that need to be answered to ensure the most effective coating for the job at hand.
The third and final newsletter in the summer series will focus on Understanding the End-Use Environment.
Understanding the End-Use Environment:
- What is the end-use service temperature?
- Will there be chemical exposure?
- Weak acids and bases: PFA, ETFE, or One Coats
- Srong acids and bases: PFA or ETFE with thicker DFT
- Vapors and permeation issues: Filled ETFE or PFA
- Will the part be in contact with food?
- All product lines have FDA-conforming products.
- Primer and topcoats must all be FDA-conforming.
- Are there any abrasion/durability concerns?
- PFA and ETFE: Very tough with thick film capability
- Ceramic reinforced specialty systems: 857G-040, 857G-140, and 857G-240
- Filled PFA powder: Knight Armor PFA 532G-13032
- PTFE One Coats: 958G-406 Abrasion Resistant Black and 958G-414 “The Green Monster”
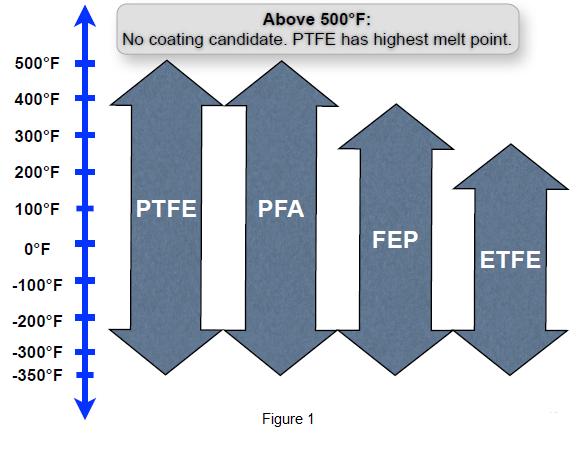
For additional resources on the coating selection process please contact us directly at 302-366-8530, refer to the Compass Corrosion Guide, or refer to our Comparative Property Chart.
Teflon™ coatings are primary used in
the oil and gas field service category, a market that consists of some 8,000 companies with a combined $89 billion in annual revenue. The field service and equipment industry is very fragmented and while there are some large players (e.g., FMC, Schlumberger, Haliburton, Baker Hughes, etc.), over half of the companies in the oil and gas services market employ fewer than 5 people. Not surprisingly, there is a heavy geographical concentration in Texas and the Gulf of Mexico in the U.S., while activity in Canada is centered in the Edmonton and Calgary markets. The demand for coating parts is primarily driven by new equipment manufacturing. The U.S. government’s recently issued target to reduce oil imports from the Middle East by 75% by the year 2025 represents an additional market driver that promises to boost business growth significantly in North America.
Key Benefits of Teflon™ industrial coatings:
- Corrosion resistance
- Chemical resistance
- Low coefficient of friction
- Anti-galling
Typical Applications:
- Fasteners – Anti-galling with corrosion resistance
- Subsea completions equipment -Anti-galling, corrosion resistance, and minor chemical resistance
- Trees – Subsea trees also known as Christmas trees for above ground applications. Trees control pressure and use fluids and chemicals to control that pressure
- Well Heads
- Manifolds – stations of connection points where all the separate trees flow together, it’s where the oil and gas are combined and balanced from a pressure standpoint. Each tree has a different pressure and content of oil and gas and the manifold balances that pressure and content.
- Sleds – termination junction points used to flow multiple jumpers (pipes) from the trees into one point
- Separators – used in deep drilling sites to separate the liquid from the gas fumes and use that pressure to pump it up to the surface.
- Pump parts – low coefficient of friction is utilized in pump parts, specifically in the oil and sand industry
For more information on the coating markets for Teflon™ industrial coatings and resources available, click
here.
Francesca Vavala
Market Development
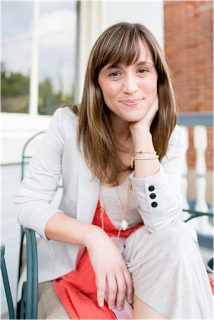
I am thrilled to join Intech Services this year in the role of Market Development. Since becoming a part of the team in January, my primary focus has been working with President Mike Patterson to produce and implement new policies that define and reflect Intech’s unique culture, attract exceptional new talent, and grow the company. The creation of the team structure, open PTO plan, company’s core values, and the ongoing project of writing a new handbook have been fulfilling and exciting.
Recently, I have also assumed the responsibility of exploring potential growth in new markets for our partners. This opportunity is a great way for me to use my skills as a researcher, content writer, and presenter to benefit Intech and our clients. Customers will profit from my critical thinking and assessing potential opportunities to advance their business as well as reap numerous other benefits of my work with Mike to grow Intech’s services and strengthen its internal structure. Prior to working at Intech, I left my position as an English Lit teacher in a local private high school to pursue (and achieved) a successful career as a full time Realtor. My experience as an entrepreneur in sales and business development along with my passion for reading, writing, and researching provided the perfect skillset to step into my role at Intech.
When not at Intech, I enjoy running in perfect weather, getting to the beach whenever possible, petting all the animals, reading good books, and participating in local theater productions.
To reach me directly, you can e-mail me at FrancescaVavala@intechservices.com.
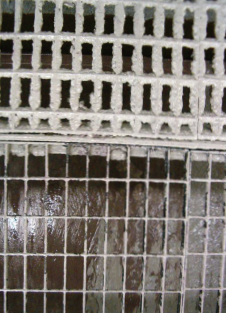
The metal coating industry consists of about 6,000 companies with estimated annual revenue of $19 billion. Major sub-segments include engraving and coating (50%); electroplating, galvanizing, and anodizing (30%); and heat treatment (20%). Major customers for these fabricators are the auto, aerospace, building construction, petrochemical processing, and utility markets. While most companies are small and compete within a focused niche close to their geographic location, there are some major players such as Tower Automotive, Precoat Metals, and North American Galvanizing and Coating.
Fixturing in these industries can be expensive, and the cleaning process is also expensive and/or hazardous to the environment. The need for industry participants to find more efficient ways to clean fixtures represents a market opportunity for coating companies. In addition, use of Teflon® offers an alternative to current processes such as burn-off (e-coat) and high pressure water washing (wet paint).
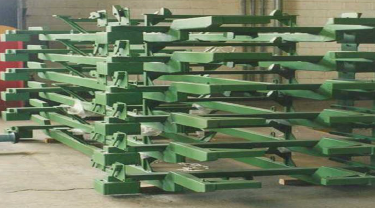
Key Benefits of DuPont™ Teflon® industrial coatings:
Typical Applications:
- Grates
- Car carriers
- E-coat racks
For more information on the coating markets for DuPont™ Teflon® industrial coatings and resources available, visit our Solution Center
All Teflon® product SDS’s have been updated on our website. To see the updated SDS’s, create or login to your account on our website.
What’s the difference between MSDS and SDS?
Both MSDS’s and SDS’s are documents for hazardous substances that explain all the dangers associated with the material and information on handling, storage, and disposal. There were several formats of MSDS’s, so OSHA’s Hazard Communication Standard (HazCom) has been updated to globally standardize the content of all safety data sheets.
Why has this been done?
June 1, 2015 was the deadline by which manufacturers, distributors, and importers must reclassify chemicals and update all SDS’s and labels to the new GHS (Globally Harmonized System) format. The GHS conversion by June 1 was not unique to Chemours (DuPont). It applied to all chemical manufacturers in the US.
The June 1, 2015 deadline is just the next in a series of ongoing deadlines as part of OSHA’s GHS implantation transition. Other important dates include:
- December 1, 2015: Deadline for distributors to eliminate inventory with old labels. Effectively, they can continue using the pre-GHS labeling system until December 1.
- June 1, 2016: The final deadline and date by which employers must be in full compliance with GHS. That means making any necessary updates to their hazard communication programs, training employees on new hazards identified during the reclassification process, updating workplace labels, and anything else required by HazCom 2012.
Our customers are not impacted by the compliance with the regulation. The products have not changed, just how they are labeled.
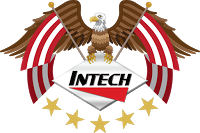
This summer Intech Services will provide a series of blogs dedicated to the Teflon® coating selection process. In order to select the right product for your coating job, there are three important areas that need to be understood:
- Understanding the Project
- Understanding the Part
- Understanding the End-Use Environment
Within each of these areas are vital questions that need to be answered to ensure the most effective coating for the job at hand.
The second in the summer series will focus on Understanding the Part.
Understanding The Part:
- What is the substrate?
- What are the heat limitations of the part?
- Low melt temperatures: Tin, lead, and zinc
- Thin metal concerns: structural integrity, inability to hold heat, and grit blast limitations
- Non-metals: Plastics, glass, wood
- Lowest cure DuPont™ Teflon® industrial coating is 300°F
- What are the part dimensions?
- Can the part fit in the oven?
- Is the part mass consistent?
- Can the surface be grit blasted?
- Will the part be able to hold heat for powder application?
- Can it be removed from the end user’s facility?
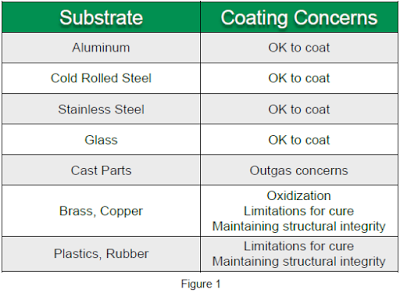
For additional resources on the coating selection process please contact us directly at 302-366-8530, refer to the Compass Corrosion Guide, or refer to our Comparative Property Chart.
This summer Intech Services will provide a series of blogs dedicated to the Teflon® coating selection process. In order to select the right product for your coating job, there are three important areas that need to be understood:
- Understanding the Project
- Understanding the Part
- Understanding the End-Use Environment
Within each of these areas are vital questions that need to be answered to ensure the most effective coating for the job at hand.
The first in the summer series will focus on Understanding the Project.
Understanding The Project:
- What is the reason for coating?
- What has been tried in the past?
- What type of coating was used previously – other fluoropolymer coatings or non-fluoropolymer coatings?
- What were the previous modes of failure – poor coating selection or the process itself?
- Was the coating specified or is it open to change?
- How long did the coating last?
- What is the value of the coating?
- What is the value of the coating relative to the cost?
- Is there enough value to justify the cost for the end user?
- If so, how much value is added with the coating?
- Examples of value:
- Cost savings
- Efficiency
- Less waste
- Less rework

For additional resources on the coating selection process please contact us directly at 302-366-8530, refer to the Compass Corrosion Guide, or refer to our Comparative Property Chart.
Intech Services is dedicated to providing customers with the most accurate information for specific Teflon® coating needs. By assessing the particular requirements, constraints and applications, our technical staff can help guide coaters in the right direction, solve coating problems and improve operational efficiency of the production line.
We are very excited about the creation of Precision Quincy’s new Industrial Ovens Options Brochure.
Intech Services represents Precision Quincy Ovens, an industry-leading manufacturer of many types of industrial ovens. For over 60 years, Precision Quincy Ovens have been used industry-wide across the globe.
For the past few months, Intech and Precision Quincy have been working hard to create a new client brochure. The Precision Quincy Options Brochure is the perfect guide to selecting the right oven options for your process application.
Controllers and Programmers
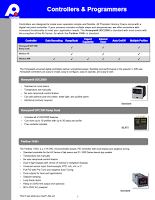
Controllers are designed to make oven operation simple and flexible. All Precision Quincy Ovens come with a digital set point controller, but if your process includes multiple steps and temperatures, we offer controllers with increased functionality to meet your application needs.
Don’t see what you need in the brochure? Just ask us!
Click here to download the Precision Quincy Options Brochure
For new oven inquires, contact sales@pqovens.com.
For parts and service, contact service@pqovens.com.
The medical devices and equipment industry consists of roughly 12,000 companies with a combined annual revenue of $78 billion. The majority of the industry is represented by the makers of surgical and medical instruments, syringes, catheters, and hypodermic needles. The industry is concentrated to the extent that the 50 largest companies (e.g., Johnson and Johnson, Boston Scientific, Baxter, Medtronic, etc.) hold a 60% market share. Manufacturing activity is concentrated in the Northeast.
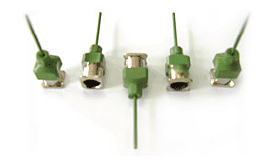
Key Benefits of DuPont™ Teflon® industrial coatings:
- Low coefficient of friction
- Chemical resistance
- Release
- Ease of cleaning
- Regulatory compliance (FDA)
Typical Applications:
- Medical waste trays
- Surgical handles
- Forming mandrels
- Pill molds
- Gel cap molds
- Centrifuge baskets
- Lab equipment
- Dental molds
For more information on the coating markets for DuPont™ Teflon® industrial coatings and resources available, visit our Solution Cente
Teflon® & Tefzel® by Chemours MSDS Sheets Transition To SDS Sheets
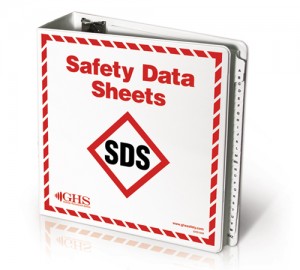
As part of the Global Harmonized Hazmat System created by the United Nations, and adopted by OSHA, traditional MSDS sheets that are now made available by manufacturers and distributors of CAS listed substances and products will be transitioning to a new harmonized safety data sheet (SDS).
The changes are designed to simplify communication regarding hazardous materials and promote international consistency in labeling, compliance, worker and responder training.
MSDS and SDS: What’s the difference?
An MSDS (Material Safety Data Sheet) is a document that accompanies a hazardous chemical, substance or product that has an assigned CAS number. It indicates all the dangers associated with the material, as well as instructions regarding handling, storage and disposal. MSDSs are a key aspect of the Right-to-Know provision of OSHA’s Hazard Communication Standard (HazCom). The HazCom standard is being updated because the earlier version allowed for several formats for an MSDS, including an OSHA version with eight sections and an ANSI version with 16 sections, etc. OSHA’s updated HazCom program, now aligned with the GHS program, requires that all manufactures and end users of CAS listed materials and substances to utilize the new harmonized SDS format.
The “M” in MSDS is being dropped as well. So in short, the name is being simplified, and the format and content are being standardized to global standards.
Timeline For Compliance:
- JUN 01, 2015: Manufacturers and/or importers of any item or substance covered under MSDS (now SDS) requirements will have MSDS sheets (now SDS) available in the new harmonized format.
- DEC 01, 2015: Distributors will have access to, and make available, the new harmonized SDS data sheets.
- JUN 01, 2016: Full OSHA HazCom compliance necessary for employers, manufacturers and distributors.
Teflon® & Tefzel® by Chemours SDS Sheets Available For Download Now – Instructions
All Teflon® & Tefzel® branded fluoropolymer materials are CAS registered products that require Safety Data Sheets (SDS) for each product.
The new Teflon® & Tefzel® SDS sheets can be found on the Fluorogistx website at: https://fluorogistx.com/technical-support/material-safety-data-sheets-msds
- Click the Fluorogistx “Safety Data Sheet” web link provided above.
- Select the appropriate product family.
- Click on the desired product to open the SDS in .pdf format.
- Right click on the document to Save As to any location you wish.
*Additional information on the MSDS to SDS transition can be found here:
https://www.osha.gov/Publications/HazComm_QuickCard_SafetyData.html
https://www.osha.gov/Publications/OSHA3514.pdf
If you should need assistance in transitioning from MSDS sheets to SDS sheets for any Teflon® or Tefzel® branded material please feel free to contact us.
This series is intended to highlight the long-standing careers of devoted Teflon® coaters and their accomplishments in the industrial coating field. These pioneers in the Teflon® coating industry are early adopters of the coating and have helped to shape the way Teflon® has grown and evolved as a reputable industrial fluoropolymer. With the pioneers’ vision and ingenuity, Teflon® coating continues to be regarded as the elite fluoropolymer of choice.
Our interview series continues with a spotlight on Don Garcia of Boyd Coatings Research Co. Boyd Coatings Research Co. applies a wide varietyof high-performance coatings, specializing in the medical, industrial and aerospace markets. Besides applying virtually every coating from every manufacturer on the market, Boyd manufactures a line of custom-developed fluoropolymer coatings for specialty applications. Boyd is a Licensed Industrial Applicator of Teflon® fluoropolymers including PTFE, ETFE, FEP, and PFA.
Q: When was your company founded?
A: December 10, 1965
Q: Who founded the company and why?
A: Pedro Diaz and Edward Boyd. They considered starting the company while working for a Teflon® coating company and decided they could do a better job servicing the customers. Once they determined they could provide a better service to customers, they started their own company, incorporating in 1965.
Q: What was the first significant piece of equipment you purchased?
A: In 1965, a 9 foot long, 5 foot tall, 5 foot wide oven.
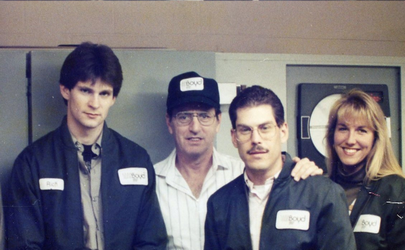
Q: How would you describe the changes in the company now from when it was first started?
A: Wow! It was started on a premise that service and value are what we need to bring to our customers; to give them what they want when they want, in a way that they would want to buy it again. That mind-set hasn’t changed in nearly 50 years. What has changed is the way we provide those services, the systems we employ from physical system to technical support, and all the employee training to give customers the best possible service. So those things have changed but the CORE philosophy of the company hasn’t changed except for the way we do it and how much we do!
Q: What would you consider significant milestones in your company?
A: One milestone would be our focus on engineering and technical expertise. Another would be our quality systems ISO 9001, 2008. The increase in our number of employees as well as our growth and revenue is a significant milestone. On December 10th 2015 we plan on celebrating our biggest milestone, our 50thanniversary!
“It’s the people and the relationships we’ve developed over the 50 years that really have made us successful.”
Q: How has the coating industry itself changed over time?
A: In addition to having to deal with regulatory changes and additional regulatory burdens placed upon us, changes to the science of how we apply coatings and ways to make the process more value-driven have changed as well. There have been significant changes in “how we do what we do” but the basic polymers and their applications haven’t changed. Customer demands for higher quality and lower costs have evoked much of the changes we have seen.
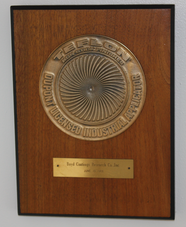
Q: When did you get your LIA license from DuPont?
A:In 1967. We have the original plaque, a substantial piece of brass that has the original LIA swirl. We consider it a nice memento of recognition from DuPont hanging in our lobby.
Q: How has being an LIA affected your company?
A: Being an LIA lends credibility to our business and was especially helpful in our early years when establishing a reputation for excellence was a priority. Back in the 80’s, we were involved with DuPont and the LIA network in providing training for DuPont employees and potential LIA’s, which also helped to further our reputation as leaders in the industry. Today our LIA status continues to provide support that contributes to our continued success.
Q: What is your favorite DuPont coating?
A: For us it would have to be PFA. This coating serves so many different purposes and I think it can be used in so many different applications. Teflon® S also comes to mind, as a general purpose coating that can be used in all kinds of situations. However, from a higher performance standpoint, PFA is the coating of choice!
Q: What excites you about the future of the coating industry?
A: There is still opportunity for these polymers to be employed in new technologies and in new ways. That’s always exciting. We have the opportunity to employ a tried and true material with the highest quality, the quality that DuPont and Intech Services provides us. We can take those polymers and use our ingenuity to apply them in ways that haven’t been done before and make products better or that make life better. That’s always very, very exciting!
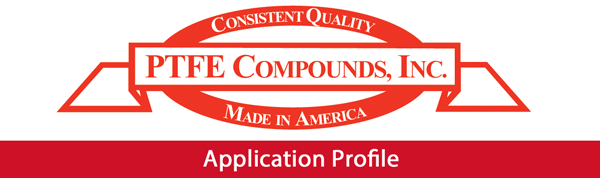
Quality and Consistency in Innovative Compounded Materials
Introduction
PTFE COMPOUNDS, INC., backed by more than 30 years’ experience in the industry, was formed to meet the demanding need for quality and consistency in compounded materials, not only within lots, but from lot to lot as well. Their large capacity blending equipment enables them to offer billet quantities up to 1200 pounds. They provide a homogenous filled compound that ensures uniformity and stripe free skived sheet. Two examples which show the strength of their innovation are TUFFSHEET and PCI Bearing Compound 213.
TUFFSHEET
TUFFSHEET is a new proprietary blend of DuPont Kevlar® and Teflon®, which combines the properties of these materials into a durable low wear composite with reduced deformation and creep resistance. TUFFSHEET is suitable for a wide range of applications such as bushings, dry bearings, thrust washers, dry air compressor rings, gaskets, o-rings, rollers, and wear strips. TUFFSHEET product is available as a low flow compression molding powder, as skived sheet, rolled slit strips, wear-strip (with or without adhesive backing), and CNC machined parts made to customer specifications.
Key Benefits
- Extended Wear Resistance
- Reduced Deformation
- Lower Creep Rate
- Reduced Permeability
- Enhanced Durability
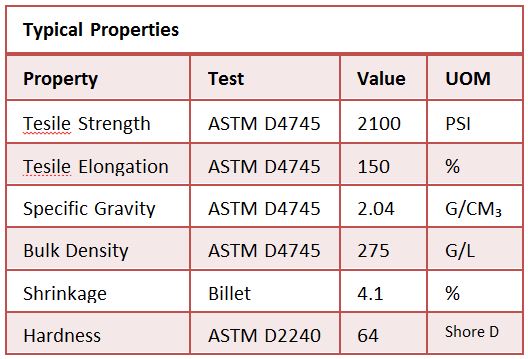
PCI Bearing Compound 213
PCI Bearing Compound 213 is a white molding grade compound containing a white mineral filler blended with Teflon® PTFE. Both the filler and PTFE used in the compound are approved by the FDA for use in food contact applications.
Key Benefits
- Low Coefficient of Friction
- Superior Wear Resistance
- High Operating Temperature
- FDA Compliant
- Low Deformation Under Load
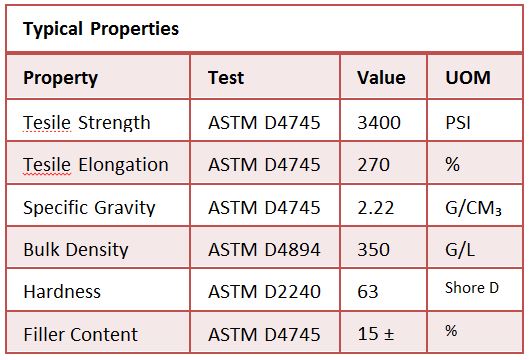
Please contact PTFE Compounds for more information on their product line and manufacturing capabilities.
mail@ptfecompounds.com
Click Here to download a copy of this article.
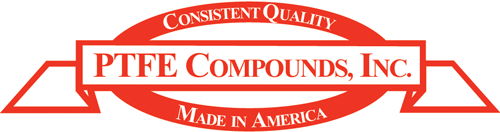
PTFE Compounds, Inc.
Upper Chesapeake Corporate Center
220 Chesapeake Boulevard
Elkton, MD 2192
410-392-9080
In the lighting industry where process conditions can be delicate when coating glass, Teflon® coatings provide the ability to prevent shattering in the manufacture of a broad range of glassware products.
Process conditions can be delicate when coating glass, so experience and good process control are essential to success. Teflon® coatings provide the ability to prevent shattering, and this concept can be used across various glassware products. Similar to what happened in the food processing industry, potential legislation changes that would require shatter-proof bulbs could also drive growth.
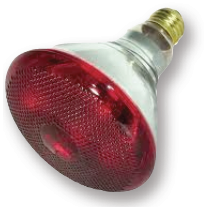
Key Benefits of DuPont™ Teflon® industrial coatings:
- Excellent thermal stability
- Shatter prevention
- FDA-approved
Typical Applications:
- Incandescent light bulbs
- HID bulbs
- Globes
- Lenses
For more information on the coating markets for DuPont™ Teflon® industrial coatings and resources available, visit ourSolution Center
Cookie and Cracker
The cookie and cracker manufacturing industry includes 300 companies for a combined annual revenue of about $10 billion. Cookie and cracker manufacturing begins by grinding starter ingredients like sugar, oils, and flavoring in industrial mixers. Following the initial blend, workers mix in water and bonding agents to form the dough. After the dough is mixed, it is lifted into a hopper and spread onto trays. Once on the tray, the product is cut or rotary cut into shapes. These pieces are then put on conveyor belts for baking and flavoring. Finished products are then packed per their requirement. Large companies include Kraft’s Nabisco subsidiary, Kellogg’s, Campbell’s Pepperidge Farms, Lance, and Interbake Foods.
The industry is highly concentrated with the top 50 companies accounting for 90% of the total revenue. Geographically, food manufacturing is located across the country. Demand is driven by population growth, health concerns, and taste. These products are considered “impulse” consumables and compete against fresh-baked items, fast food, and the candy and chip industry. Companies are profitable by having efficient operations and good marketing groups.
Dairy
The US dairy manufacturing industry consists of 1200 companies that have a combined annual income of $60 billion. The four major segments in this industry are fluid milk, cheese, frozen desserts, and butter. Most companies focus on one segment, although some of the largest companies play in all four segments. Large companies include Land O Lakes, Dean Foods, and Dairy Farmers of America. Because of the nature of the perishable raw materials most production is localized around their raw material supply.
The industry is rapidly consolidating with the 50 largest companies holding 75% of the market. Changes in consumer income drive demand for various types of dairy food. The profitability of individual companies depends on efficient operations and marketing, as milk is a commodity. Manufacturing is standardized across the segments and highly automated.
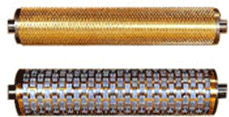
Key Benefits of Teflon™ industrial coatings:
- Extreme temperature resistance
- Nonstick surface
- Low coefficient of friction
- Corrosion resistance
- Compliance with health standards
Typical Applications:
- Cheese products – eliminates problematic build up of dried cheese crust
Fast food restaurants – helps reduce recoating frequency on cooking equipment
- Potato chip manufacturing – helps reduce residue build up by coating knives used to cut potatoes, resulting in less downtime and lower cleaning and maintenance costs
- Processing of pineapple and similar products with high acidity – reduces corrosion caused by acidic juices, reduces need for lubrication with food-grade oil and results in improved replacement frequency levels due to longer life of the housings
For more information on the coating markets for Teflon™ industrial coatings and resources available, click here.
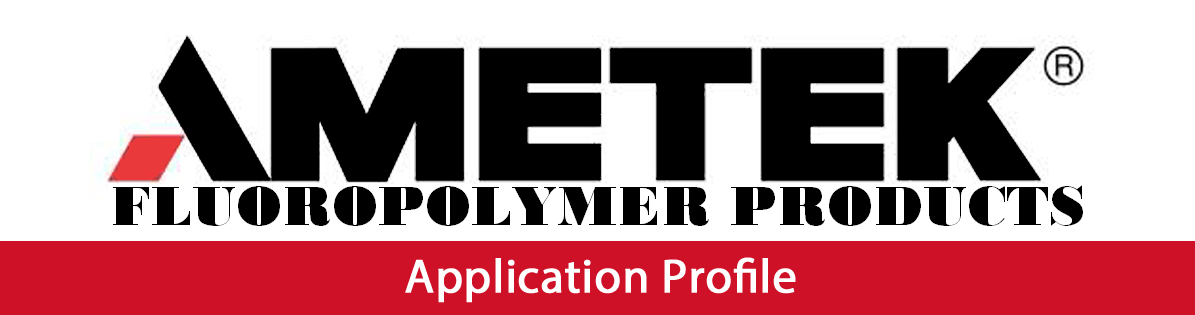
Cooler/Absorber Boosts Efficiency, Resists Corrosives
Introduction
Ametek has developed a patented cooler/absorber for stripping aggressive gases (HCI, SO2, etc.) from chemical or refinery process streams. The versatile design functions like a column with the tubing acting as temperature-controlled packing that can add as well as remove heat. The new design uses clusters of small-diameter tubing made from Ametek’s “Q” resin, a patented thermally conductive compound based on Teflon® PFA fluoropolymer resin and graphite.
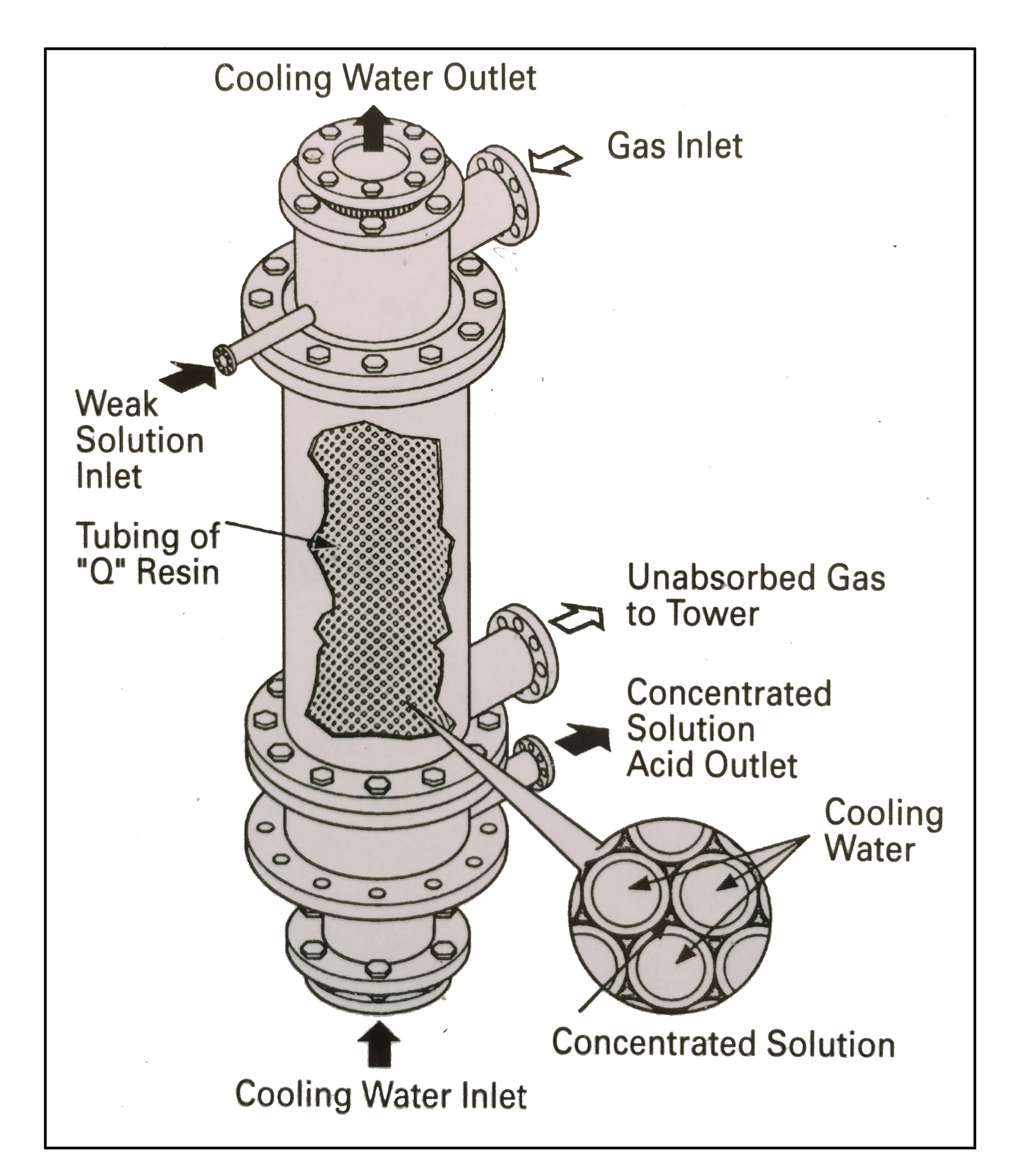
In a typical installation, 1860 tubes measuring 0.125 in. (3.2 mm) in diameter by up to 25 ft. (7.3 m) long are vertically disposed in a steel column lined with Teflon® PTFE fluoropolymer resin. Cooling water flows upward through the heat-conductive tubing. Gas and droplets of water or another absorbing medium flow downward through the column, outside the tubing. The gas dissolves in the absorbing medium, which collects on the outer tubing wall.
The heat of solution is absorbed through the wall by the cooling water.
Clusters of thermally conductive tubing.
Benefits Gained
Corrosion and Heat Resistance
Thanks to the chemical and heat resistance of Teflon®, the cooler/absorber can be used with a wide range of aggressive chemicals at temperatures up to 400°F (204°C)
Smaller, Less Expensive
Ametek says that its units take less space and cost less than conventional designs because “Q” resin has double the thermal conductivity of unfilled fluoropolymers.
More Durability
Ametek reports that its cooler/absorber provides more resistance to thermal and mechanical shock and fouling, and requires less maintenance than traditional graphite units.
Materials Selected and Why
Teflon® PTFE and Teflon® PFA meet needs for broad chemical resistance. Teflon® PFA allows compounding for conductivity and extrusion as small diameter tubing.
Please contact Ametek for more information on their product line and manufacturing capabilities.
info.fpp@ametek.com
Click Here to download a copy of this article.

AMETEK Fluoropolymer Products specializes in highly corrosion resistant, high purity, and high temperature products to serve the chemical processing, metalworking, semiconductor, aerospace, and other industrial applications. Its core products are based on Fluoropolymers, silica and phenolic resins and are marketed under the following trade names: Fluoropolymer Heat Exchangers, Fluoropolymer Tubing, Fluoropolymer Pipe, Havaflex® Ablative Products, and Flexsil® Molten Metal Filters.
Ametek Fluoropolymer Products
455 Corporate Boulevard
Newark, DE 19702
302-456-4431
info.fpp@ametek.com
The National Fire Protection Association’s Bulletin 86 (NFPA 86) is the minimum standard, required by law, establishing fire safety standards, including standards for the safe operation of oven and furnace processes.Understanding and complying with the NFPA 86 standard can minimize the risk of a catastrophic event at your plant and is the single most important thing an oven builder, buyer, and operator can do.This standard is updated on a regular basis with the latest revisions happening in 2015.
There are four classes of ovens as defined by NFPA 86: Class A, B, C, and D. In this blog we will be focusing on direct gas-fired ovens (Class A).
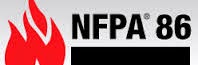
Direct Gas-Fired Ovens: All direct gas-fired ovens carry the Class A rating automatically because they introduce products of combustion into the oven work area. These volatile materials must be exhausted in a forcible manner. Direct gas-fired Class A ovens must include the following safety features:
- Powdered Exhaust Fan – an exhaust fan of sufficient size is necessary to evacuate the required amount of fumes, smoke, etc., eliminating buildup of hazardous materials in the work area
- Extra Airflow Safety Switch – Should the exhaust fan fail, the second switch will shut down the heaters
- Manual Reset Excess Temperature Control – should the unit produce too much heat, the oven will trip and shut down the burner.
- Purge Timer – used prior to heating to remove any flammable vapors and/or gasses that may have entered the work area while the oven was idle.
- Internal Pressure Relief – if a buildup of fumes leads to an explosion, this required feature will ensure that the event has an avenue of “controlled” release.
- High-Low Gas Pressure Switch – should the sensor detect that gas flow is too high or too low, this switch will shut down the oven. Fairly even gas pressure must be supplied to prevent a buildup of combustible vapors.
- Flame Safety/Spark Ignition – this control sends a high voltage signal to the spark plug for ignition, and the pilot gas valve opens to ignite the pilot flame. If no pilot flame is detected, the flame safety stops the attempt at ignition.
Click to view the safety controls specified for Class A and Class B electrically heated ovens.
This is a simple overview of NFPA 86 for class A ovens. Please consult the full NFPA 86 standard for all specifications and additional details.
Contact a Precision Quincy representative today at (302) 602-8738 or sales@pqovens.com for more information on NFPA 86 and how to become compliant.
All Precision Quincy Ovens are of welded steel construction and quality components are used throughout. Each oven is wired and tested at maximum temperature prior to shipping. Ovens meet or exceed NFPA-86, NFPA-70, OSHA & UL requirements.
Robert D. Smith, Bob, Vice President of Sales and Marketing for Fluorogistx LLC located in Greenville, DE. was one of eight recipients of the Wire and Cable Manufacturers’ Alliance’s (WCMA) 2015 Distinguished Career Award. The award was presented to Smith during the 31st annual Awards Dinner Ceremony on March 28, 2015, in Hartford, Conn. at the Connecticut Convention Center. The WCMA’s board of directors selects the new yearly recipients from those of strong character and credibility who have made significant commercial or technical contributions over a minimum 25-year industry career.
“I am honored to receive this distinguished award from the WCMA.
Wire and Cable is an important growth industry for our portfolio of Fluoropolymers.”
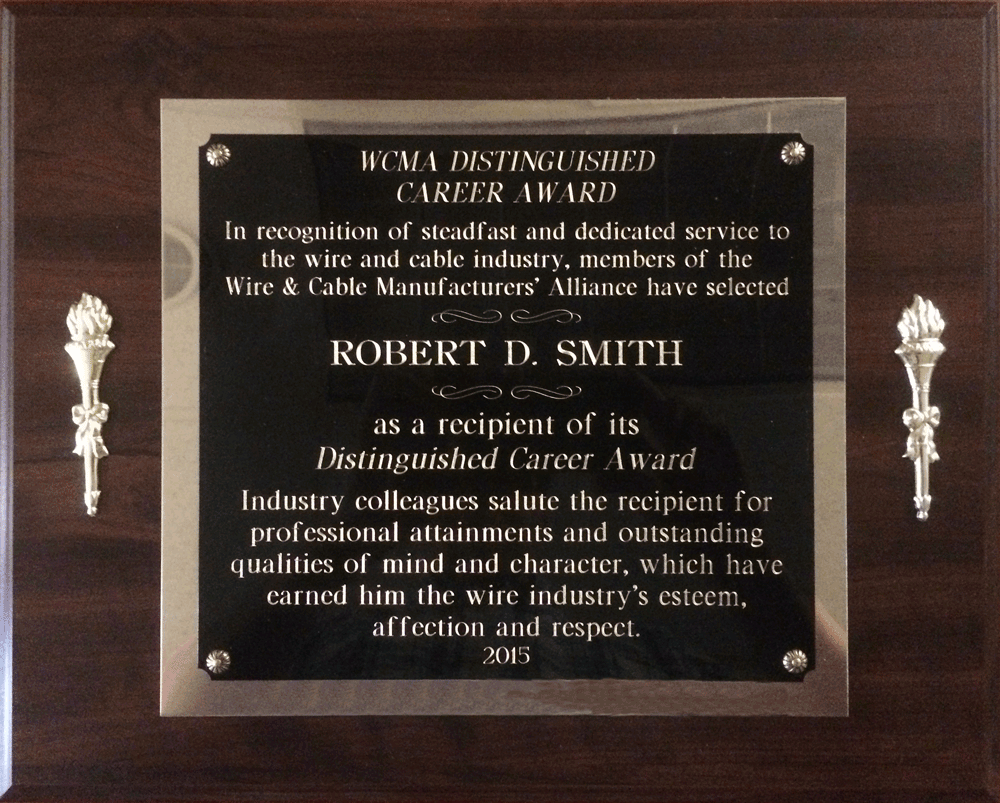
Bob Smith: Vice President of Sales & Marketing
The Wire & Cable Manufacturers’ Alliance (WCMA) is a non-profit trade association for manufacturers of electrical, electronic and fiber optic wire and cable with an established manufacturing base in North America, including the producers of signal and current-carrying wire and fiber, the producers of bulk cables, and wire and cable processors. WCMA was established in 2004 as the successor organization to the Wire & Cable Clubs of America which began the Distinguished Career Award in 1984. WCMA currently has 80 corporate members, with nearly 250 company representatives, concentrated mainly in the northeastern United States.
Bob, a class of 1980 Purdue Chemical Engineer, has 35 years of experience working in the Fluoropolymers industry. He held various U.S. website statistics and International Sales, Marketing and Business Director positions at DuPont before retiring in 2012 to join Fluorogistx to lead Sales and Marketing.
Fluorogistx LLC was established in 1993 as Delaware Marketing Services, Inc., a sales agent for DuPont Teflon® fluoropolymer resins. By 2009, it had become a full-service distribution firm with fully stocked inventories, a dedicated field-sales force, in-house technical support, a large customer service team, and a proven logistical process for meeting customer needs. Today, Fluorogistx continues to be the premier U.S. distributor of high-performance Chemours (vice DuPont) Teflon® fluoropolymers, with strong ties to the customers it serves. Two decades after its establishment, Fluorogistx remains committed to delivering on the promise of its founders: to not only supply the best products for the most demanding applications, but to also be a valued business partner customers can turn to for all their fluoropolymer solutions.
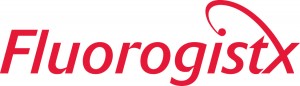
Chemours FluoroPolymer Solutions has announced some upcoming changes to the format of their Material Safety Data Sheets (MSDS).
In anticipation of a June 1st, 2015 regulatory deadline to migrate to GHS formatted Safety Data Sheets (SDS), as mandated by Occupational Safety and Health Administration (OSHA) Hazard Communication Standard 2012; DuPont will begin transitioning to the new format in March of this year.
With this transition, the new SDSs will look very different; in particular, section 3 (the composition section of an SDS) will now list only substances that may lead to hazards. If there are no hazardous components in a product, a statement will read: “Not classified as a hazardous substance or mixture according to the Occupational Safety and Health Administration (OSHA) Hazard Communication Standard 2012.” For example, most of the dry cubes, resins, and powders (Melts, PTFE) will not have any compositional information in section 3, and Dispersion products will only list surfactants.
If you have any questions, please feel free to contact us.
DuPont™ Teflon® Primers are an effective way to prepare a surface before coating is applied. Primers ensure proper adhesion, increase durability, and give additional protection to the substrate. With the use of our primers, the coating is given a smooth surface to bind to, which creates a more protective layer. This additional layer decreases porosity of the coating to the substrate.
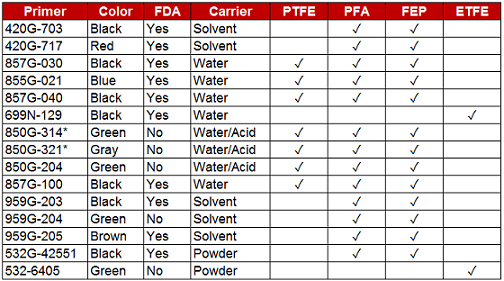
*Mix with 850-7799
Marketing Piece
To download a PDF of the marketing piece for these coatings, click here.
To see this information on the web, visit Intech’s website.
In the US, about 1200 companies produce basic industrial chemicals with a combined annual revenue of $120 billion. Industrial chemicals include gases, dyes and pigments, chlorine and caustic soda, sulfuric and nitric acids, and thousands of organic chemicals. Large companies include Dow, DuPont, and Occidental. The chemical processing industry is highly concentrated, where the 50 largest companies hold 70% or more of the revenue. Operations are generally located close to their raw materials and many need access to large water supplies for their strenuous waste treatment requirements. Some specialty chemicals contain a much larger concentration with only a few suppliers. The demand depends on the overall US economy because these products are primarily raw materials used for more complex products like fibers, paints, plastics, and paper. Efficient operations are the leading profit driver for these companies. Manufacturing companies focus on the highest possible yield for their products.

Key Benefits of Teflon™ industrial coatings:
- Excellent chemical resistance
- High temperature resistance
- Low permeation
- High corrosion resistance
Typical Applications:
- Storage tanks and drums
- Processing tanks
- Reactors
- Pipes and pumps
- Impellors, agitators, and baffles
- Ducts
- Fasteners
- Valves
For more information on the coating markets for Teflon™ industrial coatings and resources available, click here.
The National Fire Protection Association’s Bulletin 86 (NFPA 86) is the minimum standard, required by law, establishing fire safety standards, including standards for the safe operation of oven and furnace processes. Understanding and complying with the NFPA 86 standard can minimize the risk of a catastrophic event at your plant and is the single most important thing an oven builder, buyer, and operator can do. This standard is updated on a regular basis with the latest revisions happening in 2015.
There are four classes of ovens as defined by NFPA 86 – Class A, B, C, and D. In this blog we will be focusing on Class A electrically heated ovens.
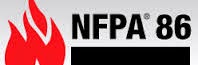
Class A: Electrically heated Class A ovens must have all the safety requirements for Class B as well as the additional items listed below:
- Powdered Exhaust Fan – an exhaust fan of sufficient size is necessary to evacuate the required amount of fumes, smoke, etc., eliminating buildup of hazardous materials in the work area
- Extra Airflow Safety Switch – should the exhaust fan fail, the second switch will shut down the heaters
- Purge Timer – used prior to heating to remove any flammable vapors and/or gasses that may have entered the work area while the oven was idle.
- Extra Kilowatts (if required) – because these ovens will be forcibly removing heat from the work area (via the required exhaust fan), more heaters may be needed to maintain process temperatures. If this issue is not considered in the design stage, the oven may have a poor response time or be unable to reach the operating temperature necessary to run the load.
- Extra Backup Contactors (if extra kilowatts are added) – if the oven is designed with extra kilowatts, additional backup contactors are required to provide adequate safeguards ensuring the heaters shut off if the primary contactors fail.
- Internal Pressure Relief – another extra that must be included in an electrically heated Class A oven is an internal pressure relief. If a buildup of fumes leads to an explosion, this required feature will ensure that the event has an avenue of “controlled” release.
Click here to view the safety controls specified for Class B ovens that are also required for Class A electrically heated ovens in addition to the above requirements.
This is a simple overview of NFPA 86 for Class A ovens. Please consult the full NFPA 86 standard for all specifications and additional details.
Contact a Precision Quincy representative today at (302) 602-8738 or sales@pqovens.com for more information on NFPA 86 and how to become compliant.
All Precision Quincy Ovens are of welded steel construction and quality components are used throughout. Each oven is wired and tested at maximum temperature prior to shipping. Ovens meet or exceed NFPA-86, NFPA-70, OSHA & UL requirements.
The National Fire Protection Association’s Bulletin 86 (NFPA 86) is the minimum standard, required by law, establishing fire safety standards, including standards for the safe operation of oven and furnace processes. Understanding and complying with the NFPA 86 standard can minimize the risk of a catastrophic event at your plant and is the single most important thing an oven builder, buyer, and operator can do. This standard is updated on a regular basis with the latest revisions happening in 2015.
There are four classes of ovens as defined by NFPA 86: Class A, B, C, and D. In this blog, we will be focusing on Class B electrically heated ovens.
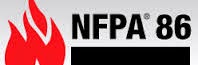
Class B: Electrically heated ovens must be equipped with the following safety equipment:
- Airflow Safety Switch – will shut down the unit should the fan cease operation
- Manual Reset Excess Temperature Control – should the unit produce too much heat, the oven will trip and shut down the heaters.
- Backup Contractors – should the primary contractors fail, the backup contractors will ensure the heaters shut down if over-temperature conditions occur.
This is a simple overview of NFPA 86 for class B ovens. Please consult the full NFPA 86 standard for all specifications and additional details.
Contact a Precision Quincy representative today at (302) 602-8738 or sales@pqovens.com for more information on NFPA 86 and how to become compliant.
All Precision Quincy Ovens are of welded steel construction and quality components are used throughout. Each oven is wired and tested at maximum temperature prior to shipping. Ovens meet or exceed NFPA-86, NFPA-70, OSHA & UL requirements.
This series is intended to highlight the long-standing careers of devoted Chemours™ Teflon® coaters and their accomplishments in the industrial coating field. These pioneers in the Teflon® coating industry are early adopters of the coating and have helped to shape the way Teflon® has grown and evolved as a reputable industrial fluoropolymer. With the pioneers’ vision and ingenuity, Teflon® coating continues to be regarded as the elite fluoropolymer of choice.
Our interview series continues with a spotlight on Mark Tate of Sun Coating Company. Located in Plymouth, MI, Sun Coating Company has been applying DuPont™ Teflon® industrial coatings since the 1960’s. They specialize in applying technologically advanced coatings to enhance and improve the properties for release, nonstick, low friction, abrasion-, wear-, and corrosion-resistance, dry-film lubrication, galling, noise reduction, high temperature, and FDA-compliance. Mark generously took some time to speak with us and share some of his successes, challenges, and views on the future of the industrial coating industry.
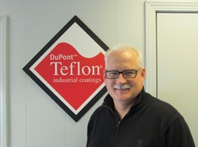
Q: When was your company founded?
A: Sun Coating was founded in 1962.
Q: Who founded the company and why?
A: My father, Joe Tate Jr. founded the company. While he was working for a well-known company in the plastics industry, Teflon® coating was being used as the “in-house” coating. Joe was asked to find a local coating source. As a result, he saw a need for coating source and started Sun Coating.
Q: What was the first significant piece of equipment you purchased?
A:Most of the early significant equipment was related to the automotive sector. Sun was a big player in the automotive sector, producing high volume coating of automotive parts, including throttle bodies, pistons, seating components and steering mechanisms.
Q: How would you describe the changes in the company now from when it was first started?
A:Sun Coating started as a garage/job shop, which then grew into the large facility it is today. We went from batch processing and simple spray equipment to automated robotics. We pushed the envelope over the years and developed and invested in some unique application techniques.
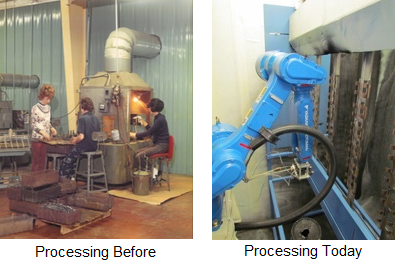
Q: What would you consider significant milestones in your company?
A:
- With my father Joe’s access to Detroit’s automotive market, he was able to develop specs for them. Sun Coating was instrumental in writing original specs; specs that did not even exist at the time. Once the specs were written, companies such as Ford were also looking for a coating source. This need resulted in contract developments between Sun and Ford, moving Sun into a fully operating production company. The need for large industrial ovens and conveyors became necessary as a result of these large contracts.
- In 1989 Sun became the first coating company to receive a Preferred Supplier Award from Ford Motor Company
- As quality changed, ISO certifications came into effect. ISO developed international standards to be used as a certification of assurance that a product, service or system meets specific requirements. Sun became the first company to get ISO 9001. Sun was the only licensed applicator to have the ISO 16949 quality rating within the automotive sector. At one point, Sun was the only company in North America to have attained it.
- Downturn in the automotive industry came and as I entered the business I saw the need to move into other markets. I used my knowledge of engineering applications to take the company into vertical markets. It was our knowledge of coatings and our capability that gave us an edge. Today, we are extremely diversified and service a variety of markets besides automotive.
Q: How has the coating industry itself changed over time?
A:The coating industry is now a world market, including Europe, Mexico, Puerto Rico, and India. The actual selling of coatings has changed as well. Today you need to do more than just go knocking door to door. Customers want information fast; the website is an aid in communicating, educating and developing the application. These technological interactions have made the world more accessible for us. Our Automotive Customers are worldwide.
“Fifty years ago, we were driving down to Dearborn to do these things. Now an international conference call is the norm.”
Doing business today on a worldwide scale can be demanding and challenging. Some of the obstacles we face include language barriers and scheduling conflicts around varying international holidays that effect production.
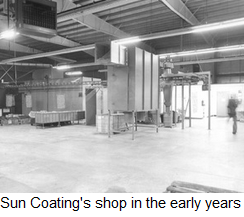
Q: When did you get your LIA license from DuPont?
A: We have a plaque from DuPont dated 1968.
Q: How has being an LIA affected your company?
A: Overall, the LIA status has given Sun credibility as an industrial coater. We are able to post our LIA status on our website which lets customers know we are in great standing with DuPont. The LIA status is a good marketing tool for us as well. It shows that DuPont takes pride in the company’s they do business with. We as coaters must uphold a certain standard to remain an LIA and that offers our customers reassurance with our ability. The marketing and advertising benefits of an LIA status are something we hope to utilize more of in the future.
“I’ve had a great relationship over the years with DuPont.”
Over the years Mike [Patterson], along with Intech, has done a tremendous job supporting Sun Coating. Intech provides timely delivery of material. Communicating and ordering is easy with their unique Intech Marketplace. We have come to rely highly on our supplier for coatings as well as leads. Intech and Sun Coating are good partners in meeting the challenges of the industry as well as growing the business and its value. Mike and his team do a tremendous job making it easy for Sun Coating to do business.
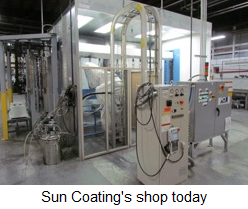
Q: What is your favorite DuPont coating?
A: “The one that brings me the next job.”
All of DuPont’s products are of the highest quality. They offer a broad variety of coatings and all the coatings are user friendly. We use many coatings in all our different sectors and markets. Without the options and variety we would not be able to accomplish all that we have as a company. We are confident that we are providing our customers a quality product with DuPont ™ Teflon® industrial coatings.
Q: What excites you about the future of the coating industry?
A: This is a tough question because we don’t know what tomorrow brings. In the world platform, business is always changing. However, we are always looking to develop new opportunities for Sun Coating’s services to be used. Whether it is finding new coatings that work and perform better for our existing customers or new customers, Sun Coating is on the forefront of the industry.
Powder coating is a dry finishing process, used on a wide array of products that has become extremely popular in the industrial finishing market. An increasing amount of companies are specifying powder coatings for a high quality, durable finish, allowing for maximized production, improved efficiencies, and simplified environmental compliance. Used as decorative and protective finishes, powder coatings are available in an almost any color and texture, and technological advancements have resulted in excellent performance properties.
So what’s in a powder coating?
- Resin: either polyester or epoxy
- Curing agents: added to bind the coating. For polyesters, primid curing agents are used. For epoxies, dicyandiamide curing agents are used.
- Additives: give the powder a desired effect
- Tint pigments: there are two types: inorganic, which are generally pale and dull; and organic, which are more brightly colored
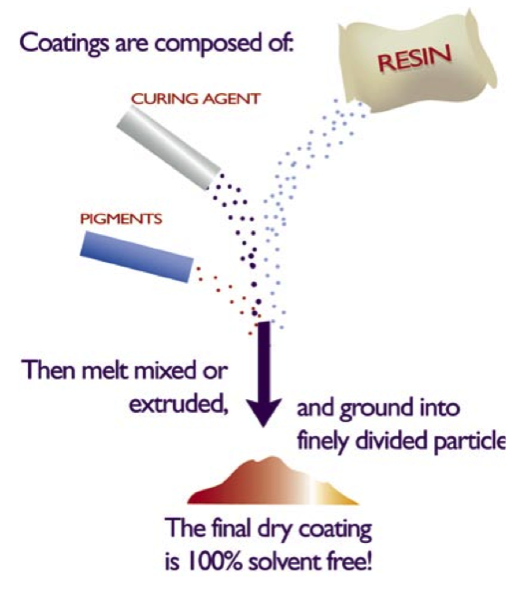
Intech Services and TCI Powder Coatings have partnered to create TruPak, a program that offers over 300 of TCI’s most popular powder coatings in 1, 3, 5, and 10 pound boxes. Together we provide a wide selection of superior products used for innovative solutions and applications within the architectural, furniture, automotive, agriculture, and construction markets. Click here for more information on TruPak powder coatings.
The North American automotive parts and accessories market consists of about 4,500 companies and has annual revenues of over $220 billion. Major product categories are transmission and power train components, engines and engine parts, metal stamping, electrical equipment, seating and interior trim, and brake systems. Large companies include Delphi, Lear, Dana, and Johnson Controls, and Eaton. Over 80% of companies employ less than 100 employees. Industry sales are concentrated among the largest companies. Tier 1, Tier 2, and Tier 3 suppliers all service the automotive OEMs such as Ford, Chrysler, and Toyota. The demand for new and replacement parts is strongly affected by employment and interest rates.
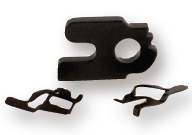
Key Benefits of DuPont™ Teflon® industrial coatings:
- Low coefficient of friction
- High chemical resistance
- Extreme temperature resistance
- Non-stick
- Non-wetting surface
- Electrically non-conductive
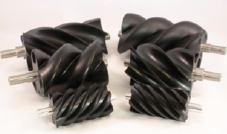
Typical Applications:
- Weld nuts/pierce nuts
- Air conditioner pistons
- Springs/hose clamps
- Seat recliner springs
- Carburetor parts
- Intake valves
- Clutch plates
- Steering column slip shafts
For more information on the coating markets for DuPont™ Teflon® industrial coatings and resources available, visit our Solution Center.
If you’re considering purchasing an industrial oven, there are many elements that need to be considered regarding oven construction. The following represent the more significant points of examination.
Exterior – An oven exterior should be constructed of heavy gauge cold rolled steel and painted with a chip/scratch resistant enamel paint. In the eventuality that an operating environment has corrosive fumes, a stainless steel exterior is recommended.
- Interior – An oven interior ought to be of aluminized steel. Aluminized steel is manufactured to resist the corrosive effects of moisture and heat, as well as other materials. If processes contain acids or corrosive materials, a stainless steel interior should be selected.
- Duct work – The duct work of an oven, in terms of materials, follows the same guidelines as the oven interior.
- Insulation and oven wall-panel construction – These are the two key elements which allow an oven, which is running at 1250°F, to remain cool to the touch on the oven’s exterior. Quality insulation should be the proper density, oversized and compressed into the panel to avoid sagging. The physical strength of an oven is found in the wall panel construction and the overall frame, also the wall panel should allow for minimal transfer of heat to the outer skin.
- Control panel – The control panel is of significant concern because it’s the primary component with which the operator will interact. Consequently, a high quality control panel must possess the following characteristics:
- Large push-button operation
- Legible legend plates
- Clear readouts on the controllers, timers, and recorders
- UL-listed
Have more questions? Contact Precision Quincy Ovens sales and engineering professionals to clarify your requirements, get your questions answered, and learn about their oven solutions. Precision Quincy Ovens has earned a position at the top of the industrial oven market by consistently producing innovative and high-quality ovens.
The aerospace industry has about 1,500 companies with combined annual revenue of $125 billion. The industry is highly concentrated with the largest 20 customers accounting for nearly 90% of its total revenues. In addition to industry giants such as Boeing, Northrop Grumman, and Lockheed Martin, a large number of subcontractors are active industry participants and many of them represent attractive growth prospects for suppliers of industrial coating products. The Federal Government, primarily the Department of Defense, is by far the industry’s largest customer. Government contracts typically begin with an announced need and end with a bidding process. Once the contract is awarded, it remains conditional on the availability of Congressional financing.
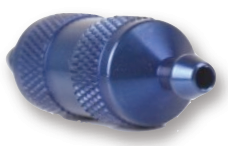
Key Benefits of Teflon™ industrial coatings:
- Low coefficient of friction
- Insulative properties
- Corrosion resistance
- Thermal stability, both to heat and to cryogenic temperatures
- Hydrophic properties
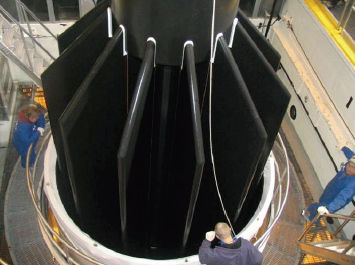
Typical Applications:
- Fuel filters
- Engine components
- Exhaust components
- Solid rocket fuel core molds
- Toilet bowls
For more information on the coating markets for Teflon™ industrial coatings and resources available, click here.
Oven temperature uniformity is important to ensure uniform heating of the product.
Uniformity is the greatest deviation, in degrees, between the lowest and highest temperature points within the work area. For example, it is important to note that ±5°F represents an actual difference of 10°F (5.5°C).
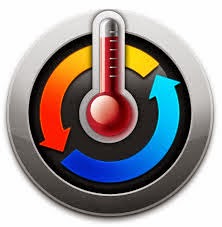
Many factors influence uniformity:
- Controller calibration
- Sensor calibration
- Sensor placement within the work area
- Oven operating temperature (higher temperature/greater variables)
- Air circulation (the greater the air circulation, the better the uniformity)
- Placement of the product within the work area
- Product geometry
- Airflow pattern
- Heat loss through walls
- Metal-to-metal conduction
It is important to take all of these variables into consideration and to utilize a 10-point thermocouple test to ensure that the specified uniformity is obtained for the application. Although this 10-point test is not always included with the oven purchase, it is recommended and usually available for an additional cost. Some applications such as paint or resin curing require a temperature uniformity of ±10°F (±5.5°C). Many drying or preheating processes only require a uniformity of ±20°F (±11°C). Some technical processes need a uniformity of ±5°F (±2.7°C). Knowing your temperature uniformity requirements will help with oven selection.
Contact a Precision Quincy representative today at (302) 602-8738 or sales@pqovens.com for more information on temperature uniformity and oven selection. Need help in the selection process? Call, email or fill out this quick form and a Precision Quincy representative will get back to you.
DuPont™ Teflon® industrial coatings are highly durable and long lasting performance coatings that have a distinct application process and qualities that offer solutions in a variety of industrial markets. This series of blogs will highlight one of these inherent properties of Teflon® coatings and how these properties can solve a variety of problems.
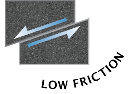
Low Coefficient of Friction: Friction is a force created when two objects rub together that hinders the motion. The coefficient of friction is generally in the range of 0.05 to 0.20, depending on the load, sliding speed, and type of Teflon® coating used. Lubricity is very important in any application that has moving parts touching each other and reapplying oil or grease is not easy. For example, in the automotive and aerospace industries, springs, clamps, and clips are coated with Teflon® coatings to avoid wearing down the part and to reduce squeaking.PTFE has the lowest coefficient of friction
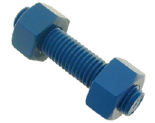
Every day at Intech we receive requests for technical help with DuPont™ Teflon® industrial coatings. If you have a technical question, please feel free to call and speak to one of our technical sales representatives. Once a month, we post a frequently asked question here on our blog.
Question: My part has a sagging look or drip marks. Why does it appear this way?
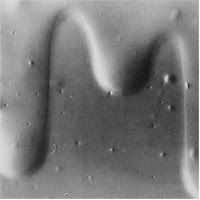
Answer: This is due to heavy application that fails to adhere uniformly. Apply less coats and check the maximum film thickness on the data sheet.
If you need more help, call us at 302-366-8530.
Before purchasing an industrial oven you will need to decide what airflow pattern best suits your process. Selecting the right airflow is an important component to successful oven operation. Coupling the wrong airflow with the wrong product configuration will create unsuitable results. There are three basic airflow types commonly used:
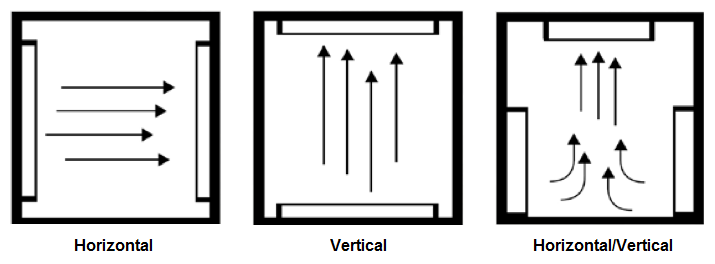
Horizontal/Vertical: Air is supplied from the sidewalls of the oven and is returned to the ceiling of the oven. Commonly used when parts are larger in nature and are loaded into the oven on a flatbed cart or skid.
Vertical: Suited when the product is hung or when small parts are placed on perforated shelves. The shelf must be designed for minimal obstruction allowing the air to pass from the supply to the return.
Full Horizontal: This pattern is used when product is hung or when loaded into the oven on shelves. This airflow allows the re-circulated air to pass above and below each shelf, encircling the product with air.
Contact a Precision Quincy representative today at (302) 602-8738 or sales@pqovens.com for more information on airflow patterns and oven selection.
Reusable respirators need cartridges and filters, which are all available in the Intech Marketplace. To make it easy, cartridge/filter combinations can be purchased together, and they all protect from different substances. The chart below will help you figure out which combination is best for your shop.
All cartridge/filter combos protect from particulates and their respective substances at concentrations up to 10 times the Permissible Exposure Limit (PEL) for half facepieces or 50 times PEL for full facepieces.
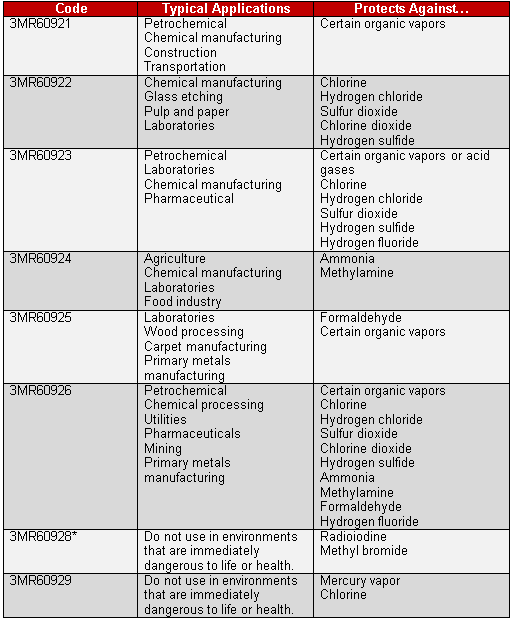
*Only use for ambient concentrations up to 5 ppm and for no more than one shift.
Intech Marketplace is the all-in-one resource for all your industrial coating needs. From respirators to rollers, and everything in between, Intech Marketplace has all the supplies you need for the coating shop. For help deciding which respirators, cartridges, filters, or accessories will work best for you, call (302)-366-8530.
DuPont Chemicals & Fluoroproduct businesses to operate within The Chemours Company, a 100-percent-owned subsidiary of DuPont.
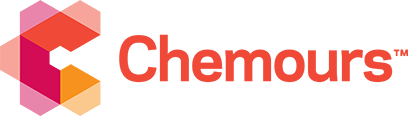
GREENVILLE, DEL., DECEMBER 1, 2014 – Fluorogistx, LLC, the premier U.S. distributor of DuPont™ TEFLON® brand fluoropolymer resins and other DuPont fluoropolymers has announced DuPont’s plans to spin off its Performance Chemicals segment, including the Titanium Technologies and Chemicals & Fluoroproducts businesses in mid-2015.
Robert Smith, Vice President of Sales and Marketing says that effective February 1, 2015, the DuPont Chemicals & Fluoroproducts businesses will be operating within The Chemours Company, a 100-percent-owned subsidiary of DuPont. The short version of the company trade name will be, simply, Chemours.
Chemours will be a world class supplier of Fluoroproducts and Industrial Chemicals, the seventh largest Chemical Company in the world. Our Fluorogistx Customer Service and Sales Representatives are fully prepared to make this a successful transition for all of our customers.
For customers of Fluorogistx, there will only be a few changes involved in the transition, most around name changes. Around mid-year 2015, customers will begin to see packaging labels, MSDS sheets, certifications (COAs), and our website change to reflect the new Chemours name. Customers will be informed on th etiming of these changes as they approach. Essentially, everything else associated with doing business with Fluorogistx will remain the same, including communications, order fulfillment, invoicing, and product deliveries. Additionally, the TEFLON® brand will be retained by Chemours and, as in the past, will be available to approved customers.
Click here to read and download the complete Chemours Notification Letter (PDF).
About Fluorogistx
Fluorogistx, is the exclusive full-spectrum distributor for all Chemours high-performance fluoropolymer products and is the largest non-Chemours source for TEFLON® brand fluoropolymers in the United States. With more than 20 years of experience in the fluoropolymer industry and deep ties to the Chemours and DuPont organizations, Fluorogistx delivers the highest level of service to clients in fields such as telecommunications, automotive, aviation, pollution control, electronics and more. Fluorogistx was originally founded by David Jones in 1993 as Delaware Marketing Services, Inc., (DMS) and later operated under the name Delaware Specialty Distribution. To find out more about Fluorogistx and its fluoropolymer offerings, call 302-479-7614 or visit our website at www.fluorogistx.com.
DuPont™ Teflon® Primers are an effective way to prepare a surface before coating is applied. Primers ensure proper adhesion, increase durability, and give additional protection to the substrate. With the use of our primers, the coating is given a smooth surface to bind to, which creates a more protective layer. This additional layer decreases porosity of the coating to the substrate.
There are a number of excellent primers designed to provide substrate and intercoat adhesion for Teflon® topcoats. The water and solvent based products allow for processing flexibility for your specific project. It is important to remember that an FDA-conforming primer must be used in conjunction with FDA-conforming topcoats to have a complete FDA-conforming coating system.
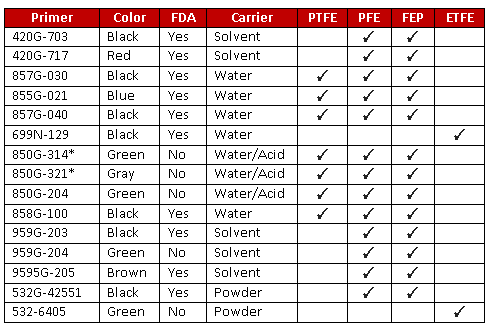
*Mix with 850-7799
For all your DuPont™ Teflon® industrial coating needs, visit Intech Services or call (302) 366-8530. Our highly skilled technical sales team can answer questions about our powder primers or any of the numerous Teflon® products we offer.
Introducing a Primers Marketing Piece
We have created a marketing piece for you to utilize in your sales efforts with customers. You can download the pdf of the Primers marketing piece here.
Every day at Intech we receive requests for technical help with DuPont™ Teflon® industrial coatings. If you have a technical question, please feel free to call and speak to one of our technical sales representatives. Once a month, we post a frequently asked question here on our blog.
Question: The humid weather is causing staining and pops in my DuPont™ Teflon® industrial coating. How do I fix this?
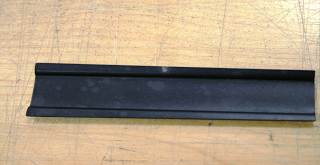
Answer: Conditions can be more challenging depending upon the region in which you do business and whether you coat with solvent or water-based Teflon® coatings.Preheat parts and coat the parts while still warm to avoid water entrapment. Try selecting better times during the day to coat if possible (early morning or evenings), ramp up your moisture control in your shop or spray room, and avoid letting coated parts sit out for extended periods of time after being coated.
If you need more help, call us at 302-366-8530.
DuPont™ Teflon® industrial coatings are highly durable and long lasting performance coatings that have a distinct application process and qualities that offer solutions in a variety of industrial markets. This series of blogs will highlight one of these inherent properties of Teflon® coatings and how these properties can solve a variety of problems.
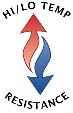
Heat Resistance: DuPont™ Teflon® industrial coatings can operate continuously at temperatures up to 500°F and can be used up to 550°F intermittently with adequate ventilation. The thermal stability of the coatings means that they can be used in high heat environments without losing or affecting any other properties. High temperature resistance is a significant concern in the food industry because food is processed at a very high temperature. PTFE and PFA have the highest in-use temperatures, but it is not recommended to push the coatings past their maximum temperatures because they will degrade and break down.
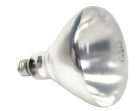
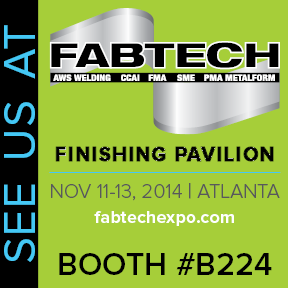
FABTECH heads to Atlanta, GA November 11-13, 2014 bringing together an anticipated 27,000 attendees and 1,400 exhibiting companies all under one roof.
In the finishing pavilion, you will find DuPont™ Teflon® industrial Coatings, TCI Powder Coatings and Precision Quincy Ovens exhibiting. DuPont™ Teflon®industrial coatingswill exhibit in conjunction with TCI Powder Coatings under the umbrella of the TruCoater Network in Booths B224/B125. Precision Quincy Ovens will be exhibiting at the show at booth B304 and have a 74-800 truck oven on display. This oven is for sale and will ship direct from the show at a special discount. If you are interested in purchasing, call(302)602-8738 for more information.
The show provides a backdrop for visitors to experience live equipment demonstration, find cost savings solutions, and network with industry peers throughout the 500,000+ square feet of show floor throughout the A, B, and C buildings at the Georgia World Congress Center. The event also provides learning opportunities beyond the exhibits with over 100 educational sessions and expert-led presentations on the latest industry trends and technology in the metal forming, fabricating, welding and finishing industries.
If you are going to be at the show, please stop by to visit us. If you would like to attend the expo for free, click here to register for your free expo pass using the code FBF14.
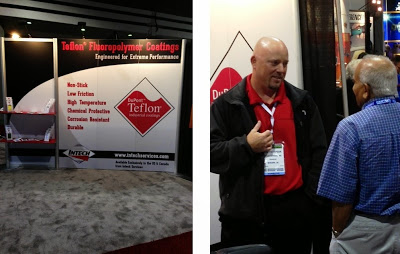
FABTECH 2014 Show Hours
Georgia World Congress Center
285 Andrew Young International Blvd NW
Atlanta, GA 30313
(404) 223-4000, gwcc.com
Tuesday, November 11, 10:00 am – 6:00 pm
Wednesday, November 12, 9:00 am – 5:00 pm
Thursday, November 13, 9:00 am – 4:00 pm
Every day at Intech we receive requests for technical help with DuPont™ Teflon® industrial coatings. If you have a technical question, please feel free to call and speak to one of our technical sales representatives. Once a month, we post a frequently asked question here on our blog.
Question: My DuPont™ Teflon® industrial coating looks like the bottom of a dry pond, with lots of deep cracks running through it. How do I fix it?
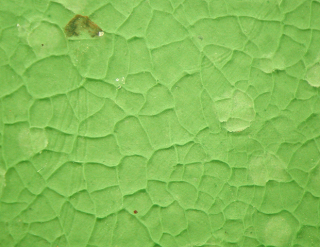
Answer: Mudcracking can be due to excessive film build or the material not being uniformly mixed. Products used may not be compatible. Also, the substrate may be too hot or too cold.
If you need more help, call us at 302-366-8530.
There are many questions involved in purchasing an industrial oven. One question some consider is whether to buy new or used. While used industrial ovens are usually less expensive than new ones, there are many pitfalls tied to used ovens, which can wind up making the overall price come close to or surpass the price of a new oven.
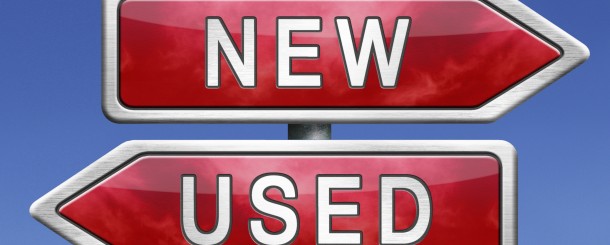
Here are some things to consider before purchasing a used industrial oven:
- End Use – A used industrial oven may not be equipped or may not have the options needed to support your process. Adding options or retrofitting the oven to meet your needs may be required and can be costly.
- Performance – With used ovens uniformity, ramp time, and airflow may be unknown, whereas a new oven is guaranteed to perform to manufacturer performance specifications.
- Safety Requirements – Older equipment may not comply with the most recent safety requirements. Updating a used oven to meet current NFPA-86, NFPA-70, OSHA & UL requirements can be expensive.
- Missing Parts and Oven Condition – Used ovens may also be missing parts and actual oven condition can be difficult to determine. Although an oven may be the right model number you’re looking for, many times changes have been made customizing the oven to its previous process.
- Incompatible Power Source – It can be very costly to convert an incompatible power source between the used oven and the new facility.
- Warranty – Buying a used industrial oven can limit the support you receive from the manufacturer and may mean going without a warranty on your investment.
Buying a used industrial oven is not always a good deal. By the time the used oven is modified and updated, the cost is usually close to or has exceeded the purchase price of a new oven. Already purchased a used oven? Intech Services is proud to represent Precision Quincy Ovens who offers oven refurbishment which can rebuild the equipment eliminating the above issues. Contact Precision Quincy for an evaluation today, call (302) 602-8738 or email sales@pqovens.com.
Operating temperature has a direct effect on oven selection. Here are some questions to think about when considering operating temperature and oven selection:
Precision Quincy Ovens can create an industrial oven to fit any application and need you may have, from large conveyor ovens, to small bench ovens, and everything in between. Contact a Precision Quincy representative today to guide you through the oven selection process at (302) 602-8738 or sales@pqovens.com
Fluoropolymer materials offer a wide variety of desirable characteristics in industrial applications where wear resistance, sealing, filtration, and high temperature performance are required. When used as an additive, coating or in a compound, fluoropolymers contribute their unique PTFE or Melts based properties to the host material to which they are paired with, providing non-stick properties, improved lubricity, anti-drip and better wear resistance.
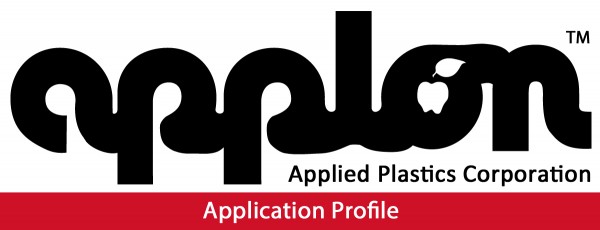
Superior Performance using Chemours Teflon® PTFE Dispersion.
Applied Plastics Corporation, of Tuscumbia AL, is an innovator in high performance coated fabrics and industrial belting products.
Under its Applon™ product line, Applied Plastics produces a number of premium PTFE impregnated products using genuine Chemours Teflon® coupled with proprietary manufacturing processes.
This proprietary PTFE impregnation process was developed by Applied Plastics in 1965 and allows for an even distribution of PTFE throughout the base material and offers superior performance to more traditional surface coating techniques.
Key Applon™ Benefits
- High thermal stability
- Continuous service temperature of 500°F
- Static dissipative properties (carbon filled version)
- Superior chemical, solvent and environmental toughness
- Excellent release properties
- Water and fluid repellency
- Ideal asbestos alternative
- Resistant to sunlight and other UV sources
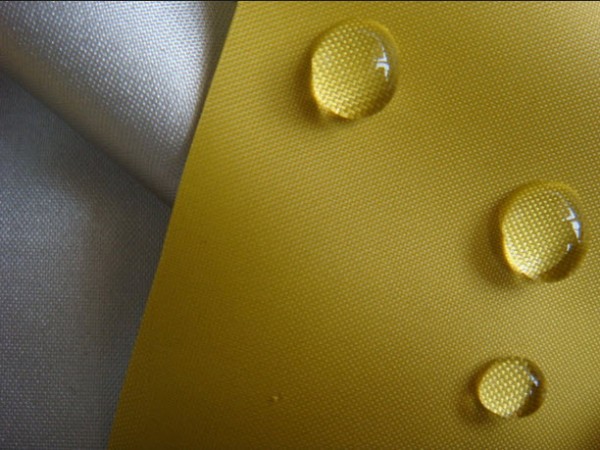
Example of fluid repellency in Polytetrafluoroethylene (PTFE) impregnated fabric.
Technology
Applied Plastics has made significant investments in proprietary fabric coating processes, specialized equipment and technology to support the production of high-temperature fabrics and belting.
In addition, all Applon™ products are manufactured with the latest aqueous fluoropolymer technology from DuPont.
Chemours Teflon® aqueous fluoropolymers are dispersions of PTFE particles in water, stabilized by non-ionic wetting agents. These aqueous dispersions offer a practical method for impregnating fabrics, belting and other base materials, with PTFE to impart many of the benefits of fluoropolymers into the finished product.
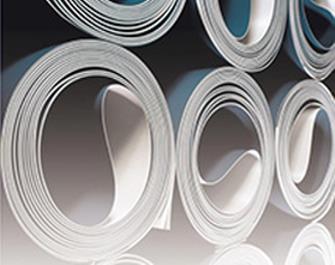
Example of Polytetrafluoroethylene (PTFE) impregnated conveyor belting.
Materials Selected and Why
Applied Plastics selected Chemours Teflon® PTFE aqueous dispersion for its unique and high performance characteristics.
Chemours Teflon® PTFE aqueous dispersions have allowed Applied Plastics engineers to move past traditional design boundaries to produce extreme duty PTFE impregnated fabrics and belting that exhibit consistent quality, performance and durability.
Applon™ PTFE impregnated fabrics and belting are designed for continuous service temperatures up to 500°F and are available in any desired length, in thicknesses up to .125 inch and widths to 88 inches.
To request additional information, please contact:
Richard Stutts VP / General Manager
applonapc@aol.com
Click here to download a copy of this article.
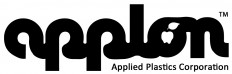
Applied Plastics Corporation was founded in 1965 and has evolved into a full service fabric and belting OEM supporting a broad range of industries and end use applications
An ISO-9001 certified company.
1748 Woodmont Drive
Tuscumbia, AL 35674
(205) 383-6700
DuPont™ Teflon® industrial coatings are highly durable and long lasting performance coatings that have a distinct application process and qualities that offer solutions in a variety of industrial markets. This series of blogs will highlight one of these inherent properties of Teflon® coatings and how these properties can solve a variety of problems.
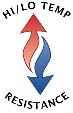
Cryogenic Stability: Many DuPont™ Teflon® industrial coatings can withstand temperatures as low as -454°F without loss of physical properties. Their ability to withstand sub-freezing temperatures means that Teflon® coatings will not lose any of their other characteristics when exposed to such low temperatures. One-coat systems are not recommended for low temperatures because the binder resins in the coatings are not able to adhere to the substrate when temperatures drop too low.
To see all properties of DuPont™ Teflon®industrial coatings, click here.
Film thickness consistency plays a big role in saving money in the coating shop. Having inconsistent thicknesses means you’re probably wasting coating, and therefore wasting money. By using these simple techniques, you’ll be able to cut out the waste, as well as achieve a better, more consistent finish for your DuPont™ Teflon® industrial coatings.
Click here to see the first 3 tips from last week.
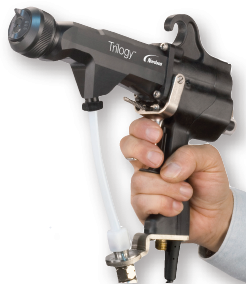
Spray Pass Speed: Adjust the spray gunspeed to achieve consistent films. Before pulling the trigger, consider the coating flow rate and the target wet film thickness. Adjust the equipment before spraying to find a flow rate that lets the applicator move at a controllable, comfortable speed. Spraying too fast can lead to decreased film thickness, and sometimes extra coats will be needed to make up the deficit.
Trigger Control: Maintaining a consistent trigger pull on each spray pass directly impacts the flow rate, spray pattern size, and transfer efficiency. Start triggering immediately before the lead edge of the part and release the trigger immediately following the lag edge. Fully pulling the trigger provides constant flow rate control. The fluid knob on your spray gun can be adjusted to restrict the trigger travel distance so you can always pull the trigger all the way. Partial triggering, however, can be very useful for blending and touching up.
Edge Banding: Partially pull the trigger to spray a light coat around the edges of the part. Then spray the center of the part, blending the edges into the first coat. Banding can increase transfer efficiency and increase film thickness on the edges. This technique ensures the edges get coated completely while maintaining consistent film thicknesses.
Your application will help determine your industrial oven selection. Precision Quincy Ovens can create an industrial oven to fit any application and need you may have, from large conveyor ovens, to small bench ovens, and everything in between. Contact a Precision Quincy representative today to discuss your application and to guide you through the oven selection process at (302) 602-8738 or sales@pqovens.com.
At Precision Quincy Ovens we manufacture industrial ovens
for any coating, curing, heating, or drying process:
- Annealing
- Aging
- Curing
- Dehydrating
- Drying
- Heat Setting
- Heat Shrinking
- Pre-heating
- Stress Relieving
- Powder Coating
- Teflon® coating
- Baking
- Bonding
- Burn-in
- Curing
- Sterilizing
- Testing
Film thickness consistency plays a big role in saving money in the coating shop. Having inconsistent thicknesses means you’re probably wasting coating, and therefore wasting money. By using these simple techniques, you’ll be able to cut out the waste, as well as achieve a better, more consistent finish for your DuPont™ Teflon® industrial coatings.
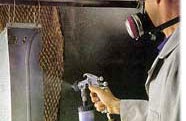
1. Spray Distance: The spray distance is based on the spray equipment, coating, complexity of the part, and spray environment. By keeping the gun at the same distance from the part the entire time you’re spraying, you can improve the consistency the film thickness over the whole part. Increasing the gun distance increases the pattern fan size, and the coating thickness decreases as it is distributed over a larger area.
2. Gun Angle: Maintain controlled gun angle to the part. Yaw and pitch spray angles will result in a non-uniform spray pattern distribution, causing inconsistent film thicknesses.
3. Spray Pass Overlap: Each spray pass should overlap 50-75% of the previous pass. Overlapping below 50% results in “striping,” or variations in the film thickness. The more you increase the overlap, the thicker the coating, so overlapping above 75% requires more spray passes and more coating.
More tips are on the way! Check the Intech Insider for more spray techniques coming soon!
2014 Parker Aerospace Supplier Conference
Fluorogistx receives the Aerospace Group Supplier Performance Award for excellence in serving Parker Aerospace. The awards were presented to the top 14 of 250 global suppliers that met Parker’s stringent criteria for continuous improvement in quality, cost, on-time delivery and supplier partnering. Debbie Edgar,Supply Chain Director for the Stratoflex Division in Fort Worth, TX.,was there to assist in making the presentation to Eric Long, Regional Sales Manager, representing Fluorogistx. Parker Aerospace, a Parker Hannifin Group, has $2 Billion in annual sales and more than 6,000 employees. We proudly accept this award and thank Parker Aerospace for this important recognition.
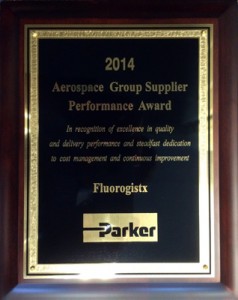
Intech is proud to represent Precision Quincy Ovens, an industry leading manufacturer of many types of industrial ovens. For over 60 years, Precision Quincy Ovens have been used in industry across the globe. Precision Quincy can create an industrial oven to fit any need you may have, from large conveyor ovens to small tabletop ovens, and everything in between.
Precision Quincy ovens are constructed with welded steel and use quality components throughout. All ovens are assembled, wired, and tested at maximum temperature prior to shipment and meet or exceed NFPA-86, NFPA-70, OSHA & UL requirements. This article focuses on the High Temperature oven line, which is a multi-use oven made for process temperatures to 1250°F.
High Temperature Walk-In Ovens are built by Precision Quincy’s proprietary “Can” Construction, meaning the oven’s interior walls are made from seamless steel plate. The seamless interior is superior to normal tongue and groove construction, which could buckle at higher heat. Buckling allows heat to escape the oven resulting in higher energy costs, less efficiency, and inconsistent product quality. High Temperature Walk-In Ovens are not standard ovens and therefore require a slightly longer quote time.
Precision Quincy High Temp Walk-In Ovens
- Maximum temperatures: 1000° F / 1250° F
- Suited for most industrial processes like aging, annealing, curing, dehydrating, drying, heat setting, heat shrinking, pre-heating, stress-relieving, and testing
- Insulated floor 3” or 6”
- Available in any voltage and with gas or electric heat
- Available in eight standard sizes or can be customized to meet your specific needs
- Air Flow: Horizontal / Vertical
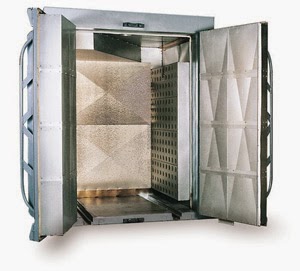
Dimensions
- Standard Height 6’
- Standard Width 4’- 6’
- Standard Depth 4’- 10’
Click here for or more information on Precision Quincy High Temp Walk-In Ovens, other available ovens, or our complete guide for installation and maintenance services.
Need help in the selection process? Fill out this quick form or call 302-602-8738 to talk to a Precision Quincy Oven Representative. We can also be contacted by email.
Teflon™ industrial coatings are highly durable and long lasting performance coatings that have a distinct application process and qualities that offer solutions in a variety of industrial markets. This series of blogs will highlight one of these inherent properties of Teflon coatings and how these properties can solve a variety of problems.
Chemical Resistance: Chemical environments usually do not affect a Teflon™ industrial coating. The only chemicals known to affect these coatings are molten alkali metals and highly reactive fluorinating agents. Minimal porosity leads to excellent permeation resistance and low chemical absorption. Teflon™ coatings’ resistance to chemical action makes the coatings a good choice for the chemical processing and semiconductor industries. PFA and ETFE have the best chemical resistance to many acids, bases, and solvents due to the coatings ability to melt-flow and achieve high film builds.
To see all properties of Teflon™ industrial coatings, click here.
The final step to the powder coating application process is curing. The following is some important information about curing TCI powder coatings:
Different Baking Needs for Different Powders:
- Thermoplastic powders need enough heat to liquefy and smooth out the coating film.
- Thermoset powders need enough heat to liquefy the film and enough time at the specified bake temperature to fully develop the coating’s properties.
The Stages of Curing Powder Coatings:
- The melt point is when powder particles change from solids to a semi-liquid state.
- The flow stage is when the powder is completely liquefied and the film will smooth out.
- The cross-linking stage refers to when the heat triggers chemical reactions within the film to change the product’s chemical and physical properties.
- The gel stage happens after sufficient crosslinking has occurred and the coating starts to solidify again.
- Cure development is the most important stage, when the coating has fully developed all of its final properties.
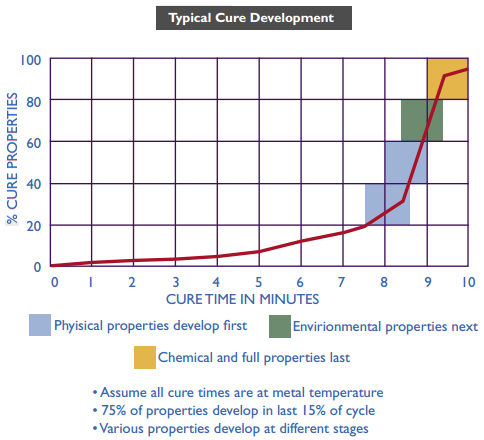
For more information about powder coating application, read TCI’s Troubleshooting Guide.
Every day at Intech we receive requests for technical help with DuPont™ Teflon®industrial coatings. If you have a technical question, please feel free to call and speak to one of our technical sales representatives. Once a month, we post a frequently asked question here on our blog.
Question: I am having issues with peeling. The Teflon® coating is peeling up right off of my substrate. We grit blasted the part then applied the coating according to the fact sheet. What went wrong with the application or the coating?
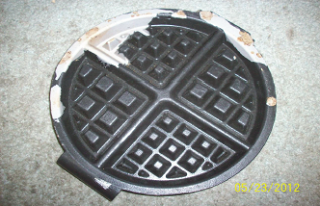
Answer:This is called inter-coat adhesion failure. It’s when the coating or base coat lifts cleanly off the part and shows the bare metal. In order to prevent this, the part needs to be cleaned properly after grit blast. In order to ensure adhesion of the coating, most Teflon® coatings require the substrate surface be roughened by grit blasting. Aluminum oxide is the recommended grit blast media. After grit blast, the part should be shot with air to remove contaminants (rust, oil, grease, etc.) from the part and wiped down with a acetone cloth. To assure all organic surface contamination has been removed, it is recommended that the part is pre-baked at (or slightly above) the final cure temperature.
If you need more help, call us at 302-366-8530.
The “Faraday cage effect” occurs when the inner recesses and corners of a charged substrate do not have a charge, and the charged powder particles create resistance, making it difficult to coat these areas. There are ways to overcome the Faraday cage effect and better coat inner corners and odd part geometries.
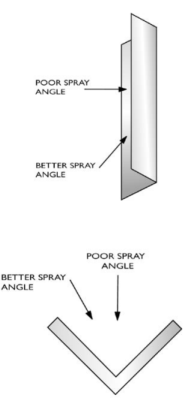
Overcoming the obstacles of the electrostatic process:
- Blast powder into recesses
- Increase the powder flow rate
- Maximize the gun to part distance
- Use slotted tip to concentrate the spray
These methods can use excess powder, have higher film thicknesses than desired, and could result in an uneven film build.
Using the electrostatic process:
- Finesse the powder into recesses
- Decrease powder gun flow rates
- Reduce gun voltage to 40-60 Kv
- Maintain gun to part distance of about 8-10 inches
- Use slotted tip to concentrate spray
- Approach recess at an obtuse angle
These methods could result in a slower application time.
Spraying in the Faraday Cage: spraying at the recesses of a part at an obtuse angle can help to apply the coating properly.
- Reduces air turbulence
- Allows deeper penetration
- Minimizes early back ionization
- Utilizes more lines of force
For more information about how to overcome the Faraday cage effect, read TCI’sTroubleshooting Guide.
Every day at Intech we receive requests for technical help with DuPont™ Teflon® industrial coatings. If you have a technical question, please feel free to call and speak to one of our technical sales representatives. Once a month, we post a frequently asked question here on our blog.
Question: We applied the abrasion resistant PFA over 420-703 primer. We put a final coat of 532-5010 on over the grey. As you can see in the attached picture, we are experiencing delamination of the PFAs down to the primer. What do you think could have caused this? We have a lot of abrasion applications where this coating could be a good fit but I am feeling a little gun shy until I can understand what went wrong here.
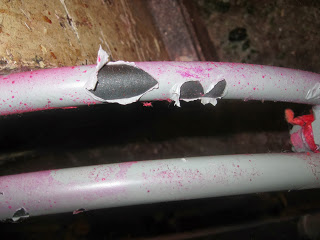
Answer: The primer was sprayed on too thick.
Tribomatic static charging is the second most common method of spraying powder coatings, after corona charging. The powder develops a charge while passing through special hoses and guns. As powder contacts these non-conductive surfaces, friction causes the particles to lose electrons. These particles then develop a powerful positive charge. No high voltage or lines of force are used which allows for easier penetration of deep recesses. Tribomatic charging is efficient in developing a static charge within the powder, however, coatings must be specifically formulated for this system.
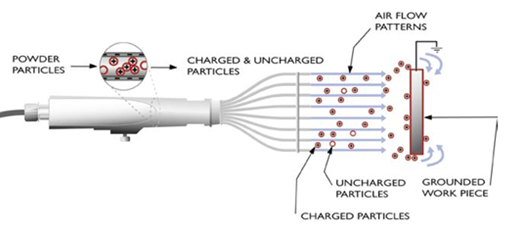
Advantages:
- No high voltage sources
- Better penetration into recessed areas
- Slightly lower capital costs
Disadvantages:
- Level of charge varies with powder chemistry and formula
- Slower rate of application
- Transfer efficiency is lower than corona charging
- Requires more guns
- Wears out parts faster
For more information about Tribomatic static charging, read TCI’s Troubleshooting Guide.
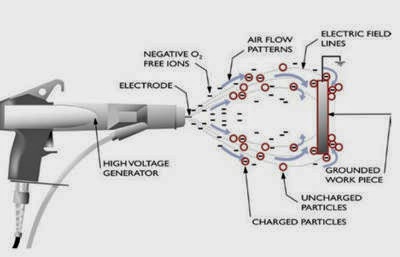
Corona charging is the most common method used in powder application. The process disperses powder into an air stream to make a cloud of powder as it leaves the gun. The particles pass through a charged corona field at the gun tip, which applies a strong negative charge to each particle. These particles have a strong attraction to the grounded part and deposit there stick to it, then can be cured to stay on.
Advantages:
- Heavy films
- High transfer efficiency
- Only one oven needed because parts are sprayed cold
- Applies quickly
- Can be automated
- Minimum operator training
- Works with most chemistries
Disadvantages:
- Requires high voltage source
- Some difficulty with deep recesses
- Thickness control sometimes difficult
- Capital cost higher than other application methods
For more information about Corona charging, read TCI’s Troubleshooting Guide.
Intech Services is proud to represent Precision Quincy Ovens, an industry leading manufacturer of many types of industrial ovens. For over 60 years, Precision Quincy Ovens have been used in industry across the globe. Precision Quincy has a variety of standard ovens available or can create an industrial oven to fit any need you may have, from large conveyor ovens to small bench ovens, and everything in between.
Precision Quincy ovens are constructed with welded steel and use quality components throughout. All ovens are assembled, wired, and tested at maximum temperature prior to shipment and meet or exceed NFPA-86, NFPA-70, OSHA & UL requirements. Truck Ovens are Precision Quincy’s most popular ovens, providing customers with versatility allowing larger quantities of product to be processed in a single batch.
Truck Ovens
- Maximum temperature 500° F / 800° F
- Suited for most industrial processes like aging, annealing, curing, dehydrating, drying, heat setting, heat shrinking, pre-heating, stress-relieving, and testing
- Full Horizontal air flow – allows air to pass freely over and below materials in process
- Standard 2.5″ insulated floor with cart guide tracks
- Digital set point controller
- Available in any voltage and with gas or electric heat
- Eight standard sizes available or can be customized to meet your specific needs
- Additional options include carts, double doors at both ends, programmers and recorders
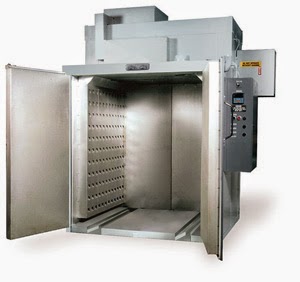
Dimensions
- Standard Height 5’
- Standard Width 3’- 6’
- Standard Depth 3’- 6’
Click here for or more information on Precision Quincy Truck Ovens, other available ovens, or our complete line of installation and maintenance services.
Need help in the selection process? Fill out this quick form or call 302-602-8738 to talk to a Precision Quincy Oven Representative. We can also be contacted by email.
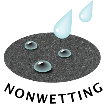
DuPont™ Teflon® industrial coatings are highly durable and long lasting performance coatings that have a distinct application process and qualities that offer solutions in a variety of industrial markets. This series of blogs will highlight one of these inherent properties of Teflon® coatings and how these properties can solve a variety of problems.
Non-Wetting: Teflon® coatings are both hydrophobic and oleophobic, making cleanup easier and more thorough. Hydrophobic substances repel the polar ions in water and resist wetting. The low surface energy of the coatings means that the cohesive forces in the water are strong enough to make the water bead up and not spread across the surface of the coating. This property of Teflon® coatings is especially important for coating laboratory glassware, such as beakers and test tubes, in order to minimize cross-contamination. PTFE shows the best non-wetting characteristics.
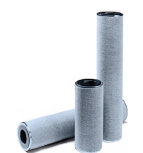
To see all properties of DuPont™ Teflon® industrial coatings, click here.
Surface preparation is the first step to the flawless performance you have come to expect from DuPont™ Teflon® industrial coatings. Many coating failures can be traced back to poor surface preparation. Here are some common coating problems that can be fixed by properly preparing the substrate’s surface.
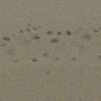
Air bubble pops:
This is called outgassing, and can be prevented by preheating the part to 250°F before applying the coating. Click here to read more about outgassing.

Crater-like holes:
These are called fish eyes, and can be caused by contaminants in the coating or on the substrate. This could even be grit from blasting that wasn’t totally removed. Make sure the spray area and substrate are completely contaminant-free before spraying. Click here to read more about fish eyes.
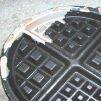
Substrate adhesion failure:
If the coating is coming off of the substrate, it could be because the blast profile is not deep enough or there are contaminants under the coating. Blast profiles of at least 2.5 microns are recommended, and profiles between 5.1 – 6.5 microns are frequently used. Always be careful to remove all of the blast media from the substrate before spraying. To make sure all grit has been removed, pre-bake the part at the coating’s cure temperature or higher.
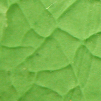
Mudcracking:
Mudcracking is when the finished coating looks like the bottom of a dry, cracked pond. This can be caused by too severe grit blasting, wire brushing, or sanding that causes pits and scratches in the substrate’s surface. When sprayed, the coating will flow into the depressions, causing cracks in the cured coating.
If you still have any trouble applying your coatings, call 302-366-8530 to talk to a Teflon® technical representative.
The fluidized bed process is used to apply powder coatings by dipping heated parts into a cloud of powder, caused either by a constant airflow or an electrostatic charge, and the powder melts to the hot surface. The final thickness depends on part temperature and how long the substrate is dipped in the powder, and film thicknesses can be achieved from 8 up to 125 mils. This process requires preheat temperatures of at least 350°F and may require a post-heat or cure cycle.
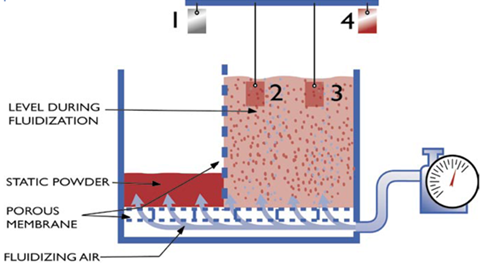
Fluidized bed steps:
1. Part is preheated to 400°F-450°F
2. Initial deposit melts onto part
3. Film builds from residual heat
4. Coated part removed when desired thickness achieved
Fluidized bed advantages:
- Uniform coating
- Thick films can be achieved
- Complex parts can be 100% coated
- Good edge coverage
- Good process control
Fluidized bed disadvantages:
- Preheat and post-heat ovens are required
- Larger, heavier parts are not easy to manipulate into bed
- Thinner substrates do not hold heat and are difficult to coat
- Complex shapes trap excess powder
- A minimum of 8 mils must be applied
For more information about the fluidized bed process, read TCI’s Troubleshooting Guide.
Surface preparation is the first step to the flawless performance you have come to expect from DuPont™ Teflon® industrial coatings. One thing you need to consider when preparing to coat is which blast media will work best for your job. DuPont recommends using aluminum oxide for Teflon® coatings, but there are several other options available. This chart explains the applications, specifications, and economic value of aluminum oxide, glass beads, iron shot or grit, ceramic beads, and nut shells as abrasive media.
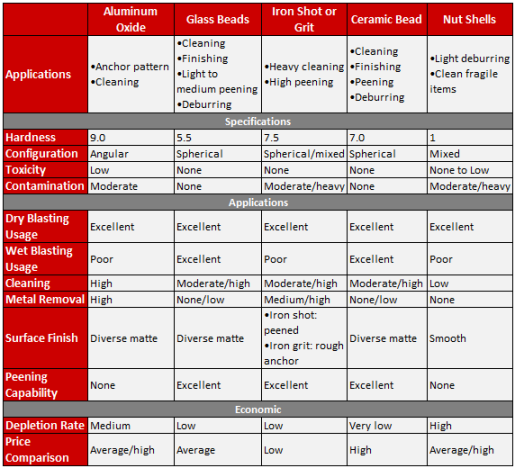
1. Clean the substrate: Teflon® coatings should be applied over clean substrates. If there are any contaminants on the part, the coating will have defects and not perform as well. You can use chemical washes, solvent cleaning, or degreasing, but make sure all the residue from the cleaning has been removed. Gloves should be worn after cleaning to avoid getting fingerprints on the metal. Fingerprints and any residual oil not removed during cleaning may show up as stains on the cured coating.
2. Preheat the part: If you heat the substrate at the cure temperature for the coating, it will help remove any residual oils and minimize the effects of humidity. Also, with most ferrous metal, this step will temporarily protect against flash rusting. If you are using acid primer, the blue oxide that forms increases the adhesion of the coating.

3. Roughen the surface: Grit blasting is the most commonly used method to increase the surface profile of the substrate, improve adhesion, and remove any contaminants left over from cleaning. DuPont recommends surface profiles of at least 100 microinches (2.5 microns), and 200-250 microinches (5.1-6.5 microns) are frequently used. DuPont recommends aluminum oxide as your blast media, but there are other options such as glass beads and walnut shells. Commonly used air pressures range from 80 to 100 psi, but the pressure you use depends on your substrate. Make sure the profile is uniform and fully covers the whole surface. Excessive or high pressure grit blasting causes pits, scratches, and cuts that can result in a bad finish, so be careful not to overdo it. If your part is too small to grit blast, zinc or iron phosphate conversion coatings can be used to increase coating adhesion.
4. Cure the coating: Curing is the last step to good adhesion of your Teflon® coatings. Reaching and maintaining proper cure temperatures for a sufficient period of time to cure the coating is one of the most important factors in achieving a finish with optimal adhesion performance. Don’t forget: all temperatures mentioned in the Fact Sheets refer to metal temperatures, so the part itself must reach the recommended cure temperature. Ovens should be calibrated at least twice per year, and thermocouples should be used to check part temperatures. Each coating has different curing instructions, so always check the Fact Sheets first, and always follow the cure schedule very carefully.
Have a Blast, But Keep It Safe!
Click here to check out Intech Marketplace’s selection of blast gloves and suits. Blast gloves keep your hands and arms safe while you’re grit blasting your substrate. Blast suits are also important to provide for your employees because they are designed specifically to protect against harsh blasting environments.
Intech Marketplace makes shopping for blasting equipment and other coating products easy because all the supplies you need for your shop are just a click away in a single location. If you’re not sure what you need, call 302-366-8530 for help selecting products.
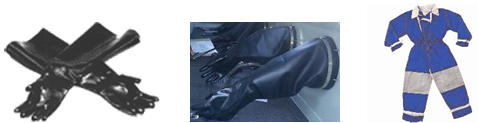
There are several ways to apply powder coatings. Each has its benefits, as well as its disadvantages, and which method you use depends on the job itself. Here is a quick overview of the different powder coating application methods.
Fluidized bed – Constant airflow keeps the powder circulating, then heated parts are dipped into the bed and the powder melts to the part.
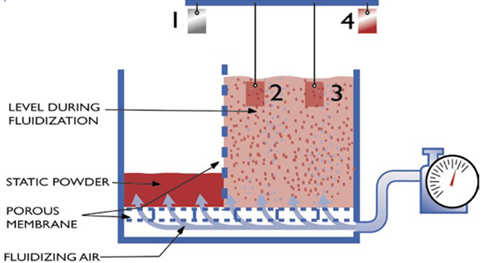
Electrostatic fluidized bed – This is similar to the conventional fluidized bed, but the powder is repelled by electrostatic charges, not air, to keep it suspended.
Corona electrostatic spray – Powder particles pass through a spray gun tip that charges the powder particles, which are then attracted to an oppositely-charged substrate.
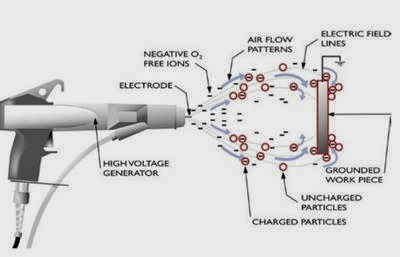
Tribomatic electrostatic spray – Electrons are stripped off the powder particles to create a charge, then they are attracted to an oppositely-charged substrate.
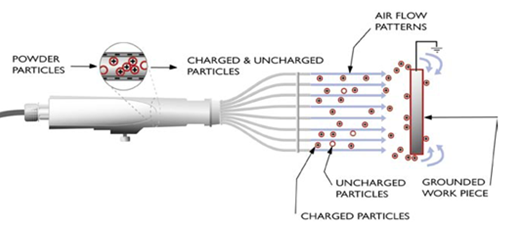
Hot Flocking – Preheated substrates are sprayed with powder, and it melts to the part immediately.
Flame spray – Used for thermoplastic powders, powder is propelled through a flame to melt it.
For more information about powder coating application methods, read TCI’s Troubleshooting Guide. More detailed advantages and disadvantages of each method will be discussed in future blogs.
Intech Services and TCI Powder Coatings have partnered to create TruPak, a program that offers over 300 of TCI’s most popular powder coatings in 1, 3, 5, and 10 pound boxes. Click here to buy TruPak powder coatings.
As we are all aware, a properly functioning oven is critical to the successful application of DuPont™ Teflon® industrial coatings. Regular preventative maintenance is an important step in this process. But what if your oven needs more than just calibration or a few new parts? Precision Quincy can help you regardless of the oven brand. The case study below highlights a recent success story where Precision Quincy refurbished a 40-year-old outdated oven back to new condition.
During a recent preventative maintenance visit with a large OEM, Precision Quincy’s Service Technician discovered the oven had an extreme amount of byproduct buildup on every moving component, which also clogged the burner itself. Replacing the oven would have been a huge unexpected expense causing a 2-3 week shut accruing addition expenses in operational downtime.
Precision Quincy suggested oven refurbishment as an alternative to purchasing a new oven. All moving components were replaced, as well as the outdated and defective burner controls. It only took 4 days to rebuild the oven onsite, eliminating the 2-3 weeks of operational downtime involved in purchasing a new oven. Precision Quincy was able to save the OEM over 7 times the cost of the rebuild, including operational downtime and new oven purchase price, by choosing oven refurbishment. The refurbished industrial oven now operates like new just as it did the day it arrived, 40 years ago.
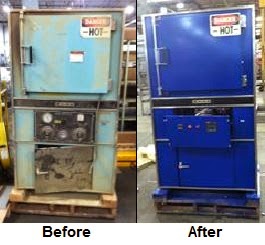
DuPont™ Teflon® industrial coatings are highly durable and long lasting performance coatings that have a distinct application process and qualities that offer solutions in a variety of industrial markets. This series of blogs will highlight one of these inherent properties of Teflon® coatings and how these properties can solve a variety of problems.
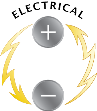
Unique Electrical Properties: Over a wide range of frequencies, DuPont™ Teflon® industrial coatings have a high dielectric strength, low dissipation factor, and high surface resistivity. Dielectric strength is the highest voltage that the coating can withstand before it breaks down. The low dissipation factor means that the absorbed energy dissipated as heat is low. PFA and ETFE have the highest dielectric strength at almost 2,000 volts per mil. However, in order to achieve these results, the coatings must be completely pinhole-free, so multiple coats are usually recommended.
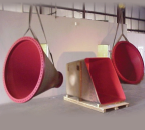
To see all properties of DuPont™ Teflon®industrial coatings, click here.
Pretreating a substrate for powder coating is an important step in the application process. Powder coating a substrate with contaminants on the surface will result in poor performance of the coating. Here is an overview of the pretreatment step for powder coatings:
1. Clean the substrate to remove all contaminants, including soils, oils, oxides, and smut. Titration readings measure the total alkalinity or acidity levels. Even if the titration readings are fine, watch out for sludge or soil buildup in tanks that because it will reduce the cleaning activity.
2. Rinse the substrate to remove any remaining contaminated solutions from the surface. It also adjusts the pH for the next step.
Conversion coatings are a film which changes the physical and chemical nature of the metal surface. A clean surface is required for the reaction. You might need conversion coatings for your application.
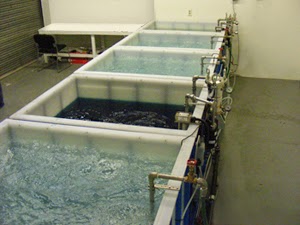
Common types of conversion coatings:
- Iron phosphate for ferrous metals
- Zinc phosphate for ferrous metals
- Chromate conversion for aluminum
- Manganese phosphate
For more information about pretreating for powder coatings, read TCI’s Troubleshooting Guide.
Intech Services and TCI Powder Coatings have partnered to create TruPak, a program that offers over 300 of TCI’s most popular powder coatings in 1, 3, 5, and 10 pound boxes. Click here to buy TruPak powder coatings.
Every day at Intech we receive requests for technical help with DuPont™ Teflon® industrial coatings. If you have a technical question, please feel free to call and speak to one of our technical sales representatives. Once a month, we post a frequently asked question here on our blog.
Question: My part appears to have a rough texture. What causes this?
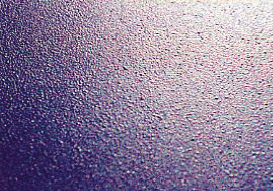
Answer: The DuPont™ Teflon® industrial coating should be smooth and have a soft touch to it. This usually happens when the part is under-baked. Use athermocoupleto make sure the part temperature is correct. When the fact sheet refers to the cure time, it is talking about the temperature of the part’s substrate NOT the oven temperature. Another issue that could cause under-baking, is your oven is not calibrated properly.
If you need more help, call us at 302-366-8530.
Handling & Storage
What is shelf life?
Shelf life is the amount of time, starting from the date the coating was manufactured, that a coating can be stored and still be fit for use.
How to maintain & store Teflon® coatings:
All Teflon® coating fact sheets contain the specific maintenance, handling, and storage information for that specific product. As a general rule, roll each coating for 30 minutes once a month if you are not using it another time for spraying to ensure the coatings last their entire shelf life or longer. Each DuPont™ Teflon® industrial coating line has a different shelf life. Most coatings should be stored at room temperature, but some have special storage instructions. For example, 850G-204 (acid primer) needs to be refrigerated. Refer to the fact sheet for specific instructions, and you can access the facts sheets by signing into your Intech portal.
Maintenance & Reincorporation
How to reincorporate Teflon® coatings:
DuPont™ Teflon® industrial coatings, both water and solvent-based, settle over time, which means proper reincorporation of the solids is necessary for a consistent quality of application over the product’s shelf life. It is recommended that Teflon® coatings be mixed by rolling them in their containers before the first use and the first time the container is opened each day, as well as several times throughout the day while they are being used. For even reincorporation of the solids in the coatings, they should be rolled the first time each day for 30 minutes at 30 RPM. When rolling throughout the day, 10 minutes at 30 RPM each time is sufficient.
Ensuring solids get reincorporated:
Sometimes when rolling, solids stay stuck to the bottom of the container. If you notice this problem, stop the roller and use a stainless steel blade to scrap the solids from the bottom of the container, then continue rolling again. To make sure the solids are fully reincorporated, test the viscosity. Almost all Teflon® liquid coatings’ viscocity can be tested using a Zahn 2 or 3 cup. Click here to see a viscocity conversion table.
Why roll Teflon® coatings instead of mixing or shaking?
Blade mixers and shakers should not be used with DuPont™ Teflon® industrial coatings because the mixing process is too aggressive for the coatings and can separate the fluoropolymer from the coating. Because Teflon® coatings are sheer sensitive, mixing and shaking can damage the coating and adversely affect performance and quality of the cured coating.
A Specific Solution: The Roller II
Intech Services has developed a custom rolling machine that is engineered to roll your DuPont™ Teflon® industrial coatings properly every time. Coatings that come in one gallon cans or jugs and five gallon pails will fit on the roller, with a variable speed selection for each size. The Roller II can be set at the desired RPM and time, and the machine will turn off automatically after the time has expired. Made from solid steel bars and a high quality, reinforced fiberglass base, the Roller II was developed specifically for industrial environments. The Roller makes rolling for shelf life maintenance or reincorporation easy and saves time.
Get Rolling: click here for more information.
Intech Services is proud to announce the launching of the Intech Services Authorized Fastener Coater Program approved by DuPont Fluoropolymer Solutions. By establishing this network, Intech Services and DuPont, hope to provide a distinguished list of coaters who have met a strict list of standards and testing requirements to give assurance of a quality coat job on fasteners.

At Intech Services, the importance of properly engineered and applied coating system is a high priority. In an effort to provide industry competent sources to apply corrosion one coat products, Intech Services, the sole distributor of DuPont™ Teflon® industrial coating in the US and Canada, established the Intech Services Authorized Fastener Coater program approved by DuPont. This program gives fastener users the assurance of a quality job performed by the coater. Chris Dohl, Vice President at Intech Services, says, “Product Stewardship is extremely important to any coating that is honored enough to carry the DuPont™ Teflon® brand name. An authorized fastener coater network is the only way to ensure that our new fastener coating line is being applied correctly. This will enable the end-user to be confident that they will get the performance that they have come to expect from any of DuPont™ Teflon® Finishes.”
The Intech Services Authorized Fastener Program requires the individual coating shops to meet a strict list of standards and testing requirements proving their ability to apply the coating in a way that maximizes the coatings’ performance. Specifically, the coater must demonstrate process and quality testing for coating and/or plating processes and have the proper equipment to apply and test the coating. The coater must submit panels with one mil of 857G-018 applied over phosphate and under go and pass the following tests: 1000 hours of salt spray per ASTM B117, cross hatch adhesion testing to ensure proper substrate adhesion, MEK rub test to ensure proper curing, and appearance test. Passing these tests demonstrates the coater is able to apply the fastener coatings to withstand the environments they are engineered to. The coaters must agree to allow Intech Services to randomly audit their coating process.
For more information on becoming authorized or finding an authorized coater, please visit Intech Services’ website.
Teflon™ industrial coatings are highly durable and long lasting performance coatings that have a distinct application process and qualities that offer solutions in a variety of industrial markets. This series of blogs will highlight one of these inherent properties of Teflon coatings and how these properties can solve a variety of problems.
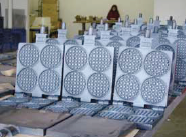
FDA Conforming: Many Teflon™ industrial coatings are approved for food contact by the Food and Drug Administration. These specific designated Teflon coatings can be used for direct food contact according to the regulations of 21CFR. Check a coating’s fact sheet to see if it is FDA compliant. All Teflon coating families have FDA conforming options, but in situations that require a primer and topcoat, both coatings require FDA conformance.
To see all properties of Teflon™ industrial coatings, click
here.
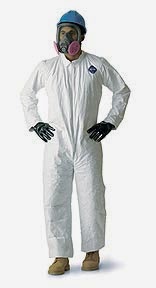
Applying DuPont™Teflon®industrial coatings is not always the cleanest job. It also can be dangerous, with hazardous substances in the air that should not be breathed in or allowed to come in contact with the skin or clothes. Teflon® coating applicators are exposed to chemicals that could potentially harm the body, as well as ruin any work clothes they come in contact with. Shop workers need coveralls and other personal protective equipment to keep safe and clean from overspray, dry particulates, and liquid splashes. Three important factors to consider when choosing coveralls are style, size, and chemical protection. This article will discuss chemical protection.
When choosing coveralls, it is important to figure out which coveralls will resist the chemicals you are exposed to during the work day. They must resist permeation, degradation, and penetration to be used when applying DuPont™ Teflon® industrial coatings. Permeation is the dissolving of molecules through the material, which would allow chemicals to touch the skin. Degradation is when the material physically changes due to chemical exposure or rough use. Penetration refers to chemicals getting under the garment through the zipper, seams, or rips in the material. Coveralls are designed to protect against harmful substances, so the material must overcome all of these factors.
Coveralls are important in the industrial coating shop environment because they add another layer of protection against the hazardous materials that must be handled carefully every day when spraying DuPont™ Teflon® industrial coatings. Wearing coveralls, gloves, respirators, safety glasses, and any other protective garments will help make your shop a much safer workplace.
One coat, solvent-based PTFE coatings for dry lubrication that require tough, durable performance.
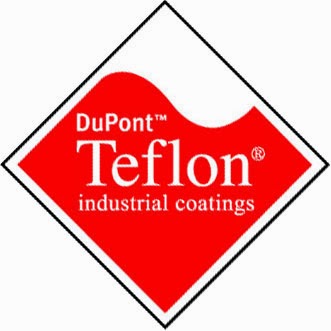
Product Overview
PTFE one coats are superior dry film lubricants with a smooth and slick finish fusing to substrates with strong adhesion to provide great durability. These coatings are excellent for minimizing friction and galling, as well as prevent seizing, especially where re-lubrication with fluid is inaccessible or there is exposure to dirt and dust. In addition to providing lubrication, fluoropolymers used as dry film lubricants provide ancillary benefits of resistance to heat and cold, chemical and corrosion resistance, and release. Flexible cure temperatures of this product line make it more accessible to a broader range of coaters and end uses.
Features and Benefits
- Great for high heat resistance, with an in-use operating temperature of up to 500°F
- Offering includes low cure temperatures as low as 350°F
- Available in a thin film option (958G-303)
- Superior adhesion
- One coat systems offers ease of application
- Solvent-based coating for easy clean up
Performance & Properties
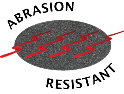
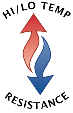
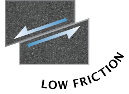
- High Lubricity in a thin film system for Low Friction
- Added Fillers provide additional Abrasion Resistance for 958G-313, 406, 414
- High Heat Resistance allows for operating temperatures of up to 500° F
Product Codes | Colors
One Coat | 958G-303 | Black
One Coat | 958G-313 | Black
One Coat | 958-406 | Black
One Coat | 958-414 | Dark Green
End Uses
- Slide gates
- Hinges
- Blades
- AC pistons
- Springs
- Bearings
- Numerous automotive components
- Lawn and garden
- Guide rails
Chemistry
PTFE with PAI (polyaimeimide) binder resin and additional fillers in 313, 406, and 414.
Application Process
Surface is grit blasted with aluminum oxide, the coating is sprayed on, and is cured at 650°F for 15 minutes. Minimum cure of 350°F can be performed with additional time.
For more information:
Download the product flyer, click here.
Visit Intech’s website- Dry Film Lubricants.
Teflon™ industrial coatings are highly durable and long lasting performance coatings that have a distinct application process and qualities that offer solutions in a variety of industrial markets. This series of blogs will highlight one of these inherent properties of Teflon™ coatings and how these properties can solve a variety of problems.
Nonstick: Very few solid substances will permanently adhere to a Teflon™ industrial coating. While tacky materials may show some adhesion, almost all substances release easily. Teflon™ coatings’ nonstick properties greatly reduce sliding wear and provide excellent release. Anti-adhesion is especially important in the food processing and plastic molding industries because the molds used in these environments must have excellent release or else a significant amount of material will be left behind in the mold. PTFE, PFA, and FEP have the best nonstick qualities.
To see more about the properties of Teflon™ industrial coatings, click
here.
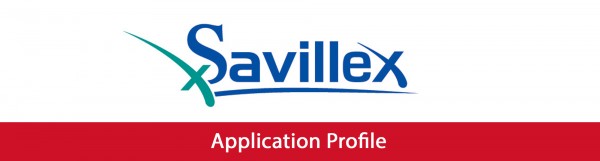
Testing at the DuPont Corporate Center for Analytical Sciences shows DuPont™ TEFLON® PFA/FEP Outperforms Non Fluoropolymer Materials.
Savillex Corporation, of Eden Prairie MN, has developed a unique two-stage stretch blow molding process for its premium Purillex™ high purity PFA and FEP biopharmaceutical packaging product line. The process development, material selection and final product testing was carried out through a close working relationship with DuPont engineers and fluoropolymer materials scientists.
The final product is unlike any other PFA / FEP biopharmaceutical package currently on the market. Manufactured with genuine DuPont™ Teflon® fluoropolymer material, the high purity Purillex™ product line has undergone extensive material testing for organic and inorganic extractables and overall purity.
As a result of this comprehensive testing, the Purillex™ product was determined to have no measurable organic extractables and only ultratrace levels of inorganic extractables, thus making the Purillex™ line of packaging ideally positioned for biopharmaceutical applications.
A full copy of the analytical data report can be obtained directly from Savillex Corporation (info@savillex.com).
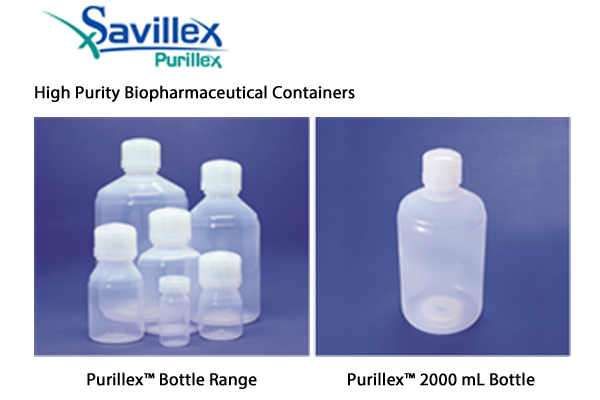
Key Benefits
High purity extreme performance material. Purillex™ PFA and FEP bottles manufactured from from DuPont™ Teflon® fluoropolymers using a proprietary Savillex process are ideally suited for pharmaceutical storage, transportation and packaging due to their excellent chemical inertness, high purity, a wide service temperature range (-200°c +260°c), permeation resistance and mechanical durability.
Unique design characteristics. Savillex has designed the Purillex™ product line with not only high performance fluoropolymer materials but also with several novel design features that allow for complete drainage upon inversion, no fluid retention in the neck threads, non-drip during dispensing and no secondary sealing required.
In addition, the Purillex™ product line has a very smooth interior surface finish which significantly improves cleaning, washout and reduces carryover to subsequent processes*.
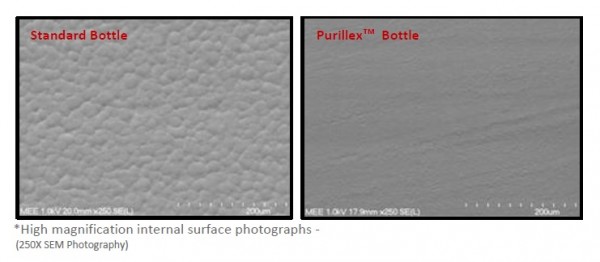
Materials Selected and Why
Purillex™ high purity biopharmaceutical packaging is manufactured exclusively with high performance genuine DuPont™ Teflon PFA and FEP fluoropolymer materials supplied by Fluorogistx of Greenville, DE.
These materials, along with significant DuPont technical and analytical resources, allowed Savillex to meet the challenges of developing a high purity packaging product for the storage, handling and transport of pharmaceutical and biotechnology liquid materials.
Savillex offers six high purity bottle sizes in the Purillex™ product line, ranging from 50 mL to 2000 mL.
Click here to download a copy of this article.
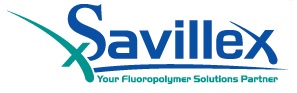
Savillex Corporation
10321 West 70th Street
Eden Prairie, MN 55344
(952) 935-4100
Every day at Intech we receive requests for technical help with DuPont™ Teflon® industrial coatings. If you have a technical question, please feel free to call and speak to one of our technical sales representatives. Once a month, we post a frequently asked question here on our blog.
Question: There are small, round, crater-like holes in the finished coating. What should I do?
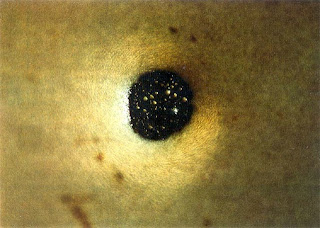
Answer: This is what we call fish eyes, and it’s a result from contaminants in the coating. They could come from improper surface preparation of the substrate, from the air, or the air line for the spray gun. Make sure the spray area and substrate are clean and contaminant-free.
If you need more help, call us at 302-366-8530.
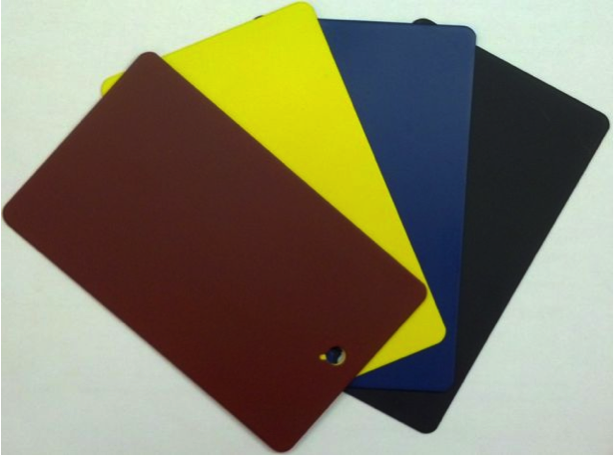
Intech Services is proud to announce the FIRST EVER yellow DuPont™ Teflon® industrial coating.
This new yellow coating (857G-575) expands the color selection of the corrosion resistant one coats, already available in blue, black, and red. We plan to continue to expand the color selection with a green coming soon. These truly water-based coatings offer outstanding corrosion resistance of up to 3,000 Salt Spray Hours with pre-treatment. Along with corrosion resistance, these coatings are targeted for applications requiring anti-galling and dry lubrication. Try this yellow coating to differentiate your shops coating options.
This coating is in stock and ready to ship, so order a jug today. To see more about the corrosion resistant one coats, please visit Intech’s website.
One Coat systems for end-uses that require lubricity, high temperature resistance properties, and FDA approval.
Product Overview
The Teflon® 420G PTFE one coat system is an extremely versatile thin film coating. These products have a high in use operating temperature of up to 500°F and is FDA approved which makes it an excellent choice for application involving food contact. The economical price and ease of application make it an excellent option for high volume jobs. The 420G product line is offered in three colors.
Features and Benefits
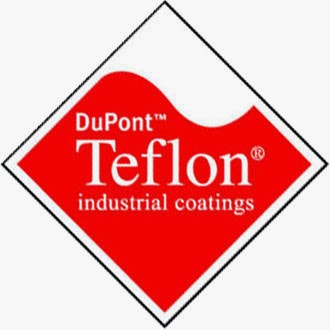
• Substrate Options: steel, stainless steel, and aluminum
• Ease of application: one coat system allows for quick application, excellent for high volume jobs
• Operating Temperature up to 500°F continuous | 550°F for intermittent
• Thin film .8 – 1mil dry film thickness (DFT) – can be applied in multiple coats
• No reduction required
Performance & Properties
• Excellent Nonstick qualities for good release
• Excellent Thermal Stability
• Good Abrasion Resistance and Durability for extended service life
• FDA approved for food contact regulations in 21CFR
Chemistry
One coat with PTFE with a PES Resin (Polyethersulfone)
Application Process
Surface is grit blasted with aluminum oxide. Single coats of .8mils are recommended and can be obtained with several passes of a spray gun, wet on wet. Cure at 700°F – 750°F for 3 to 5 minutes as instructed on the specific coatings’ fact sheet. For clean up or reduction use TN-8595.
Product Codes | Colors
One Coat | 420G-104 | Gray
One Coat | 420G-109 | Sparkling Black
One Coat | 420G-129 | Black
Product Information
Availability: Next Day shipping by Intech
Ordering: Online, Fax, and Phone
MSDS & Fact Sheets: always accessible at intechservices.com
More Information
To download literature, visit Intech’s website.
DuPont™ Fluoropolymer Solutions Increases Capacity for Melt-Processible Fluoropolymer Resins for Cabling Industry: Investment at West Virginia Site Will Enable Expansion of High-end FEP Lines
WILMINGTON, Del., Feb. 19, 2014 – DuPont Fluoropolymer Solutions today announced a plant expansion and capacity increase at its site near Parkersburg, W.Va. site. The expansion will increase production of high-performance fluorinated ethylene propylene (FEP) resins and comes at a time of growing demand for DuPont high-performance FEP.
The expansion will enable an FEP capacity increase of up to 1,000 tons and will be operational in June 2014. The plant will produce a number of FEP resins, including FEP 9494 and FEP 9835, which are melt- processible fluoropolymer resins specifically designed for high-speed extrusion of thin coatings on small-gauge wires for twisted-pair data cabling constructions. These FEP offerings are most often used for IT datacom category cables and data center cables.
“DuPont is the market leader in FEP products and innovation, and this expansion shows our ongoing commitment to the cabling industry,” said Frenk Hulsebosch, global business manager, DuPont Fluoropolymer Solutions. “This capacity increase ensures our cabling customers will continue to have access to premium FEP offerings from DuPont.”
“Our high-end FEP product is the best in the world for wire and cable applications,” said George M. Pruce, North America business manager, DuPont Fluoropolymer Solutions. “We made this investment in response to continuing market demand; we are committed to partnering with our customers to enable the highest quality and most reliable supply to support their growth initiatives.”
DuPont (NYSE: DD) has been bringing world-class science and engineering to the global marketplace in the form of innovative products, materials, and services since 1802. The company believes that by collaborating with customers, governments, NGOs, and thought leaders we can help find solutions to such global challenges as providing enough healthy food for people everywhere, decreasing dependence on fossil fuels, and protecting life and the environment.
Every day at Intech we receive requests for technical help with DuPont™ Teflon® industrial coatings. If you have a technical question, please feel free to call and speak to one of our technical sales representatives. Once a month, we post a frequently asked question here on our blog.
Question: My DuPont™ Teflon® industrial coating has a granular texture with little or no gloss at all. What is going wrong?

Answer:This is called dry spray, and can be caused by several different factors. The viscosity could be incorrect, or it could be an improper choice of thinner, reducer, or activator. Spraying too fast can cause dry spray, as well as the air pressure being too high. The spray gun might be too far from the surface while applying, or the gun may be improperly set up. Always refer to the fact sheets for proper application.
If you need with a specific question, please feel free to call us at 302-366-8530.
Intech Services is offering comprehensive Preventive Maintenance packages servicing all makes and models of industrial ovens. We are proud to represent Precision Quincy Ovens, a leader in the oven manufacturer industry for over 50 years. Precision Quincy is committed to providing the highest levels of service and support to every customer ensuring optimal oven performance.
Planned maintenance and calibration are critical for optimal oven performance. Precision Quincy is proud to offer a Preventative Maintenance Program, designed to keep industrial ovens running like new – efficient, consistent, and worry- free. Ovens should be serviced on a periodic basis. This program schedules annual visits to your facility and completes a full inspection, analysis, and makes necessary repairs. Precision Quincy service technicians are highly trained with years of experience in the industrial ovens industry.
It is important to note that the NFPA 86 requires that all gas ovens be safety tested by a certified technician every year. In addition, Factory Mutual states that the safety test must be performed twice per year, with a uniformity profile annually. These services need to be documented for insurance companies to cover any accidental loss. The Precision Quincy Preventative Maintenance program takes the guesswork out of equipment safety and compliance.
Several different packages are available that will ensure industrial ovens run at peak performance. Precision Quincy can service any oven, regardless of the manufacturer, and discounts are available for multiple oven service packages. Options in these packages include: comprehensive oven inspection, clean fan wheels, clean gas train, oven balancing, door adjustments, louver adjustments, control calibration, NFPA safety testing, 10 point uniformity profile, and onsite maintenance training.
Preventative Maintenance Program Options
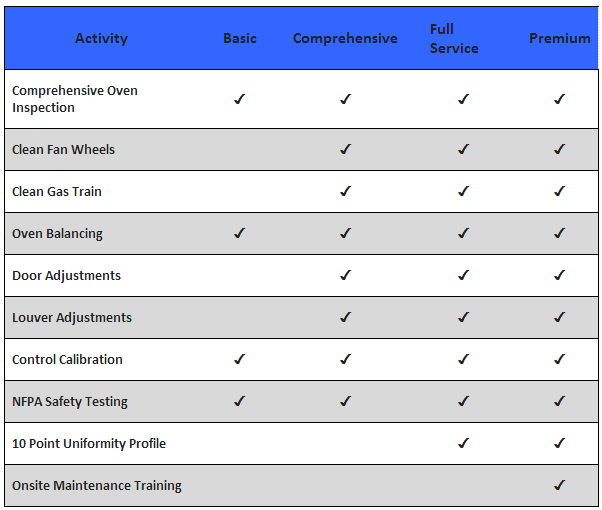
Preventative maintenance is the best way to keep your equipment in optimal working order. This will maintain excellent performance, minimize unscheduled downtime, and extend the overall life of the equipment. For more information click here or to schedule a Preventative Maintenance appointment please contact Cheryl Goldstein cgoldstein@pqovens.com, (302) 602-8738.
Precision Quincy Service
Save money on your next repair service or preventative maintenance appointment with our new Multi-Stop Discount. We are happy to pass savings along to you when we are servicing in your area. Please contact Cheryl Goldstein cgoldstein@pqovens.com, (302) 602-8738 to see when we will be in your area next. If you would like to sign up for multiple years of preventative maintenance or service we automatically apply the multi-stop discount to your account.
The Precision Quincy service team is available to assist your company in several areas in addition to preventative maintenance. These areas include emergency oven repair, oven refurbishment and oven installation. To see more information on Precision Quincy products and services visit www.pqovens.com. Click here to download our oven installation and service guide.
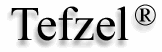
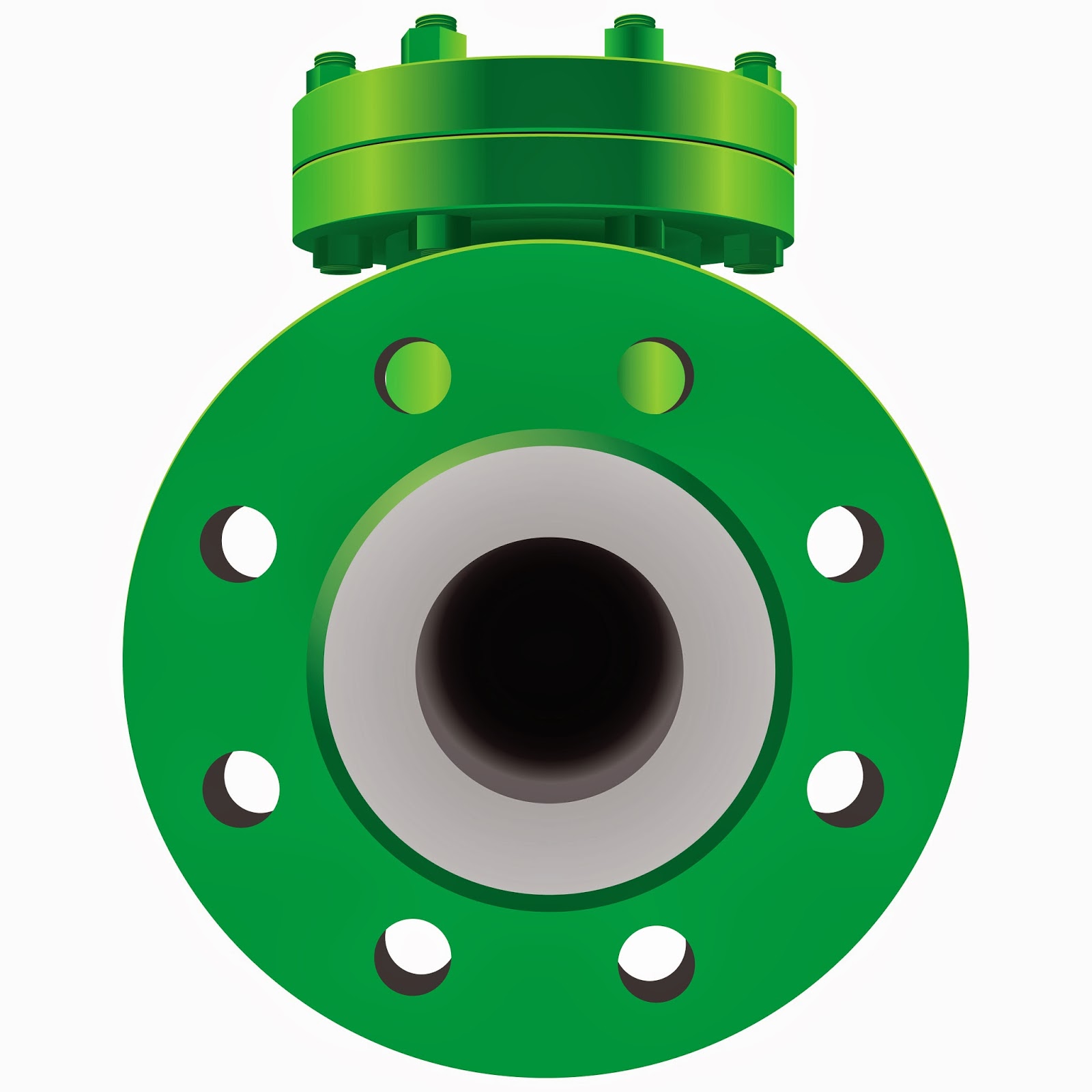
Remember Tefzel®? Contrary to some beliefs, the Tefzel® product line was never discontinued, just referred to as ETFE (Ethylene Tetrafluoroethylene). In 2013, DuPont expanded the product line by developing a powder primer (532-6405) and a high-build clear topcoat (532-6410) to compliment the existing Tefzel® products. The new high build product can be applied to film builds of 80-100 mils, depending upon the job. ETFE is a rugged thermoplastic with an outstanding balance of properties. These new coatings are more chemically resistant at higher operating temperatures. Along with having high thermal stability, when compared to the competition, Tefzel® is extremely tough and electrially insulative with superior adhesion. Tefzel®’s characteristics make the coating an ideal candidate in markets such as chemical processing, semiconductor, pharmaceutical, and food processing.
So if you come across a specification that requires Tefzel®, feel confident that the product is available and with new formulations that now allow for more options. When selecting a coating that will provide superior chemical resistance and durability, Tefzel® is the product that coaters and specifiers have depended upon for decades. In the coating marketplace, there are many solutions you can choose, but Tefzel® is the name you can trust with DuPont’s continued commitment to developing the best products in the market.
Intech Services is the sole distributor of DuPont™ Teflon® industrial coatings. TEFZEL®/ETFE coatings are in stock and ready to ship next day. Ordering and technical help is available online, by phone, or by email. To see or download more information about TEFZEL®, visit Intech’s website.
Every day at Intech we receive requests for technical help with DuPont™ Teflon® industrial coatings. If you have a technical question, please feel free to call and speak to one of our technical sales representatives. Once a month, we post a frequently asked question here on our blog.
Question: There are little pops in the fluoropolymer coating after curing where air bubbles escaped. What should I do to fix this?
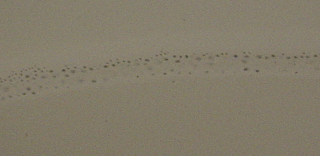
Answer: This is called outgassing. In most cases, this occurs with cast iron or cast metal substrates and can be prevented by preheating the part up to 250°F before applying the Teflon® coating. Preheating the part will release all air that is trapped inside the substrate.
If you need more help, call us at 302-366-8530.
Intech Services is proud to announce our new industrial coating Shop Evaluation program. This program is a customized, on-site shop evaluation bringing you cutting edge, state of the art research, information, and industry recommendations. During the evaluation, Intech will observe and identify quality improvements in coating techniques, shop efficiency, and effectiveness of the equipment used in your process. Having an experienced, fresh set of eyes assessing your shop process will allow for improvements, identify opportunities to enhance business practices, and create growth. With this program, we come to you, therefore there is minimal interruption to your business and no shut down is needed. We analyze your specific shop processes and give immediate recommendations, as well as create a customized business report for you post-evaluation. Everyone in your company from management to spray technicians will benefit from the evaluation and information.
This new program will evaluate your coating process from start to finish, including these critical parts of your application process:

- Material receipt and storage
- Substrate pre-treatment and preparation
- Liquid spray gun setup and maintenance
- Powder spray application process
- Spray booth
- Sprayer evaluation
- Ovens and curing process
- Quality assurance and testing
Brochure and Registration Information
The shop evaluation program adds to Intech’s Information Institute, known as I³, which is training offered by Intech Services in the business of fluoropolymers. I³’s current offerings include the Product, Market, and Sales Strategies and VirtualPaint®, a liquid spray workshop. These workshops are offered once a year in various locations in the United States, as well as a customized on-site training option.
If you want more information about the Shop Evaluation, visit Intech’s website or contact Chris Lord (302-366-8530). If you are interested in registering andscheduling a Shop Evaluation for your shop, please fill out this brief registration form.
To download the brochure, please click here.
When shopping for an industrial oven, the one of the first questions your company will need to answer is whether your oven will be electric or gas.
The first instinct may be to go with electric, because an electric oven is often slightly less expensive than a gas oven. However, in this case the bottom-line price of the oven is not the only cost consideration associated with your purchase. Generally the operational costs for an industrial gas oven will run much lower cost than the operational cost for an electric oven. In some cases, running an electric oven can cost about four times as much as a gas oven. Your operational savings will far out way the upfront cost of the oven and these operational savings are long term.
Here’s a case study of a customer who is trying to decide whether to purchase an electric or gas oven. Here is a comparison of operational costs for this customer:
Electrical Energy Price ($/kW*hr): $0.10
Natural Gas Price ($/Term): $0.83
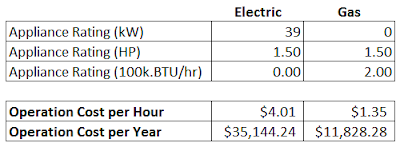
As you can see, it is three times as expensive to run an electric oven over the course of a year. In a few short months, a company could make up for the slightly higher initial costs of the gas oven and save the company money in the long run.
Intech Services is the national sales representative for Precision Quincy Ovens. To talk to someone about your specific oven needs, please call us at 302-602-8738.
For Immediate Release
WILMINGTON, DEL., FEBRUARY 4, 2014 – Delaware Specialty Distribution, the premier U.S. distributor of DuPont™ TEFLON® brand fluoropolymer resins and other DuPont fluoropolymers, has announced a comprehensive branding initiative, culminating in a new name, website and corporate identity for the firm. The specialty fluoropolymers distribution firm will now be known as Fluorogistx.
The branding initiative was undertaken to create a brand that more clearly communicates the unique technical and distribution expertise of the firm. “We wanted our name to better reflect exactly what we do,” explains Fluorogistx President David Jones. “Our customers know us well, but as the firm continues to grow, we wanted our name to convey our progressive commitment to fluoropolymers and logistical excellence. I think Fluorogistx captures that extremely well.”
Members of Fluorogistx senior management team have an average of 30 years’ experience in the chemical industry, specializing in fluoropolymers. “Our decades of experience and close partnership with DuPont have given us a level of fluoropolymer expertise that is virtually unmatched in the industry,” states Bob Smith, Vice President of Sales and Marketing.
From a logistical distribution standpoint, the firm is equally impressive. “We bring a vast, readily available inventory and an ISO 9001:2008-certified process we continually refine,” explains Todd Fredette, Vice President of Operations and Finance. “We’re very nimble and give our customers the timely and accurate turnaround they’re looking for, often next-day or even same-day.”
Representing a larger geographical footprint was also a goal of the branding initiative. “While we are headquartered in Delaware, we’ve been serving clients across the country for years as the exclusive authorized U.S. distributor of DuPont specialty fluoropolymer products,” explains Jones. “We wanted to emphasize our national scope and ability to quickly and expertly respond to customers’ fluoropolymer challenges wherever they may be.”
The firm’s new website, www.fluorogistx.com, includes an “Ask the Experts” section where in-house fluoropolymers specialists offer technical support to help solve customer application challenges. “We’re proud to be the only specialty fluoropolymer distributor with dedicated on-site experts supporting client purchases,” says Smith.
In 2013, the firm earned ISO-9001:2008 certification, formalizing its commitment to deliver the highest level of specialty fluoropolymer products and services for the most demanding applications in North America.
About Fluorogistx
Fluorogistx, formerly Delaware Specialty Distribution, is the exclusive full-spectrum distributor for all DuPont high-performance fluoropolymer products and is the largest non-DuPont source for TEFLON® brand fluoropolymers in the United States. With more than 20 years of experience in the fluoropolymer industry and deep ties to the DuPont organization, Fluorogistx delivers the highest level of service to clients in fields such as telecommunications, automotive, aviation, pollution control, electronics and more. Fluorogistx was originally founded by David Jones in 1993 as Delaware Marketing Services, Inc., (DMS) and later operated under the name Delaware Specialty Distribution. To find out more about Fluorogistx and its fluoropolymer offerings, call 302-479-7614 or visit our website at www.fluorogistx.com.
Media Contact:
Lisa Fritz
Deardorff
319 East Lea Boulevard
Wilmington, DE 19802
302-764-7573
lfritz@deardorffassociates.com
Product Overview
DuPont™ Ruby Red PFA is a filled liquid and powder PFA coating, specifically formulated to reduce permeation and provide superior chemical resistance at temperatures as high as 500°F. In the chemical industry specifically, Ruby Red has proven to hold up longer than other alternatives against extremely corrosive chemicals. There are proprietary filler materials in the Ruby Red that dramatically slow the permeation process that you won’t find in other PFA coatings. The advanced technology of the Ruby Red coating allows it to be applied in multiple layers at 3-10 mils per coat, up to 40 mils. This system’s specific design makes it an excellent choice for any chemical resistant application.

Features and Benefits
• Ease of Application: thicker application allows for less labor
• Substrate options: aluminum, stainless steel, and carbon steel
• Achieve thick film build: up to 10 mil per coat and a 40 mil maximum dry
film thickness (DFT)
• Available in liquid and powder form
• Liquid coating is water-based for easy cleaning
Performance and Properties
• Superior Permeation Resistance
• Excellent Thermal Stability
• Excellent Chemical Resistance
• Good Abrasion Resistance
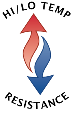
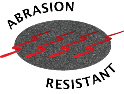
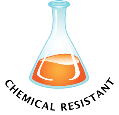

Industries
• Semi conductor
• Chemical processing
• Plating racks
Product Codes | Colors
420G- 703 | Liquid Primer
532G-42551| Powder Primer
532G-13054 | Red | Powder
858G-917 | Red | Liquid
Application Process
Surface will be grit blasted. Application process differs
between the liquid (858G-917) and the powder (532G-13054).
Powder coating is applied electrostatically with hot flocking
for additional coats. Curing temperature is 716°F -740°F and
is lowered intermittently through the curing process.
Product Information
Availability: Next day shipping and stocked by Intech Services
Ordering: Online, fax, and phone
MSDS and Fact Sheets: always accessible at intechservices.com
For more information about this Ruby Red PFA Coating or download a pdf of this information, please visit the Intech Services’ website.
Every day at Intech we receive requests for technical help with DuPont™ Teflon® industrial coatings. If you have a technical question, please feel free to call and speak to one of our technical sales representatives. Once a month, we post a frequently asked question here on our blog.
Question: We applied Teflon® coating according to the fact sheet and after my final curing cycle, the part looks discolored and brittle. What causes this?
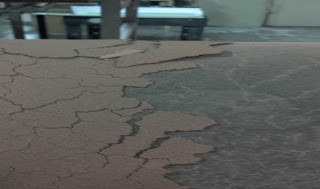
Answer: This usually means the part was over-baked. When the fact sheet states the cure temperatures, it is referring to the actual metal part’s temperature. In order to assure that your part has reached the required cure temperature, use athermocoupleto measure the part temperature while curing.
If you need more help, call us at 302-366-8530.
Because of their temperature/chemical resistance, electrical performance and low flammability, fluoropolymers are the material of choice in vital electrical, sealing, and fluid handling systems in many aerospace and military applications.
On Monday, Mike Patterson, the President of Intech Services, was recognized as a patriotic employer by the ESGR for contributing to national security and supporting employee participation in the National Guard and Reserve force. The ESGR, or Employer Support of the Guard and Reserve, is a part of the Department of Defense that promotes and rewards cooperation between service members and their employers.
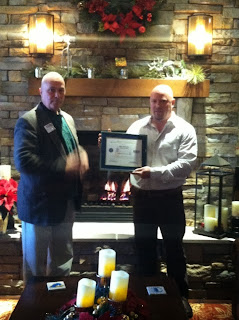
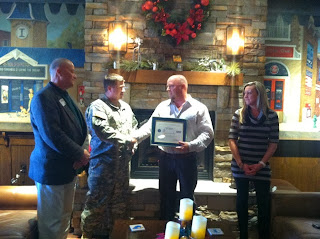
If you have ever called into the office for technical help with your DuPont™ Teflon® industrial coatings, you have probably talked to Nicole McCall at some point for technical service. Her husband, Roger, was overseas in Afghanistan for eight months and recently returned home. Roger is in the Army National Guard in the 153rd MP Company is known as SSG Roger McCall. While he was gone, Intech sent a care package to his unit, which he said was a huge help and comfort when he was so far away from home. Roger nominated Mike as a patriotic employer because of the support that the company showed during such a hard time in his life and for Mike’s commitment to help those fighting to protect our country.
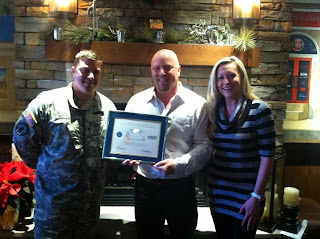
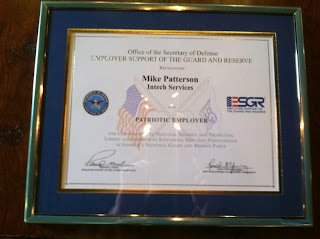
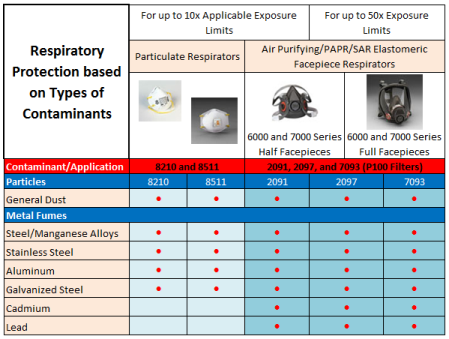
There are many different types of respirators, and each has contaminants it can filter and how much of that contaminant it can handle. The chart above is a quick reference guide for a couple popular types of respirators that are sold at Intech Services.
The contaminants listed have severe potential effects if you are exposed to them. Over exposure to…
Steel/Manganese Alloys can cause pneumoconiosis, siderosis, and central nervous system harm;
Stainless Steel can cause pneumoconiosis, kidney damage, lung irritation, and cancer;
Aluminum can cause respiratory irritation;
Galvanized Steel can cause metal fume fever;
Cadmium can cause metal fume fever, respiratory irritation, kidney damage, and lung cancer; and
Lead can cause central nervous system harm and systemic poisoning.
Particulate respirators (8210 and 8511) will filter up to 10 times the applicable exposure limits only for general dust, steel/manganese alloys, stainless steel, aluminum, and galvanized steel. Do not use particulate respirators for cadmium or lead.
Air purifying/PAPR/SAR elastomeric facepiece respirators (6000 and 7000 series half and full facepieces) will filter up to 50 times the exposure limits for all the contaminants listed.
For more information or to order respirators, check out our respirator section on the website.
We’re at the Chem Show 2013 right now!
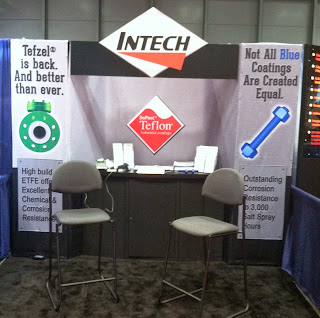
Chem Show is a trade show where process engineers, plant personnel, and executives from chemical processing industries come to learn about the latest breakthroughs in chemical technology. The event is taking place from December 10th to the 12th at the Javits Convention Center in New York City.
We are displaying DuPont™ Teflon® industrial coatings, specifically Teflon® one coat anti-corrosion coatings, the new Tefzel® (ETFE) and Ruby Red PFA coating. Chris Dohl presented today on our new DuPont coating technologies including the new Tefzel® and corrosion resistant Teflon® one coats in a New Product Presentation. It was a success and gave more exposure of these coatings and other fluoropolymer coatings to the chemical industry.
If you are at the show, please stop by our booth #743.
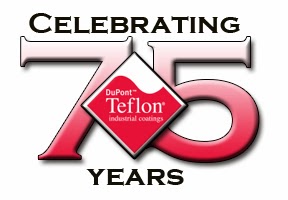
This year marks the 75th anniversary of the invention of PTFE, later named and trademarked as DuPont™ Teflon®. The “accidental invention” of Roy Plunkett, a DuPont chemist, is a flouropoloymer that is now used in virtually every manufacturing industry, service industry, military and many medical applications. It has become an essential part of our everyday lives in the most unassuming of ways.
While researching new, safer chlorofluorocarbon refrigerants in 1938, Plunkett had tetrafluoroethylene gas stored in containers at dry-ice temperatures. When he opened a container, onoe of the gas came out. Instead, a white powder had formed inside, which was later found to be the polymer of tetrafluoroethylene (polytetrafluoroethlyene), known today as Teflon.
By 1941 PTFE had a patent process and trade name, Teflon®. From its original development, Teflon® coatings have evolved from machine and industrial applications to its most famous use, a non-stick surface for cookware. Further development of fluoropolymers included the discovery of these other widely used fluorpolymers, ETFE, PFA, and FEP. DuPont is still innovating today with their fluoropolymers.
Today, Teflon® coatings have expanded into many polymers found in industries as diverse as aerospace and pharmaceuticals. This is a multi-million dollar industry that is sold in over 40 countries worldwide.
The impact of Teflon® coating is felt in most aspects of everyday life. Flouropoloymers are critical to new development in the fields of medicine, environmental conservation, energy solution, space exploration and civilian and military safety.
Without Dr. Plunkett’s inadvertent discovery, the world as we know it would not exist and function as it does today.
See Intech’s website for more information about industries where DuPont™ Teflon® industrial coatings are used.
Fluoropolymers are specified in many local area network, computer, and mobile telephony applications due to their outstanding electrical performance and fire/temperature resistance — vital for system critical equipment and devices. This has become increasingly important as more and more interactions in society become technology-dependent.
Click here to view a video on the uses of DuPont Melts in consumer electronics.
On a daily basis, Intech fields questions regarding Teflon™ industrial coating recommendations for use in chemical environments. Generally speaking, Teflon coatings perform very well in environments that require excellent chemical resistance; however, some of our coating families like Ethylene/Tetrafluoro Ethylene (ETFE) and Perfluoroalkoxy (PFA) perform better than others. If you still have questions, there’s a great reference manual used at Intech that can assist specifiers with additional supporting information.
The Chemical Resistance Guide for Plastics provides the most comprehensive, third party chemical resistance data that is available in the marketplace. There are thousands of chemicals, as simple as beer to something highly aggressive, like hydrofluoric acid that have been evaluated against a wide variety of fluoroplastics, fibers and thermoset resins. So regardless of the coating or lining that you are applying, there’s a good chance you’ll find some performance data to support your recommendation in the Chemical Resistance Guide for Plastics.
The next time your customer asks for a coating with superior chemical resistance, identify the specific chemical, concentration, and operating temperature. Then for additional information refer to the Chemical Resistance Guide for Plastics to answer your questions. In most instances, the data will be there, and you’ll feel better about your recommendation. If you can’t find the information you need in the guide, please contact Intech for further detail.
To see more information or to purchase the Chemical Resistance Guide for Plastics, please visit Intech’s website.
Article written by Chris Lord, Technical Sales at Intech Services.
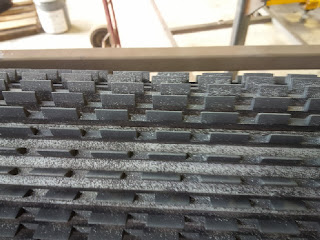 |
A picking roller with 3-coat reinforced coating that was over baked. |
DuPont’s premier coating system combines excellent durability and lubricity in a thin film (1.5mils). This 3-coat, reinforced, water based system, 857G-040, 857G-140 and 857G-240, differs from many of our other water based Teflon*coating options because it contains a primer, a mid-coat and a topcoat. However, it requires a high temperature, short duration bake cycle and due to the sensitivity of this cure cycle, the coating is susceptible to curing errors leading to re-work and lost money.
In order to control the sensitive cure of this DuPont™ Teflon® industrial coating system, it is highly recommended that the use of direct wired thermocouples attached to the substrate to prevent the three most common curing errors for this system: under-cure, over-cure, and improper part temperature ramp up. The use of IR thermometers is discouraged because they create inaccuracies and oven heat loss.
From an application perspective, this coating is relatively easy to apply. The primer is applied over an ambient part that has either been grit blasted or is smooth (aluminum) and force-dried at 250F to drive off the water. The mid-coat and topcoat are applied wet over wet, so there isn’t a cure or drying required between mid-coat and topcoat.
The last step in this process is a five minute cure at 800F, which is the highest cure of any DuPont Industrial Teflon*products. This coating system does allow for a higher cure, 815F for three minutes, but peak temperature should never reach more than 825F and the amount of time at that high temperature should not extend past three minutes.
With an undesired film finish, it is imperative to understand the end result and how to rectify. An under cured film will lack gloss and produce a soft film, which can be fixed by recurring at the proper oven temp. An over cured film will display a haze and a yellowish color, but in extreme over bake situations the film will discolor to a blue/gray state. Unfortunately, the only way to correct an over bake situation is to grit blast the part and start the coating application process again.
The least common problem is an improper part temperature ramp up which can result in the coating experiencing too high of a temperature in an expedited timeframe. This can cause a situation called “skinning” where there is a vast difference in the substrate temperature and the coating’s temperature or the substrate temperature elevates too quickly. It is not recommended that a freshly coated, ambient part be placed in an oven that is at 815F.
How often do curing errors occur in your shop? Is re-work a common issue for your coaters?
Register for an account on Intech Services to create your own private customer center portal and order a 3-coat reinforced coating for your needs.
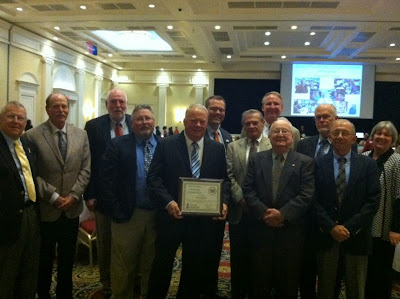
Bob Patterson, the recipient of the 2013 Governor’s Outstanding Volunteer Award
We would like to honor and congratulate one of Intech Service’s founders, Bob Patterson, for receiving the 2013 Governor’s Outstanding Volunteer Award in Community Service. One might know Bob for his great achievements in building Intech Services to what it is today, but he also has achieved much outside of the business and in retirement has been able to invest even more time in these volunteer efforts.
The Governor’s Outstanding Volunteer Awards recognize exceptional individuals and groups who make a difference in Delaware by volunteering countless hours to benefit Delawareans.
The recipients of these awards have made significant contributions by improving the lives of those less fortunate, advocating for causes and raising both money and awareness for important needs. These individuals are strong leaders who are inspiring and generous in there support of volunteerism.
Bob has been an integral part of Sussex County’s Habitat for Humanity for nearly 20 years. Doing everything from volunteering with construction, sitting on the Board of Directors, and being a member of the Construction Management Team, Bob has completed homes in over 10 towns in Sussex County.
In the past 5 years, Bob has worked over 2500 volunteer hours and in the past year alone he has completed 22 projects. A Brush with Kindness, Bob’s newest challenge, helps homeowners who live in owner-occupied poverty homes with much-needed repairs and renovations. As the leader of A Brush with Kindness, Bob has led youth, adults, and seniors on projects such as ramp building for wheelchairs and replacing roofs.
Bob’s love of Habitat for Humanity has no limits. In addition to his work in Delaware, he has traveled to Alabama, Mexico, and Guatemala to participate in other construction projects. Additionally, Bob volunteers with his church in Lewes as well as another organization, Samaritan’sPurse.
Thank you Bob for all your great work!
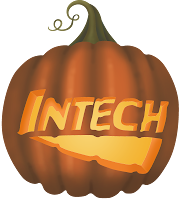
November 1, 2013 marks the beginning of our freeze protect season and runs through April 1, 2014. Intech Services, Inc. takes great care, through additional packaging and by services offered by our common carriers, to protect our customer’s shipments from freezing. The water-based product lines affected by this freeze policy are (by prefix): 699N, 850G, 851G, 852G, 855G, 856G, 857G, 858G, and 953G. Our solvent based and powder products do not need to be freeze protected.
For freeze protected freight shipments in the Northeast, Mid Atlantic, and Canadian regions Intech Services will ship Monday – Friday. For the remainder of the United States, freeze protected freight will ship Monday and Tuesday only. Freeze protected ground shipments will ship on Monday and Tuesday. The freeze protect fee is $29.00. For freight shipments, this is a per pallet charge, for ground shipments this is a per container charge. Overnight service is available if receipt of the material is critical.
It is important that when you receive a freeze protect shipment that you follow the instructions attached to your bill of lading and the container. In all freeze protect shipments there will be a freeze indicator. If the freeze indicator in a shipment is blue or purple, this is only an indication that the product MAY have frozen during shipment. Please accept the shipment and contact Intech immediately. Intech Services, Inc. must be notified of claims within 4 days of the receipt of the shipment. Intech Services will replace any freeze damaged product, except where a customer waives the Freeze Protect Service or fails to notify Intech of the freeze damage within the required timeframe.
Please share this information with anyone in your shipping, receiving, procurement, or any other divisions that need to be aware of this policy. If you need any additional clarification, please contact us at (302) 366-8530 or review our Freeze Protect Policy on our website. We appreciate your attention to this matter and, as always, thank you for your business.
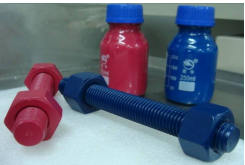
After extensive salt spray and kesternich testing, Intech Services is proud to announce the placement of DuPont 857G-018 fluoropolymer product on the DuPont SP11C specification for fluoropolymer-coated fasteners. As of an update in May 2013, the DuPont™ Teflon® industrial coating 857G line is now an option for application to meet SP11C standards.
DuPont SP11C specification is the corporate engineering standard for fluoropolymer-coated fasteners that require excellent corrosion resistance. DuPont SP11C is a specification for fasteners that are intended for use in severe atmospheric corrosive environments. It is not recommended for use in immersion service. The coating system is comprised of two coats: a sacrificial base coat of electroplated zinc or ceramic/metallic coating, and a fluoropolymer top coat applied by an applicator qualified by DuPont. Since fluoropolymer coatings have a low coefficient of friction, the make-up torque values for fasteners coated according to SP11C will be reduced.
The DuPont™ Teflon® industrial coating 857G product line is a new technology targeting applications requiring anti-galling and dry lubrication. It is a water-based, low VOC, easy-to-use coating offering outstanding corrosion resistance that can be applied at .0005 to .0045 inches thick by conventional spray or dipspinning. The performance test ASTM B117 showed less than 10% rust on fasteners coated with 857G-018, the blue version of these coatings, after 3,000 salt spray hours. VOC emissions were less than 3.0 pounds per gallon. There are several coating color options. “Getting the DuPont 857G coating line included on SP11C took years of development and testing. Its inclusion on the specification in May of 2013 should indicate to the coating and corrosion engineering communities the robustness of this coating,” said Chris Dohl, Vice President of Intech Services.
Intech Services is the sole distributor for DuPont™ Teflon® industrial coatings to the US and Canada. For more information about purchasing, applying, or data on these fluoropolymer coatings, contact Chris Dohl at Intech Services by phone (302-366-8530) or email. For more information, testing, and data about this new DuPont Corrosion Resistant Coating technology, please visit intechservices.com.
To view the control version of the SP11C standard specification, please visit the Standards Intranet Homepage. For more information from DuPont about their specification, contact Valerie Lamison by email (Valerie.s.lamison@dupont.com)
Click here to see the full press release.
Fluorogistx, the exclusive authorized U.S. distributor of DuPont™ TEFLON® brand fluoropolymers and other DuPont fluoropolymer resin products, announced it has received ISO-9001:2008 certification as of March 8, 2013. With certification, the company has formalized its long-standing commitment to deliver the highest level of specialty fluoropolymer products and services for the most demanding applications in North America.
“If you want to have a quality attitude, you must have a quality system, and ISO 9001 certification validates that we have well-defined and documented procedures in place,” explains Todd Fredette, Vice President of Operations for Fluorogistx.
To attain the highly respected certification, Fluorogistx met the requirements of the world’s largest developer of voluntary international standards, the International Standardization Organization (ISO), which publishes standards implemented by more than a million companies and organizations in 170 countries. The organization presents precise specifications for products, services and practices that help ensure safety, reliability and good quality for customers.
Steve Selway, Quality Manager, adds “Our ISO certification ensures that our processes are controlled so that we ship exactly what our customers want, exactly when they want it. It also certifies that we are always striving for continuous improvement to better serve our customers.”
Fluorogistx, the exclusive authorized U.S. distributor of DuPont™ TEFLON® brand fluoropolymers and other DuPont fluoropolymer resin products, has announced the addition of Robert D. (Bob) Smith, formerly of DuPont FluoroPolymer Solutions, as Vice President of Sales and Marketing.
Smith, who reports to David Jones, president and founder of Fluorogistx, joins the senior management team bringing more than 30 years of DuPont experience, primarily in fluoropolymers and most recently as Business Director and Sustainability Manager for DuPont FluoroPolymer Solutions. His experience includes both U.S. and global management of sales and marketing teams within the company’s fluoropolymer businesses, and helping DuPont to maintain its global market leadership position throughout his career.
At Fluorogistx, Smith will build on his successful track record of leading teams and delivering strong results by focusing on advancing market development and customer focus to provide tailored solutions – for TEFLON® brand fluoropolymers and more.
“Fluorogistx has always been known for helping our customers grow their businesses through innovative applications using DuPont™ TEFLON® and other DuPont fluoropolymers. The collective fluoropolymer knowledge at Fluorogistx, coupled with the strength of our working relationship with DuPont, provides a level of technical expertise and customer service that are unmatched in the industry,” said Smith. “I look forward to contributing to the continued growth and success of our customers as well as Fluorogistx.”
Diane Iuliano Picho, NA Regional Business & Market Director, DuPont Chemicals & Fluoroproducts, recognizes what a significant asset Smith will be for Fluorogistx. “Bob brings a tremendous amount of experience, knowledge and results-driven leadership to the Fluorogistx team,” she said. “Creating a positive customer experience is always his top priority, and Bob is extremely adept at building relationships and problem solving.”
Typical Troubleshooting with Spray Guns
Problem
|
Cause
|
Correction
|
Gun will not spray |
1. No air pressure 2. Fluid needle adjusting screw is not open enough 3. Fluid is too heavy for suction lead |
1. Check air supply and air lines 2. Change to proper suction feed air cap 3. Increase fluid pressure at the tank, open fluid needle adjusting screw |
Fluid leak or fluid jetting from fluid tip |
1. Contamination on needle or tip 2. Incorrect fluid tip or fluid needle fitted to gun 3. Fluid needle stuck or binding up |
1. Remove tip and needle and clean surfaces thoroughly 2. Check needle/tip charts and find correct size 3. Remove and clean fluid needle shaft, lubricate and loosen needle packing |
Paint build up on air cap |
1. Damaged air cap holes 2. Gradual build up of bounce-back on gun head |
1. Replace with new air cap 2. Thoroughly clean gun |
Stiff trigger action |
1. Air valve stem bent 2. Contamination on air valve stem 3. Contamination on trigger bearing screw 4. Contamination on fluid needle shaft 5. Fluid needle packing is too tight |
1. Replace damaged air valve 2. Remove air valve and clean 3. Remove screw and clean 4. Remove fluid needle and clean 5. Loosen packing nut |
Unable to get round spray |
1. Fluid tip or baffle incorrectly fitted 2. Air baffle chimney damaged |
1. Remove and check components for damage 2. Replace air baffle |
Air leak from around air valve stream |
Air valve seal damaged or missing |
Replace air valve |
Air valve will not operate when trigger is pulled |
1. Air valve stem bent 2. Contamination on air valve stem |
1. Remove valve and replace damaged stem 2. Remove valve and clean |
Incorrect Spray Patterns
Causes and Corrections
Spray Pattern
|
Cause
|
Correction
|
Top- or bottom-heavy spray |
1. Plugged horn holes 2. Fluid tip obstruction 3. Dirty air cap |
Clean, ream with non-metallic point |
Right- or left-heavy spray |
1. Plugged right or left horn holes 2. Dirt on one side of fluid tip |
Clean, ream with non-metallic point |
Center-heavy spray |
1. High fluid pressure 2. Material flow is faster than air cap’s capacity 3. Spreader adjustment valve is set too low 4. Atomizing pressure is too low |
1. Balance air and fluid pressures 2. Thin or adjust fluid flow 3. Adjust valve 4. Increase pressure |
Split spray |
1. Fluid adjusting knob turned in too far 2. Atomization pressure is too high 3. Fluid pressure is too low |
1. Back out counter clockwise to achieve proper flow 2. Reduce pressure at the regulator 3. Increase fluid pressure or choose a larger tip |
Spray Gun Cleaning
To clean air caps: Remove the air cap from the gun, place it in a clean solvent, and blow dry. If the small holes are clogged, after soaking the cap in the solvent, use a toothpick or some other similar soft implement (not wires or nail becuase they can damage the cap) to ream the holes.
To clean pressure feed guns with an attached cup: Turn off the air supply, loosen the cup cover and remove the fluid tube from the paint. Pull the trigger while holding the gun over the paint cup to let the rest of the paint drain back into the cup. Empty the cup and wash with a clean solvent and cloth, then fill the cup halfway with clean solvent and spray it through the gun to wash out the fluid passages. Make sure you spray into an approved, closed container and that you follow local codes about disposing of solvents! Clean the air cap and wipe the gun with a cloth soaked in solvent.
To clean pressure feed gun with a detached cup or tank: Turn off the air supply and open the relief valve. Material in the hoses may be blown back, so make sure the lid is loose and the gun is higher than the cup or tank! Loosen the air cap and pull the trigger until all the material is back in the cup or tank. A gun cleaner should be used to ensure proper cleaning. Place the gun and cups over the nozzles in the cleaner and close the lid tightly. The cleaner will spray solvent through the nozzles, keeping the solvent contained so it can be disposed of properly. Be sure to dispose of the solvent correctly according to local codes.
Intech Marketplace has cleaning, repair kits, and seal kits for spray guns from BInks & Devilbiss and Nordson.
VirtualPaint Training™
Intech Services offers a VirtualPaint™ training workshop for spraying liquid coatings as part of our Intech Information Institute. If you have not heard of it, this program allows attendees to improve their spraying technique, film thickness, and transfer efficiency in a virtual spray environment, eliminating any waste associated with spray application training.
Click here to find out more information or register for our upcoming workship on September 26, 2013 in Newark, Delaware.
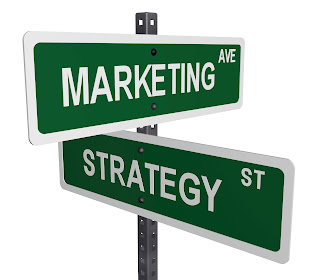.jpg)
Marketing is always changing and expanding, and it can be difficult to keep up, especially with industrial marketing. Not only do you have to learn all the new technology involved in marketing, you have to use it to your advantage.
You should always use all of the resources available. This includes reading articles about your industry, keeping up with relevant blogs, and collaborating with other people in your company to gain a better understanding of your processes, products, or services.
Decide how you want to focus your marketing efforts. Do you want to focus more on print advertising, email communications, social media, or other marketing areas? Prioritize your tactics by figuring out which marketing channel is best for your industry.
Industrial marketing can get a little overwhelming sometimes, but if you sit down and reevaluate the situation, your marketing efforts will pay off.
If you ever need help marketing DuPont™ Teflon® industrial coatings, please contact Intech’s Kate Morgner (302-366-8530 x121). She would enjoy working together to market our coatings to your end users and customers.
If you are interested in Industrial marketing information, you can read this article and others on the Marketing Maven blog.
When purchasing DuPont™ Teflon® industrial coatings, ordering the appropriate thinner or reducer is often an afterthought. All liquid DuPont™ Teflon® coatings are ready to be applied straight from the container. Thinners can be used for jobs where a lower viscosity is needed or for cleaning and maintaining your spray equipment. Thinners are a cost effective and simple way to clean spray guns, by simply running thinner through the gun to clean out the coating from the passage. Well-maintained guns apply coatings with more efficiency and uniformity, as well as save time and money caused by equipment breakdowns.
Intech Services has specific thinner/reducers for the solvent-based DuPont™ Teflon® coating product lines and it is extremely important that the correct thinner is used. DuPont fact sheets give instructions for the appropriate thinner to be used for reduction and cleanup for the specific coating. Here is a summary of the recommended thinners for the various product types:
- TN-8595 – 420G, 958G, and 959G solvent-based products
- TN-8748 – 954G line solvent-based products
- De-ionized water is recommended for reduction and clean up for all water-based products
When adding thinner to reduce material, it is recommended that you do so in small increments, around 2-3% at a time. After adding thinner/reducer, the material should be re-incorporated by rolling. Rolling is the preferred re-incorporation method for liquid DuPont™ Teflon® coatings.
The reduction of the liquid coatings will change the performance properties of the finished coating and the coating mixture while spraying. Thinning can have effects on: the appearance of the finished product, the performance quality of the coating, increase the sensitivity to the required bake cycles, and shorten the pot life of the material. Technicians should be aware of these potential changes when applying reduced material.
Powder coating transfer efficiency is one of the most important aspects of a powder coating process. It is defined as the amount of powder that is adhered to the part versus the amount of powder that is sprayed. Higher transfer efficiency makes it easier to achieve thicker coatings, have better coverage, generate less waste or reduce recycle volumes, and increase through put.
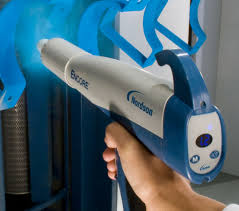
Which processing and equipment parameters affect transfer efficiency? All of them. The most important may be grounding. There must be a very good earth ground to the part. There must be clean metal to metal connections between the part and all hooks, racks, carts, and the ground wire. Ideally the ground will be an eight foot long grounding rod driven into the ground with a heavy gauge wire leading to the process area. If it is a batch operation or a large part, connect a ground wire right to the part or to the holding fixture. The most common problems with grounding are overspray build up on hooks or fixtures that interfere with the grounding pathway or not grounding to a good ground point. Having a cart or fixture sitting on concrete is not a grounded system, nor is clipping a ground wire to a painted building beam. Grounding to the powder coating control unit’s ground lug is usually not sufficient either.
The next most important component of transfer efficiency is the electrostatic setting on the powder coating control unit. The electrostatic settings on the coating gun need to be lower than what is typically used for epoxies and polyesters, in the range of 25 – 35kV or 20 – 30µA. The high charges that are used for epoxy powder coatings will make fluoropolymer powders overcharge and get repelled from the part. Overcharging will also prevent powder from coating into recesses and corners. Automatic current control settings may be found that work in a particular application, but many times a manual voltage setting will work the best.
Other coating properties that will affect transfer efficiency are air and powder flow, powder gun nozzle type, shape of the part, particle size distribution, powder polymer type, humidity, booth airflow, and operator technique.
Article written by Craig Hennessey, Research Investigator with DuPont in the Teflon finishes division. Craig started at DuPont in February 2000 and has a degree in Chemical Engineering. As Research Investigator, he formulates DuPont fluoropolymer powder coatings and provides technical service for customers using DuPont coatings. Craig is experienced in industrial application of fluoropolymer coatings, especially in powder coating of large chemical processing equipment.
This is the first of many articles for the Intech Insider written by a DuPont employee. Intech and DuPont work closely together to bring you the best fluoropolymers on the market. We also want to provide cutting edge information and a broad expertise in the coating business.
The semiconductor industry is almost entirely dependent on fluoropolymers as they are the only materials that can hold and transport the harsh chemicals used in the manufacturing process. Without them, electronic equipment such as personal computers, cellular phones, LCD, Plasma and LED displays could not be produced.
As relatively lightweight plastics with exceptional chemical resistance, fluoropolymers help aircraft and auto makers meet ever-increasing standards for weight, fuel economy and emissions. Their ability to withstand the harshest environments, from high-temperature sealing and electrical systems to fluid handling, is critical.
Inert, corrosion-resistant fluoropolymers preserve equipment and system integrity for the chemical processing industry. They not only help protect workers, but also provide valuable benefits to business, including higher productivity and less potential liability.
Fluoropolymers are used in power generation and pollution control systems. With low permeability and chemical and temperature resistance, they help protect people and avoid emissions to the environment, while also ensuring system reliability when used in applications from filters to wire insulation to process components.
Chemical and corrosion resistant fluoropolymers used in fluid handling or component carriage systems help ensure a process free of contaminants. Industries that depend on high-purity environments have also begun considering fluoropolymers as an alternative to traditional stainless steel in their operations.