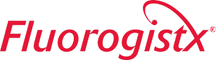
When
coating services employees’ hands are in contact with hazards, employers must
require the proper hand protection to be worn. To figure out which kind of
glove works best for hazardous environments such as surface blasting and
Teflon™ coating, coating services companies must evaluate the gloves’
protection requirements relative to the tasks being performed, and consult
industry standards for safety.
The
Occupational Safety and Health Administration, or OSHA, has the general
requirements for selecting appropriate gloves (Standard
1910.138 – Hand Protection). This standard covers protection selection requirements when
hands areexposed to
hazards such as those from skin absorption of harmful substances, severe cuts
or lacerations, severe abrasions, punctures, chemical burns, thermal burns, and
harmful temperature extremes.
The
American National Standard for Hand
Protection Classification is another guide for selecting appropriate gloves. The document
gives test methods
and classification levels for many glove characteristics. It also has pass/fail criteria
for hazardous exposures, such as chemical permeation, detection of holes, and
heat and flame resistance. Here we review common high-temperature gloves that
should be part of your Teflon™ coating supplies, and the
basics of sizing and maintenance.
For
applications where high heat protection is the top priority, Kevlar®
gloves
are often the answer. The looped construction of Kevlar traps air, making these
gloves excellent insulators. The fabric also gives greater durability and cut
resistance than regular string knit work gloves. Other high-temperature
gloves
include reversible mitts, Flextra® unlined heat resistant gloves, and heavy
duty olive drab flame retardant knit wrist gloves.
Butyl gloves have the highest permeation
resistance to gases and water vapors of any other glove material. They offer
excellent resistance to methyl isobutyl ketone and methyl pyrrolidone, found in
thinners TN-8595 and TN-8718. Blasting gloves protect hands and arms from high
pressure particles, and welders gloves include options such as reflective
aluminized leather back wool-lined gloves.
Regular
glove maintenance is important in ensuring employee hand protection. Proper
care can also save you money by extending the life of each pair. Proper glove
maintenance focuses on three main areas: cleaning, inspection, and storage. Each
pair should be inspected for damages on both the inside and outside prior to
use, and all gloves should be kept in well ventilated containers away from
direct sunlight.
When
choosing gloves for workplace safety, two key factors that should always be
considered are glove size and cuff style. Choosing appropriately sized gloves
is as simple as measuring the circumference of your hand just below the
knuckles.