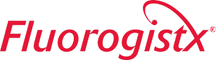
Salt spray testing is used to ensure long-lasting coating performance in a number of industries. For instance, the Oil & Gas industry often requires salt spray testing to confirm that fasteners (nuts, bolts, etc.) are being coated properly to be used in particularly harsh environments, such as on oil rigs in the ocean. The end-user can require assurance—and certification—that the parts that a coater is supplying will be both corrosion resistant and perform well many years down the road. The results of the salt spray testing supplies that assurance and certifcation.
Salt Spray Testers are closed cabinets that continually introduce a salt water (5% NaCl) solution to parts via a mist or fog. Spray nozzles atomize the salt water with pressurized air, accelerating a corrosive environment for test parts.
One Teflon™ product line that does particularly well in corrosion-resistance and salt spray testing for Oil & Gas industry parts is the PTFE 857G product line. These coatings have low coefficient of friction, anti-galling, and dry lubrication properties that are ideal for the Oil & Gas industry. The 857G coating system is available in blue, red, yellow, and black.
Other one-coat Teflon products that have excellent salt spray resistance for industrial applications would be FEP Teflon S One-Coats. These user-friendly thin film options are a combination of fluoropolymer with binder resin and are thermally set:
The Teflon 857G coating system is comprised of two coats: a sacrificial base coat of electroplated zinc or ceramic/metallic coating, and a fluoropolymer top coat applied by a qualified applicator. The coating is water-based, low VOC, and easy-to-use, applied at .0005 to .0045 inches thick by conventional spray or dip-spinning. When tested according to the ASTM B117 Standard, fasteners coated with 857G-018 (blue) showed less than 10% rust after 3,000 salt spray hours, and VOC emissions were less than 3.0 pounds per gallon. Find Authorized 857G Coaters here, or become an Authorized Coater yourself here.