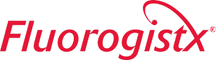
Both the powder and liquid versions of Ruby Red PFA Teflon™ coatings are excellent chemically resistant options because of their high permeation resistance to both liquids and gasses. This permeation resistance is a result of the proprietary filler materials in Ruby Red Teflon™ coatings that you won’t find in other PFA coatings.
In the chemical industry specifically, Ruby Red has proven to hold up longer than other alternatives against extremely corrosive chemicals at temperatures as high as 500° F. The advanced technology of the Ruby Red coating allows it to be applied in multiple layers at 3 – 10 mils per coat—and up to 40 mils total.
Ruby Red PFA coatings require high oven curing temperatures, as high as 750 – 800° F, and the chemical industry parts coated with Ruby Red tend to be large. Ruby Red is used most often on aluminum, steel, cold-rolled steel, and stainless steel products.
The main differences between Ruby Red liquid and powder are the maximum thicknesses and the curing times for each. Because of the differences, liquid Ruby Red PFA is more often used when coating larger parts.
Liquid Ruby Red can achieve thick film builds, up to 10 mil per coat and a 40 mil maximum dry film thickness (DFT). The powder Ruby Red has a lower maximum DFT of 20 mil. However, Intech and Chemours do not recommend pushing those upper limits when avoidable.
Liquid Ruby Red also requires longer cure times, up to 3-hour final bakes, while the powder Ruby Red has shorter cure times. Powder coating is applied electrostatically with hot flocking for additional coats. One other advantage of the liquid coating is that it is water-based for easy cleanup.
The length of active service life for Ruby Red PFA depends greatly on the quality of the initial coating. Here are some tips for keeping that coating quality high: