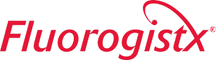
Powder coating transfer efficiency is one of the most important aspects of a powder coating process. It is defined as the amount of powder that is adhered to the part versus the amount of powder that is sprayed. Higher transfer efficiency makes it easier to achieve thicker coatings, have better coverage, generate less waste or reduce recycle volumes, and increase through put.
Which processing and equipment parameters affect transfer efficiency? All of them. The most important may be grounding. There must be a very good earth ground to the part. There must be clean metal to metal connections between the part and all hooks, racks, carts, and the ground wire. Ideally the ground will be an eight foot long grounding rod driven into the ground with a heavy gauge wire leading to the process area. If it is a batch operation or a large part, connect a ground wire right to the part or to the holding fixture. The most common problems with grounding are overspray build up on hooks or fixtures that interfere with the grounding pathway or not grounding to a good ground point. Having a cart or fixture sitting on concrete is not a grounded system, nor is clipping a ground wire to a painted building beam. Grounding to the powder coating control unit’s ground lug is usually not sufficient either.
The next most important component of transfer efficiency is the electrostatic setting on the powder coating control unit. The electrostatic settings on the coating gun need to be lower than what is typically used for epoxies and polyesters, in the range of 25 – 35kV or 20 – 30µA. The high charges that are used for epoxy powder coatings will make fluoropolymer powders overcharge and get repelled from the part. Overcharging will also prevent powder from coating into recesses and corners. Automatic current control settings may be found that work in a particular application, but many times a manual voltage setting will work the best.
Other coating properties that will affect transfer efficiency are air and powder flow, powder gun nozzle type, shape of the part, particle size distribution, powder polymer type, humidity, booth airflow, and operator technique.
Article written by Craig Hennessey, Research Investigator with DuPont in the Teflon finishes division. Craig started at DuPont in February 2000 and has a degree in Chemical Engineering. As Research Investigator, he formulates DuPont fluoropolymer powder coatings and provides technical service for customers using DuPont coatings. Craig is experienced in industrial application of fluoropolymer coatings, especially in powder coating of large chemical processing equipment.
This is the first of many articles for the Intech Insider written by a DuPont employee. Intech and DuPont work closely together to bring you the best fluoropolymers on the market. We also want to provide cutting edge information and a broad expertise in the coating business.