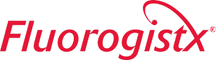
The fluidized bed process is used to apply powder coatings by dipping heated parts into a cloud of powder, caused either by a constant airflow or an electrostatic charge, and the powder melts to the hot surface. The final thickness depends on part temperature and how long the substrate is dipped in the powder, and film thicknesses can be achieved from 8 up to 125 mils. This process requires preheat temperatures of at least 350°F and may require a post-heat or cure cycle.
Fluidized bed steps:
1. Part is preheated to 400°F-450°F
2. Initial deposit melts onto part
3. Film builds from residual heat
4. Coated part removed when desired thickness achieved
Fluidized bed advantages:
Fluidized bed disadvantages:
For more information about the fluidized bed process, read TCI’s Troubleshooting Guide.