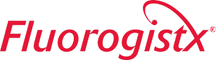
Polyurethane foams are used in construction for insulation, sound
absorption, various types of padding, and structural reinforcement. Outside of
construction, polyurethane foam is an integral part of household appliances,
automobiles, packaging, and footwear. The Teflon™
coating properties that allow for excellent release are
non-stick, low coefficient of friction, ease of cleaning, and FDA compliance.
The polyurethane
molding industry has long relied on manually applied release
agents on their metal molds for rubber or plastic components during the
manufacturing process. The procedure of applying these release agents is both time-consuming
and expensive. Teflon™ coatings are now offering long-term solutions that
completely replace release agents for a variety of the products used in polyurethane
molding.
When maintained properly with regular cleaning, Teflon™ coatings
can perform through thousands of molding cycles. Removing release agents offers
significant benefits to polyurethane foam manufacturers in the form of enhanced
compliance with environmental regulation, improved safety conditions for
employees, reductions in product defects, and the complete elimination of dry
ice blasting.
Teflon™ coatings are also now being used to coat polyurethane mixing
blades for easy cleaning and extended service life of the blades. Hardened
foam quickly builds up on the steel mixing blades, and the processes for
removing it can be very time-consuming and labor-intensive. One case
study saw polyurethane foam production increase dramatically. By
cleaning quickly between mixes with methylene chloride and paper towels, the
company was able to accomplish up to 13 mixes in a single day.