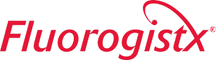
Film thickness consistency plays a big role in saving money in the coating shop. Having inconsistent thicknesses means you’re probably wasting coating, and therefore wasting money. By using these simple techniques, you’ll be able to cut out the waste, as well as achieve a better, more consistent finish for your DuPont™ Teflon® industrial coatings.
Click here to see the first 3 tips from last week.
Spray Pass Speed: Adjust the spray gunspeed to achieve consistent films. Before pulling the trigger, consider the coating flow rate and the target wet film thickness. Adjust the equipment before spraying to find a flow rate that lets the applicator move at a controllable, comfortable speed. Spraying too fast can lead to decreased film thickness, and sometimes extra coats will be needed to make up the deficit.
Trigger Control: Maintaining a consistent trigger pull on each spray pass directly impacts the flow rate, spray pattern size, and transfer efficiency. Start triggering immediately before the lead edge of the part and release the trigger immediately following the lag edge. Fully pulling the trigger provides constant flow rate control. The fluid knob on your spray gun can be adjusted to restrict the trigger travel distance so you can always pull the trigger all the way. Partial triggering, however, can be very useful for blending and touching up.
Edge Banding: Partially pull the trigger to spray a light coat around the edges of the part. Then spray the center of the part, blending the edges into the first coat. Banding can increase transfer efficiency and increase film thickness on the edges. This technique ensures the edges get coated completely while maintaining consistent film thicknesses.