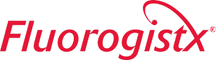
In previous blog posts, we’ve covered the common types of spray guns, choosing spray guns and keeping them clean, troubleshooting spray gun issues, and overcoming the Faraday Cage Effect. Here we’ll review some techniques that will help you save money while spraying and also how to choose which feed system and gun type will be best for your applications.
Film thickness consistency plays a big role in saving money in the coating shop. Having inconsistent thicknesses means you’re probably wasting coating, and therefore wasting money. By using these simple techniques, you’ll be able to cut out the waste, as well as achieve a better, more consistent finish for your application.’
1. Spray Distance
The spray distance is based on the spray equipment, coating, complexity of the part and spray environment. By keeping the gun at the same distance from the part the entire time you’re spraying, you can improve the consistency the film thickness over the whole part. Increasing the gun distance increases the pattern fan size, and the coating thickness decreases as it is distributed over a larger area.
2. Gun Angle
Maintain controlled gun angle to the part. Yaw and pitch spray angles will result in a non-uniform spray pattern distribution, causing inconsistent film thicknesses.
3. Spray Pass Overlap
Each spray pass should overlap 50% to 75% of the previous pass. Overlapping below 50% results in “striping,” or variations in the film thickness. The more you increase the overlap, the thicker the coating, so overlapping above 75% requires more spray passes and more coating.
4. Spray Pass Speed
Adjust the spray gun speed to achieve consistent films. Before pulling the trigger, consider the coating flow rate and the target wet film thickness. Adjust the equipment before spraying to find a flow rate that lets the applicator move at a controllable, comfortable speed. Spraying too fast can lead to decreased film thickness, and sometimes extra coats will be needed to make up the deficit.
5. Trigger Control
Maintaining a consistent trigger pull on each spray pass directly impacts the flow rate, spray pattern size, and transfer efficiency. Start triggering immediately before the lead edge of the part and release the trigger immediately following the lag edge. Fully pulling the trigger provides constant flow rate control. The fluid knob on your spray gun can be adjusted to restrict the trigger travel distance so you can always pull the trigger all the way. Partial triggering, however, can be very useful for blending and touching up.
6. Edge Banding
Partially pull the trigger to spray a light coat around the edges of the part. Then spray the center of the part, blending the edges into the first coat. Banding can increase transfer efficiency and increase film thickness on the edges. This technique ensures the edges get coated completely while maintaining consistent film thicknesses.
We have a large selection of spray guns with many combinations of gun platforms and feed systems. Here is some information to help you decide on the best feed system for your shop:
GRAVITY FEED SYSTEMS use cups attached to the top of the gun and use gravity to feed the coating into the gun. Gravity feed guns can have different coatings switched out quickly and require less pressure to operate. However, the cups are usually small and do not hold much coating, so they are best for coating small parts.
SIPHON FEED SYSTEMS use cups attached to the bottom of the gun and create a vacuum that sucks the coating into the gun. Siphon feed guns are heavier that gravity feed guns, but the cups hold more coating.
PRESSURE FEED SYSTEMS use pots that utilize air pressure to push the coating through a tube into the gun. No fluid can leak from the pot, so you don’t have to worry about wasting coating. The gun itself is lighter than gravity and siphon feed guns because there is no cup attached to the gun at all. You can also spray with the gun upside-down or at sharp angles and not worry about the coating coming out of the cup.
CONVENTIONAL SPRAY GUNS use a basic high pressure. The coating is blasted onto the part at this high pressure using an air compressor. The high pressure finely atomizes the spray giving the coating a very smooth finish. Transfer efficiency for Conventional spray guns is typically 50% or less.
HIGH-VOLUME LOW-PRESSURE (HVLP) spray guns increase transfer efficiency, typically to about 65%, meaning more of the coating actually makes it to the part instead of being wasted. With HVLP guns, air is delivered at much higher volume than conventional guns, but with a much lower pressure, so that more finish ends up on the part instead of in the air. HVLP guns are compliant with the California South Coast Air Quality Management District.
TRANS-TECH SPRAY GUNS use low volume, medium pressures. Transfer efficiencies are normally about 60% or better. Trans-tech guns are the best of both worlds: the finish quality is almost that of a conventional spray gun with close to the efficiency of an HVLP spray gun. Trans-Tech is used where compliance is not required but cost savings is important.
Here’s a handy chart for deciding between Conventional/Air Spray, HVLP, and Trans Tech/Compliant.
And more on Troubleshooting spray guns here.
How to overcome the Faraday Cage Effect.
…and more on the most common spraying methods.