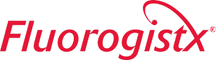
All liquid products must be rolled, shaken or stirred to ensure that all settled solids are reincorporated. Some Teflon™ products are shear sensitive, and cannot be stirred using high speed mixing equipment. This information is contained in the Fact Sheet for each product.
All liquid products must be rolled, shaken or stirred to ensure that all settled solids are reincorporated. Some Teflon™ products are shear sensitive, and cannot be stirred using high speed mixing equipment. This information is contained in the Fact Sheet for each product.
Most products are supplied ready to spray, at normal spray viscosity. If the product must be thinned before spraying, check the Fact Sheet for the correct material to use.
Most products are supplied ready to spray, at normal spray viscosity. If the product must be thinned before spraying, check the Fact Sheet for the correct material to use.
Any substrate which is dimensionally and thermally stable at the bake temperature required for the particular product can be coated with Teflon™ Industrial coatings.
Articles to be coated should be free of sharp corners and edges, excessive pits or porosity and excessive roughness as at welds and joints.
At bake temperatures greater than 450ºF/232°C, certain metallic substrates are unacceptable. The melting points of tin (450ºF/232ºC) and lead (622ºF/328ºC) are too low to permit some Teflon™ bakes. The poor adhesion of copper to the copper oxide formed when copper is baked in air at high temperatures results in poor adhesion of the Teflon™ industrial coatings. Because of reactivity at the high baking temperatures, Teflon™ coatings have relatively poor adhesion to magnesium and to aluminum/magnesium alloys containing more than 0.5% magnesium. Aluminum permanent-mold castings and die castings are successfully coated with Teflon™ coatings, but may show a high reject rate due to the formation of blisters caused by expansion of air bubbles in the metal during the high temperature bake.
In all cases, Teflon™ coatings should be applied over clean substrates. Normal industrial practices, such as chemical washes or solvent cleaning and degreasing can be used, but precautions must be taken to remove all residues from the cleaning process. Depending on the initial condition of the metal, it may be necessary to physically remove dirt, rust, mill scale, paint, etc. After cleaning, the metal should be handled with gloves. Fingerprint contamination may show up as a stain on the finish. Residual oil also may cause stains.
Preheating metal substrates to the temperature of the Teflon™ bake is advantageous in removing traces of oil and other contaminants, especially when the metal is cast and somewhat porous. With most ferrous metal, this procedure has the advantage of temporarily passivating the surface against rusting and the blue oxide formed increases the adhesion of the acid primers. In the case of aluminum and stainless steel, these advantages are not apparent and the preheating step can be omitted where clean metal is involved. Copper and brass should not be preheated in air because the resulting oxide has poor adhesion to the metal. A formic acid rinse reduces oxide formation somewhat on copper.
Grit blasting is the method most commonly used to obtain good adhesion of Teflon™ finishes. Grit blasting should always precede preheating on ferrous metals in order to retain the protective oxide formed. With other clean substrates the order of these two operations is not important. Surface profiles in excess of 100 microinches (2.5 microns) are recommended and 200-250 microinches (5.1-6.5 microns) are frequently employed. On hard substrates, aluminum oxide grits from #40 to #80 are commonly used at air pressures ranging from 80 to 100 psi (5.8-7.3 kg/cm2) at the gun. Aluminum and brass are commonly used at air pressures ranging from 80 to 100 psi (5.8-7.3 kg/cm2) or below. Maximum air pressures on stainless steel may exceed 100 psi (7.3 kg/cm). Chilled iron grit, because of its high density and sharp particle shape, has found considerable use in blasting metal substrates. This grit is recommended for centrifugal abraders because its density is approximately twice that of aluminum oxide. (NOTE: Due to imbedding of small particles of ferrous grit, some rusting may be visible when light-colored aqueous-based Teflon™ fluoropolymer coatings are used). Sand is considered too smooth, uniform and short-lived to be useful in preparing metal substrates and is not recommended. Glass beads have produced surface roughness equal to aluminum oxide grits.
Grit blast profiles are commonly measured in microinches or root mean square (RMS) by means of a profilometer. A rough estimate of profile is also obtained (on non-ferromagnetic metal) by means of an eddycurrent thickness gauge.
It should be noted that profiles measured by the methods above, including common profilometers, indicate only depth of profile. They do not measure uniformity or coverage of the grit, nor the sharpness of the peaks. Full coverage of the grit blast is indicated by lack of gloss on the metal surface when viewed at a flat grazing angle.
Too severe grit blasting, wire brushing, or sanding causes pits, scratches, and cuts and should be avoided because the finish may flow into the depressions and mud cracking can occur.
While grit blasting is the preferred metal treatment for the application of most Teflon™ finishes, other methods of surface roughening are employed in special cases. Wheel sanding, wire brushing, and directional grinding may be used where best adhesion is not required. These operations reduced adhesion in the direction of the grind. Chemical etching gives smooth Peaks, without the sharp “tooth” required for best adhesion. Rough, as-cast surfaces also are too smooth in microprofile for best adhesion.
Cleaning by grit blasting, sandpaper, steel wool, or No.400 emery cloth is much better than any wet method such as chromic acid, hydrochloric acid, or sulfuric acid. In addition, the etching reagents require immediate rinse to stop the action and prevent salts from depositing on the surface. This creates an oxidizing or rusting problem that may require additional No.400 emery cloth or steel wool hand work plus rinsing and dry off to remove the oxide.
For reinforcement of a substrate, a discontinuous layer of stainless steel such as 309 alloy may be applied to grit blasted metal. However, we do not recommend this procedure for a dissimilar substrate such as aluminum, because for the potential of bimetallic corrosion, no matter what the chromium content of the stainless steel.
Conversion coatings are the modified surfaces of metal resulting from specific chemical treatment. These conversion coatings, which can be on steel, aluminum, or most other metals, typically include zinc, manganese, and iron phosphates or chromates. The principle function of these coatings is to improve adhesion of finishes and maximize corrosion resistance. The functionality of conversion coatings depends upon their uniformity and the integrity of the coating, both before and after application of the final finish.
In general, the acid primers 850-Line and 851G-204, are not suited for application over conversion coatings since the strongly acidic nature of these products severely disrupts the conversion coating. Furthermore, in most cases PTFE coatings cannot be applied to conversion coatings since the high temperature bake destroys the integrity of the conversion coating. This is particularly true when the substrate is steel.
Conversion coatings are often used with 954, 958, and 959-Lines. For steel substrates, micro crystalline zinc phosphate is an effective conversion coating. Also, manganese phosphate has proven to be very effective, particularly in corrosive environments. The use of iron phosphate on steel is less effective, particularly where corrosion resistance is needed. For aluminum, chromate conversion coatings are best. The generalities offered here may not be valid, and any particular system may be viable depending on the processing limitations and the end-use conditions.
Since steel and iron rust rapidly after grit blasting, coatings should be applied immediately. Where delay is expected; or under conditions of high humidity, a solvent rinse with VM &P naphtha, or toluene containing 5 % of kerosene may be employed. When the volatile solvent evaporates, a very thin film of kerosene remains to prevent rusting temporarily. While the presence of thin films of kerosene does not appear to affect the application of the 850-Line primers, the kerosene film may collect dust on long standing and require solvent washing before the finish is applied.
Many types of application equipment can be used for Teflon™ coatings. The most widely used are listed below. Certain types are better for different coatings. Where one is particularly suitable, or not recommended, the product Fact Sheet will guide your choice. Teflon™ products are generally applied by commercial spray techniques. This must be done in a hood or well ventilated area to prevent fluoropolymer or solvent fumes from affecting breathing air of employees. See Safe Handling Fact Sheet for respirator recommendations.
Many types of application equipment can be used for Teflon™ coatings. The most widely used are listed below. Certain types are better for different coatings. Where one is particularly suitable, or not recommended, the product Fact Sheet will guide your choice. Teflon™ products are generally applied by commercial spray techniques. This must be done in a hood or well ventilated area to prevent fluoropolymer or solvent fumes from affecting breathing air of employees. See Safe Handling Fact Sheet for respirator recommendations.
Separate spray guns should be used for water-based and solvent-based products.
Once a part has been coated and allowed to dry, do not allow overspray from other areas to fall on the part. Overspray will not melt back into the finish therefore, will leave rough areas on the finish.
Many coatings are shear sensitive, and the action of the needle moving in the fluid tip of the gun can cause coagulation. This shear induced coagulation can be minimized by keeping the fluid delivery open and altering the fluid delivery by regulating the pressure on the pressure pot.
In most cases, compressed air and standard spray equipment are the most suitable for fluoropolymer coatings. The spray guns should be held perpendicular to the piece using a flat, rectangular motion of the spray gun. “Whipping” the gun in an arc tends to make the wet film bubble and will cause excessive beading on the edges of the part.
Suction, gravity, or pressure type spray equipment are all suitable for spraying Teflon™ coatings. All spray equipment should be made from aluminum or stainless steel, or coated with Teflon™ S. Transfer lines should be chemically inert and solvent resistant (e.g. Teflon™ tubing, polyethylene, stainless steel). Air lines must be trapped to prevent oil or water from contaminating the compressed air or the product.
Normal distance from the gun to the part is 4-12 inches (10-30 cm). If the gun is too close, the finish will look rippled. If it is too far, the spray will be dry and rough. Reducing the atomizing pressure will help resolve both problems, too.
Automatic spray guns are generally used in large volume, conveyorized systems, where the parts to be coated are uniform in shape. While the set-up requires experience and careful adjustment, films can be applied more uniformly and at a faster rate. The finishes are fed to the guns through pressure pots with fluid pressures in the range of 5-8 psi (0.5-0.6 kg/cm2).
Where flat items are carried on a flat bed conveyor, the spray guns may reciprocate transversely and spray continuously.
Electrostatic guns or discs are suitable for the application of many Teflon™ coatings. The advantages of electrostatic application include better film uniformity and 10-15% savings in material, due to the reduction in overspray. High volume production is usually required to justify the expense of automatic electrostatic systems, but relatively low-priced hand units are available.
Many Teflon™ coatings are water-based with low resistivity (‘1igh conductivity). For these finishes, electrically isolate all the coating equipment, including pressure pots and transfer lines. Consult the equipment supplier for proper grounding techniques. Electrostatic potentials for 80,000 to 90,000 volts are commonly used for Teflon™ coatings.
Certain Teflon™ S products must be adjusted with non-polar solvents before being sprayed electrostatically.
This technique uses high pressures to atomize and direct the coating material. Since the opening of the gun tip is generally smaller in diameter than in conventional compressed air spray, shear conditions during spray may be too high for aqueous Teflon™ products. Airless spray is generally used when coatings must be applied in deep recesses.
Teflon™ powder coatings are free-flowing powders which are applied with conventional electrostatic powder equipment, with either spray guns or fluidized bed. The application voltage and technique depends on the particular equipment, although the highly attractive nature of the powder permits a wide range of application voltages.
After one or two coats, the part may become too insulated for subsequent coats of Teflon™ powder to be applied electrostatically. In this case, the part may be sprayed hot (hot flocked) as it comes out of the oven from curing the previous coat. This requires adequate ventilation. Even the small amounts of decomposition products of fluoropolymers which occur at bake temperatures may cause discomfort to people in the area if the fumes are not vented to the outdoors and allowed to be diluted by the outside air.
Dip and flow coating techniques have been successfully used to apply Teflon™ S coatings.
Roller coating has been used with some Teflon™ S resin-bonded coatings. The aqueous Teflon™ coatings are generally too shear sensitive to use in this manner.
Brushing on Teflon™ or Teflon™ S coatings is only practical for making small repairs. Brush techniques cannot normally apply uniform films thin enough to prevent cracking and popping during baking.
Many Teflon™ coatings can be applied in multiple coats. This process requires careful attention to bakes of intermediate coats to prevent deterioration of underlying coats. Ability to apply multiple coats also depends on the wetability of the intermediate coats. This property varies considerably depending on the product. Consult the Fact Sheet for the product you are using to see if it can be applied in multiple coats.
Many Teflon™ coatings can be applied in multiple coats. This process requires careful attention to bakes of intermediate coats to prevent deterioration of underlying coats. Ability to apply multiple coats also depends on the wetability of the intermediate coats. This property varies considerably depending on the product. Consult the Fact Sheet for the product you are using to see if it can be applied in multiple coats.
Reaching and maintaining proper cure temperatures for a sufficient period of time to sinter, melt flow, or set the film is one of the most important factors in achieving a finish which will perform at its optimum. All temperatures mentioned in the Fact Sheet refer to metal temperatures, meaning that the part must be placed in an oven set at a high enough temperature and for a long enough time to allow the part itself to reach the recommended cure temperature. Ovens should be calibrated at least twice per year, and thermocouples should be used on the parts.
For coatings which are primarily PTFE, PFA and FEP fluoropolymers, no film formation will take place below certain minimum temperatures. This means there is a limited, but practical, baking range for PTFE, FEP, PFA products mentioned in the <!–Fact Sheet for the product.
Reaching and maintaining proper cure temperatures for a sufficient period of time to sinter, melt flow, or set the film is one of the most important factors in achieving a finish which will perform at its optimum. All temperatures mentioned in the Fact Sheets refer to metal temperatures, meaning that the part must be placed in an oven set at a high enough temperature and for a long enough time to allow the part itself to reach the recommended cure temperature. Ovens should be calibrated at least twice per year, and thermocouples should be used on the parts.
For coatings which are primarily PTFE, PFA and FEP fluoropolymers, no film formation will take place below certain minimum temperatures. This means there is a limited, but practical, baking range for PTFE, FEP, PFA products mentioned in the Fact Sheet for the product.
Teflon™ S coatings contain organic binders in addition to the fluoropolymer resins. Cure time and temperature are important considerations for these coatings also, but there usually is a greater range of possible cure temperatures, resulting in varying film properties. Excessive bakes (time and/or temperature) will degrade the auxiliary organic binder, causing discoloration, film embrittlement and loss of adhesion.
Teflon™ S coatings stratify during the cure process, so that the fluoropolymer is more concentrated at the surface. The result of underbaking (or baking at the lower end of the specified temperature range) will be limited stratification, as well as reduced adhesion, hardness, corrosion resistance and abrasion resistance.
All commonly used types of industrial ovens are used for curing Teflon™ industrial coatings. Teflon™ coatings are not affected by the combustion products of coal gas or natural gas, so direct fired gas ovens may be used. Both batch ovens and high production conveyorized ovens are used. Conveyorized ovens must be carefully designed to give accurate and uniform temperature control since maximum conveyor speed and minimum oven length are important economic factors which operate to reduce dwell time.
Ovens should be calibrated at least twice per year, and thermocouples used on the parts themselves or in the oven at several locations, recognizing that air temperatures are of little value except when based on experience with a given oven and oven load over a period of time.
Factors which affect total bake time (including warm up):
May be gas fired, direct or indirect, or heated by electrical resistance coils. Good circulation is required for uniform heating. Convection ovens require longer time to warm up than infrared ovens, and conveyorized systems require greater floor space for equivalent line speeds.
Offer the advantages of rapid transfer of radiant energy, ability to control speed of warm-up by placement of the radiant elements and reduced dwell time. It is less effective where coated parts are complex in shape, since infrared energy travels in a straight line and the intensity of heat is inversely related to the distance (squared) from the source, so inner crevices and angles will not cure at the same rate as outer surfaces facing the source. High velocity air may be used to make the air temperature more uniform.
Ventilation of ovens is very important for the safety of workers. Ventilation is usually provided via an outdoor stack. Negative pressure should be maintained at all times with an inward draft at both the entrance and exit of the oven. Even the small amounts of decomposition products of fluoropolymers which occur at bake temperatures may cause discomfort to people in the area if the fumes are not vented to the outdoors and allowed to be diluted by the outside air.
If you are experiencing any coating application issues, please fill out this form and we will be happy to help troubleshoot the problems.