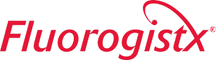
TEFLON™ PTFE granular molding powders are manufactured in an enclosed, positive pressure system using purified air and water. The packaging area is under positive pressure with “air-lock” doors, tile floors, enamel walls and flush-mounted lighting. The following storage and handling recommendations will help to preserve the high quality of these resins.
Teflon™ granular resins are not shipped refrigerated. However, when these resins are shipped in a truck with fine powder resins, the granular products may arrive at the customer’s plant below PTFE’s room temperature transition temperature of 19°C (66°F).
Chilled resin: When granular PTFE resins arrive in a refrigerated truck, the drums should not be opened immediately. Good practice is to let them sit in the sealed container for 24 to 48 hours at a temperature of 23°C-27°C (73°F-80°F). Granular PTFE resins stored by customers in a refrigerated area must be removed from cold storage to an area where they will have time to warm before the drums are opened.
While PTFE resins are not hygroscopic, powder which has been chilled and then exposed to a damp atmosphere will become wet from condensation. Moisture will cause the preform to crack during sintering.
It is important not to preform PTFE powder below the 19°C (66°F) transition temperature even when the relative humidity is below 50%. Preforming cold powder will result in cracked preforms because the resin expands 1.5% in volume as it goes through the room temperature transition. The easily damaged preform cracks because it cannot resist the forces of the large volume change. To avoid this type of cracking, it is important to preform all granular powders at 23°C (73°F) or higher.
Unchilled resin: Unchilled resin received by customers should be stored at a temperature of 23°C-27°C (73°F-80°F) in a clean, dry area.
The Importance of Cleanliness: The importance of cleanliness in processing PTFE resins can hardly be over-emphasized. PTFE readily attracts particulate contaminants because it is a highly electrostatic material. The high sintering temperature and the whiteness of the resin intensify the effects of contamination. The smallest speck of atmospheric dust, oil or other organic substance can be carbonized during sintering leaving clearly visible dark, white or clear spots in a contaminated molding. While such imperfections may not have important effects on physical properties, they are undesirable in appearance. Conditions and practices suitable for molding other plastics may not be adequate for PTFE resins.
Opening the Drum: Before opening a drum of “Teflon” PTFE granular resin carefully clean the outside of the lid to remove contaminants picked up during shipping and storage. Granular PTFE resin is packed in a drum lined with a loose polyethylene bag. The bag is twisted and tied at its top. Before removing the tie, the outer surface of the bag should be vacuum cleaned to remove particles of contamination. Remove the tie, untwist the bag and fold the bag over the rim of the drum to protect the powder from contaminants trapped between the outside of the bag and inside of the drum. Promptly remove the amount of resin needed (into a clean container with a lid), close and twist the bag, and retie. Replace the drum lid until more resin is needed.
It is important to vacuum the inside of the drum and the outer surfaces of the bag liner when the entire drum is to be dumped into the mold cavity at one time (see footnote A). This will prevent loose particles trapped between the liner and the inside of the drum from falling into the mold cavity along with the resin.
Preforming: Preforming normally is carried out at temperatures between 23°C-27°C (73°F-80°F). Storing the powder before use in a room maintained at 23°C-27°C (73°F-80°F) and below 50% relative humidity helps avoid moisture condensation and also minimizes the tendency of the powder to form lumps in hot weather. Improved product quality, uniformity and reduced scrap losses justify the investment in such facilities.
An ideal arrangement for the molder consists of a room at 23°C-27°C (73°F-80°F) for temperature conditioning, weighing and preforming the powders. The room should be separated from the sintering operation and from the processing of other plastics. It should have a separate filtered air supply maintaining a slight positive pressure inside the room. Cleanliness conditions and practices suitable for molding other plastics are usually not adequate for PTFE resins. Operators should wear clean, lint-free coveralls and maintain a high standard of cleanliness.
Lumps: Granular PTFE resins may compact and form lumps during shipment. Soft lumps usually can be broken up sufficiently with a clean scoop to permit filling of mold cavities over 25mm (1 inch) wide. In rare instances screening through a clean, coarse (8 to 10 mesh) screen may be advisable. Remember: it is difficult to screen the resin and avoid contamination.
Harder lumps should be placed in a clean, covered container, chilled to about 10°C (50°F) and shaken vigorously. Be sure to allow the container and the resin to warm to the 23°C-27°C (73°F-80°F) range before removing the container’s lid.
Footnote (A): We do not recommend or encourage dumping an entire bag of resin into the mold cavity at one time. This practice will produce moldings with non-uniform density and can cause cracking. We recommend loading powder evenly into the cavity (no matter how large the mold) with a clean scoop.