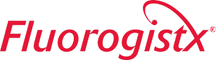
The following characteristics are common to all Teflon™ coatings in varying degrees. The unique combination of properties inherent to all Teflon™ industrial coatings make them a natural choice in a number of industries.
Very few solid substances will permanently adhere to a Teflon™ coating. While tacky materials may show some adhesion, almost all substances release easily. Wear due to sliding is very low due to the anti-adhesive properties. For many applications, a significant problem is the buildup of foreign particles, and Teflon™ nonstick coatings’ excellent release qualities help solve these issues.
Friction is a force created when two objects rub together that hinders the motion. With a Teflon™ industrial coating, the coefficient of friction is generally lowered to a range of 0.05 to 0.20, depending on the load, sliding speed, and type of coating used. Lubricity is very important in any application that has moving parts touching each other.
Heat – Teflon™ fluoropolymer coatings can operate continuously at temperatures up to 550ºF, and can be used for intermittent service up to 600ºF with adequate ventilation. The thermal stability of the coatings means that they can be used in high heat environments without losing or affecting any other properties.
Cryogenic Stability – Many Teflon™ coatings can withstand temperatures as low as -454ºF without loss of physical properties. Their ability to withstand sub-freezing temperatures means that Teflon™ industrial coatings will not lose any of their other characteristics when exposed to such low temperatures.
Chemical environments usually do not affect a Teflon™ fluoropolymer coating. The only chemicals known to affect these coatings are molten alkali metals and highly reactive fluorinating agents. Permeation resistance due to the low porosity of the coatings means that they are extremely corrosion resistant and are chemically inert.
Teflon™ nonstick coatings are both hydrophobic and oleophobic. The low surface energy of the coatings means that the cohesive forces in the water are strong enough to make the water bead up and not spread across the surface of the coating. Cleanup is easier and more thorough.
Over a wide range of frequencies, Teflon™ coatings have a high dielectric strength, low dissipation factor, and high surface resistivity. Dielectric strength is the highest voltage that the coating can withstand before it breaks down. The dissipation factor is the percentage of electrical energy absorbed and lost when current is applied to the coating. A low dissipation factor means that the absorbed energy dissipated as heat is low. Adding fillers to certain coatings can make them electro-conductive enough to be used as an anti-static coating.
Teflon™ coatings are very resistant to scratches and abrasion due to their excellent durability and toughness. Surface scarring is minimal, especially in certain coatings when fillers are added.
Many Teflon™ industrial coatings are approved for food contact by the Food and Drug Administration. These specific Teflon™ coatings can be used for direct food contact according to the regulations of 21CFR. All types of Teflon™ coatings have FDA conforming options. Check a coating’s fact sheet to see if it is FDA compliant.
Property | ASTM Method | Unit | Teflon™ PTFE | Teflon™ FEP | Teflon™ PFA | Teflon™ ETFE |
Non-Stick | none | --- | Excellent | Excellent | Excellent | Good |
Abrasion Resistance | none | --- | Fair | Good | Very Good | Excellent |
Chemical Resistance | none | --- | Good | Excellent | Excellent | Excellent |
Max Use Temperature | °F °C °F °C | 550 600 | 400 450 | 500 550 | 300 390 | |
Melting Point | D3418 | °F °C | 621 | 500 | 582 | 512 |
Specific Gravity | D792 | 2.15 | 2.15 | 2.15 | 1.76 | |
Coefficient of Friction | D1894 | Static Dynamic | .12 - .15 .05 - .10 | .12 - .20 .08 - .30 | .20 | .24 - .50 |
Hardness | D2240 | Shore D | 50 - 65 | 56 | 60 | 72 |
Tensile Strength | D638 | Mpa | 21 - 35 | 23 | 25 | 40 - 47 |
Elongation | D638 | % | 300 - 500 | 325 | 300 | 150-300 |
Flexural Modulus | D790 | Mpa | 500 | 600 | 600 | 1200 |
Thermal Conductivity | see note 1 | 1.7 | 1.4 | 1.3 | 1.65 | |
Dielectric Strength | D149 | V/µm | 18 | 53 | 80 | 79 |
Dielectric Constant | D150 | 1 MHz | 2.1 | 2.1 | 2.1 | 2.6 |
Arc Resistance | D495 | sec | >300 | >300 | >180 | 122 |
Volume Resistivity | D257 | ohm·cm | >10 18 | >10 18 | >10 18 | >10 17 |
Surface Resistivity | D257 | ohm/sq. | >10 18 | >10 16 | >10 17 | >10 15 |
Weather Resistance | Florida Exposure | years unaffected | 20 | 20 | 10 | 15 |
Water Absorption | D570 | % | <.01 | <.01 | <.03 | <.03 |
Contact Angle | water ° | 104-111 | 95-105 | 104-111 | 90-100 |
note 1: thermal conductivity units = (BTU)(in) /(ft2)(hr)(deg F)
Download This Information As A PDF
Download The Teflon™ Product & Market Guide
For more information about the properties of Teflon™ coatings, download your free copy of the Teflon™ Product & Market Guide.
Download Teflon™ Product & Market Guide