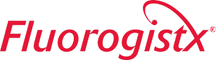
Teflon™ can be found on equipment and components in so many industries that it’s impossible to list them all. In addition to the largest market opportunities outlined under the “MARKETS” section of this site, below are six more growth-opportunity industry markets for Teflon™, and the coating systems most commonly used in each industry.
In the semiconductor industry, manufacturers use Teflon™ coatings in their wafer dipping baskets to get the most consistent non-stick and chemical resistance with the smallest damage potential. These manufacturers typically rely on either 532G-5010 (a PFA coating), 532-6310 or -6410 (ETFE coatings), or 954G-303 (an FEP Teflon™ S One Coat). Teflon’s most attractive qualities for this industry are its chemical resistance, inertness, and high purity.
Teflon™ is often used in the military for coating vehicle components and equipment for corrosion resistance, smooth lubricity, and matte finish. These same qualities are desirable for gun and ammunition manufacturers because Teflon™ improves firearms’ non-stick performance, ease in cleaning, and durable finish without the gloss. The most common Teflon™ coatings for these markets are PTFE One-Coats such as 958G-303 or 313, which offer high durability in a thin film system.
The flawless, repeatable release properties properties of Teflon™ make it ideal for sealing applications on packaging lines. Teflon™ often coats seal bars that seal plastic packages as well as the glue pots that dispense glue for sealing. The 3-Coat Reinforced System (857G-040/-140/-240) is the preferred Teflon™ coating for packaging because of its high temperature rating, nonstick properties, and industry leading durability. Other applications on packaging lines use FEP Teflon™ S One Coats, and pure FEP and PFA topcoats. Chemours™ offers a variety of solutions for this industry.
The durability and lubricity of Teflon™ coatings are attractive to 3D printing manufacturers. The application in this segment include the lead screws that move guide the printing application, resin basins that hold both the molded and unmolded resins, in addition to outer casings that need to be cleaned frequently due to resin buildup. Popular coatings used in 3D printing are PTFE One-Coats such as 958G-303 or -313 and FEP Teflon™ S One Coats such as 959G-203 or -204.
Teflon™ is often the best choice for industrial dryer drums because of the need for durability at high temperatures. Another textile processing application is coating non-woven rollers for non-stick performance. Pure FEP topcoats are commonly used in the textile industry, along with PFA coatings, and the 3-Coat Reinforced System (857G-040/-140/-240).
Hot plate welding usually means either pipe fusing or melting plastics for sealing purposes. Teflon™ is desirable for these applications because of its non-stick performance and release properties at high temperatures. The most common Teflon™ system for hot-plate welding is a pure PTFE topcoat system because of its great release properties and resistance to high temperatures.